0 引言
铁芯是变压器的重要部件,铁芯由硅钢片叠装而成。变压器铁芯叠片机器人能提高变压器叠片工艺效率,提高铁芯叠片质量,降低变压器的空载损耗和噪音,同时降低操作工人的劳动量,改善工人劳动强度和劳动环境,对于变压器生产厂商而言,自动叠片机的投入使用会使人工成本大幅降低。
国外有三家公司研制出了用于叠片的工业机器人,分别是德国乔格、瑞士阿尔斯通、加拿大MTM,由于技术保密原因,可以查到的关于国外叠片机器人的资料十分有限。在国内,河南开封大学的朱峰,林吉靓设计了CZC-1型自动叠片机器人,该机器人使用大功率静音空气压缩机作为动力源,机械结构主要有机架、工作台、主溜板、副溜板、导轨、机械手、料槽和叠片工作台组成,可以实现JSZW3、6、10等型号的铁芯硅钢片的叠放,采用PLC进行控制[1]。浙江大学的章昱帆、蒋振军采用TC55控制器对整个叠片过程进行控制,自动叠片机采用框架结构,有三个平移自由度,其中X、Y两个平移自由度分别由步进电机驱动同步带型直线滑台和丝杠型直线滑台获得,Z向平移自由度以气缸作为动力源,抓手采用真空吸盘 [2]。南车株洲公司的宋悠全对动车组变压器铁芯自动叠片机器人进行了研究,设计的叠片机器人由上料平台、叠片工作台、安全系统、分片取片装置、叠片输出装置组成[3]。上述叠片机器人均只能对小型铁芯进行叠装。在变压器中,大型变压器的作用尤为重要,其高压输电的作用无可替代。目前国内尚未见到对大型铁芯自动叠片机器人的报道,而国外相关技术对外保密,设备价格不菲,因此对大型铁芯自动叠片机器人进行研究十分必要。
1 叠片工艺介绍
叠片是将四垛堆放在一定位置的厚度只有0.25mm的硅钢料片叠成“E”字型铁芯,铁芯由4部分组成,分别为竖直方向的左柱、中柱、右柱和水平方向的底轭。其中左柱和右柱形状相同,在铁芯中的位置对称,中柱位于左柱和右柱中间位置,轭片和以上三柱垂直,图1是某变压器型号的铁芯结构示意图。
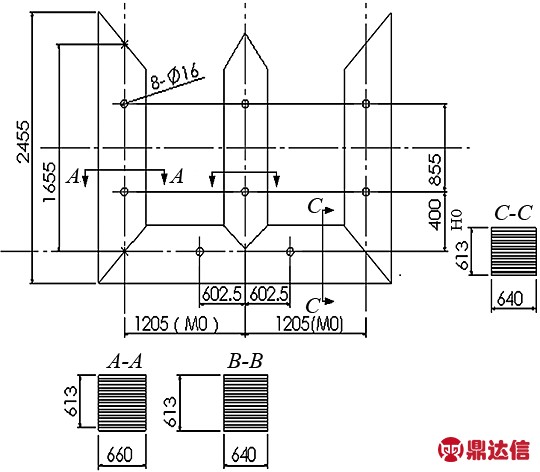
图1 铁芯结构示意图
