摘 要:为提高微型热光电系统的输出性能,本文设计了一种内置错列挡板的平板式微型燃烧器,并通过构建的三维计算模型,研究了其工作过程的基本特征以及挡板间距和位置等结构参数的影响。研究结果表明:直通道内部设置挡板后,得益于换热效果的增强,辐射壁面的温度值和均匀性都有一定程度的提升;在2~5 mm的挡板间距范围内,每缩小1 mm,壁面温度约能提高17 K;挡板初始设置点则对壁面高温区域的分布形态和均匀性有直接影响,在4 mm时燃烧器工作效果最佳。
关键词:微型热光电系统; 微型燃烧器; 错列挡板; 燃烧特性; 外壁温度; 换热效果
随着微型机电系统(micro electro-mechanical system,MEMS)研发水平的不断进步以及应用领域的持续拓展,如何对其动力供给部分进行合理开发,也逐渐被引起广泛的重视。近年来,一些基于燃烧的微型动力装置由于工作时间长、能量密度高等优点,有望很好地解决这一问题,因而成为了各国科研竞争的焦点之一。
作为一种典型的微型动力装置,微型热光电系统(micro-thermophotovoltaic system,MTPV system)结构相对简单、没有运动部件、制造装配也容易,故优势相对其他装置也较为明显[1]。目前,该装置的能量转换效率还不够高,离实际应用尚有一段差距,这其中很大程度上是受微尺度燃烧过程中燃料驻留时间短、大面容比造成热损失过大以及燃料选择面窄等一系列特点制约的[2]。作为微型热光电系统最为重要的部件,燃烧器设计的好坏不仅会对内部燃烧过程的稳定性造成影响,而且其外壁面的温度分布状况还会直接影响到系统的输出性能。为此,国内外学者在该系统燃烧器的设计开发方面也作出一些尝试,如:Yang等[3]在圆管燃烧器的基础上加工出了一种带有内部台阶的燃烧器结构型式;Baigmohammadi等[4]进一步分析了线状物的插入对固定火焰位置的作用;Park等[5]设计了带有回热通道的双层管燃烧器,Jiang等[6]则从熵增的角度分析了回热措施的效果;潘剑锋等[7-8]则认为平板结构的燃烧器更容易实现微型热光电系统的模块化叠装,并进一步设计了局部催化的燃烧室;Li等[9]的研究表明多孔介质的填充可以提高燃烧器外壁面温度的均匀性;范爱武等[10-11]指出钝体的设置可大幅提高混合气的可燃流速,随后又提出了一种内置凹腔的燃烧器设计思路。此外,采用液体燃料的微尺度燃烧器设计和研究工作也正在积极地开展[12-13]。这些新颖结构的提出对于改善微尺度火焰稳定性起到了一定的帮助作用。然而,对于该类燃烧器,燃料化学能的利用程度跟高温混合气与燃烧器壁面间的换热过程也有着密切关系,而这方面的研究却没能被引起足够的重视。
