摘要:系统研究了聚乳酸微管的挤出成型工艺,获得了注气量、螺杆转速、牵引速度对微管外径、壁厚和椭圆度的影响规律。实验结果表明,注气量、螺杆转速、牵引速度对微管外径和壁厚的影响显著,且呈非线性变化。其中,牵引速度和螺杆转速相对于注气量对微管外径的影响程度较大;螺杆转速、牵引速度和注气量对微管壁厚的影响程度依次减弱。注气量直接影响微管截面的椭圆度,注气量越大,椭圆度越小,在注气量较小时,注气量增大1倍,椭圆度可降低68%。通过改变牵引速度、螺杆转速、注气量及其组合,可以达到采用1套模具顺序挤出4种规格聚乳酸微管的目的。
关键词:聚乳酸微管;挤出成型工艺;挤出模具;微管外径;微管壁厚
聚乳酸(PLA)以其良好的生物相容性、生物可降解性和可再生性,越来越多地应用于医疗器械领域。尤其是近年来随着可降解聚合物血管支架的兴起,对应用于血管支架的聚乳酸微管的尺寸及精度提出了更高的要求。因此,对聚乳酸微管的研究具有重要意义。然而,目前对聚乳酸的研究主要是对其进行改性[1~5],对聚乳酸微管的研究较少。Guerra等[6]通过浸渍涂层工艺制备了用于血管支架的聚乳酸微管,采用光纤激光对其进行雕刻,并研究了工艺参数对支架成型质量的影响。Grabow等[7]将聚乳酸与P4HB以一定比例混合,通过浸渍涂层工艺制备了聚乳酸微管,并雕刻成血管支架,研究了所雕刻支架的力学性能和降解性能。Arbeiter等[8]通过挤出成型的方法制备了用于制备血管支架的聚乳酸微管,并研究了热处理对微管力学性能的影响。可以看出,对聚乳酸微管的研究主要都集中于聚乳酸微管的成型方法,而对其挤出成型工艺研究得较少,尤其是针对挤出工艺参数对微管尺寸及形状精度的影响方面鲜有研究。
本文针对聚乳酸微管的挤出成型,设计并改进了聚乳酸微管挤出模具。通过挤出成型工艺实验,研究了挤出工艺参数对聚乳酸微管截面尺寸及形状精度的影响规律。通过改变挤出成型工艺参数及其组合,试图以一套模具挤出成型出不同规格的聚乳酸微管。
1 聚乳酸微管挤出模具设计
1.1 聚乳酸毛细管流变实验
为了获得聚乳酸的流变性能,首先对其进行流变测试。实验设备为英国Malvern公司的Rosand-RH7D双料筒毛细管流变仪,选择直径为0.5 mm长口模及相应的零口模。实验前先将聚乳酸(NatureWorks 4032D)原料置于烘料箱中烘干4 h,烘料温度79 ℃,分别测试其在190 ℃、200 ℃、210 ℃、220 ℃时的流变特性。
实验结果如Fig.1所示。通过流变特性曲线可以看出,聚乳酸材料的剪切黏度(η)随着剪切速率的增大而减小,属于非牛顿流体。剪切黏度随着剪切速率增大呈指数下降,但随着剪切速率的继续增大,剪切黏度下降较为平缓。剪切黏度随温度的升高而降低,当温度高于200 ℃时,不同温度下的剪切黏度比较接近。因此,在模具设计时,可按聚乳酸在200 ℃时的黏度特性进行计算。将聚乳酸在200 ℃时测得的流变数据与非牛顿流体的幂律函数方程(式(1))进行拟合,得到流体稠度K=23.79 kPa,非牛顿指数n=0.306。
