摘 要:为了提高装砖码垛机器人的工作效率,同时减小振动对机器人的影响,基于三次样条插值法,提出一种使机器人轨迹最优的规划方法,对各关节进行轨迹规划。利用权重系数法定义目标函数,以运动学和动作时间为约束条件,使码垛机器人在运行过程中其时间和冲击达到综合最优。采用遗传算法求解出最优时间序列,进一步求解出最优轨迹。研究结果表明:末端轨迹跟踪误差在合理的范围之内,该方法在装砖码垛机器人轨迹规划方面是可行的、合理的;可以为工作效率与冲击等矛盾问题到达综合最优提供一种解决方案。
关键词:装砖码垛机器人;时间- 冲击最优;轨迹优化;遗传算法
0 引 言
随着工业自动化水平的不断提高,很多人工作业的领域逐渐被工业机器人所取代。码垛机器人作为工业机器人的一种,凭借其高精准、高效率、大负载,得到了广泛的应用,大大地提高了生产效率、经济效益,减轻了工人负担[1]。在砖瓦行业,码垛机器人也逐步得到应用,“高劳低效”的问题逐渐得到解决,使该行业的自动化水平得到了很大的提高。而轨迹规划(trajectory planning)作为机器人运动控制系统的基础研究,决定着机器人的运动方式和作业性能。根据不同的使用场合和作业要求,需要选择不同的规划方案[2-4]。轨迹规划方案的选择不仅要保证机器人拥有较高的工作效率,还要满足机器人运动平滑,避免产生位置、速度和加速度的突变,防止运动发生波动,加剧机械部件的磨损,导致机器人系统的振动和冲击,影响机器人的运动精度和自身的使用寿命[5-7]。
