NOMEX 蜂窝具有轻质高强、密度低等优点,作为复合材料结构件选用的高频材料,其成型后的复合材料蜂窝芯夹层结构件具有刚性大、强度高、隔音和隔热性好、质轻、抗冲击、抗疲劳、热稳定性好等优点,广泛应用于航空飞机领域,特别是飞机机身结构件,如整流罩、襟翼、副翼、方向舵等主承力结构件和次承力结构件。整流罩和襟翼均为曲率较大的复合材料结构蜂窝件,在成型的过程中,提高NOMEX 蜂窝芯的成型精度,对于提高复合材料夹芯构件成型质量至关重要,对我国航空领域内的大曲率、双曲率复合材料蜂窝结构件研制和生产具有重要的意义[1-3]。西方发达国家的飞机制造业经过长期的技术发展和积累,在复合材料成型方面具有较多的经验,其中针对大型客机中的主承力和次承力结构件已形成可靠成熟的技术体系和质量体系,在复合材料NOMEX 双曲面蜂窝零件的数控加工方面,其技术较成熟,如采用先进的数控加工专用超声机床、根据零件结构特点优化装夹方式等,较好地解决了蜂窝零件加工弱刚性的问题,然而该类技术一直是西方工业发达国家的核心秘密,并对中国实施技术封锁。国内对于双曲面蜂窝零件的数控加工技术相对落后,由于缺乏系统的数控加工工艺方案,导致切削参数相对保守、加工效率低、加工质量不易保证。虽然国内各加工中心和各大航空企业在蜂窝等复合材料零件的数控加工技术方面积累了一定经验,但应用于大尺寸的双曲面薄壁蜂窝零件有其自身显著特点,如壁厚更薄、刚度更弱、轮廓精度要求更高,从而对数控加工技术要求更高。因此,大幅双曲面薄壁板类零件的高效、高质量数控加工技术对我国航空制造领域特别是大飞机制造领域的技术水平提升和行业发展至关重要[4-10]。
目前高速铣削和蜂窝超声加工成了国内外学者研究的热点[11-18],重点研究和分析高速铣削加工中不同刀具对蜂窝零件加工的影响,建立蜂窝加工模型。对比超声加工,主要介绍超声加工原理,并对其进行有限元模态分析,研究圆形刀主振型与固有频率的关系及变化规律,分析了圆形刀楔角大小的改变对圆锯片的固有频率及其振型的影响;建立切削力下圆形刀应力场数学模型,结合圆形刀静力学和模态分析的结果,并未对实际生产的零件进行检测,尤其是双曲面蜂窝芯零件。例如,Choon 等[11]研究蜂窝材料及蜂窝构件的机械性能,重点研究材料性能与机械加工间的关系,研究出最佳的加工模式,并未提出合理的检测方法。由于NOMEX 蜂窝为弱刚性材料,具有切削性能差的特性,与传统金属结构件相比,NOMEX 蜂窝结构件不同,可通过控制加工参数,来提高加工精度。但加工过程中容易造成芯材纤维拔出、变形,产生毛刺,且通过传统组合铣刀加工后,NOMEX 蜂窝芯材料工件表面往往留有大量的纤维毛刺,本论文创新提出了弱刚度大型双曲面蜂窝数控切削及检测一体化技术,不仅解决了NOMEX 蜂窝零件弱刚性难于固持的问题,同时运用一套完整用组合铣刀加工NOMEX 蜂窝材料的方法,采用高速铣削加工工艺,通过优化加工编程策略,有效地解决双曲面蜂窝芯零件成型后精度问题,加工后利用校验膜技术,对蜂窝零件预装配,检验与上下蒙皮的配合精度是否满足要求。
1 试验材料与方法
1.1 双曲面NOMEX蜂窝加工方案