为此,本文提出了一种内置错列挡板的平板式微型燃烧器的结构形式,并采用数值模拟的研究方法,分析了氢气/空气的预混气在该燃烧器内流动、换热及燃烧过程的基本特征,揭示了挡板的设置对于改善高温尾气换热强度、提高燃烧器壁面整体温度和系统输出性能的作用效果。随后,通过改变通道内挡板间距、设置位置等结构参数的计算,获取了燃烧器进一步优化设计的相关参考依据。
1 微型燃烧器结构
本文在现有平板式微型直通道燃烧器[7-8,14]的研究基础上,提出了一种内置多排错列挡板的平板式微型燃烧器,其结构如图1所示。
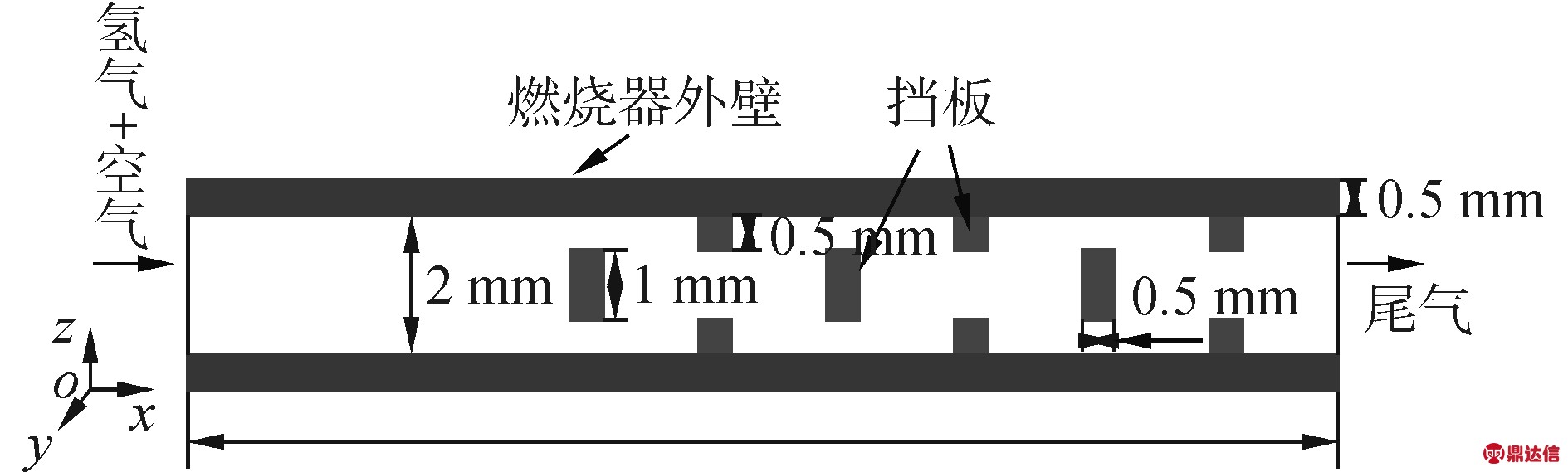
图1 内置挡板式微型燃烧器剖面结构示意图
Fig.1 Schematic diagram of the micro-planar combustor with baffles
整个燃烧器外观呈长方体结构,长(x方向)、宽(y方向)、高(z方向)的尺寸分别为18 mm×9 mm×3 mm。燃烧器外壁厚0.5 mm,其内部整体结构为高度2 mm的直通道,并在通道的中心区域和上下壁面上设置了多块挡板,两侧开口端则为燃烧器的进气和排气口。挡板在气体流动方向上呈错列的布置方式,长度均为0.5 mm,宽度跟通道宽度保持一致(即8 mm宽),其中位于通道中心区域的挡板高度为1 mm,其前后排上下壁面处对称布置的挡板高度为0.5 mm,计算中挡板的间距和起始设置位置则为可变参数。工作时,氢气和空气经充分预混后通入燃烧器进口端,燃烧器和挡板的材料均选用316不锈钢,该材料能承受1 400 ℃左右的高温。
2 计算模型的建立与验证
2.1 几何模型和网格划分
内置挡板式微型燃烧器在实际加工制造过程中,挡板和燃烧器内壁面是紧密相连的,因此若在计算过程中采用图1所示的二维几何模型,则中心挡板和燃烧器侧壁间的直接导热就会被忽略,这势必会引起一定的计算误差。为此,根据燃烧器的实际结构和尺寸,建立了一个三维的计算模型,以对通道内的燃烧过程和燃烧器壁面温度分布进行更为准确的预测。
考虑到燃烧器整体结构的规整性,本文采用了正六面体的结构化网格划分方法,并对网格进行了相关性检查(如图2所示),根据检查结果最终确定长、宽、高三个方向上网格划分的密度均为0.1 mm,总网格数目为243 000。