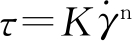
(1)
式中:τ——剪切应力;K——流体稠度;剪切速率;n——非牛顿指数。
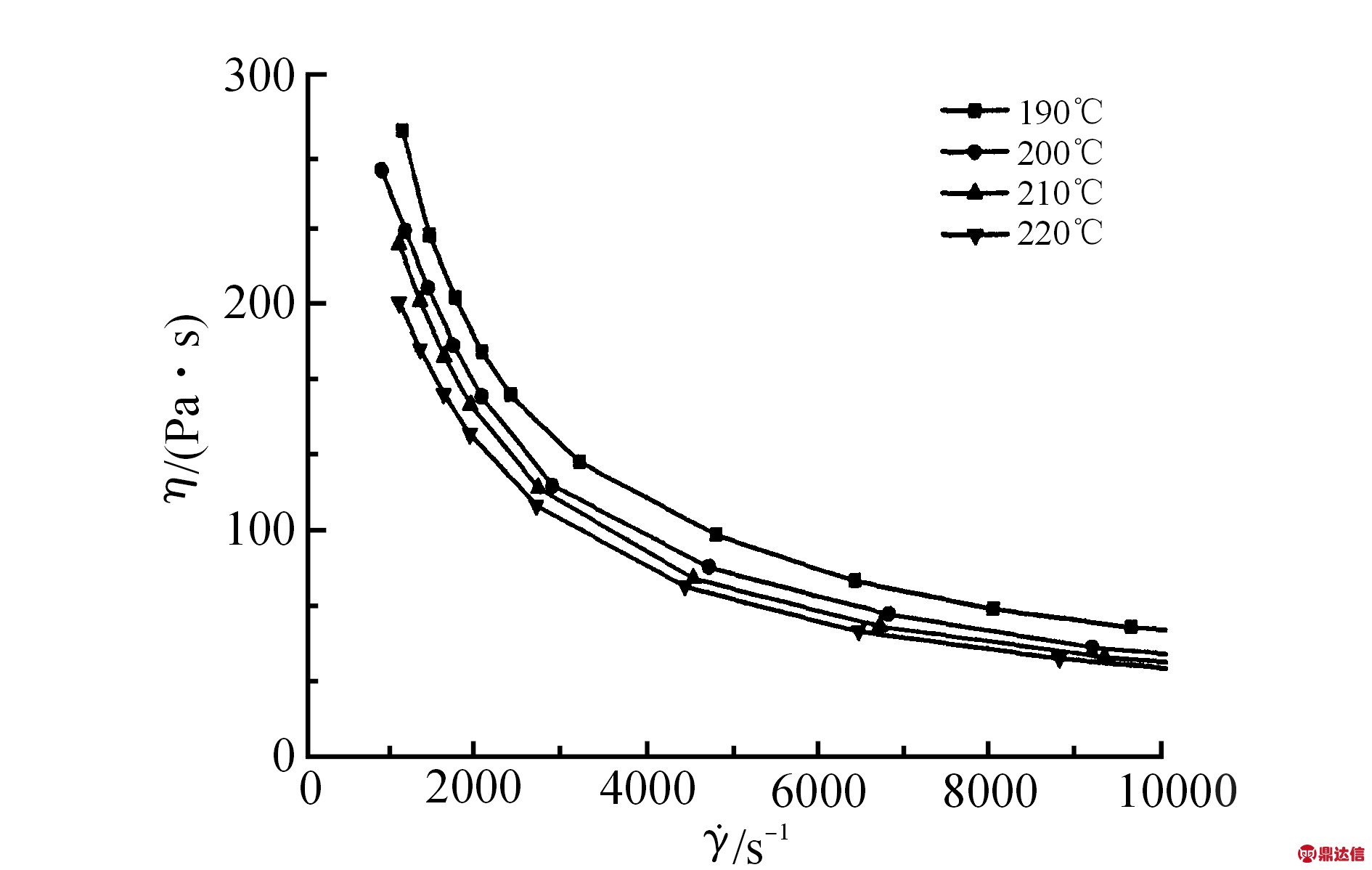
Fig.1 Rheological characteristic curves of PLA
1.2 聚乳酸微管设计要求
聚乳酸微管截面为圆环形,4种微管的规格(外径×壁厚)分别为1.00×0.07 mm、1.50×0.10 mm、2.00×0.15 mm和2.50×0.15 mm。要求壁厚均匀度G>90%,椭圆度Y0<3.0%。其中壁厚均匀度根据式(2)计算。
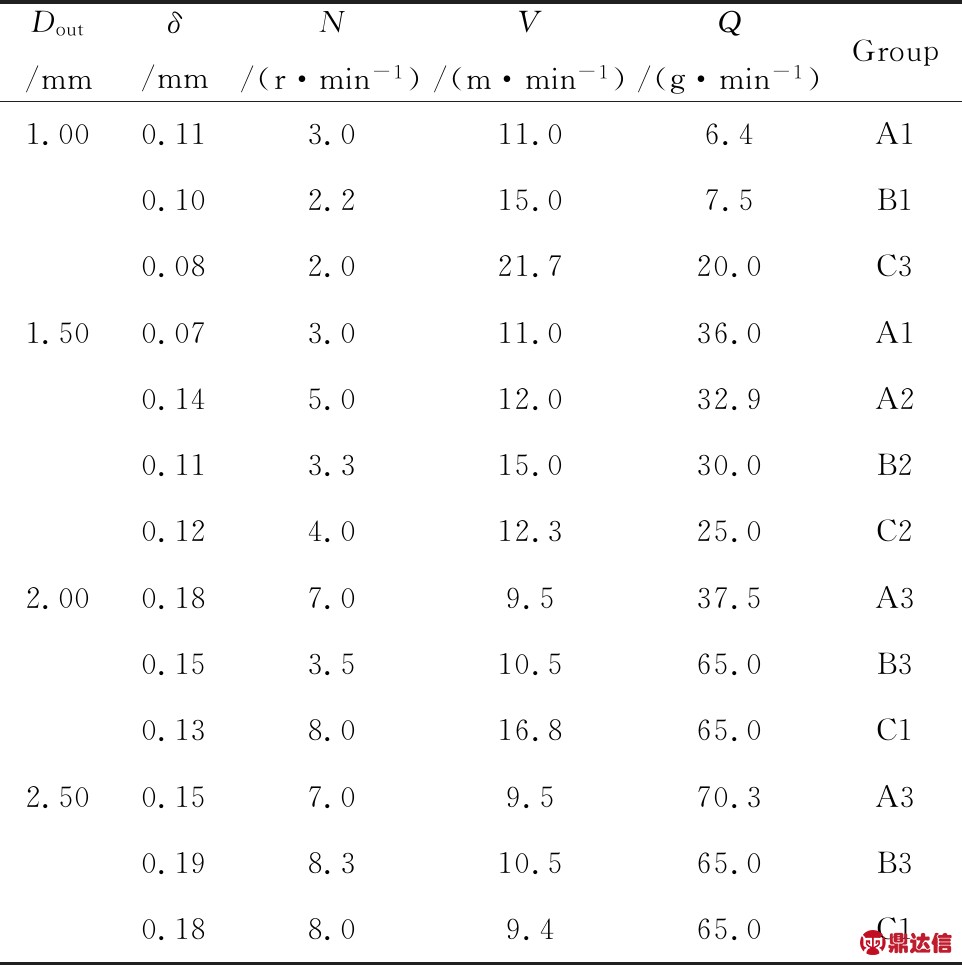
(2)
式中:分别为壁厚标准偏差和壁厚均值,可表示为:

(3)
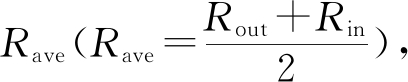
(4)
式中:δi——微管横截面周向上每一点的壁厚测量值;k——测量点数量。
椭圆度根据式(5)计算:
Y0=2(Dmax-Dmin)/(Dmax+Dmin)
(5)
式中:Y0——椭圆度;Dmax、Dmin——分别表示微管的最大外径和最小外径。
1.3 聚乳酸微管挤出模具设计
挤出模具采用直通式挤出结构。因所设计微管尺寸微小,引入微注气系统,注气方向与熔体流动方向呈90°,其结构图如Fig.2所示。成型段口模内径、芯模外径与成型段长度直接影响微管尺寸和成型质量,因此,本文对这3个参数进行设计。
1.3.1 成型段口模内径和芯模外径计算:成型段口模内径和芯模外径对挤出的微管尺寸至关重要。口模内径或芯模外径过大或过小均无法通过调整挤出工艺获得最终的尺寸。对于微小尺度下口模内径和芯模外径尚无准确计算公式,通常是结合材料的拉伸比并根据经验来确定,拉伸比按式(6)计算:
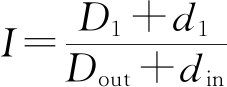
(6)
式中:I——拉伸比;D1、d1——分别是口模内径和芯模外径;Dout、din——分别是微管外径和内径。
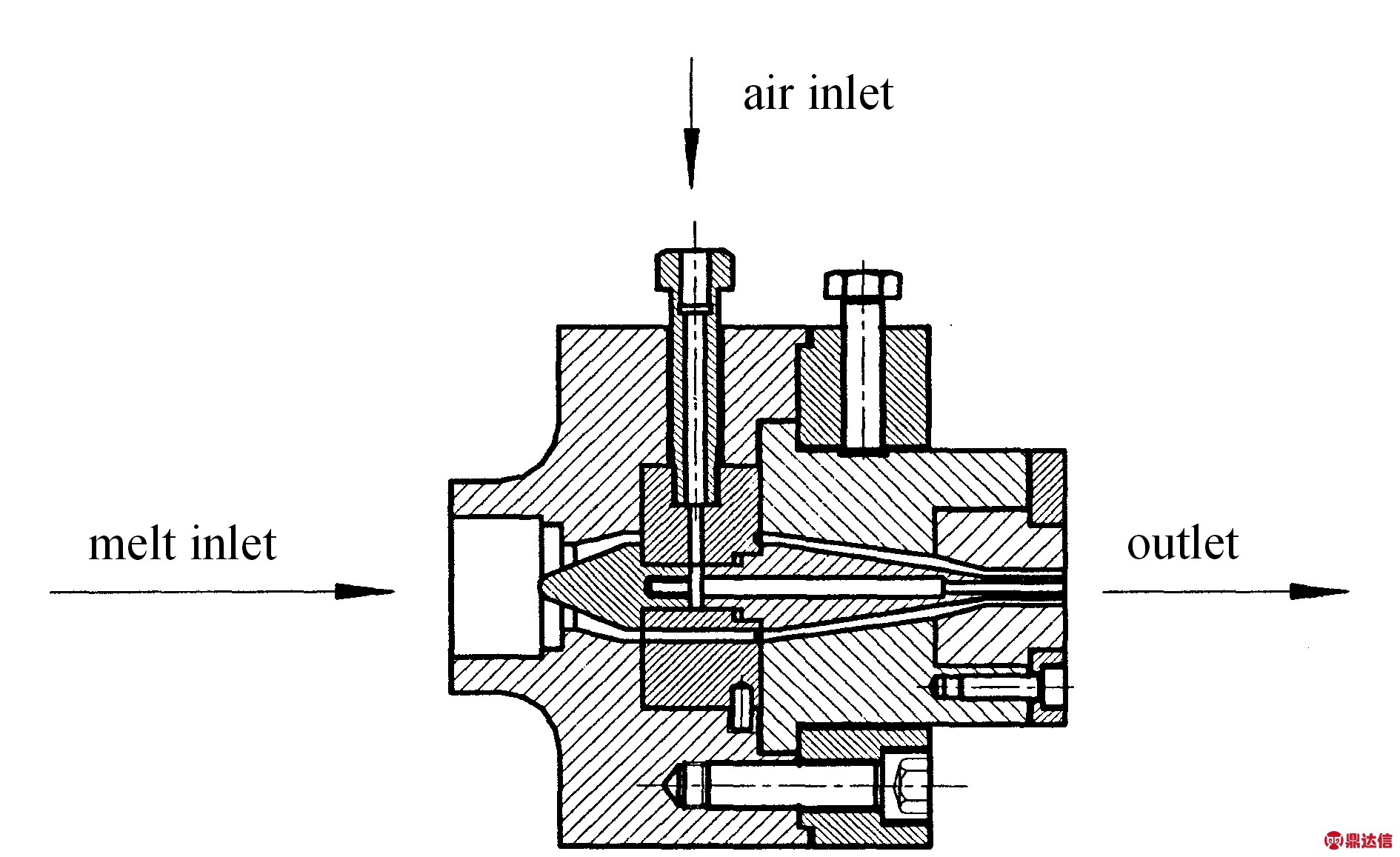
Fig.2 Structure of the in-line micro tube extrusion die
通过前期实验,聚乳酸的拉伸比范围为1.1~4.8。根据经验初步将口模内径确定为3.40 mm,芯模外径确定为3.00 mm。达到微管尺寸设计要求的所需最大拉伸比小于3.44,最小拉伸比大于1.36,在材料的允许范围内,可以满足挤出成型工艺要求。