本文以大型复合材料尾缘结构双曲面NOMEX 蜂窝为研究对象,零件结构形式为双曲面变厚度NOMEX 蜂窝,零件双面整体分别为凹、凸曲面,四周轮廓亦多为曲面,设计要求保证上、下型面轮廓度在±0.3mm 范围内,零件厚度为17~84mm 的变量,零件最大长度尺寸约为8000mm,蜂窝宽度约170~340mm,数模见图1。NOMEX蜂窝材料分为低、中、高密度,密度小于48kg/m3 的蜂窝属于低密度蜂窝,密度大于48kg/m3 的蜂窝属于中、高密度蜂窝。本文选用48kg/m3 蜂窝作为研究加工对象。采用自主设计和研制的双曲面蜂窝数控铣削及检测一体化工装进行加工,其数模如图2所示。选取90mm 厚的蜂窝作为加工原材料。对蜂窝型面铣削采用高速铣削工艺,蜂窝加工常用的铣削刀具有圆盘刀,不同材质的圆形刀在相同的切削参数下,铣削后的加工性能差异较大,其效果也明显不同。常用的加工圆盘刀材料有硬质合金和高速钢材料,其材料性能对比见表1。因蜂窝为芳纶纸,对刀的硬度要求不高,蜂窝结构中空洞所占面积远大于切削面积,所以盘刀的耐磨性和导热性要求不高,硬质合金刀头修磨较高速钢更为困难,综合性价比及其他因素考虑,本文采用组合铣刀进行加工,蜂窝组合铣刀由刀柄、钢齿切削部分、圆片铣刀组成。圆片铣刀与蜂窝芯壁相接处作用效果明显,切削时,圆盘刀将按照编程中要求进行型面铣削,将多余的蜂窝材料与工件分离,紧接着锯齿部分将分离部分切断,因在进给和切削方向上被分离的蜂窝材料大小不一,型面的即时距离与刀具之间的距离也不一致,形成了刀片分离-锯齿切断的循环切削形式。本文选取Φ38.1mm 的高速钢材质圆盘刀对蜂窝进行铣削加工。加工环境温度:18~32℃;相对湿度:≤65%,与超声加工相比较,刀具成本较低,经济适用性较强。

图1 蜂窝零件数模
Fig.1 Mold of honeycomb part
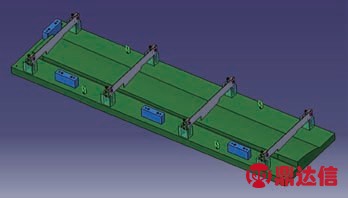
图2 一体工装加工蜂窝零件数模
Fig.2 Intergration mold of honeycomb part processed by integrated tooling
表1 刀片材料性能对比
Table 1 Performance comparison of cutting tool material
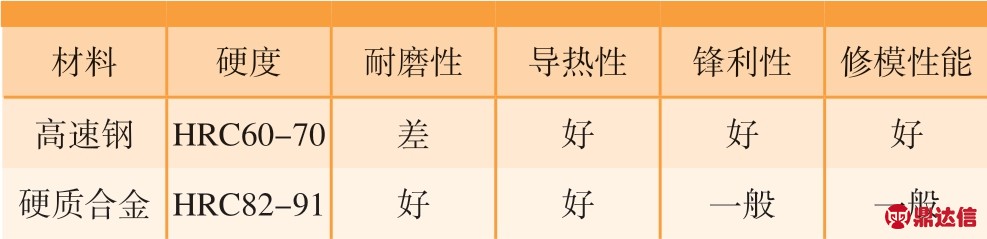
1.2 双曲面NOMEX蜂窝检测方案
NOMEX 蜂窝芯固持困难也是高速铣削中的一大难题[19],本文采用自主设计制造的加工检测一体化工装,将蜂窝芯通过真空吸附的方式固定在成型工装上,将加工与检测基准统一为同一基准,且工装型面误差不会累积,有效地改善固持问题,同时避免了零件加工到检测的拆装,不仅提供了检测的准确性,而且提高了检测效率。对加工后的蜂窝在线检测完毕后,针对双曲面蜂窝芯装配精度问题,采用校验膜对蜂窝芯拼接阶差及双曲面变厚度蜂窝芯与上下蒙皮预装配的间隙进行检查,在成型工装上,对蜂窝零件与已固化次级零件胶接进行预装配,采用校验膜的方式对其进行装配间隙检测,将胶膜夹在两层无孔隔离膜或PVC 薄膜之间,无孔隔离膜或PVC 薄膜的厚度应为0.1mm;通过在固化后的胶膜上产生清楚的压痕来检验蜂窝芯与零件的预装配情况。
2 结果与分析