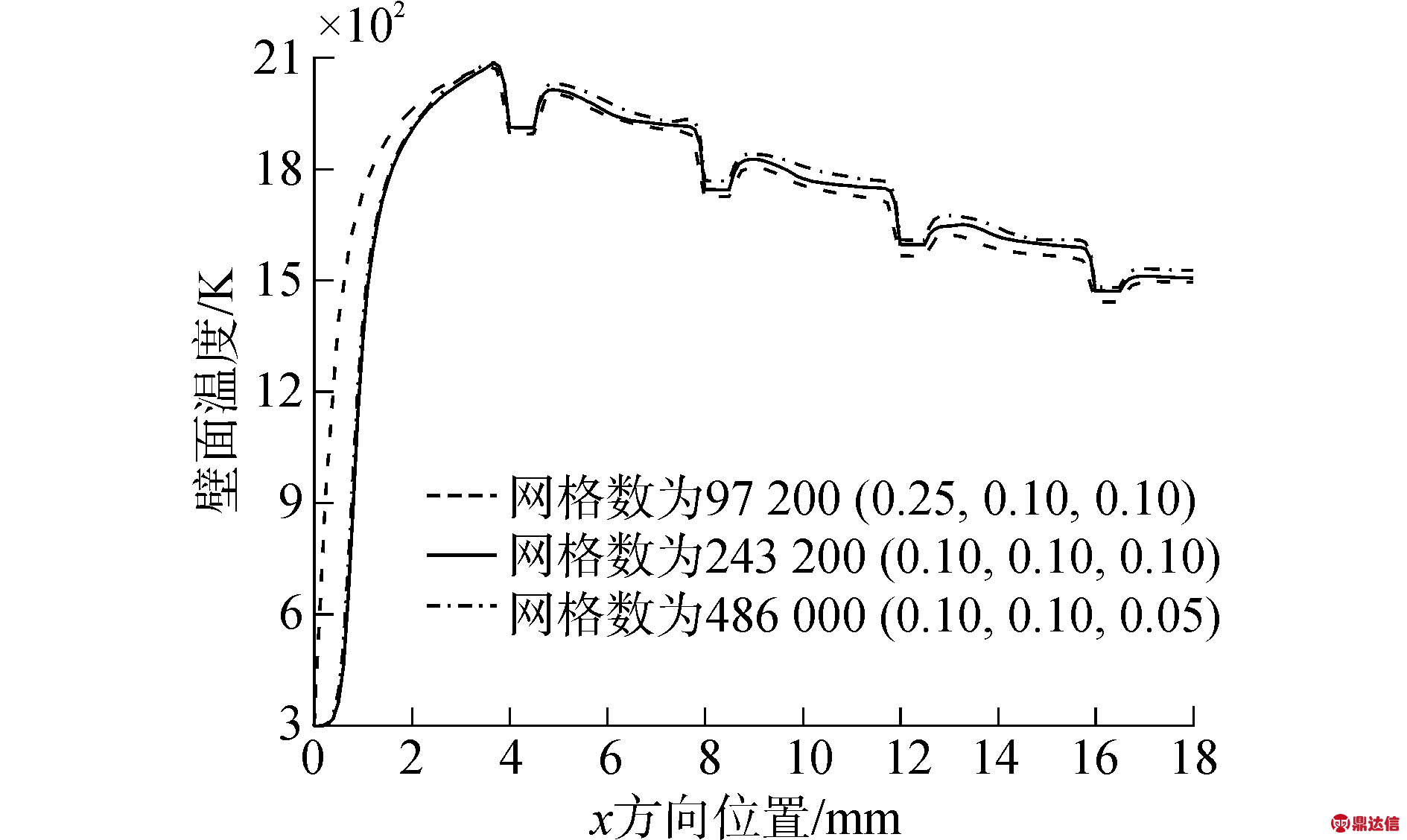
图2 不同网格密度下通道内中心线的温度分布
Fig.2 Centerline temperature profiles of combustor at different mesh densities
2.2 模型建立方法
本文采用了氢气/空气的详细气相化学反应机理模型[15],该机理共包括19个基元反应,9种气相组分,分别为H2、H、O2、O、OH、H2O、HO2、H2O2和N2。对于本文的燃烧器,根据通道高度以及气体分子平均自由程长度计算所得的Kn数约为2×10-5,这个数值远比连续介质区10-3的界定值要小,因此Navier-Stokes 方程及Fourier 热传导等定律仍旧适用。基本的控制方程包括连续性方程、动量守恒方程、化学组分输运方程和能量守恒方程[14]。对上述方程采用有限容积法和欠松弛的隐式求解方法,并选择Fluent作为计算分析的软件。各方程均采用一阶精度的迎风格式进行离散[4],并将SIMPLE算法作为压力速度耦合的处理方法。
本文涉及到的计算工况在冷态下的雷诺数范围为418~1 669,但考虑到挡板对于提高混合气扰动程度的作用以及Ronney等的建议[16],将流动模型设置为标准的k-ε模型,对应的燃烧模型则选用有限速率模型。氢气/空气混合气体的密度按照不可压缩理想气体定律计算[17],混合气比热根据混合定律计算,粘度和导热系数则由各组分对应值经质量加权平均获取,混合气的质量扩散系数依据分子运动理论进行计算[18]。对于各组分、比热按温度的分段多项式插值计算,粘度和导热系数也按照分子运动理论进行计算。计算过程中,忽略了Dufour效应、气体辐射以及粘性耗散的影响[6]。
在边界条件设置上,混合气进口端设为速度边界条件,给定入口混合气的总流速、温度(300 K)及混合物组分的质量百分比;排气端设为自由出流边界条件;考虑到燃烧器工作时外壁面将同时以热辐射和对流换热的方式与外部空间进行热量交换,所有外壁面均设成综合热边界条件,其中对流换热系数为设为15 W/(m2·K),而根据红外光谱仪的测试结果,壁面发射率则设为 0.65。
此外,316不锈钢的比热容以及密度与普通不锈钢的数值差别不大,而导热系数则随着温度明显变化[19],考虑到微型燃烧器壁面的温度状况,计算时将其设定为25 W/(m·K)。
2.3 模型验证