1.3.2 成型段长度计算:口模成型段长度对微管的质量和挤出效率有显著的影响。成型段太短,挤出胀大严重,甚至无法挤出微管,成型段太长,则模具内挤出压力过大,熔体在模具内停留时间过长,易分解或降解。
成型段长度可根据狭缝型口模理论来计算。
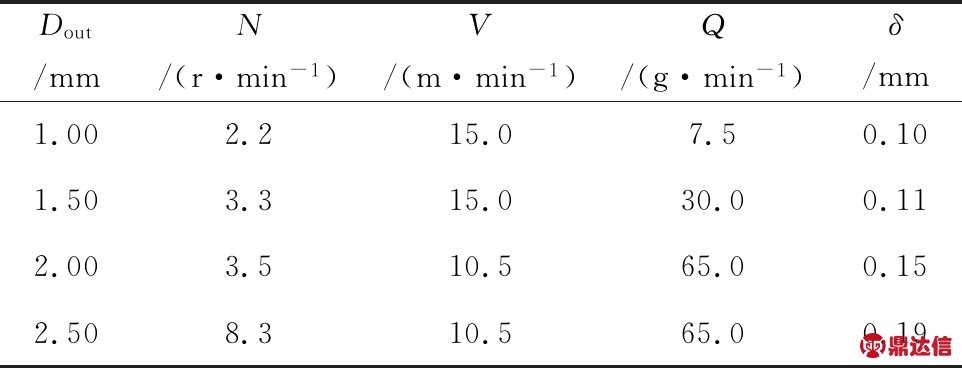
(7)
式中:qv——体积流率;ΔP——压力降;L——成型段长度;K——流体稠度;n——非牛顿指数;W——狭缝宽度;H——狭缝厚度。
由式(7)可得到狭缝型口模成型段长度。
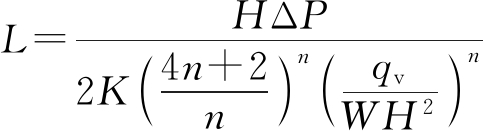
(8)
通常,口模必须满足W/H,方可看作是狭缝型口模。
对于所设计的微管挤出模具,H为成型段口模与芯模的间隙,W为成型段口模与芯模构成圆环的平均周长,即:
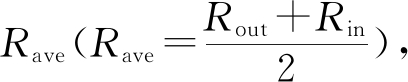
(9)
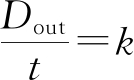
(10)
式中:D1、d1——分别为成型段处口模内径和芯模外径。通过式(9)和式(10)得到H=0.2 mm,W=10.05 mm,W/H=50.25>10,故可采用狭缝型口模理论计算。
上述K和n是根据聚乳酸在200 ℃时的流变属性获得,分别为23.79 kPa、0.306,ΔP和qv可通过实验获得,分别为14.3 MPa、129.6 mm3/s。将W、H、n、K、ΔP、qv代入式(8),得到L≈5.00 mm。
2 聚乳酸微管挤出成型工艺实验
2.1 实验设备和方法
挤出成型实验设备是美国戴维斯标准公司的HPE-100H单螺杆挤出机系统和所设计的挤出模具(Fig.3)。微管尺寸测量采用苏州欧卡精密光学仪器有限公司的VTM-3020F工具显微镜,测量精度±0.001 mm。气体流量控制采用深圳弗罗迈测控系统有限公司的FLC-100D气体质量流量控制器,单位g/min。
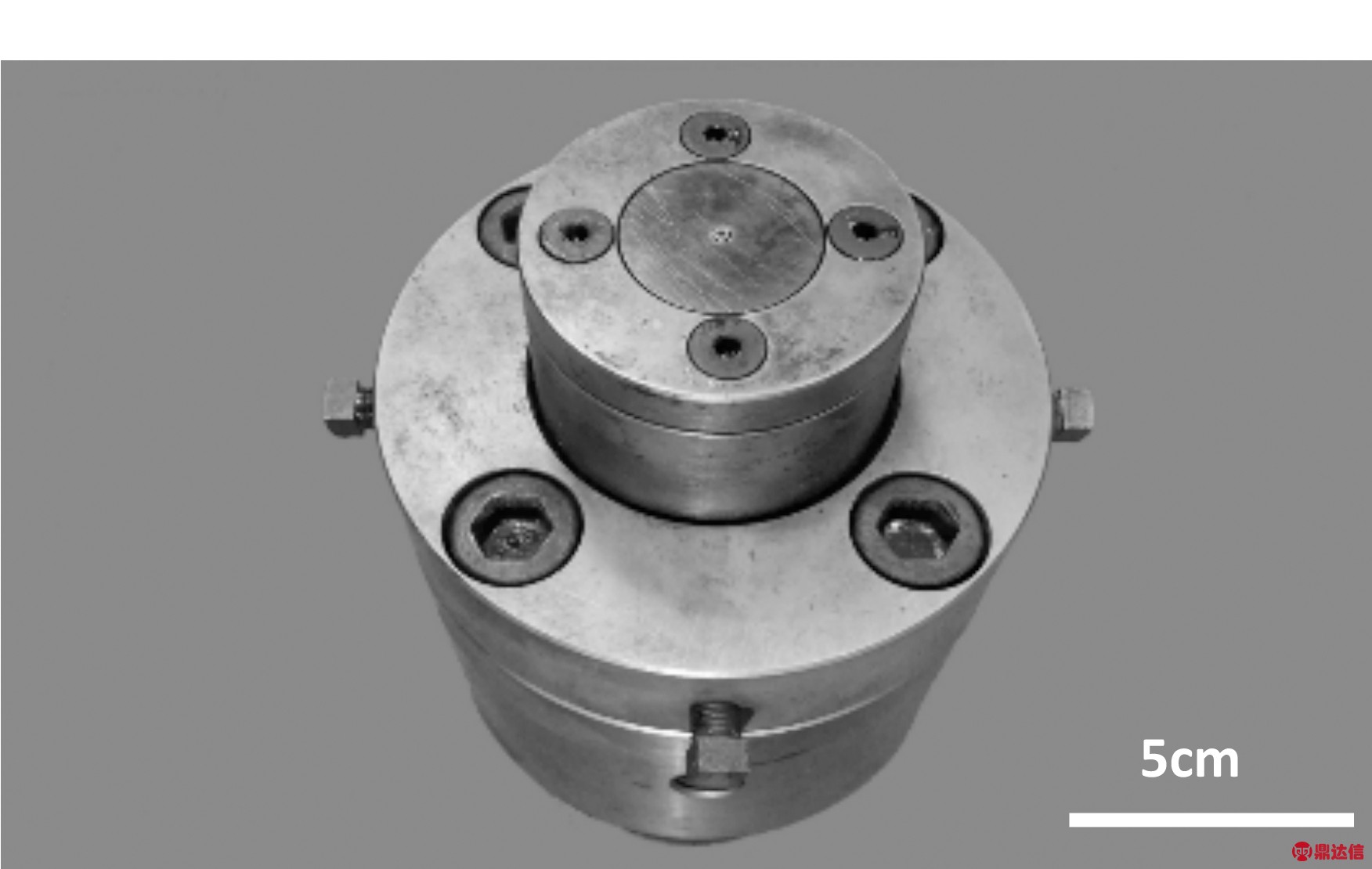
Fig.3 Extrusion die
实验前先将聚乳酸(NatureWorks 4032D)原料放置于烘料箱烘干4 h,烘料温度为79 ℃。根据聚乳酸的物料特性,挤出机料筒温度从入口到出口依次设置为180 ℃、190 ℃、195 ℃。挤出成型的微管离开口模后进入常温水箱冷却定型。根据前期挤出工艺实验和流变实验可知,微管外径、壁厚及椭圆度受模具温度和真空度影响较小,故真空度设为0,模具温度设置为200 ℃。微管外径和壁厚测量方法是在微管横截面的圆周上均匀选取16个点,并通过工具显微镜对每一点的外径和壁厚进行测量,最后取平均值。微管壁厚均匀度按式(2)计算,微管椭圆度按式(5)计算。
通过初步实验,确定了注气量(Q)的取值范围为5.0~75.0 g/min,螺杆转速(N)的取值范围为1.0~9.0 r/min,牵引速度(V)的取值范围为9.0~31.0 m/min。