2.1 双曲面蜂窝零件成型结果分析
零件为双曲面蜂窝,首先通过真空吸盘吸附在加工平台上对其单面加工,能有效改善弱刚度蜂窝芯原材料翘曲变形,真空吸附的固持方式能有效解决双面胶带、磁粉固持或其他固持方式带来的缺陷,如加工过程中极易出现带起和撕裂,导致零件厚度不均或局部变薄,加工后零件表面平整,断面整齐。在蜂窝材料高速铣削过程中,铣削力主要受到表2 中主轴转速、进给量、切宽和切深的影响。蜂窝切削加工中切削力的主要来源不是剪切破坏,而是大量的挤压和拉伸破坏[20],由于蜂窝切削力的复杂程度,简单的线性拟合不能满足对切削力的描述,通过四元二次正交旋转组合设计,对试验的因素和水平进行合理的配置,分析出单因素效应切削力随主轴转速、进给量、切宽和切深的影响。得出以下结论:切削力随着进给速度、切宽和切深增大而增大,随着主轴转速增大而减小。切深的影响最大,其次是切宽和进给速度,而主轴转速对于铣削加工的影响较小。优化后其参数设置如表2所示,以满足零件加工中切削力的最小化。采用组合铣刀加工,加工过程中,由于圆片铣刀的契角非常小,加工时按照表2 中的转速进行粗加工和精加工,切削刃与锯齿都按一定的角度成螺旋状排布。在很高的切削速度下可以轻易地将上部已经分离的蜂窝材料均匀地打碎成粉末,并通过空气吹动将切屑排掉,同时刃齿排布稳定,且磨损量小,所受的切削力也比较均匀。选取表2 中的铣削参数能够有效将铣削力优化,既保证了加工过程中蜂窝的固持稳定性,减少加工过程中零件飞边,同时也保证了蜂窝的加工效率和加工质量。在将加工好的单面蜂窝进行装夹,本论文中加工检测一体工装为切削夹具,在双曲面蜂窝检测加工一体工装对蜂窝零件分段加工,通过弱刚度蜂窝铣削加工及检测一体化技术对蜂窝零件加工及检测。确保加工与检测基准的一致性,解决了因蜂窝软性材质及加工与检测分开造成的基准不一致问题,提高了蜂窝检测的可靠性,同时能实现加工到检测的快速切换,缩短蜂窝整体的生产周期。采用双曲面加工检测一体工装[21],其零件加工结果如图3所示。
从图3 可以看出,分段加工后的双曲面蜂窝芯在成型工装上预装配效果良好,分段蜂窝间并未出现明显阶差,能很好地与下蒙皮及其他次级零件装配,其装配间隙小于0.15mm。针对零件断面切断对齐问题,改变原有切断方式,采用插铣方式切边,进给方向为上下钻孔方式,加工过程中不产生横向分力,减少带起现象。针对双曲面的轮廓插铣加工,轮廓线抽取比较困难,其边缘轮廓沿长度和宽度方向均为波浪形,无法按近似直线连接成轮廓,必须按曲面抽取出轴线进行编程,厚度方向与曲面保持一致,编程效果如图4所示,型面加工刀具为由碎屑刀体和切断刀片组合而成,粗加工去量时会出现边缘不均匀的情况,留下台阶状的边缘残余,对于较厚蜂窝零件粗加工型面产生的台阶状残余需要先用蜂窝立铣刀去除大部分残余,再进行后续的插铣加工。
表2 加工参数
Table 2 Parameters of process
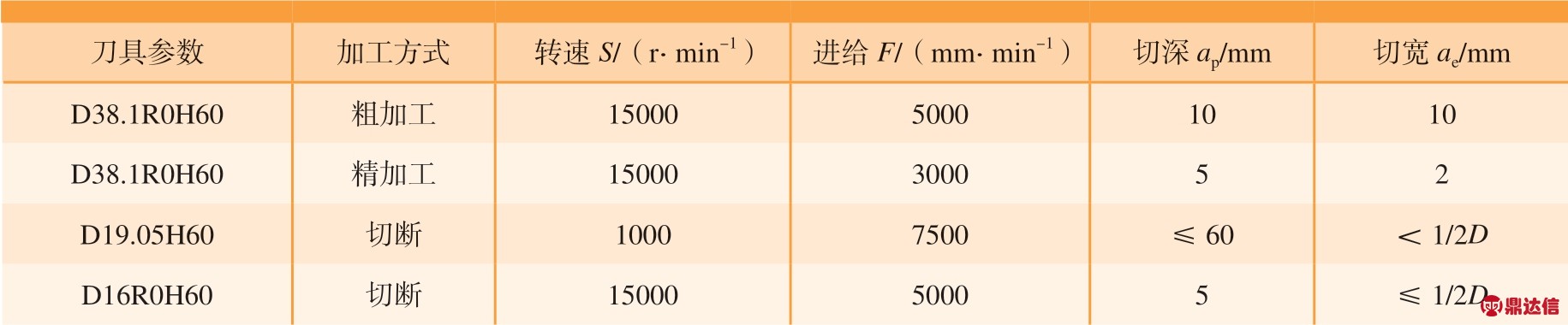