为对模型的适用性进行验证,加工了相同尺寸、内部未装置挡板的直通道微型燃烧器,并将部分计算结果同对应的实验测试作了对比,如图3所示。实验中的壁面温度采用红外热像仪进行测量,型号为ThermovisionTM A40,微尺度实验台架的相关介绍参见文献[20]。从图3可以看出,在氢气600 mL/min和900 mL/min的流量下(当量比为1),不管是模拟得出的外壁面高低温区域的位置和形态,还是外壁面中心线上的温度曲线,都能跟实验结果做到较好的吻合,采集的数据最高相对误差仅为3.5%,这也充分论证了所构建的平板式微型燃烧器燃烧和传热过程计算模型的正确性。
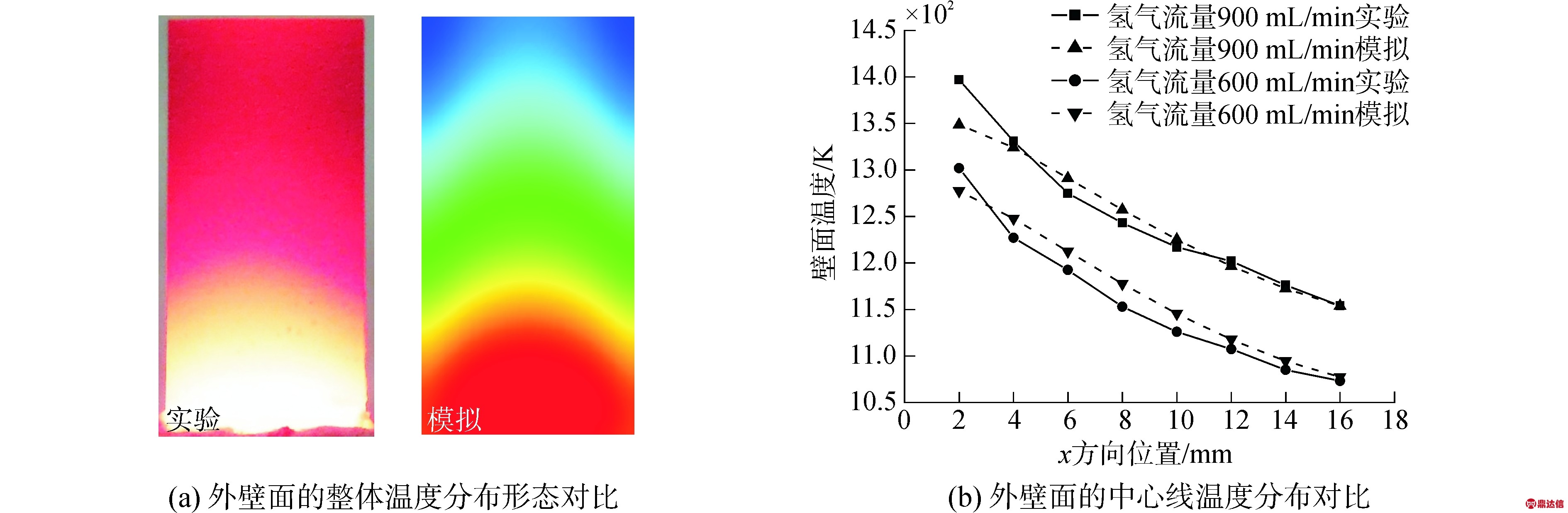
图3 计算模型的实验验证
Fig.3 Experimental validation of computational model
3 计算结果与分析
3.1 两种燃烧器的对比
为掌握内置错列挡板式微尺度燃烧器的基本工作特性,首先将其内部速度场和温度场、外壁面温度场以及壁面平均温度与相同工况下直通道型燃烧器作了对比。计算中,混合气的计量采用入口流速的形式,各挡板间距取为3 mm,首块挡板距离通道入口4 mm。
图4给出了两种燃烧器中心截面的速度场和温度场对比情况。从图中可以看出,氢气和空气的混合气一进入通道即被点燃,反应在距离入口2 mm的区域内就已完成,这充分说明了氢气易于燃烧的特点。在入口流速为6 m/s的情况下,燃烧后高温烟气在直通道型和内置挡板型燃烧器内的平均流速分别达到了31 m/s和35 m/s,其中前者流速分布较为均匀,而后者则差别较为明显,其隔板区域由于通道变窄,流速得到了大幅提高,最高流速达到了86 m/s。同时,类似于换热翅片的隔板,对于增强混合气与壁面间的接触和扰动程度也有着很大的促进效果。在该两方面的综合作用下,内置挡板型燃烧器内部的平均换热系数达到了223 W/(m2·K),而直通道型的对应值仅为67 W/(m2·K),从而使得更多高温尾气的热量能被壁面吸收,这也是图4(b)中内置挡板型燃烧器通道内混合气温度明显逐渐变低的原因所在。本文各个工况下的平均换热系数可由牛顿冷却公式推出,计算方法如下
h=
式中: Q为燃烧器内部的整体换热量, A为与混合气接触的燃烧器所有内壁面积, Δt为混合气及内壁面平均温度的差值。
图5为入口流速6 m/s时两种燃烧器辐射壁面的温度场对比图。从图中可以看出,两个燃烧器的低温区域都位于燃烧器末端的两个角上,直通道型的高温区域处于燃烧器前段0~6 mm的位置,内置挡板型燃烧器的高温区域则要往后一些,而且高温区域的面积也显得更大。在壁面温度梯度值(壁面最高最低温度的差值)方面,两个燃烧器分别为188 K和140 K,这说明错列挡板的设置还起到了提高壁面温度均匀性的作用。