2.2 实验结果与讨论
2.2.1 注气量对微管外径、壁厚和椭圆度的影响:挤出成型时,以一定速率注入气体至微管内腔,以防止熔体离开模具后在重力作用下发生变形而粘连在一起。取3组不同的螺杆转速和牵引速度,使其能够涵盖设计微管的所有外径尺寸,每组参数及所对应注气量的取值范围如Tab.1所示。
Tab.1 Ranges of gas flow rates and combinations of the other process parameters
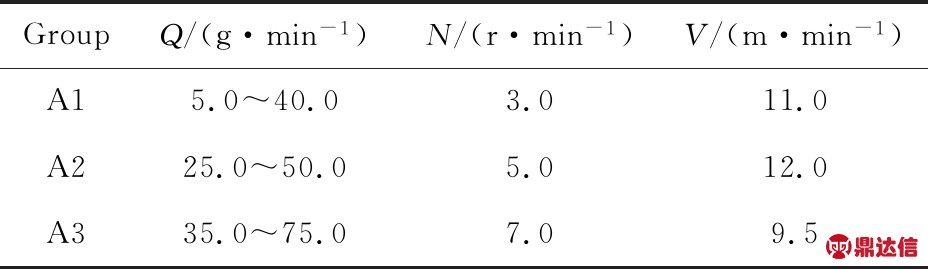
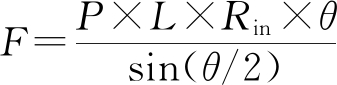
Fig.4 Relationships between micro tube outer diameter and wall thickness with gas flow rate
微管外径和壁厚随注气量的变化如Fig.4所示。其中,直径最大误差<±0.05 mm,壁厚最大误差<±0.02 mm。可以看出,随着注气量增大,微管外径增大,壁厚减小,尤其在注气量较小时,变化较为显著,以A1组工艺参数为例,在注气量较小时,如由10 g/min增加1倍,直径增加了19%,壁厚减小了20%。直径和壁厚的变化率随着注气量的增大逐渐降低,呈非线性。
为分析注气量对微管外径和壁厚的影响,取弧度(θ)范围内的型坯,其变形前内半径为Rin,外半径Rout,壁厚为h,宽度为L,平均内半径为气体作用于型坯的压力为P,截面拉力为F,如Fig.5所示。

Fig.5 Parison subjected to internal pressure
由于型坯在径向受力平衡,可以得到:
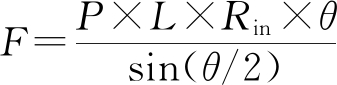
(11)
则型坯截面上的应变为:
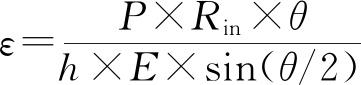
(12)
式中:ε——型坯截面上的应变;E——型坯的弹性模量。假设变形后外半径为内半径为
平均内半径为
壁厚为h′,则:

(13)
根据式(12)和式(13),得到:

(14)
可以看出,微管的平均内半径随内腔压力的增大而增大。同时,因内腔压力与注气量呈正相关,因此,微管外径随注气量的增大而增大。此外,假设型坯变形前后体积不变,则

(15)
将代入式(15),得到
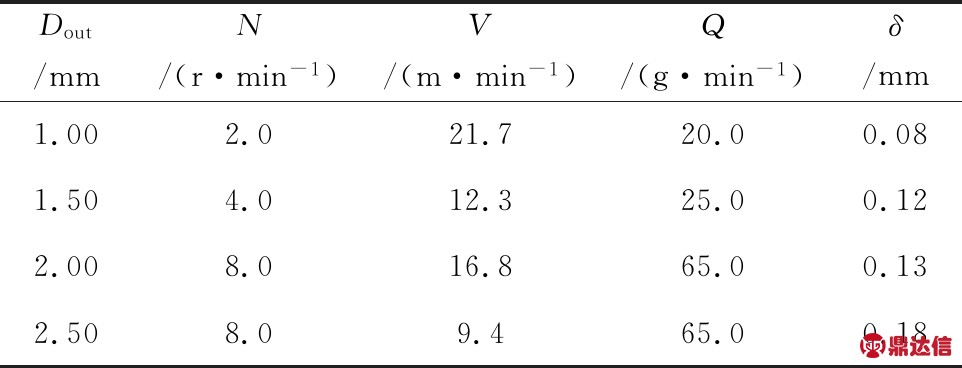
(16)
因随着内腔压力的增大,则壁厚逐渐减小。因此,壁厚随注气量的增大而减小。直径和壁厚的变化率随着注气量的增大呈非线性变化是因为随着微管外径逐渐变大,熔体沿周向的分子取向程度增强,分子间的作用力加强,从而抑制了注气压力产生的变形,结果导致微管外径和壁厚的变化率随着注气量的增大逐渐降低。