从图3 中可以看出,型面拼接阶差小于0.2mm。本次加工过程中,针对双型面分段加工情况,增加半精加工程序,按零件公差要求设置等量精加工程序,分层精加工,边加工边检测。蜂窝加工去量使用小切深、小切宽、快进给进行轻量切削,并保持固定角度去量,可减少或避免粘刀情况出现,如图5所示。传统的蜂窝型面编程加工策略,只能沿宽度方向走刀,效率低下,下刀时刀轨非常不规则,加工存在风险,其编程策略刀路如图6所示,采用精加工四轴策略可沿长度方向单向走刀,零件外侧进刀,宽度方向沿型面由低向高推进,犹如剃刀理发方式切削零件进行去量加工,提高粗加工去量效率和精加工加工质量,如图7~8所示。
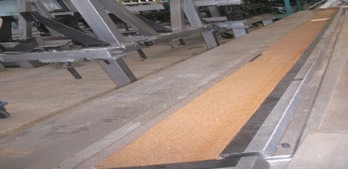
图3 加工后的蜂窝
Fig.3 Finished cell
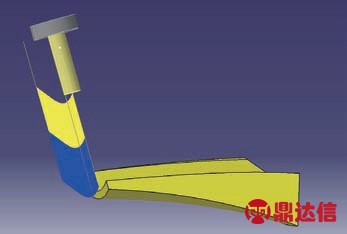
图4 双曲面蜂窝轮廓的插铣编程效果
Fig.4 Effect of hyperboloid cellular contour milling programming
2.2 双曲面蜂窝零件检测结果分析
本文对分段加工后的双曲面蜂窝芯进行预装配,并通过校验膜的方式对其进行验证,验证结果如图9所示。从图9 可以看出,板芯区域蜂窝芯格清楚印压在固化后的胶膜上,蜂窝芯格界限明显,蜂窝拼接处无明显胶瘤流淌,即蜂窝拼接处未产生明显阶差,拼接间隙小于0.2mm。板板区域胶液分布均匀,因此可以看出,蜂窝芯与上下蒙皮的装配效果很好,未产生干涉。
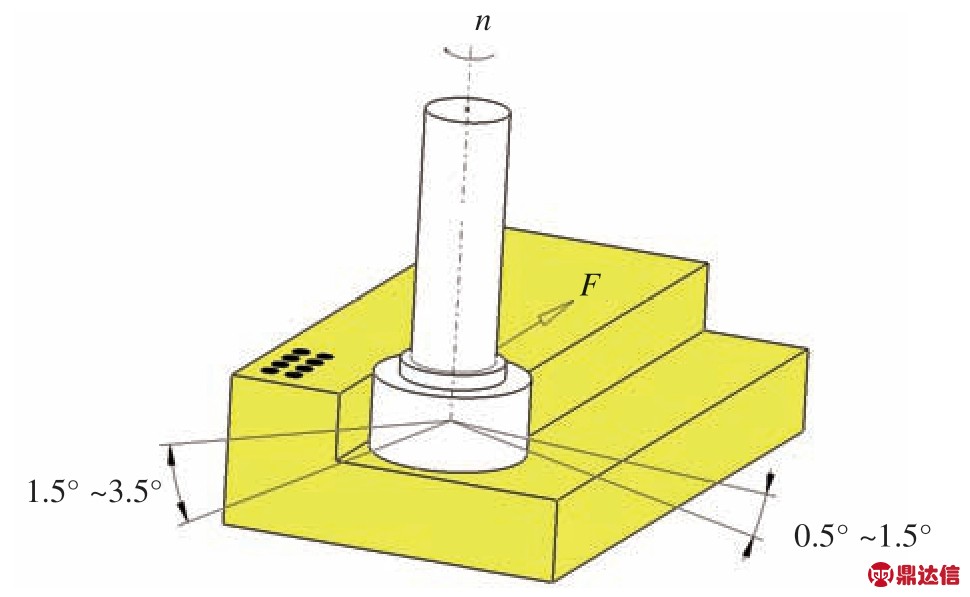
图5 蜂窝加工角度设置
Fig.5 Angle setting of honeycomb process
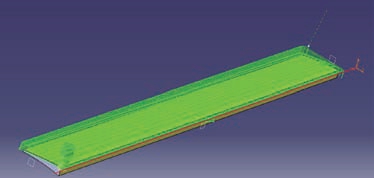
图6 传统编程策略刀路
Fig.6 Cutting tool path of traditional programming strategy

图7 优化编程策略刀路
Fig.7 Cutting tool path of optimization strategy programming
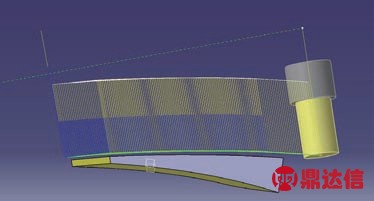
图8 加工模拟图
Fig.8 Simulation of machining
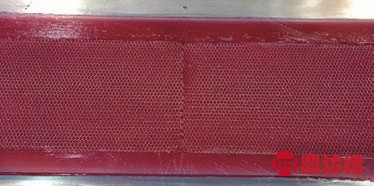
图9 校验膜
Fig.9 Verification film
成型后的蜂窝一般采用检验样板或数字化测量方式进行检测。检验样板对于双曲面蜂窝芯的检测较困难,由于检测的基准不能很好地找准,且检验样板的加工精度需在±0.1mm 以内,会在装配过程中产生测量误差,难以满足装配要求。采用三坐标计量机检测其检测探头的角度未能掌握其检测矢量误差,检测误差不易确定,由于蜂窝零件蜂窝方向刚性较差,检测时基准不易校准,造成产品型面检测数据误差大,不能反映产品真实数据,同时需要带工装进行计量,否则无检测基准,而频繁搬运工装,既会导致工装变形,也使得双曲面蜂窝产品检测周期加长。本文采用自主研制和设计的加工检测一体工装,能在线检测蜂窝型面,保证蜂窝产品在加工状态和检测状态的基准一致,真实反映产品加工数据,保证产品装配的合格率。
3 结论