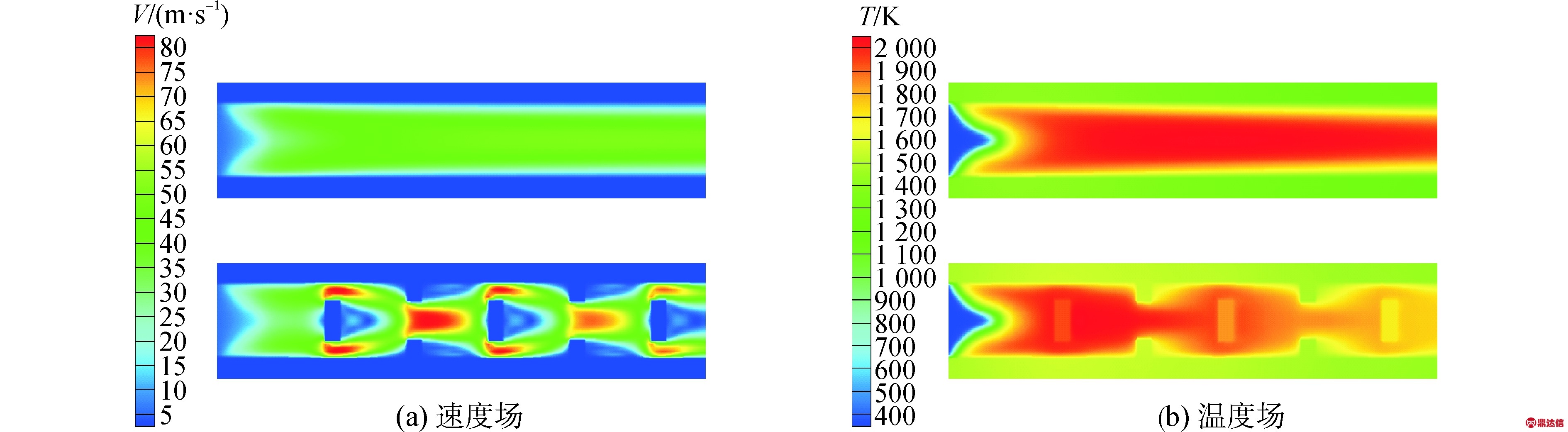
图4 中心截面速度场温度场对比(入口流速为6 m/s)
Fig.4 Comparison of velocity and temperature distributions on the combustor center section (inlet velocity is 6 m/s)

图5 燃烧器外壁面温度场对比(入口流速为6 m/s)
Fig.5 Comparison of temperature distributions on the combustor external wall (inlet velocity is 6 m/s)
图6给出了各个流速下两种燃烧器辐射壁面平均温度和可用辐射能的具体数值。图中四种结构的燃烧器,壁面平均温度都会随着入口流速的增加而有所提高,这是符合燃料热值规律的,并且这种增长趋势在低流量下均尤为明显,流速从2 m/s升到4 m/s时,壁面温升分别达到了130 K和187 K,而流速从6 m/s升至8 m/s时,对应的增幅仅为36 K和42 K,可见通过单纯提高进气流量的做法,并不是提升系统工作总效率的有效措施。同时,也应当看到,在4个不同的入口流速下,内置挡板型燃烧器壁面的平均温度相对直通道型燃烧器的增幅分别达到了68、126、131 和137 K,这说明混合气流量越大,挡板提高通道换热强度的作用就会越来越明显地发挥出来,这也使得新型燃烧器在入口流速4 m/s时1 401 K的平均温度,比直通道型燃烧器在8 m/s的流速工况下高出了35 K。
在微型热光电系统的工作过程中,壁面平均温度的增加是提高系统功率输出和能量转换效率最为直接有效的途径[1-2]。图6中的三个高流速工况下,新型燃烧器所获得的可用辐射能(小于光电池截止波长的辐射能,本文计算时选用GaSb电池)均几乎达到了直通道燃烧器对应值的两倍。从这个角度来讲,通过这种设置挡板的简单方法,就可带来燃烧器外表面辐射能量“质”和“量”的飞跃,这也充分彰显了平板式内置挡板型燃烧器的优势所在。