叠片工艺的技术要求:窗宽M0≤±1mm,铁芯厚度偏差≤±1mm,铁芯起立后的柱片的倾斜度≤铁芯总高度的0.4%,H0≤±1mm。
目前工厂的叠片现场如图2所示。
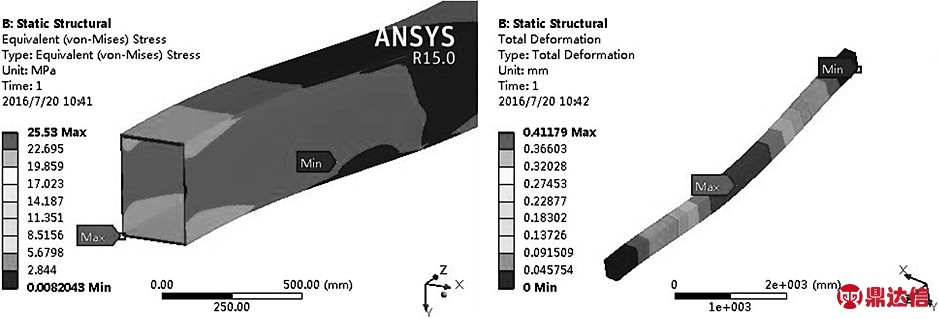
图2 叠片现场
叠片时,4部分料片相对铁芯的位置如图3所示。
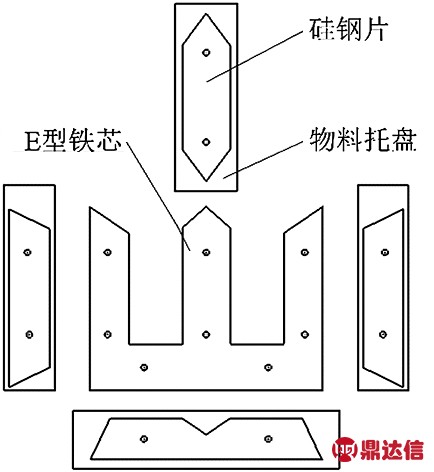
图3 料片相对铁芯位置
先将竖直方向的左柱、中柱和右柱叠放到相应的位置,然后叠放轭柱。目前,这种型号的铁芯的叠片工艺需要四人同时配合才能完成。
2 机械本体设计
自动叠片机器人用于大型变压器的铁芯叠片工序,铁芯叠片机器人工作采用龙门桥架系统,主要由主龙门机架、桥架、四个叠片机械臂、两个翻转台、两台运料AGV和用以安全措施的隔离网组成。由于直角坐标机器人与其它机器人相比,具有以下优势:有X、Y、Z三个直线运动自由度、可重复编程、运动精度高、运动速度快、方便控制,非常适用于搬运物料,因此叠片机器人采用直角坐标机器人的形式[4]。示意图如图4所示。
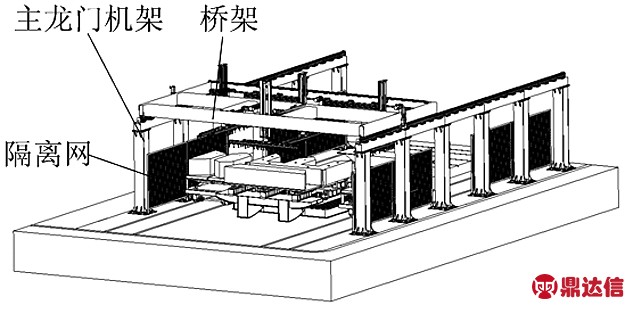
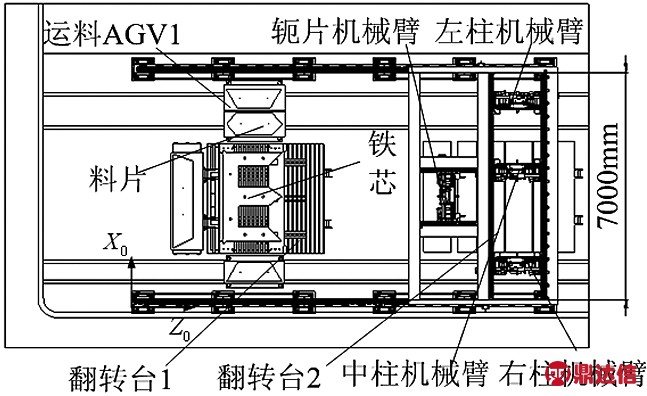
图4 大型叠片机器人示意图
自动叠片机器人工作站的工作原理为:首先桥架可沿着主龙门机架在两个翻转台之间平移运动,位移反馈采用光栅尺,传动方式为高精度齿轮齿条。当桥架移动到一个叠装台上方时,桥架停止运动,运料AGV会停止在翻转台侧边位置。然后叠片机械臂按着根据控制系统计算的相对位置运动,抓取运料AGV的硅钢片,将其叠放到翻转台上。叠片臂共有4个,其中三个用于叠放柱片,一个用于叠放轭片,只要更换机械臂末端的真空吸盘抓手,就可以适用不同规格的铁芯。在叠放的过程中,高度检测传感器会实时检测叠片高度,工控机接收高度传感器传回的数据并根据编制好的程序控制叠片机械臂在Y轴方向的高度。为了提高效率,龙门机器人设计为双工位形式,工位一完成叠片工序时,桥架运动到工位二进行叠片,工位一由工人将铁芯固定在翻转台上、然后继续完成翻转台翻转90°、转移叠好的铁芯以及为下台铁芯的叠装准备等工作,叠片机器人按照这个节拍循环工作。图5是叠片机械臂示意图。