孙玥等[8]采用五次多项式插值法对码垛机器人进行轨迹规划,该方法实现了速度和加速度的平滑过渡,末端运行精度得到很大的提高。韩江等[9]利用混合插值法对关节轨迹进行了规划,改善了机器人的运动性能,但同时大大增加了机器人控制系统的运行负担。郭超等[10]运用直角门字路径法,使末端执行器速度和加速度连续,但运动时在拐角处易产生抖动。本文结合装砖码垛机器人工作任务的特点,基于三次样条插值法对运动轨迹进行规划,并采用遗传算法在满足运动学和时间约束的前提下对规划轨迹进行优化,使时间-冲击达到综合最优。
1 码垛机器人路径描述
装砖码垛机器人在工作时,需要经过提升点(A)、转向点(B)、下降点(C)并最终达到码放点(D),码垛机器人工作路径如图1所示。
由图1可知,码垛机器人在工作过程中,末端执行器从A到B点(C点到D点)的过程中,为了减少或消除末端执行器与周围环境发生干涉,需要保证末端轨迹有一定的直线度(误差值为±1 mm),确保工作的顺利进行,提高工作效率。
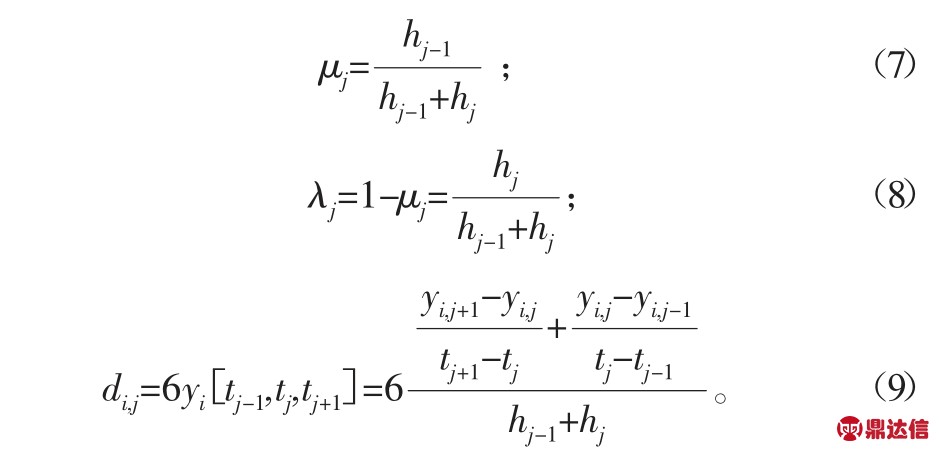
图1 码垛机器人运动轨迹
2 最优轨迹规划问题描述
由机器人的运动的路径特点可知,若采用传统的机械式搬运动作,当机器人在经过各个节点时会产生速度、加速度突变,对各关节会产生较大的冲击,同时还会引起末端执行器的抖动,影响砖块的抓取工作,甚至会导致在转运过程中砖块脱落的现象,带来不安全因素,会影响工作效率。