(1)针对双曲面NOMEX 蜂窝成型,采用加工检测一体双曲面成型工装进行高速铣削,通过优化编程策略,选取合适的加工参数,能满足双曲面蜂窝成型精度,并进行在线检测,利用校验膜二次检测,结果表明双曲面蜂窝芯成型后与上下蒙皮装配间隙小于0.15mm;蜂窝芯拼接缝小于0.2mm;与超声加工相比较,节约加工成本。
(2)校验膜技术可用于复合材料板芯胶接预装配验证,通过固化后校验膜成型质量判定预装配间隙和精度。本试验结果表明,固化后蜂窝芯格能清晰复现在校验膜上,成型面上无蜂窝芯格撕裂、损伤等缺陷,其装配精度满足要求,二次验证双曲面NOMEX 蜂窝成型精度和拼接间隙均能满足与上下蒙皮装配要求。
参考文献
[1]GIBSON L J,ASHBY M F.Cellular solids:structure and properties[M].2nd ed.Cambridge:Cambridge University Press,1997.
[2]KOSMATKA J B,OLIVER J.Development of an inflight structural health monitoring system for composite unmanned aircraft[C]//Newport,Rhode Island:47thAIAA/ASME/ASCE/AHS/ASC Structures,Structural Dynamics,and Materials Conference.2006.
[3]常洋洋.复合材料夹芯结构壁板箱型制备技术与弯曲性能研究[D].长沙:国防科技大学,2011.
CHANG Yangyang.Study of manufacturing process and flexural properties of a box-section bean with foam-core sandwich walls[D].Changsha:National University of Defense Technology,2011.
[4]RIKARDS R,ABRAMOVICH H,KALNINS K,et al.Surrogate modeling in design optimization of stiffened composite shells[J].Composite Structures,2006,73(2):244-251.
[5]LANZI L,GIAVOTTO V.Post-buckling optimization of composite stiffened panels:computations and experiments[J].Composite Structures,2006,73(2):208-220.
[6]BLOM A W,STRICKLER P B,GÜRDAL Z.Optimization of a composite cylinder under bending by tailoring stiffness properties in circumferential direction[J].Composites:Part B,2010,41(2):157-165.