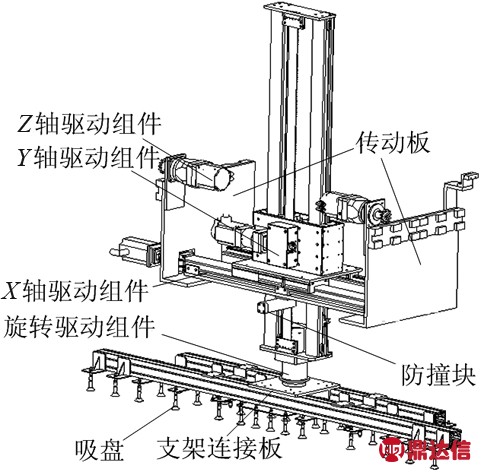
图5 叠片机械臂及吸盘机械手
图6是翻转台翻转前后的示意图。

图6 翻转台
硅钢片厚度只有0.25mm~0.3mm, 因此在叠片机械手抓取硅钢片的时候,两片硅钢片有可能粘连在一起,因此在运料AGV加上了硅钢片分片装置,硅钢片分片装置采用市场上成熟运用的磁力分张器。磁力分张器是利用同名磁极相互排斥的原理工作的,当磁性材料靠近磁铁时就会被磁化,磁化的材料极性相同,所以材料与材料之间产生互斥力,原来紧贴的材料就会分开。图7是利用磁性分张器做的试验。
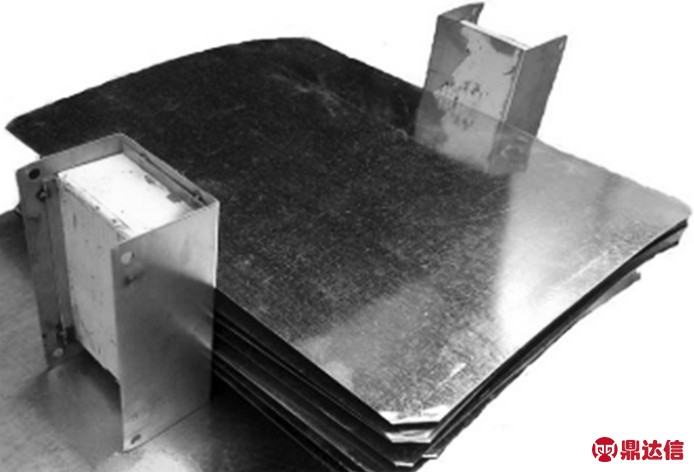
图7 磁性分张器分片试验
3 桥架横梁设计与尺寸优化
桥架是叠片机器人一个重要的部件,桥架包含三根跨度达7m的横梁,为箱形三梁桥架结构,纵梁的横截面同横梁的横截面相同。桥架如图8所示。
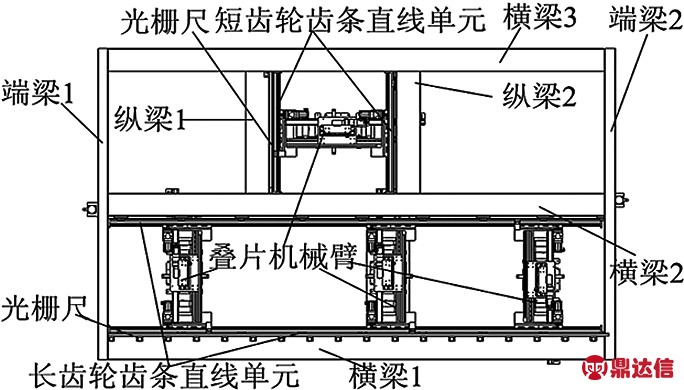
图8 桥架
四个叠片机械手安装在桥架上,桥架的变形或者振动对机械手的叠片精度有极大的影响,因此对桥架加以研究十分必要,研究内容包括两点:①用SOLIDWORKS进行横梁的设计,建立三维模型。②因为零件的抗弯、抗扭刚度和刚度除与其截面面积有关外,还取决于截面形状。合理地改变截面形状,增大惯性矩和截面系数,可提高机架的强度和刚度,从而充分发挥材料的作用[5-6],因此采用ANSYS WORKBENCH的优化模块对梁的截面进行优化,使其在质量较小的情况下变形在可接受的范围。