码垛机器人为多关节机器人,对于关节i(i=1,..,N),定义时间序列为t0,t1,...,tn-1,对应关节的位置序列为yi,0,yi,1,...,yi,n-1;hj=tj+1-tj,其中j=0,1,.....,n-1,hj为相邻两点之间的时间间隔;相应区间端点的加速度值定义为:Mi,j=si,j"(tj),其中si,j(t)为在子区间[tj,tj+1]上的一个三次多项式,因此si,j"(tj)在子区间上为一个线性函数,即加速度函数,可定义为

需要满足的条件为:码垛机器人各关节位移、速度、加速度在子区间和相邻子区间之间均连续的;在抓取、码放时各关节角速度从零开始,结束于零。基于上述条件,对式(1)积分得关节的速度表达式为

对式(2)积分得关节的位移表达式为
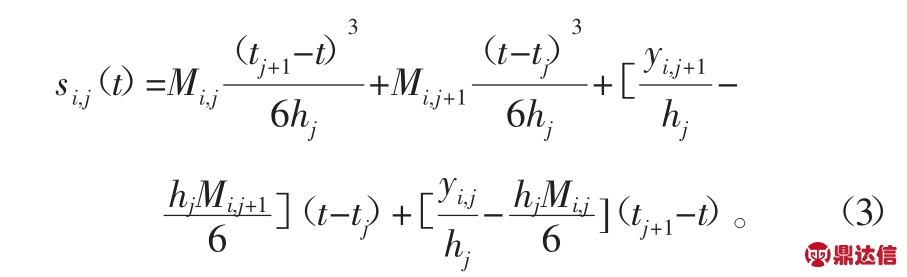
对式(1)求导得关节的加加速度表达式为

由上述条件可知,一阶导数是连续的,即si′(tj-0)=si′(tj+0),代入式(2)得
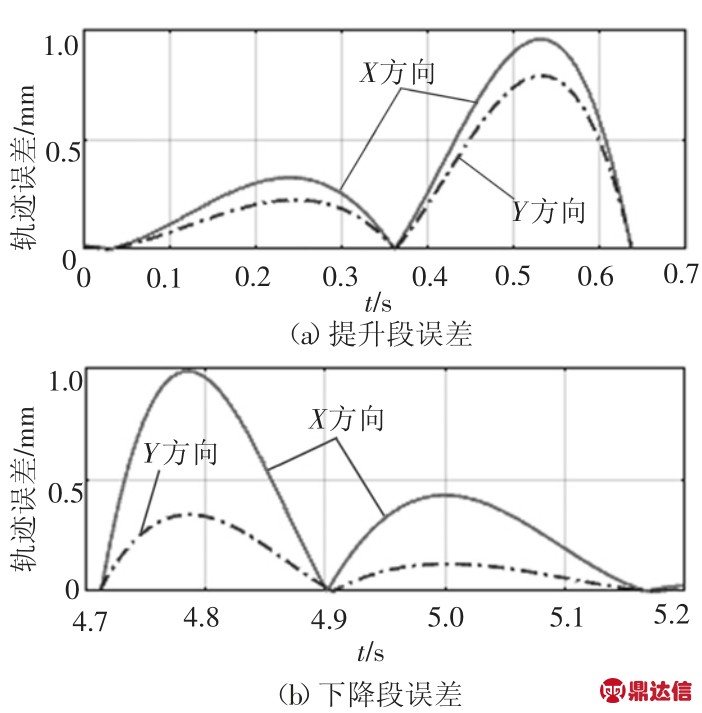
整理得

其中:
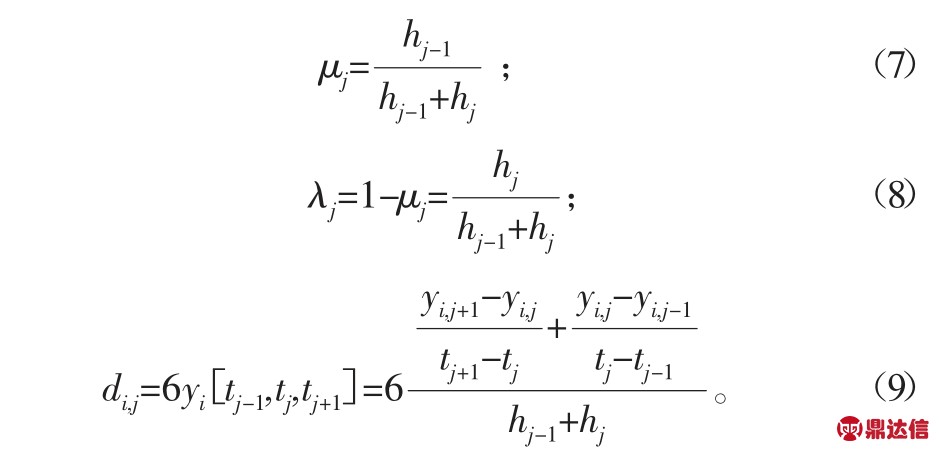