[7]ARJOMANDI K,TAHERI F.A new look at the external pressure capacity of sandwich pipes[J].Marine Structures,2011,24(1):23-42.
[8]李河清,赵景丽.无人机复合材料夹层结构件工装制造[J].航空制造技术,2004,47(4):104-105.
LI Heqing,ZHAO Jingli.Unmanned aerial vehicle(UAV)composite sandwich structure tooling manufacturing[J].Aeronautical Manufacturing Technology,2004,47(4):104-105.
[9]高涛,骆金威,林勇,等.基于超声波机床的蜂窝芯数控加工技术研究[J].机械制造,2013,51(1):41-43.
GAO Tao,LUO Jinwei,LIN Yong,et al.based on the ultrasonic machine tool of honeycomb core numerical control processing technology[J].Machinery Manufacturing,2013,51(1):41-43.
[10]侯小林,祝益军.蜂窝结构件的数控加工[J].航空制造技术,2009,52(S1):60-63.
HOU Xiaolin,ZHU Yijun.NC machining of honeycomb structure[J].Aeronautical Manufacturing Technology,2009,52(S1):60-63.
[11]CHOON C F,GIN B C,LEONG K S.Mechanical properties of Nomex material and Nomex honeycomb structure[J].Composite Structures,2007,80(4):588-594.
[12]张菊霞,田卫.浅谈蜂窝芯零件的数控加工[J].航空制造技术,2010,53(6):87-89.
ZHANG Juxia,TIAN Wei.Introduction to the honeycomb core components of the NC machining[J].Aeronautical Manufacturing Technology,2010,53(6):87-89.
[13]张菊霞,田卫.碳纤维、芳纶纤维、蜂窝芯零件数控加工刀的选用[J].航空制造技术,2010,53(15):71-73.
ZHANG Juxia,TIAN Wei.Carbon fiber,aramid fiber,the honyecomb core parts selection of NC cutter[J].Aeronautical Manufacturing Technology,2010,53(15):71-73.
[14]朱秀文.Nomex 蜂窝材料直刃尖刀超声切割切削力分析[D].大连:大连理工大学,2016.
ZHU Xiuwen.Study on cutting force in nomex honeycomb composites ultrasonic cutting by straight blade knife[D].Dalian:Dalian University of Technology,2016.
[15]ROY R,PARK S J,KWEON J H,et al.Characterization of NOMEX honeycomb core constituent material mechanical properties[J].Composite Structures,2014,117:255-266.
[16]方亮.NOMEX 蜂窝材料超声铣削圆形刀研制[D].杭州:杭州电子科技大学,2014.
FANG Liang.Development of ultrasonic milling circular tool made of NOMEX cellular materials[D].Hangzhou:Hangzhou Dianzi University,2014.
[17]陈建桥.Nomex 蜂窝芯超声精加工圆形铣刀磨损检测技术研究[D].杭州:杭州电子科技大学,2014.
CHEN Jianqiao.Research on wear detection of Nomex honeycomb core ultrasonic finishing round cutter[D].Hangzhou:Hangzhou Dianzi University,2014.
[18]吴胜游.NOMEX 蜂窝复合材料超声切割断裂机理研究[D].杭州:杭州电子科技大学,2016.
WU Shengyou.Research on fracture mechanism of ultrasonic cutting for NOMEX honeycomb composites[D].Hangzhou:Hangzhou Dianzi University,2016.
[19]柯映林,金成柱,刘刚.NOMEX 蜂窝芯高速铣削加工工艺的优化[J].中国机械工程,2006,17(12):1299-1302.
KE Yinglin,JIN Chengzhu,LIU Gang.Optimization of highspeed milling prosess for NOMEX honeycomb[J].China Mechanical Engineering,2006,17(12):1299-1302.
[20]李杰.NOMEX 纸基蜂窝材料的组合铣刀高速铣削研究[D].大连:大连理工大学,2012.
LI Jie.Rearch on high-speed milling NOMEX paper-based honeycomb material with interlocked cutter[D].Dalian:Dalian University of Technology,2012.
[21]刘望子,管海新,许漂,等.一种提高双型面全尺度蜂窝成型精度的工装:CN206536228U[P].2017-10-03.
LIU Wangzi,GUAN Haixin,XU Piao,et al.Improce frock of dimorphism face full-scale honeycomb moulding precision:CN206536228U[P].2017-10-03.