自熊彼特以来,技术创新与产品市场势力的关系一直是研究的重点和难点之一。合作创新与产品市场势力的关系成为该分支的最新拓展。学者们从各自的视角出发,在不同的分析框架下,得出了大相径庭的结论。有一类静态分析框架模型认为,合作研发影响企业间生产成本的差距,从而改变产品市场结构和企业产品市场势力。利用这个框架分析的学者,可以在一个模型中同时考察合作创新的研发投资、产品市场势力、利润以及社会福利绩效,但是却无法体现变量之间跨期的影响作用。为了弥补这个缺陷,学者们引入了动态模型,以期刻画企业合作研发行为对长期定价,进而对产品市场势力的影响机制。
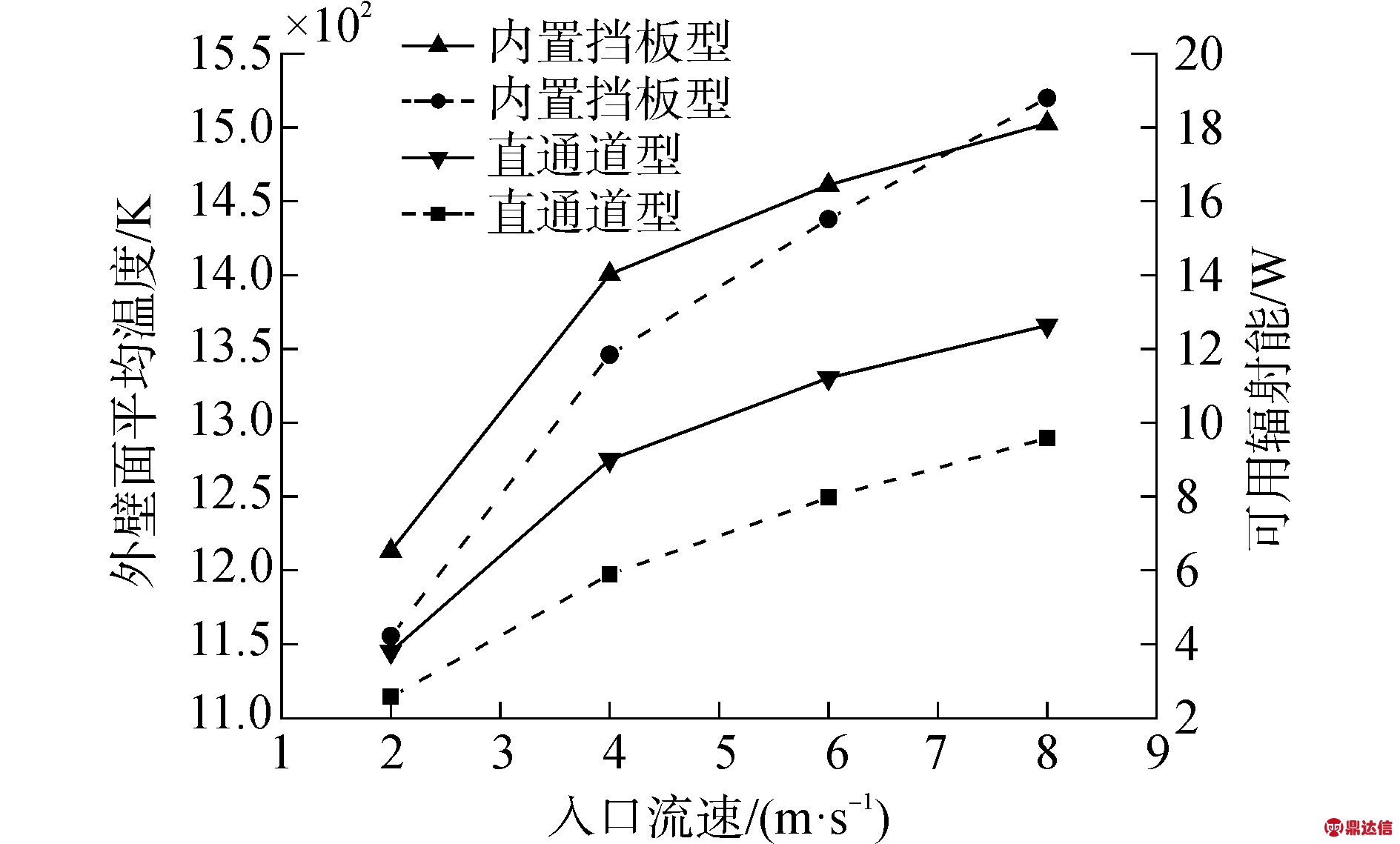
图6 不同流速下燃烧器外壁面平均温度和可用辐射能对比
Fig.6 Comparison of mean temperature on external wall and usable radiant energy at different inlet velocities
3.2 挡板间距的影响
图7给出了燃烧器外壁面中心线的温度分布对比,从图中可以看出:受挡板起始位置的影响,0~4 mm范围内不同间距下壁面中心线的温度变化趋势比较类似,均沿着气流方向逐步增加,在4 mm左右处达到最高值;而4 mm以后壁面温度分布的形态则受间距的影响很大。一方面,间距过大时,通道内挡板的数目相对较少(间距5 mm时,仅为3排挡板),这将造成上下挡板位置对应的壁面温度“平坦区”,而当间距较小时,整个中心线温度曲线的连续性则提高了很多;另一方面,间距越小,混合气在通道内部的湍动程度就越高,并且接触的壁面也越来越多。
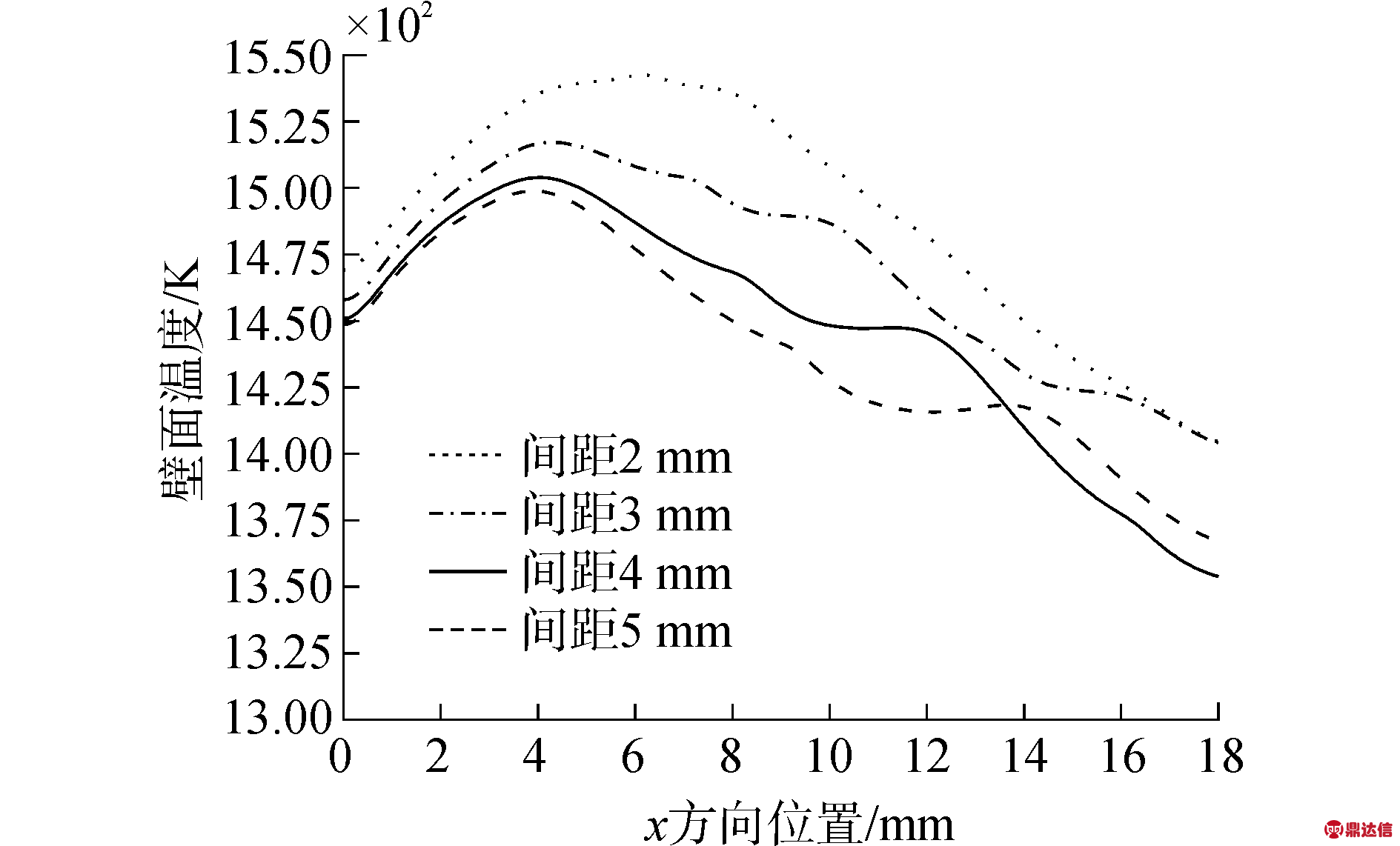
图7 不同挡板间距时燃烧器外壁面中心线温度分布(入口流速为6 m/s)
Fig.7 Centerline temperature profiles at differentbaffle intervals (inlet velocity is 6 m/s)
因此,从图8中可以看出,在同样的燃料输入下,间距缩小后通道内的平均换热系数和平均热流密度均有不同程度的提高,这也使得壁面中部高温区域的幅值整体上移。在入口流速6 m/s的计算工况下,间距为2~5 mm,燃烧器外壁面的平均温度依次为1 481、1 461、1 435 和1 430 K,壁面处的可用辐射能则可从17.2 W降低至13.4 W。由此可见,当间距缩小时,壁面温度整体呈增加之势,在间距较小时增幅尤为明显,故从提高系统输出性能的角度来讲,错列挡板的间距应尽可能的小。但间距2 mm时,通道内挡板总数目已为7排,而当间距为1 mm时,挡板数目将达到14排,这无形中会增加燃烧器的加工制作难度。因此,针对本文提出的内置隔板微型燃烧器,间距选为2~3 mm较为合适。