由压紧样条边界[11]si,0′(t0)=0和si,n′(tn)=0,分别可得:
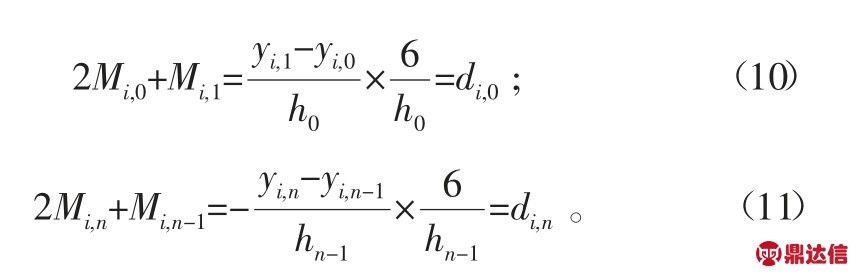
根据上述关系和边界条件,整理可得方程组为
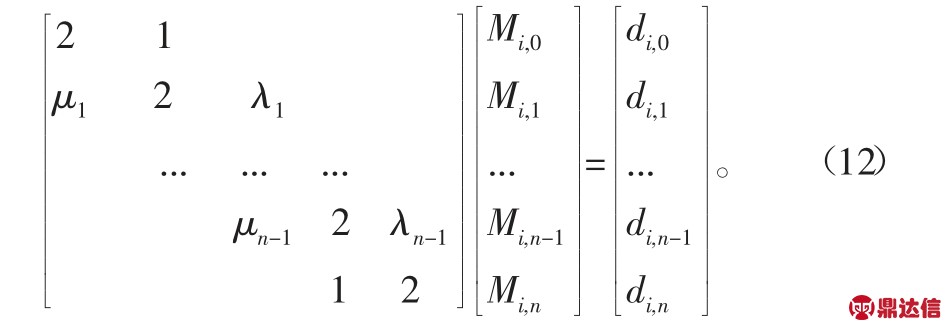
此方程组的系数矩阵为对角占优矩阵,即存在唯一解,可以利用追赶法求解方程组Mi,0,Mi,1,...Mi,n的值。
3 基于遗传算法的轨迹优化
3.1 遗传算法简介
遗传算法(Genetic Algorithm,GA)是一种基于进化理论的全局优化搜索算法,是把实际问题中可能潜在的解作为个体(individual),经过一定数目个体的基因编码形成一个种群(population),初始种群确立之后,按照生物进化原理,根据初始种群对实际问题适应度的大小进行个体的选择(selection)、组合交叉(crossover)和变异(mutation),产生更能适应环境的新种群。此算法通过模拟生物进化的过程,逐步产生新的解集,直到产生满足收敛条件的最优解。
3.2 轨迹优化模型的建立
机械臂的脉动由加速的变化(即加加速度)来体现,K. J. Kyriakopoulos等[12]研究表明,机械臂的脉动与机械臂的冲击有直接关系,脉动越小则冲击越小。为此兼顾机器人的运行时间和运行过程中的冲击,使之运动性能综合最优。
1)目标函数。以运行时间最短和冲击最小为优化目标函数,即:

其中:N为机器人关节数;α为弹性系数,由于工作时间与冲击函数(由加加速度平方的积分)在数量级上有差别,会削弱其中的一项,影响结果的准确性,需要α来进行平衡;tf为码垛机器人的工作时间;KT为工作时间的权重,KJ为冲击函数的权重,且KT+KJ=1。
2)设计变量。动作时间与冲击函数都是由hj来表示的函数,设变量为

3)约束条件。
a.速度约束。由上述可知速度为二阶函数,速度的最大值会出现在端点处或者是区间的极值点处,因此速度约束可表达为

其中:Vim为i关节最大速度;i=1,2,..N; j=0,1,.....,n-1。
把tj,tj*,tj+1分别代入式(2)得:
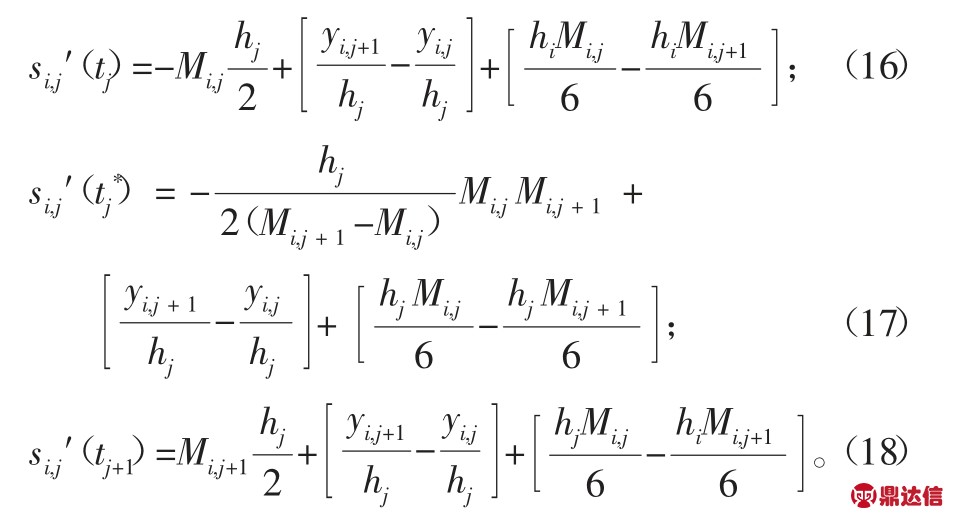
b.加速度约束。根据式(1)可知,加速度在相应的区间为线性函数,最大值只能发生在t2,t3,...,tn-1处,因此加速度可表达为:

其中:Aim为i关节最大加速度;i=1,2,..N; j=0,1,.....,n-1。
周国平先生说:人生的价值,可用两个词来代表,一是幸福,二是优秀。两者皆取决于人性的健康生长和全面发展,教育的使命即在于此。

其中:Jim 为i关节最大加加速度;i=1,2,..N; j=0,1,.....,n-1。
d.时间约束。码垛机器人动作时间为,因此动作时间可表示为