梁两端的连接方式会对梁的受力及变形情况有较大的影响,在本文中梁的约束可简化为两端固定约束,为三次超静定梁 [7]。超静定结构较之相应的静定结构由于存在多余约束,其内力分布范围大,峰值小;且刚度大,使变形小。机械臂的连接板与主梁的腹板相连通过导轨滑块直线单元相连,所以力作用在横梁的侧方,梁在受到弯矩的同时受到扭矩,扭矩使梁产生扭转角,弯矩使梁产生挠度。因此采用抗扭刚度和抗弯刚度都较好的箱型梁。
对于一般机架,垂直方向的挠度与长度之比限制在1/500~1/1000,自动叠片机器人的精度要求高,所以将挠度与跨度之比设为1/12000。
力学模型按照随后的三条规则建立:①齿轮齿条直线单元重量均匀施加在横梁侧边。②叠片机械臂以集中力的方式施加在横梁侧边。③两个横梁之间的载荷平均分配到两个横梁。
在横梁的优化中,目的是在某种类型载荷作用下,在满足变形要求下发现使横梁的质量最小的截面尺寸,得到截面的哪些尺寸对刚度、质量影响较大,然后对关键尺寸进行加强,对影响较小的尺寸进行削弱[8]。从桥架示意图中可得到横梁2的负载最大,如果横梁2的的形变满足要求,其余两根横梁的形变也会满足要求,因此选择横梁2进行分析,横梁2受到来两部分力的作用,一部分是自身重力;另一部分是纵梁、机械臂以及直线单元的重量。横梁的初始尺寸如下图所示。
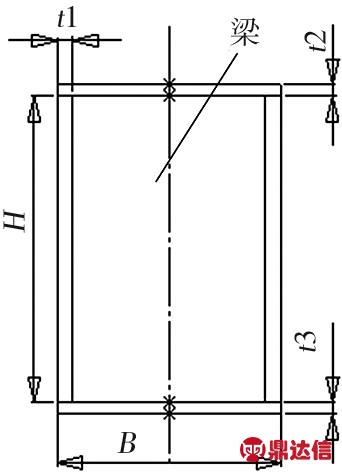
图9 横梁截面图
表1 横梁截面初始尺寸表

表2 横梁所受载荷

研究思路如下,首先利用ANSYS WORKBENCH静力结构分析工具对梁进行分析,然后将所得结果导入参数相关性优化工具,得到输入各个参数的重要程度,最后利用直接优化分析工具,从一系列的由软件按照正交试验原理生成的设计点中选出最优的设计点[9-10]。
梁的材料为结构钢,弹性模量为200GPa,泊松比为0.3,密度是7.85g/cm3。划分网格的单元数为82600,节点数为578790。网格质量检测工具检测结果为网格质量良好。静力结构模块分析所得结果如图10所示。
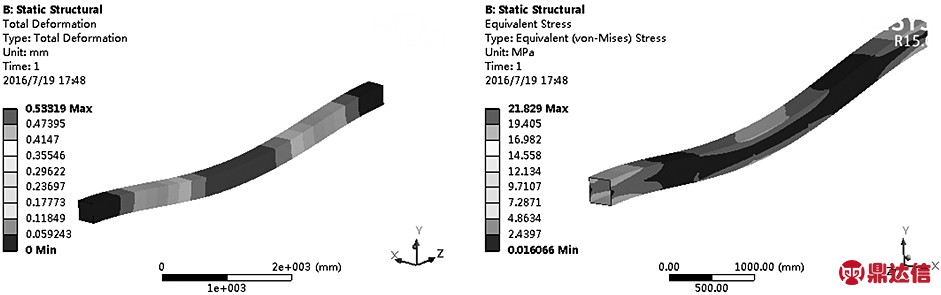
图10 优化前横梁应力应变图