以A1组工艺参数为例分析注气量对微管椭圆度的影响,二者关系如Fig.6所示。可以看出,椭圆度随着注气量的增大而降低,开始时非常显著(注气量由5 g/min增加到10 g/min,椭圆度降低了68%),达到一定值后椭圆度稳定在2.0%左右。这是因为当注气量较低时,型坯内部气体压力不足以抵抗由重力引起的变形,则微管变形严重,对椭圆度的影响显著。随着注气量增大至型坯内压足以抵抗重力变形后,则对椭圆度的影响较小。
后续挤出工艺实验均应保证注气量足够,通过前期挤出工艺实验可知,在注气量足够的情况下,螺杆转速和牵引速度对椭圆度影响很小。
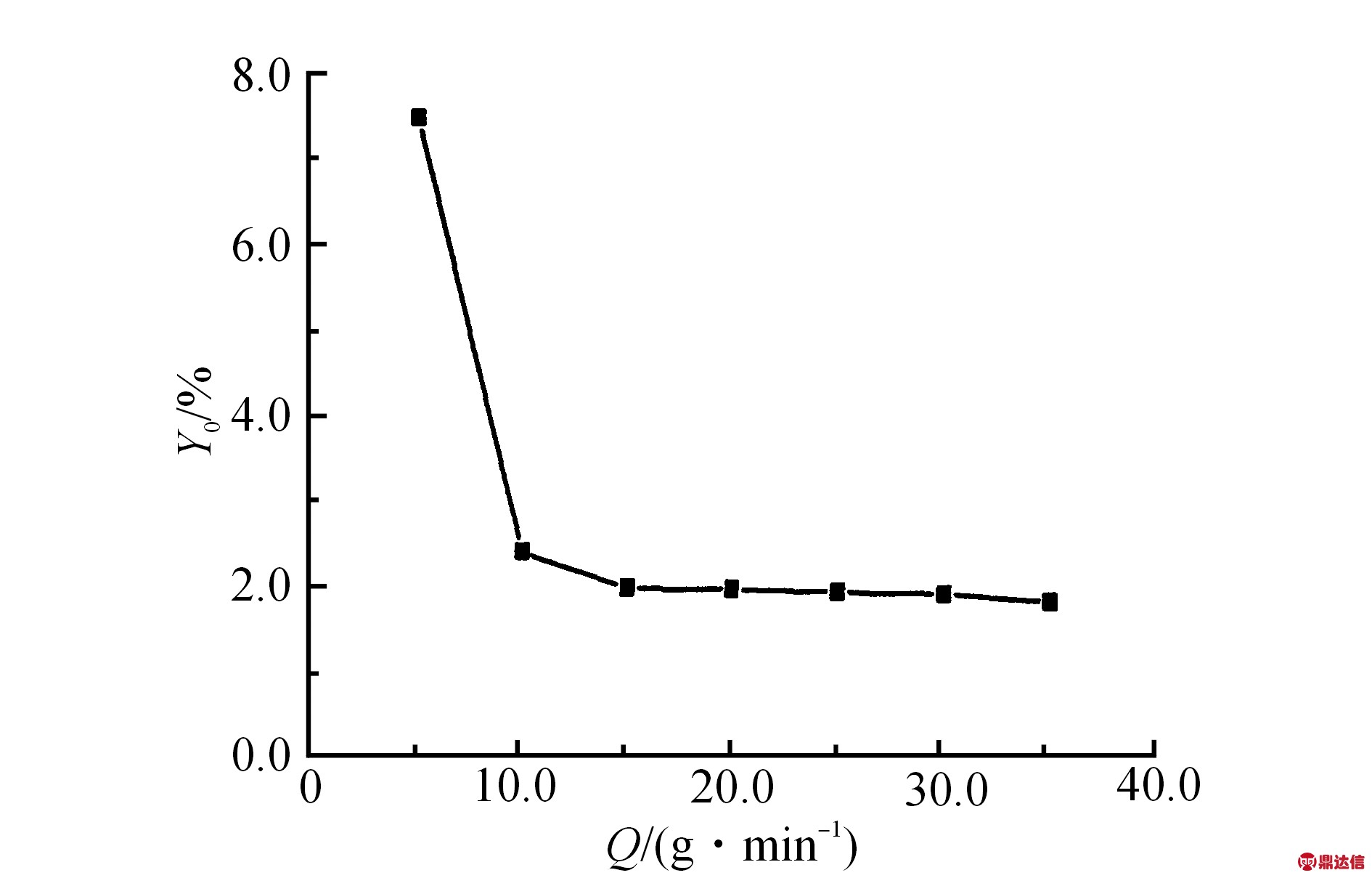
Fig.6 Relationship between micro tube ovality with gas flow rate
根据微管外径和壁厚随注气量的变化曲线可以获得微管外径为1.00 mm、1.50 mm、2.00 mm、2.50 mm所对应的工艺参数组合与相应的壁厚,如Tab.2所示。
Tab.2 Combinations of extrusion process parameters and the wall thickness corresponding to the micro tubes with four kinds of outer diameter
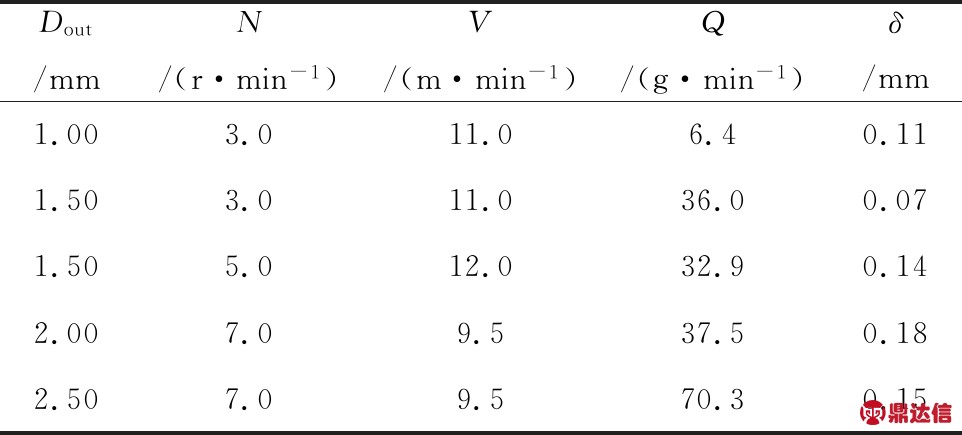
2.2.2 螺杆转速对微管外径和壁厚的影响:挤出机通过螺杆旋转将熔体挤出,因此螺杆转速对熔体体积流率有显著影响。取3组不同的牵引速度和注气量参数,以使其能够涵盖设计微管的所有外径尺寸,每组参数与所对应的螺杆转速的取值范围如Tab.3所示。
Tab.3 Ranges of screw speeds and combinations of the other process parameters
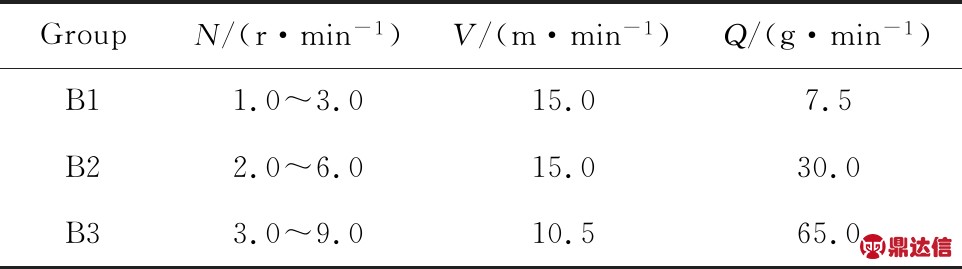
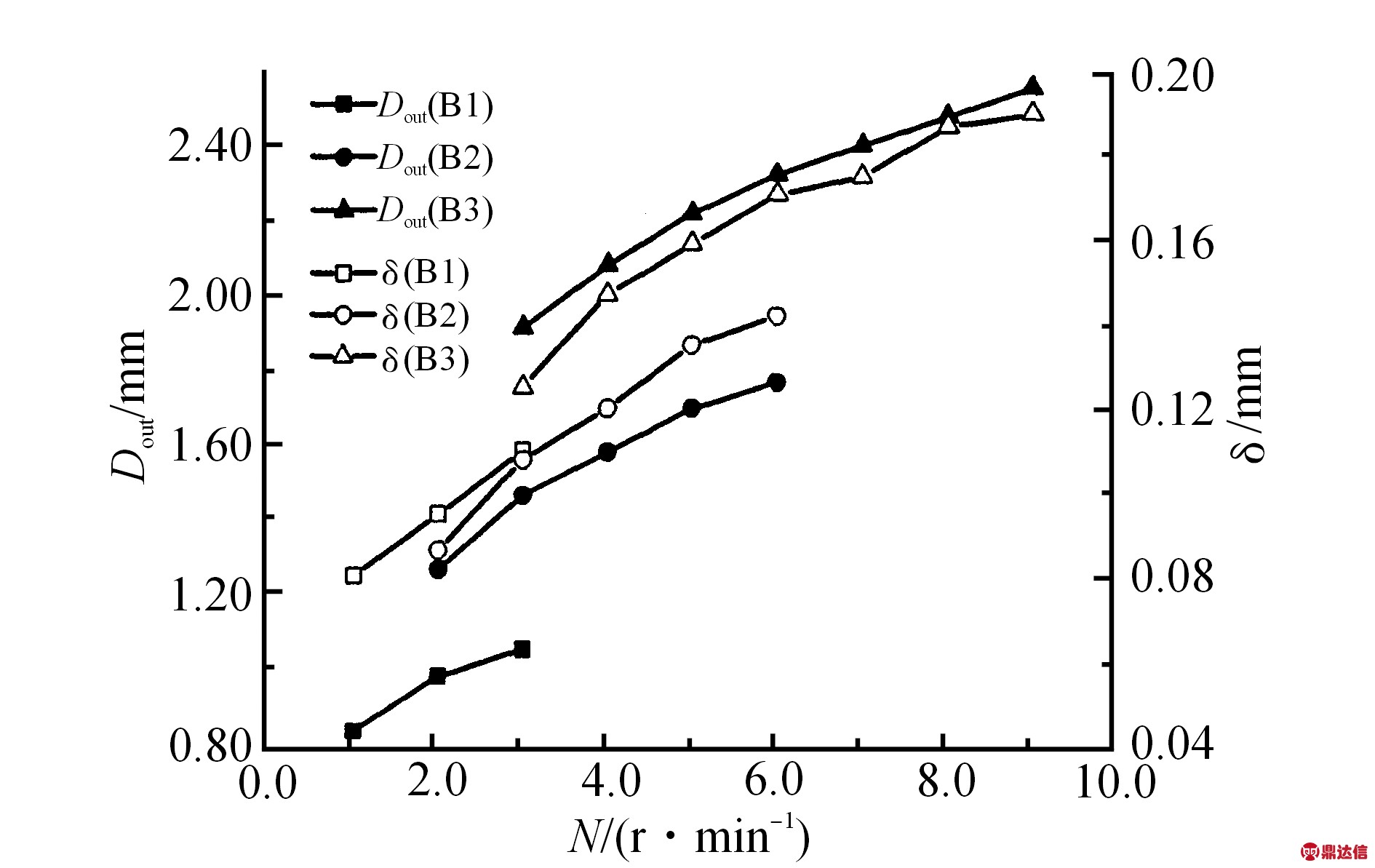
Fig.7 Relationships between micro tube outer diameter and wall thickness with screw speed
微管外径和壁厚随螺杆转速的变化关系如Fig.7所示。其中,直径最大误差<±0.03 mm,壁厚最大误差<±0.01 mm。可以看出,螺杆转速增大,微管的外径和壁厚均增大,在螺杆转速较小时,变化较为显著,以B2组工艺参数为例,螺杆转速由2 r/min增加1倍,直径增加24%,壁厚增大50%。随着螺杆转速的增大,微管外径和壁厚增大趋势逐渐变缓,呈非线性。微管外径和壁厚随着螺杆转速的增大而增大,其原因主要有两方面:一方面是螺杆转速增大则熔体体积流率增大,进而导致剪切速率增大,对于假塑性流体,通常在挤出过程中,熔体在破裂前离模膨胀率随剪切速率的增大而增大,在发生离模膨胀时,外径向外扩张,内径向内扩张[9],故其外径和壁厚随着螺杆转速的增大而增大。另一方面,根据流体连续性定理:
V0×S0=V×S
(17)
式中:V0、S0——分别为定型型腔内熔体流动速度和型腔截面积;V、S——分别为牵引速度和牵引后微管截面积。螺杆转速增大意味着V0增大,而S0和V不变,则S增大。S增大是内壁向内扩张和外壁向外扩张共同作用的结果,故微管外径和壁厚增大。
微管外径和壁厚增大速率逐渐变缓,是因为随着螺杆转速增大,熔体的剪切速率增大,导致剪切变稀,熔体变稀使熔体的体积流率增大速率变缓,因此微管外径和壁厚的增大速率逐渐变缓。该观点可通过毛细管流变实验验证。
毛细管口模体积流率可以表示为[10]:
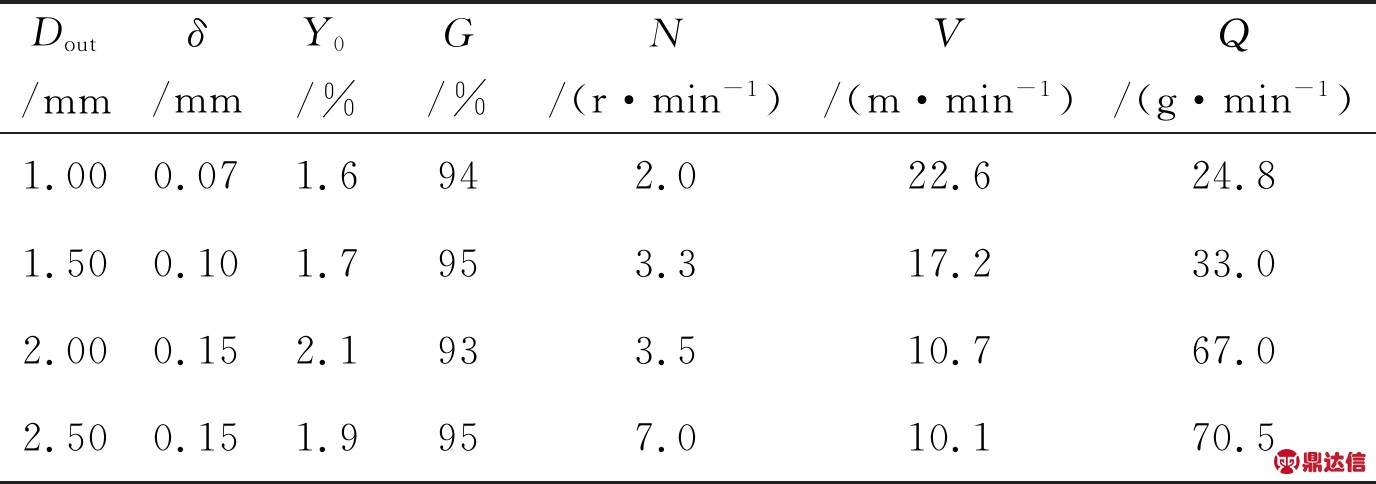
(18)
式中:qv——体积流率;n——非牛顿指数;剪切速率;Rd——毛细管口模半径。
已知毛细管口模半径Rd=0.25 mm,通过提取熔体温度为200 ℃时聚乳酸的流变实验数据,可以得到不同压缩速率下的n和代入公式,即可求出体积流率。获得的剪切速率与体积流率曲线如Fig.8所示,可以看出,体积流率随剪切速率的增大而增大,同时增大趋势逐渐变缓,验证了上述观点。
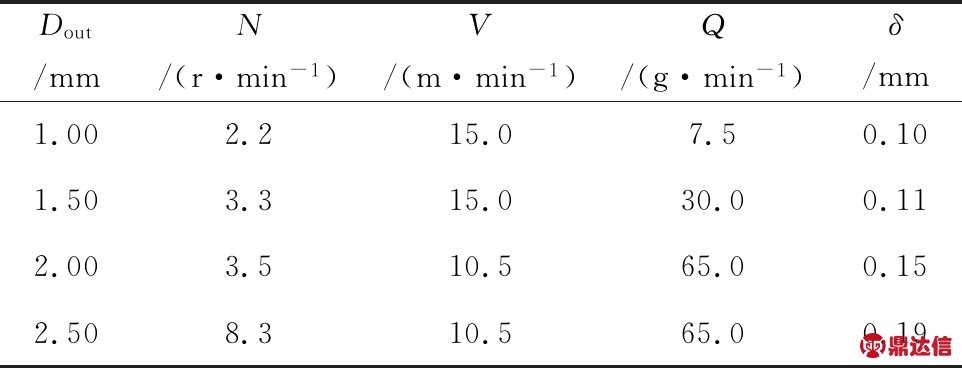
Fig.8 Relationship between corrected shear rate and volume flow rate
根据微管外径和壁厚随螺杆转速的变化曲线可以获得微管外径为1.00 mm、1.50 mm、2.00 mm、2.50 mm所对应的工艺参数组合与相应的壁厚,如Tab.4所示。
Tab.4 Combinations of extrusion process parameters and the wall thickness corresponding to micro tubes with four kinds of outer diameter
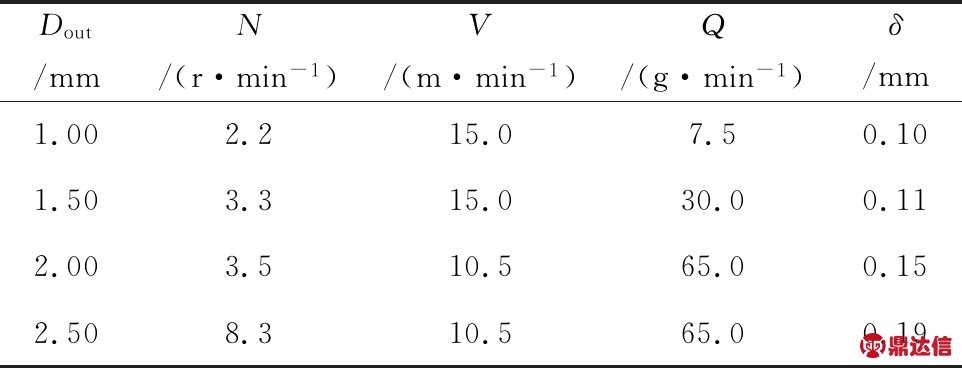
2.2.3 牵引速度对微管外径和壁厚的影响:微管在牵引机上、下夹板的作用下使熔体挤出后沿着挤出方向运动。取3组不同的螺杆转速和注气量参数以使其能够涵盖设计微管的所有外径尺寸,每组参数与所对应的牵引速度的取值范围如Tab.5所示。
Tab.5 Ranges of pulling speeds and combinations of the other process parameters
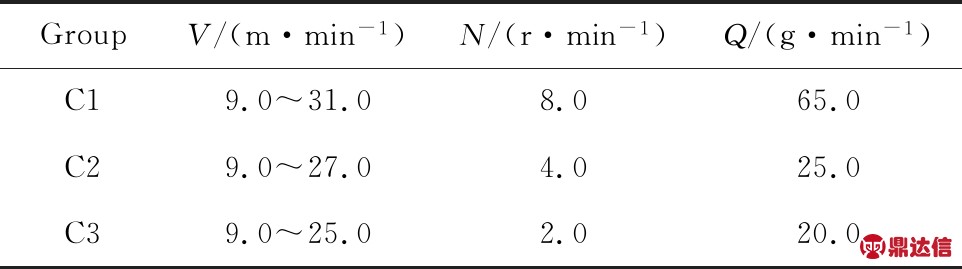
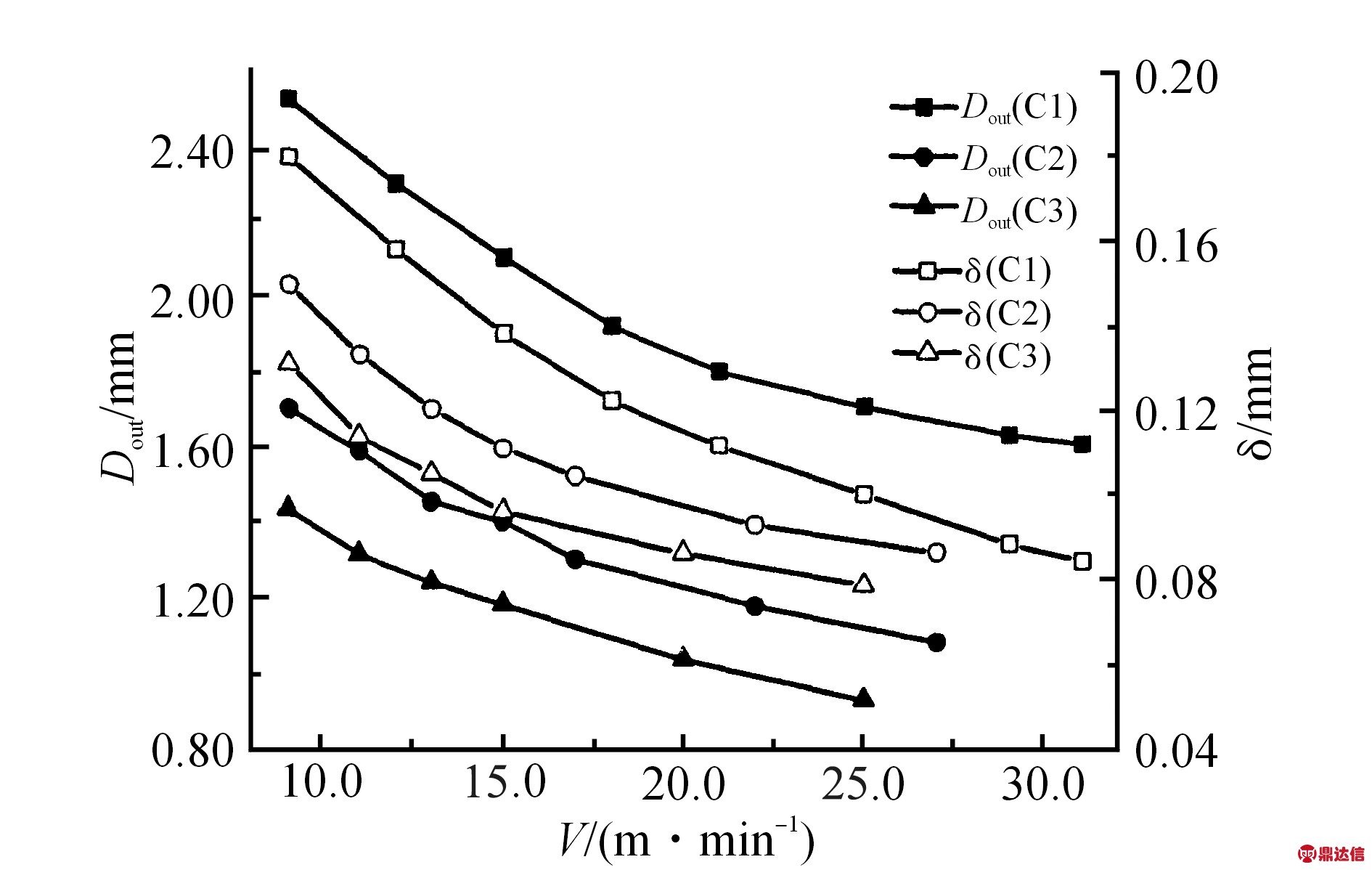