式(13)~式(21)均以hj为变量,整理得到非线性约束最优化问题的标准形式为:
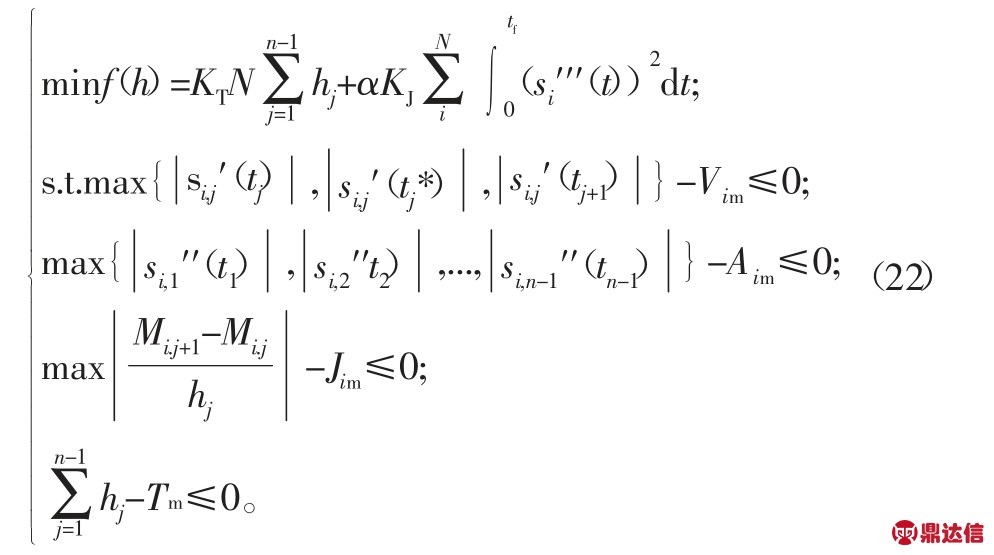
式中:i=1,2,..N;j=0,1,...n-1。
4 仿真分析
码垛机器人在工作时需要经过的节点为点A(1400,1233,310)、点B(1400,1233,610)、点C(-2904,-304,610)、点D(-2904,-304,310)。轨迹的光滑性、约束性与路径的点数相关,选择合理的点数和点间距进行轨迹规划可以提高码垛机器人的运动精度和工作效率[13]。本文在已有节点的基础上共选择10个点,在上升、下降段中相邻两点的间距为100 mm[14]。
根据对工作路径的离散化处理,由运动学逆解求出各关节对应的位置序列,如表1所示。各关节的运动学约束,如表2所示。
表1 各关节角位移 rad
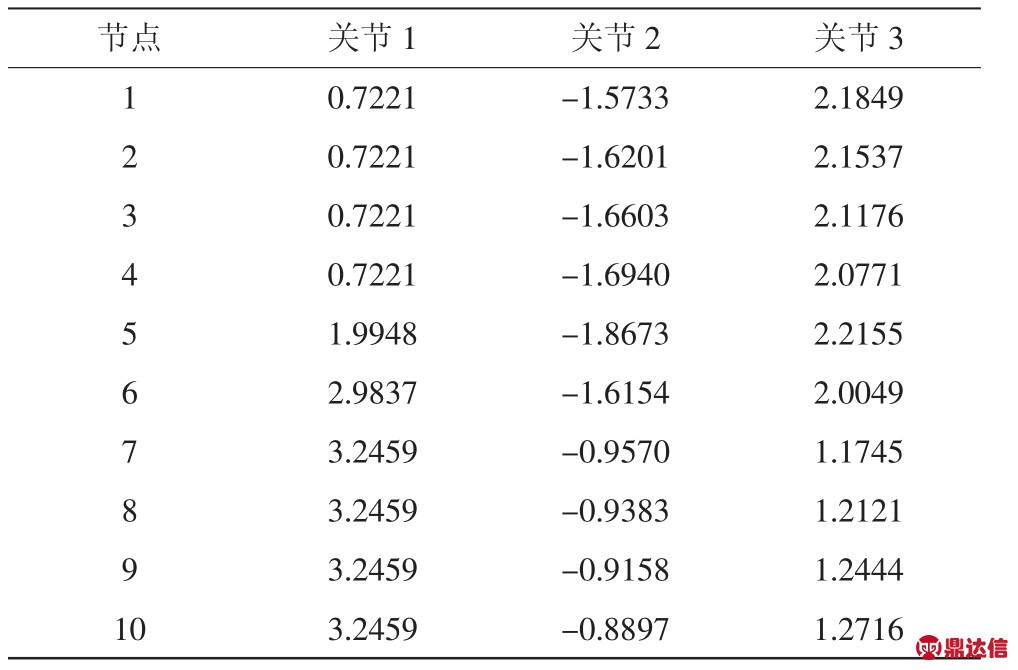
表2 各关节运动约束条件[15]
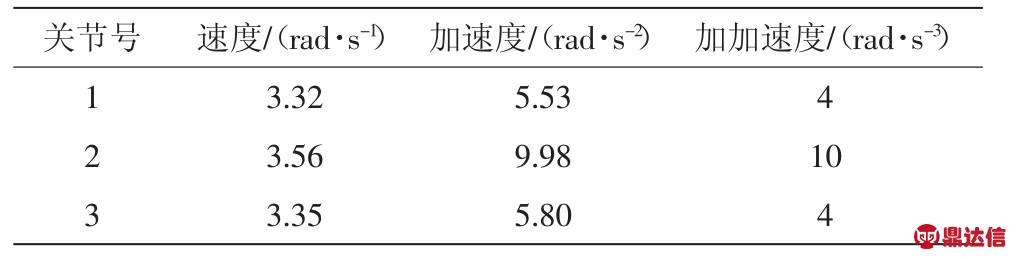
码垛机器人的时间约束为t≤7 s;令弹性系数α=0.01;权重分别为:

遗传算法设置种群数为100;精英数目和交叉后代比例分别为10和0.75;最大迭代数目为100,分别在不同的KT、KJ值情况下,对各关节运动轨迹进行优化,优化的最终结果如表3所示。
表3 轨迹优化结果