从仿真结果可知,最大变形量约为0.533mm,出现在横梁中部,从变形图中可以观察到变形的方向为Y向,即与重力作用的方向一致;最大应力为出现在梁两端,为21.829MPa。
利用参数相关性优化分析工具得到的各参数关系如表3所示。
表3 线性关系表
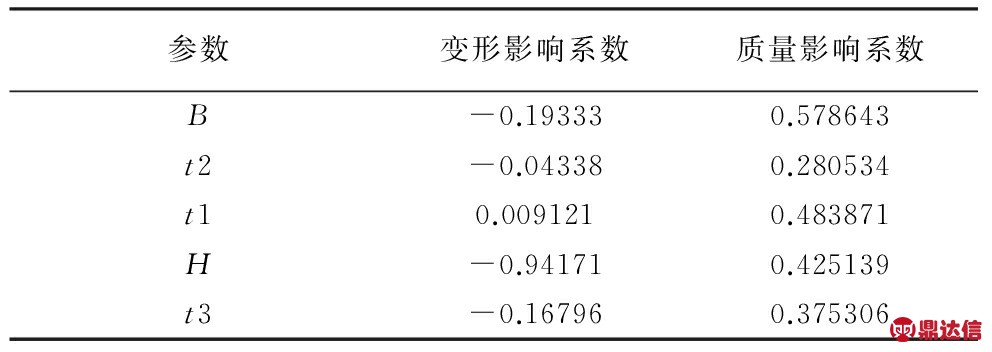
表中的负数代表参数的使目标减小,正数代表参数使目标增加。从关系表中可得到以下结论:增加H对减小变形最有效;增加B虽然能减小变形,但是对质量增加较大;增加t3既能使变形有效的较小,对质量影响也不太大;t1对变形的影响系数为正,结合其较大的质量影响系数,说明由于t1增加使质量增速较快,增加的自身重量抵消了t1增加的刚度,但是t1不能过小,会造成局部失稳。
输入参数是B、t2、t1、H、t3,输出参数是横梁的最大总变形和质量。根据参数相关性分析工具得出的结论设置参数变化范围为:200mm≤B≤300mm,300mm≤H≤400mm,5mm≤t1,t2,t3≤15mm。
直接优化分析工具设置生成的设计点数为120,从中选出3个候选设计点。
目标为横梁质量最小,约束条件为横梁最大总变形小于0.5mm。3个最优候选点如表4所示。
表4 最优候选点
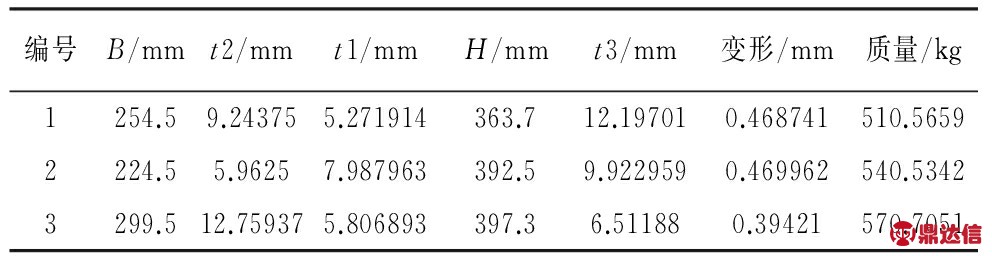
3个候选点相对于初始点的变形和质量且变形满足约束条件,三个候选点相对初始数据的变形及质量变化如表5所示。第一个候选点的质量最小,因此选择第一个候选点为依据作为横梁截面尺寸,根据参数相关性分析工具的结论对第一个参考点的数据进行圆整,即对能使变形量减小的参数省略小数点后加一,对使变形量增大的参数直接省略小数,得到优化的横梁截面尺寸如表6所示。
表5 变形及质量变化表
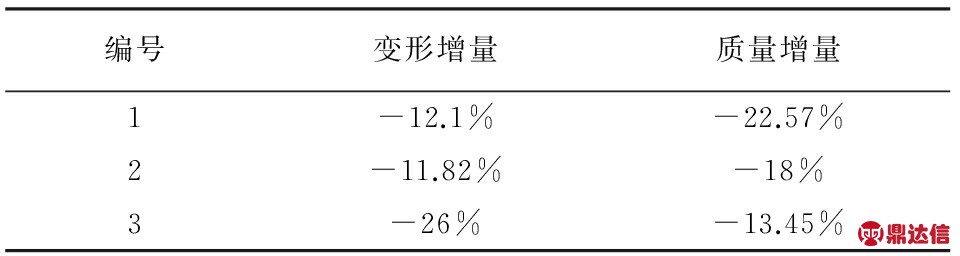
表6 优化后横梁截面尺寸表

对优化后的横梁进行仿真,得到其最大总变形和最大应力,如图11所示。
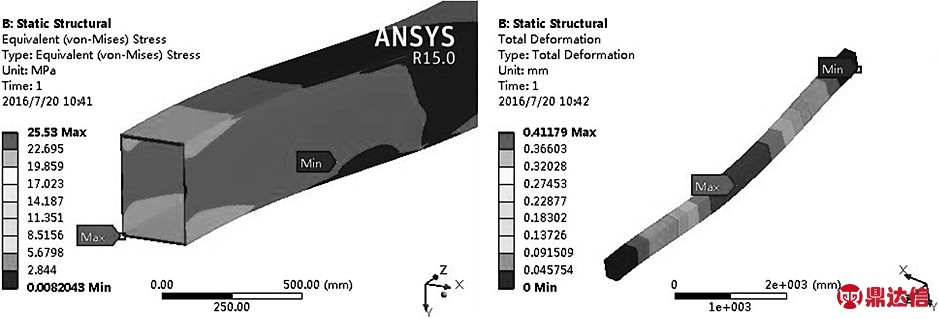