Fig.9 Relationships between micro tube outer diameter and wall thickness with pulling speed
微管外径和壁厚随牵引速度的变化关系如Fig.9所示。其中,直径最大误差<±0.03 mm,壁厚最大误差<±0.01 mm。可以看出,微管的外径和壁厚均随牵引速度的增大而减小,开始较为显著,以C1组工艺参数为例,牵引速度由9.0 m/min增加1倍,直径减小24%,壁厚减小36%。随着牵引速度继续提高,微管外径和壁厚降低较为平缓。
微管外径和壁厚与牵引速度的关系可通过质量守恒定律进行分析,即
W=ρ×S×V
(19)
式中:W——熔体质量流动速率;ρ——熔体密度;S——型坯截面积;V——牵引速度。根据式(19)可以得到:

(20)
因微管在拉伸过程中管材外径及壁厚满足公式[11]:
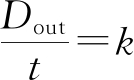
(21)
式中:k——常数。将式(21)代入式(20),得到:
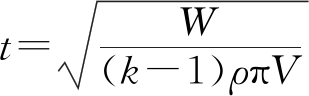
(22)
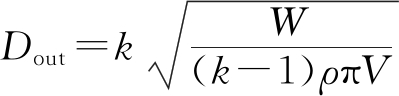
(23)
根据式(22)和式(23)可以看出,Dout和t均与V-1/2呈正相关。因此,直径和壁厚随着牵引速度的增大而减小,且呈非线性。此外,因型坯离开口模时发生离模膨胀,在牵引力作用下,首先要将离模膨胀引起的变形“拉直”,因此在低牵引速度下,微管外径和壁厚减小较为明显,随着牵引速度的继续提高,离模膨胀引起的变形逐渐被弱化甚至消失,因此导致微管外径和壁厚降低速率减小。
根据外径和壁厚随牵引速度的变化曲线,可以获得微管外径为1.00 mm、1.50 mm、2.00 mm、2.50 mm所对应的工艺参数组合与相应的壁厚,如Tab.6所示。
Tab.6 Combinations of extrusion process parameters and wall thickness corresponding to micro tubes with four kinds of outer diameter
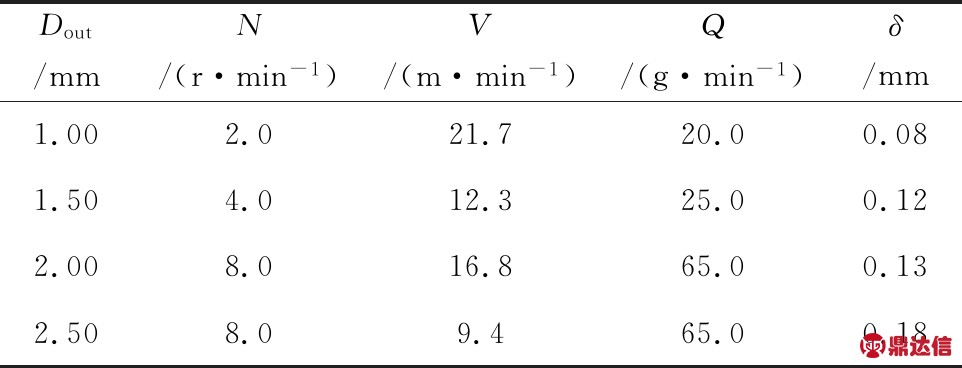
Tab.7 Combinations of process parameters corresponding to four kinds of outer diameter of micro tubes
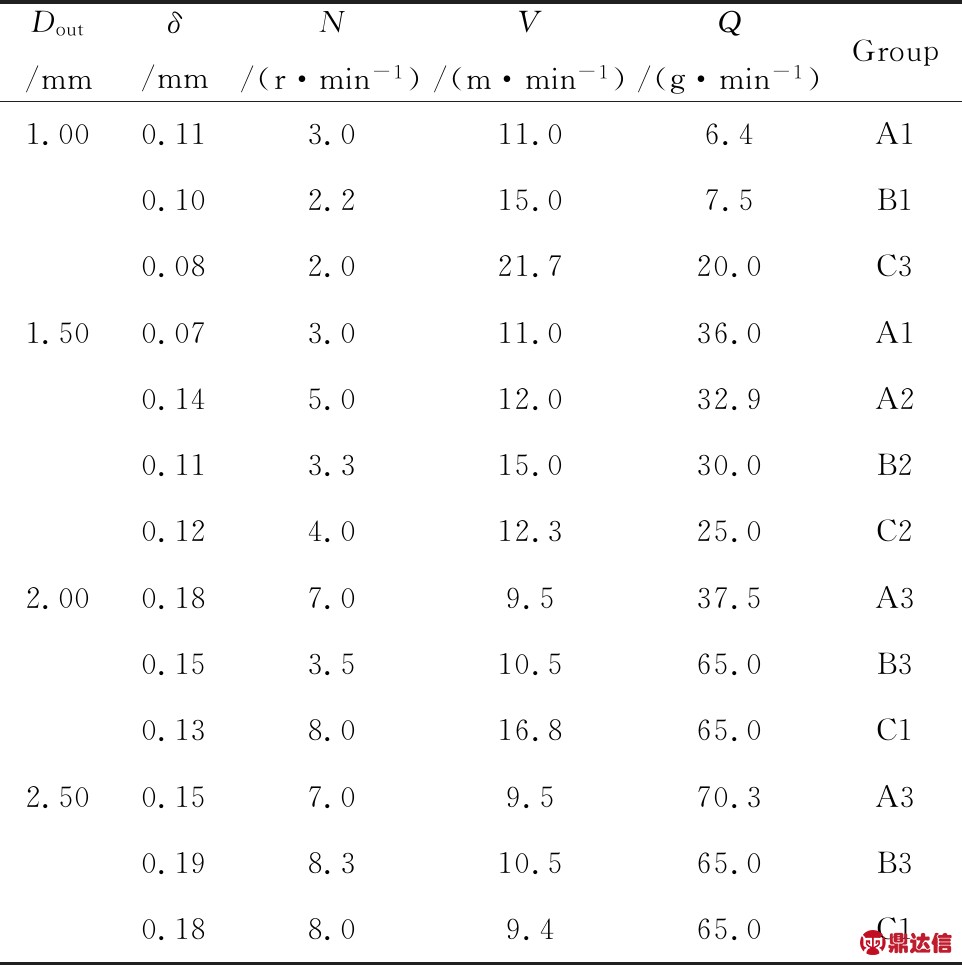
综上,可以得到不同微管外径对应的工艺参数组合与相应的壁厚,如Tab.7所示。针对所设计微管的尺寸规格,选择最接近设计尺寸规格所对应的工艺组编号,结合工艺参数对微管外径、壁厚的影响规律,适当调整参数值,可快速确定成型出设计微管的工艺参数组合。