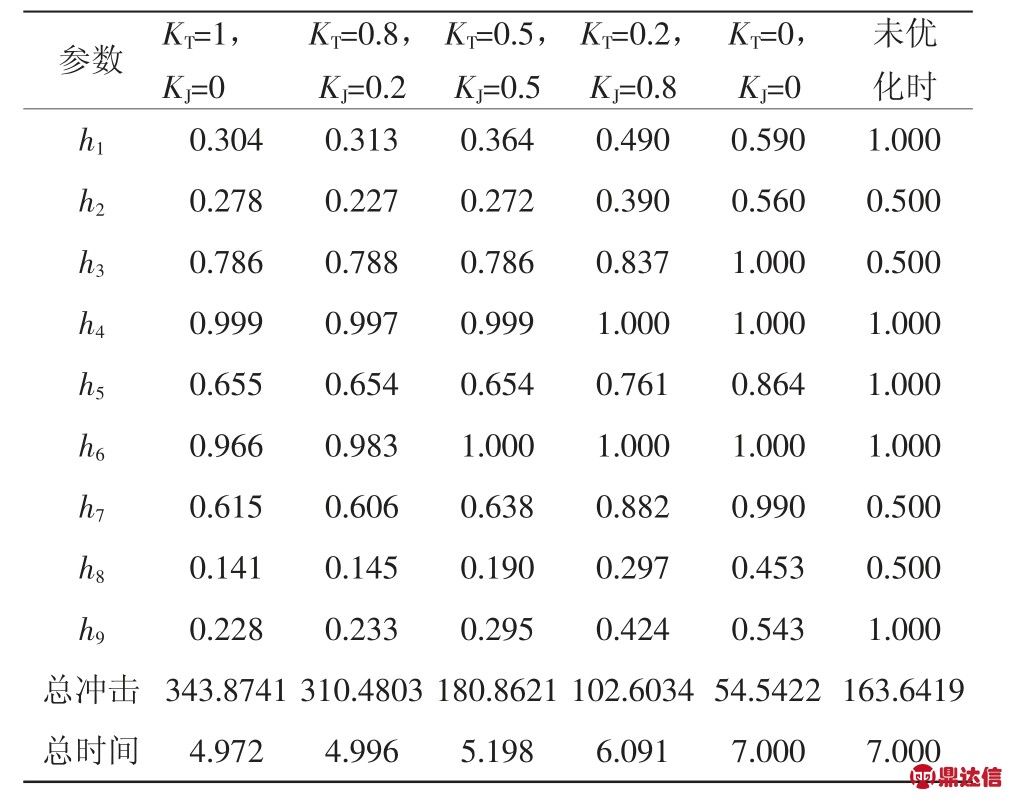
由表3可知在运行时间(7 s)相同的情况下,未经过优化的冲击为163.641,经过优化的冲击为54.5422,冲击减少了66.67%,因此在关节运动学约束的基础上增加加速度约束,有利于减少码垛机器人在运行过程中冲击。随着权重系数(KT:1→0,KJ:0→1)的逐阶变化,码垛机器人的工作时间由4.972 s增大到7 s;冲击由343.8741 减少到54.5422。
当KT=1时,只对动作时间进行了优化,工作效率虽然最高,但冲击也是最大的,这种情况下增大了码垛机器人的振动,降低了机器人的使用寿命;当KT=0时,只对冲击进行了优化,在工作效率方面会大大降低。为了达到综合最优,经过对表3数据的对比分析,本文取权重系数KT=KJ=0.5作为码垛机器人轨迹最优的取值。分别对KT=1、KJ=0,KT=0.5、KJ=0.5,KT=0、KJ=1时,进行各关节仿真。以第1、3关节为例,仿真结果如图2、图3所示。其中曲线1表示的是动作时间最优;曲线2表示的是动作时间和冲击两者综合最优;曲线3表示的是冲击最优。由图2,图3可以看出,码垛机器人在抓取和码放时速度均为零;在整个运动过程中各关节的角速度、角加速度、角加加速度均在规定的范围内,满足规划要求。
在KT=0.5、KJ=0.5时,运动时间和冲击达到综合最优,利用MATLAB编程对码垛机器人进行仿真试验,得到末端执行器运动轨迹,如图4所示。