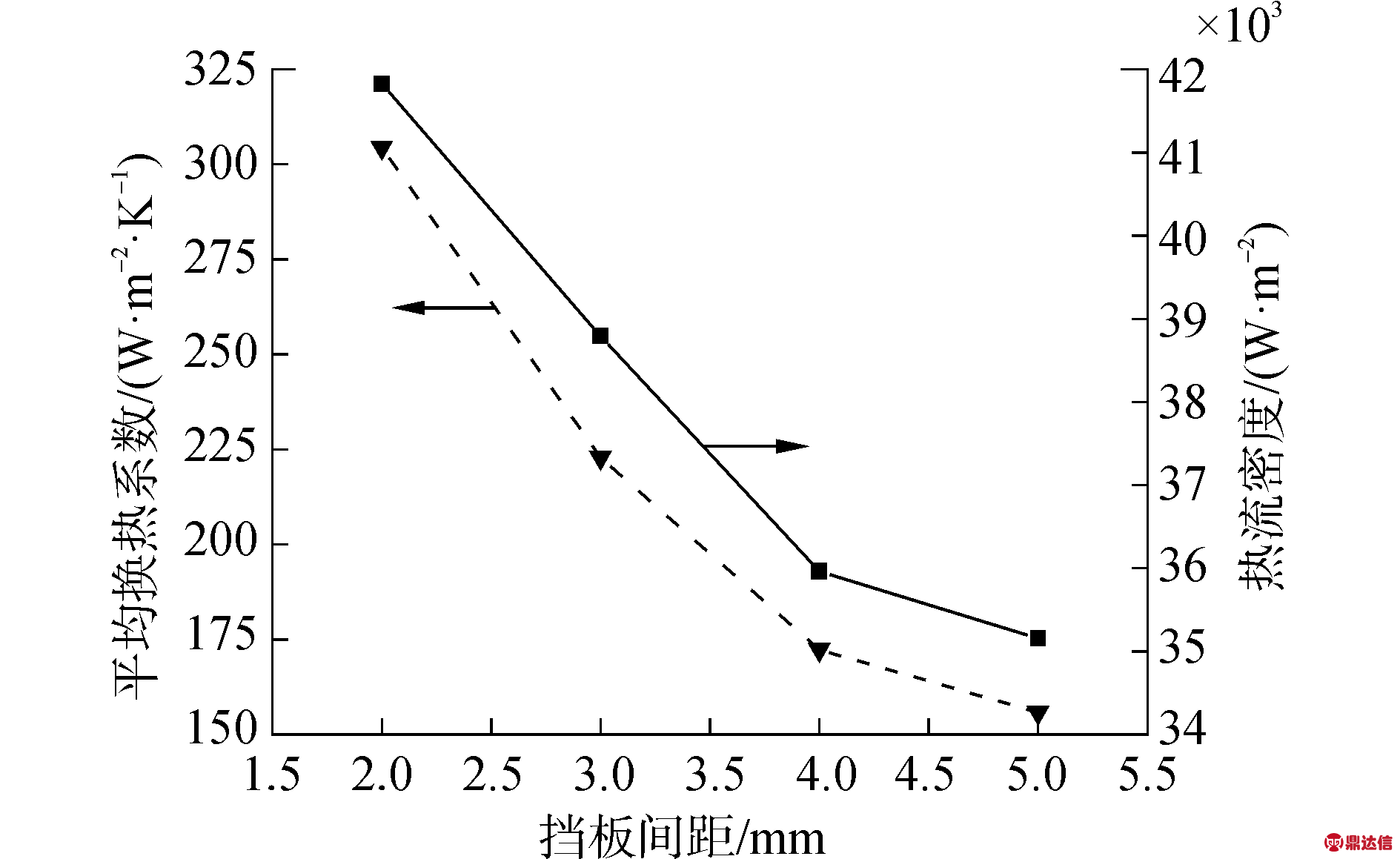
图8 不同挡板间距时通道内平均换热系数和热流密度对比(入口流速为6 m/s)
Fig.8 Comparison of mean heat transfer coefficient and heat flux at different baffle intervals (inlet velocity is 6 m/s)
3.3 挡板起始位置的影响
为进一步考察挡板位置数目等对燃烧器工作过程的影响,将挡板的起始位置作为研究对象,并分别选取距离入口2、4、6 和8 mm这4个特征值进行了相关计算,各错列隔板的间距均设为2 mm。
从图9所示的燃烧器外壁面温度场对比图中可以看出,挡板的起始设置点会影响到燃烧器表面高温区域的分布位置和形状。在不同挡板起始位置下,各外壁最高温度的区域均与第一块中间挡板的位置保持对应,起始挡板位置越靠后,高温区域也将会随之后移,各壁面低温区也都集中在燃烧器的出口附近。同时,由于壁面最高温度值的下降(2 mm时为1 550 K、8 mm时为1 508 K),起始设置点的后移会造成高温区所占的相对面积随之变小,但是壁面高温区域向出口侧低温区导热距离的缩短,也使得整个壁面温度的均匀性反而得到了提高,挡板起始位置8 mm时111 K的温度梯度,比2 mm时小了近100 K。高温状态下,材料内部温度差异过大将会引起较大的表面热应力累积到一定程度后,将导致材料脆裂,从而影响到燃烧器的使用寿命。
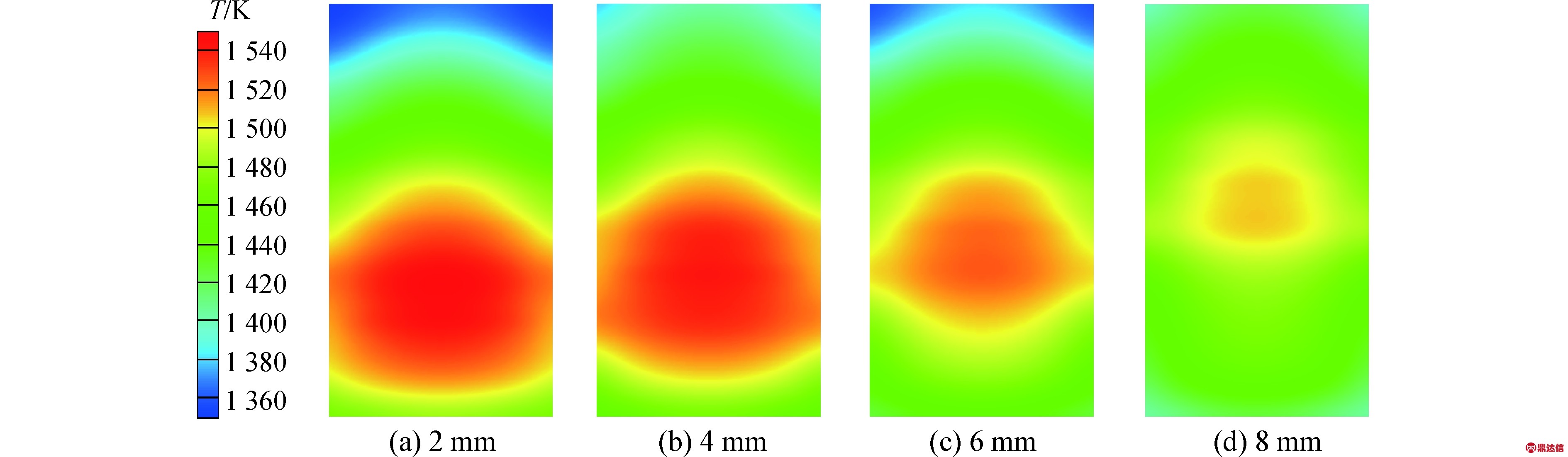
图9 不同挡板起始位置下燃烧器外壁面温度场对比(入口流速为6 m/s)
Fig.9 Comparison of temperature distributions on the external wall at different baffle arrangement positions (inlet velocity is 6 m/s)
图10给出了不同挡板起始位置下燃烧器外壁面平均温度和可用辐射能的对比情况,从图中可以看出:不同流速时该两个参数随起始位置的变化规律是一致的,即最高值都对应着4 mm的起始位置,并沿着2、6 和8 mm的顺序依次降低。从数据上看,起始位置对壁面平均温度和辐射能输出的调节效果要比间距的影响相对小一些,两个入口流速下最大差值仅为20 K和1.68 W,而起始位置从6 mm变为8 mm时,壁面平均温度的值也只下降了5 K。