以挤出成型外径1.00 mm、壁厚0.07 mm的微管为例,可选择C3工艺参数组合,适当增大注气量以降低壁厚,同时提高牵引速度以保证微管外径保持在1.00 mm。
最终成型出的微管尺寸规格、形状精度与相应的工艺参数组合如Tab.8所示,微管截面如Fig.10所示。
Tab.8 Dimensions and shape precision of the micro tubes and corresponding combinations of process parameters
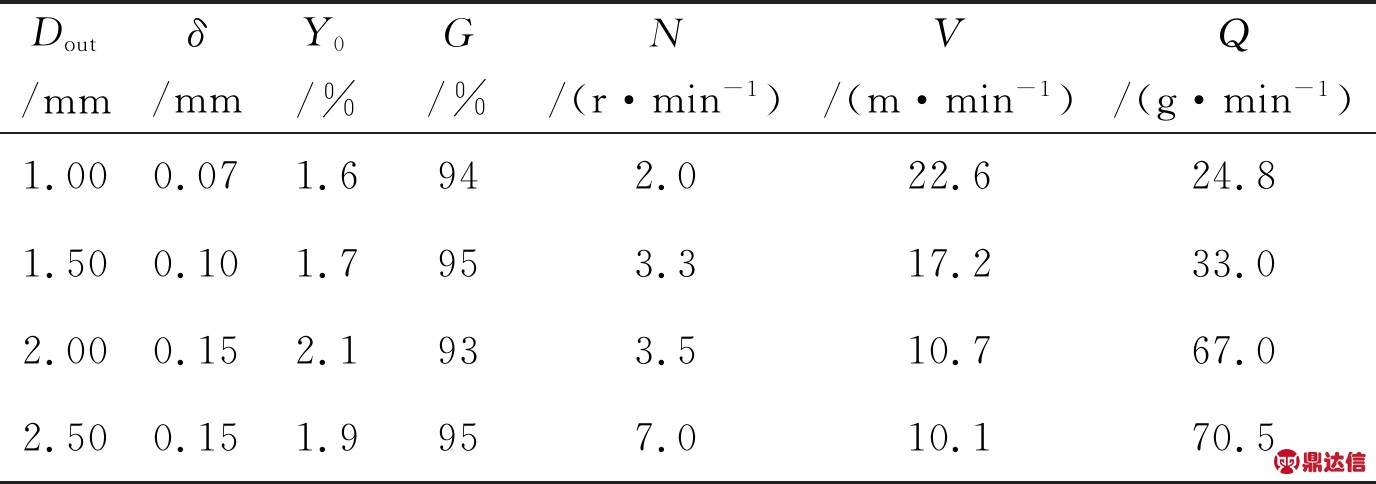
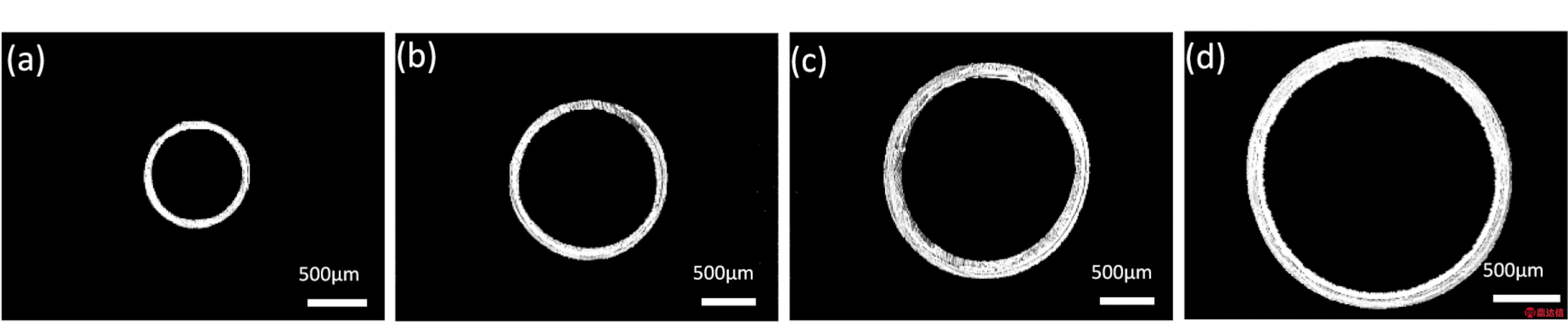
Fig.10 Cross sections of extruded four specification micro tubes
(a): Dout=1.00 mm, δ=0.07 mm; (b): Dout=1.50 mm, δ=0.10 mm; (c): Dout=2.00 mm,δ=0.15 mm; (d): Dout=2.50 mm,δ=0.15 mm
综上所述,牵引速度和螺杆转速对微管外径和壁厚具有显著影响,椭圆度主要与注气量有关。因此通过改变牵引速度、螺杆转速、注气量及其组合,可以获得外径分别为1.0 mm、1.5 mm、2.0 mm、2.5 mm 4种尺寸规格的聚乳酸微管。
3 结论
(1)通过系统研究聚乳酸微管的挤出成型工艺,获得了注气量、螺杆转速、牵引速度对微管外径、壁厚和椭圆度的影响规律,以及挤出不同规格聚乳酸微管的工艺参数组合。通过改变牵引速度、螺杆转速、注气量及其组合,达到了采用一套模具顺序挤出4种规格聚乳酸微管的目的。所成型的4种规格微管的椭圆度≤2.1%,壁厚均匀度≥93%,满足设计要求。
(2)挤出成型工艺实验结果表明,微管外径随注气量和螺杆转速的增大而增大,随牵引速度的提高而减小,且均呈非线性;微管壁厚随注气量和牵引速度的增大而减小,随螺杆转速的提高而增大,也均呈非线性。微管的最终外径和壁厚是型坯内外压差、离模膨胀和轴向拉伸共同作用的结果。微管椭圆度主要由注气量决定,注气量越大,椭圆度越小,尤其在注气量较小时,注气量增加1倍,椭圆度可降低68%,随着注气量的继续增大,椭圆度稳定在2.0%左右。其原因是当注气量较低时,型坯内部气体压力不足以抵抗由重力引起的变形。
(3)不同工艺参数对外径和壁厚的影响程度不同。在初始阶段,注气量增大1倍,外径增大19%,壁厚减小20%;螺杆转速增大1倍,外径增大24%,壁厚增大50%;牵引速度增大1倍,外径减小24%,壁厚减小36%。可见,螺杆转速和牵引速度相对注气量对微管外径的影响程度更大;螺杆转速、牵引速度和注气量对壁厚的影响程度依次减弱。