由于码垛机器人在提升段和下降段的运行精度将直接影响工作的安全、顺利进行,在运行时间和冲击最优轨迹规划的情况下,考虑到码垛机器人系统误差对轨迹的影响,仿真得到轨迹误差,如图5所示。由图5可知,末端轨迹在X轴和Y轴方向轨迹误差均在1 mm的范围内,满足工作要求。
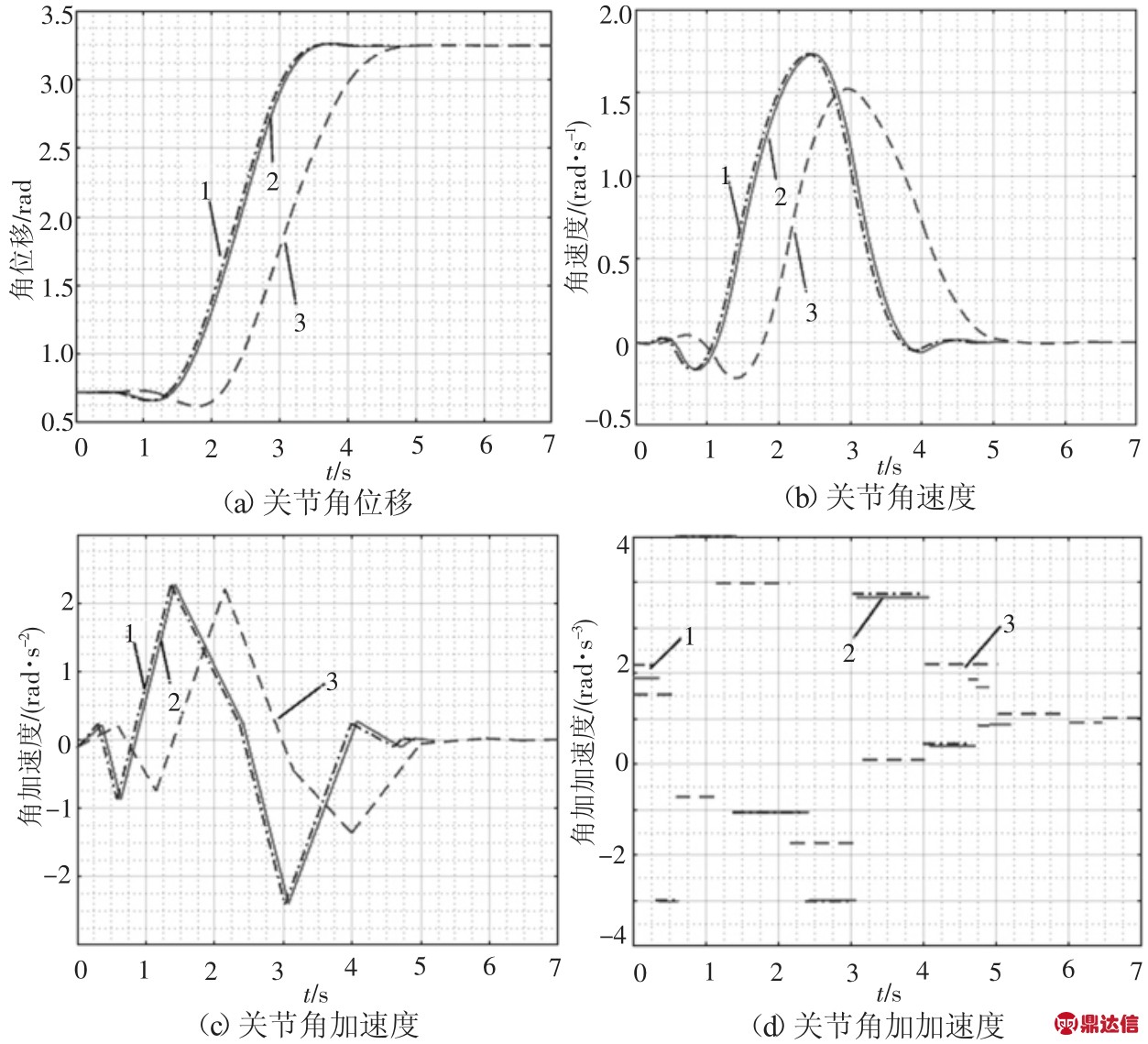
图2 关节1的最优轨迹
1.KT=1,KJ=0;2.KT=0.5,KJ=0.5;3.KT=0,KJ=1
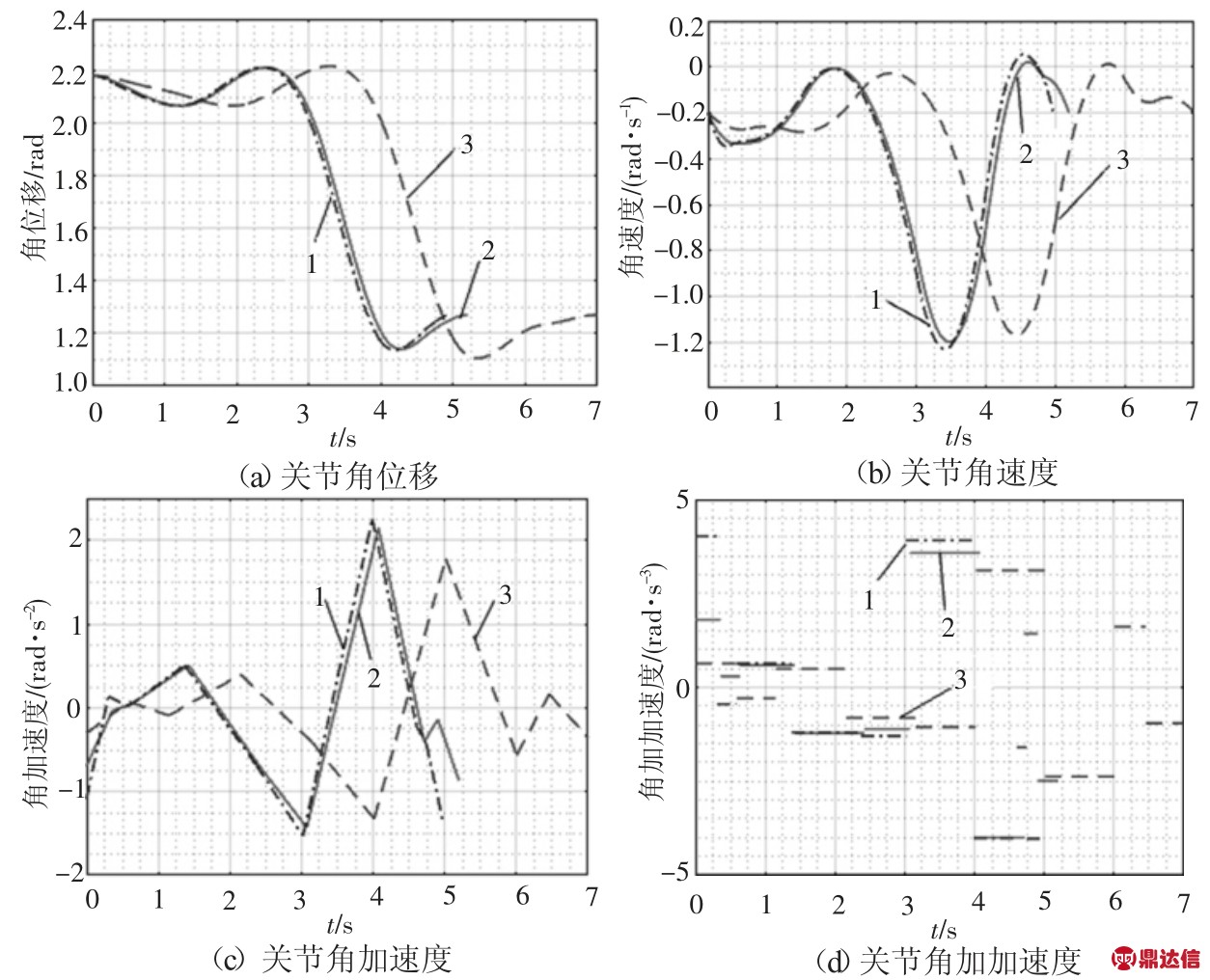
图3 关节3的最优轨迹
1.KT=1,KJ=0;2.KT=0.5,KJ=0.5;3.KT=0,KJ=1
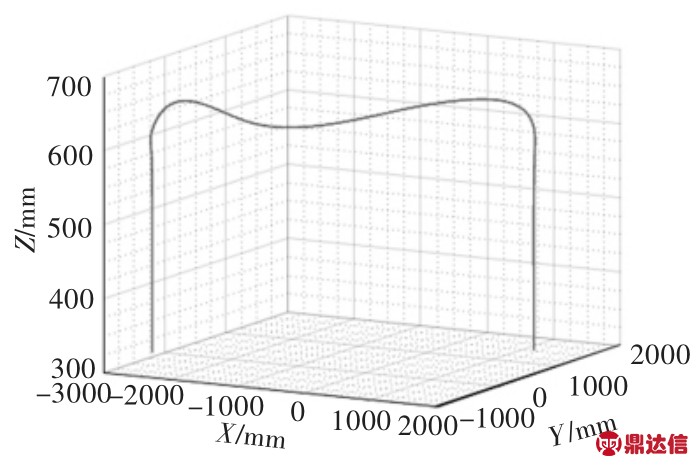
图4 末端运动轨迹
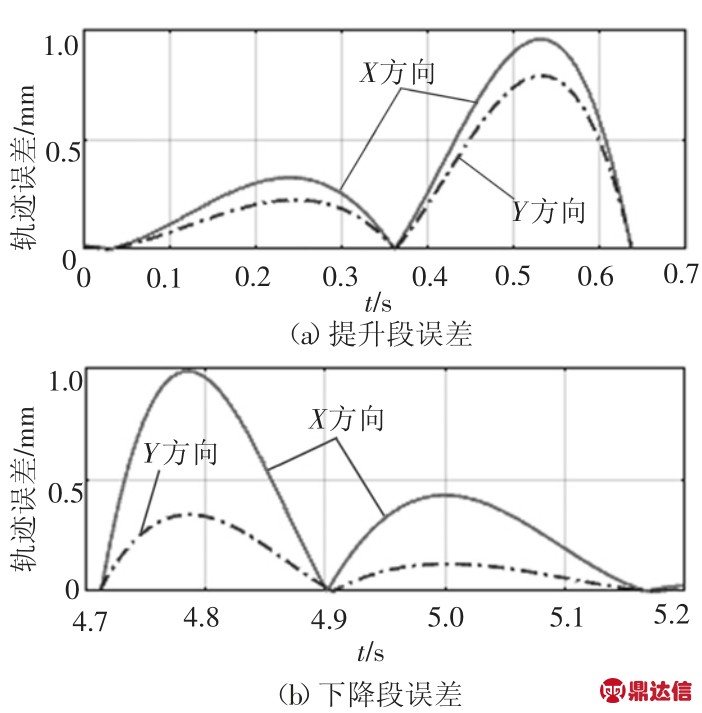
图5 轨迹误差
5 结论
1)针对装砖码垛机器人的工作特点,提出三次样条插值法对轨迹进行规划,保证了码垛机人在整个运动过程中各关节和末端运行平滑、连续;2)采用遗传算法对码垛机器人运动轨迹进行了优化,使得时间-冲击达到了综合最优;3)通过对运动轨迹的仿真,验证了轨迹规划、优化的合理性和可行性,可为进一步分析提供理论基础。