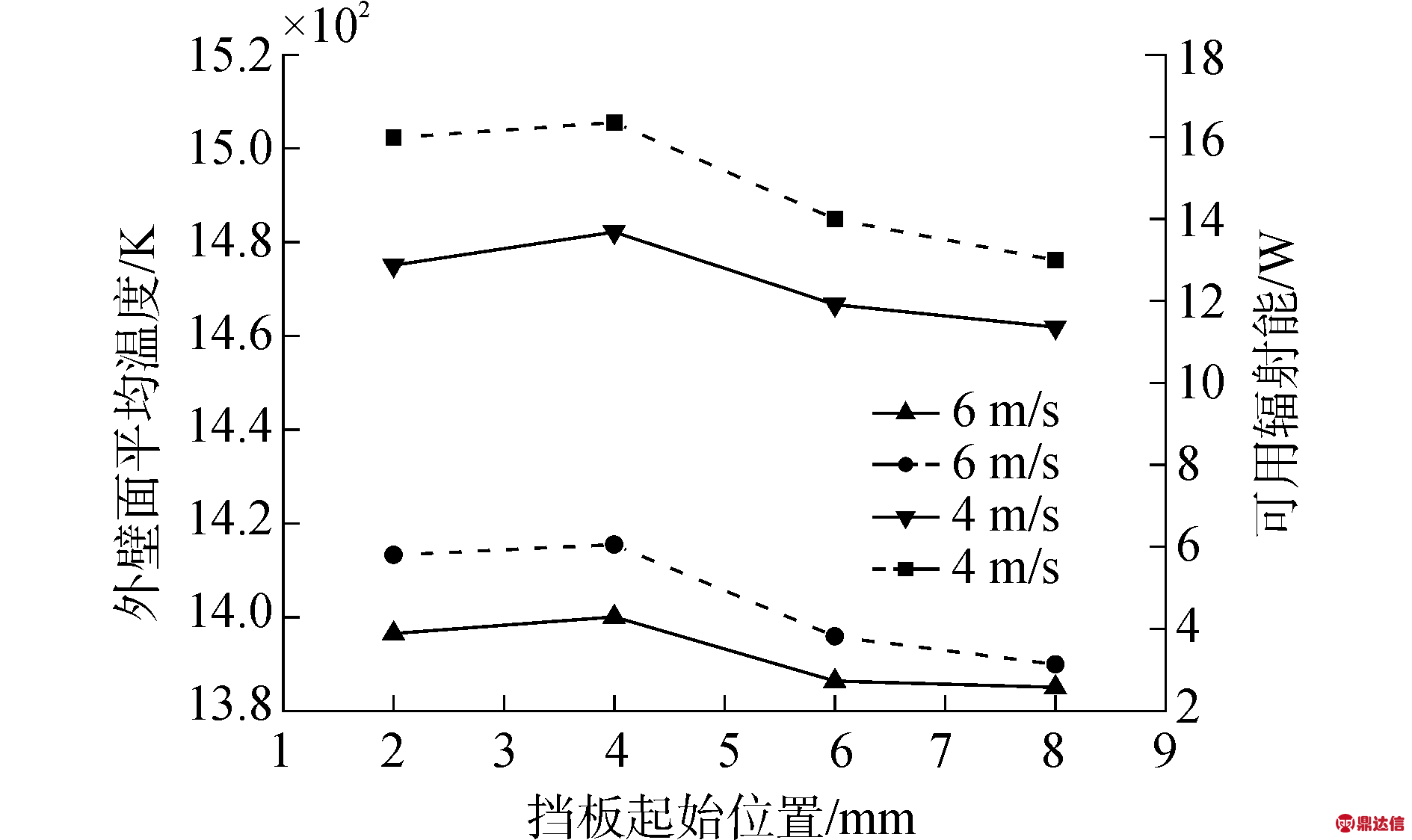
图10 不同挡板起始位置下,燃烧器外壁平均温度和可用辐射能对比
Fig.10 Comparison of mean temperature on external wall and usable radiant energy at different baffle arrangement positions
上述现象可以从图11中平均换热系数和火焰最高温度的变化中得到解释。在相同间距下,挡板设置的越靠前,通道内挡板的数目就会越多,平均换热系数也会得到相应的提高,因此起始位置2 mm时的225 W/(m2·K)的换热系数达到了8 mm时的1.8倍。但是,挡板位置与通道内火焰的温度分布也有着直接的关系,过早的障碍物设置会使得火焰形态发生变化,进而造成火焰温度的下降,图中2 mm时2 000 K的最高火焰温度就比8 mm时低了78 K,这一定程度上也造成了热量传递驱动力上的差异。
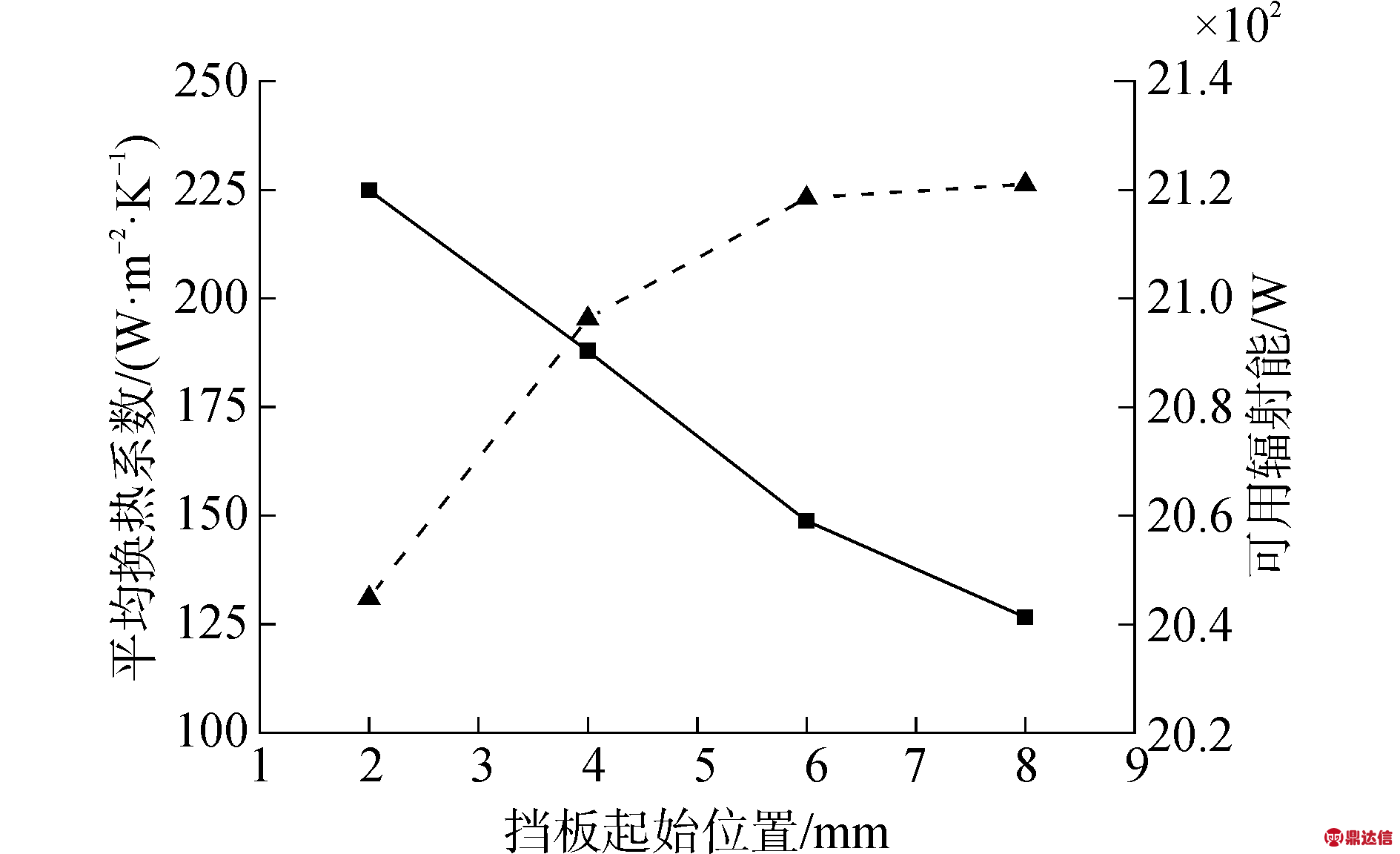
图11 不同挡板起始位置下,通道内平均换热系数和火焰最高温度对比(入口流速:4 m/s)
Fig.11 Comparison of mean heat transfer coefficient and maximum flame temperature at different baffle arrangement positions(inlet velocity is 4 m/s)
可见,内置挡板的微型燃烧器外壁面平均温度的高低以及均匀程度,实际上是由以上两个因素共同决定的。综合考虑实际的换热效果,在挡板起始位置的选择上,认为4 mm的特征值应该优势更为明显。
4 结论
1)错列挡板的设置,对于增强混合气与壁面间的换热效果有着很大的帮助,相对于无挡板的直通道型燃烧器,大部分计算工况中辐射壁面温度可提高100 K以上;
2)挡板间距的选取对于壁面平均温度的高低有着重要影响,间距越小,平均温度也越高,间距每缩小1 mm,壁面整体温度约提高17 K;
3)挡板的起始设置点将直接影响到燃烧器表面高温区域的分布形态和均匀性,在火焰温度和换热效果两方面的综合作用,起始位置为4 mm时壁面平均温度相对较高。