图11 优化后横梁应力应变图
最大应力为25.53MPa,最大总变形为0.412mm,满足工程技术要求。
4 结论
首先对大型铁芯叠片机器人的机械本体进行了设计,首次提出了采用四个机械手同时叠装硅钢片及将双工位的方法用于叠片机器人,大大提高了叠片的效率。然后基于ANSYS WORKBENCH对关键部件桥架的横梁进行尺寸优化设计,优化后的横梁在质量减少-22.57%的情况下,变形减少了12.1%。
[参考文献]
[1] 朱峰,林吉靓.硅钢片自动叠片机的研究与设计[J].机械设计与制造,2014(7):43-44,48.
[2] 章昱帆,姜振军,熊树生,等.硅钢片自动叠片装置设计及结构优化研究[J].机电工程,2015,32(10):1295-1299,1305.
[3] 宋悠全.动车组变压器铁心自动叠片工艺研究[J].科技传播,2013(11下):155-156.
[4] 李瑞峰.新一代工业机器人系列产品开发[J].机器人,2001,23(7):633-635.
[5] 张海波,张瑞军,常影.基于ANSYS的汽车悬架控制臂有限元分析[J].组合机床与自动化加工技术,2014(3):150-151,155.
[6] 韦杰,王文韬,王凤晨,等.基于ANSYS的不同悬伸量微型铣刀有限元模态分析[J].组合机床与自动化加工技术,2013(12):112-114.
[7] 于锋钊,赵明扬,辛立明,等.基于ANSYS的龙门式直角坐标机器人横梁分析[J].机械设计与制造,2008(5):182-183.
[8] 张祥,苏衍宇,王伟东,等.一种平面混合驱动夹持器的结构优化设计[J].机器人,2016,38(3):343-351.
[9] 刘晓,赵铁石,边辉,等.大型舰载稳定平台机构及优化设计[J].机器人,2013,35(3):339-345.
[10] 茅启园,沈建明.基于ANSYSWorkbench的加工中心横梁有限元分析与优化[J].组合机床与自动化加工技术,2016(6):78-80.