随着现代制造技术的进步和发展,人们在铝合金挤压型材生产中追求通过技术创新来大幅提高现有挤压机的生产效率,新的一模多孔挤压技术无疑是最佳的途径之一。而一模双孔挤压技术是实现一模多孔挤压的基础,是在一套模具上同时同步挤出两根相同的铝型材制品,这对提高挤压机的效能和产品成品率有重要的意义。在铝型材市场需求中半空心型材占相当大的比例。而半空心型材的生产中模具是关键的要素。半空心铝型材的模具设计复杂程度较高,解决模具的强度是关键。笔者以一种常见的铝型材实例介绍专门针对半空心铝型材采用的遮盖式一模双孔挤压模具的结构,以及设计中各种参数的选择,供同行参考。
易非知道,如果刚才陈留不在场,老妈肯定会说:怎么样了?你不是出差了吗?我一个人睡大床?……我让他们睡得宽敞一点啊!……怎么了,怎么了?你今天回来了,今天不睡不就是了吗?
1 遮盖式一模双孔挤压模的结构
所谓遮盖式就是改变传统的挤压半空心铝型材采用的平面模结构,而采用一种遮盖式分流模结构。目前半空心铝型材分流模结构中常用的是分割式结构,这种结构易产生拉丝和起筋现象。遮盖式分流模结构是利用分流模上模的中心部位将悬臂遮盖起来,使得悬臂在挤压过程中不直接承受金属的正面压力,将悬臂保护起来;而在分流模的下模,悬臂部分要向上突起,但不与上模接触,突起的顶部与上模之间留有一定的间隙(应力间隙),使得即使上模在挤压过程中向下发生挠曲时,也不会触及悬臂对悬臂施加力的作用。这样就改变了悬臂的受力状态并保护了悬臂,因而大大提高模具的强度。对于一模双孔的模具则充分利用分流桥作为对悬臂的保护,这是考虑到挤压机在挤压筒径向上存在压力梯度,通过合理的布置模孔,避免悬臂特别是悬臂的端部直接承受金属挤压时的正面压力,达到提高模具强度的同时提高铝型材挤压效率。
2 模具结构参数的确定
2.1 挤压机能力的确定
确定选用挤压机的能力要考虑到挤压产品的变形程度、挤压系数。挤压系数过大,挤压过程中挤压力会过高,容易出现挤压困难,一方面不利于产品成形,另一方面将会降低模具的寿命。挤压系数小则挤压力小,这有利于产品成形,但在一模双孔挤压时,在同样的坯料长度下会使挤出的型材长度减少,导致工艺废料的比例增加,降低了成品率。而若增加坯料的长度,挤压筒是有限的,同时会使挤压力急剧上升。这是双孔模具结构设计中必须要考虑的。经验数据表明,在综合考虑的情况下,挤压系数在60~80范围内最为合适,比较有利于产品成形、生产过程控制和模具寿命等。
图1所示为一款民用建筑铝门窗型材,是典型的半空心型材。其断面面积为221 mm2,舌比经计算为6.5。采用单孔模挤压时一般选择8 MN~11 MN挤压机。采用双孔模挤压则可选择18 MN挤压机,其挤压筒内径尺寸选择Φ185 mm。经计算挤压系数为66.5,挤压机比压为670 MPa。坯料尺寸可选用Φ180 mm×520 mm。
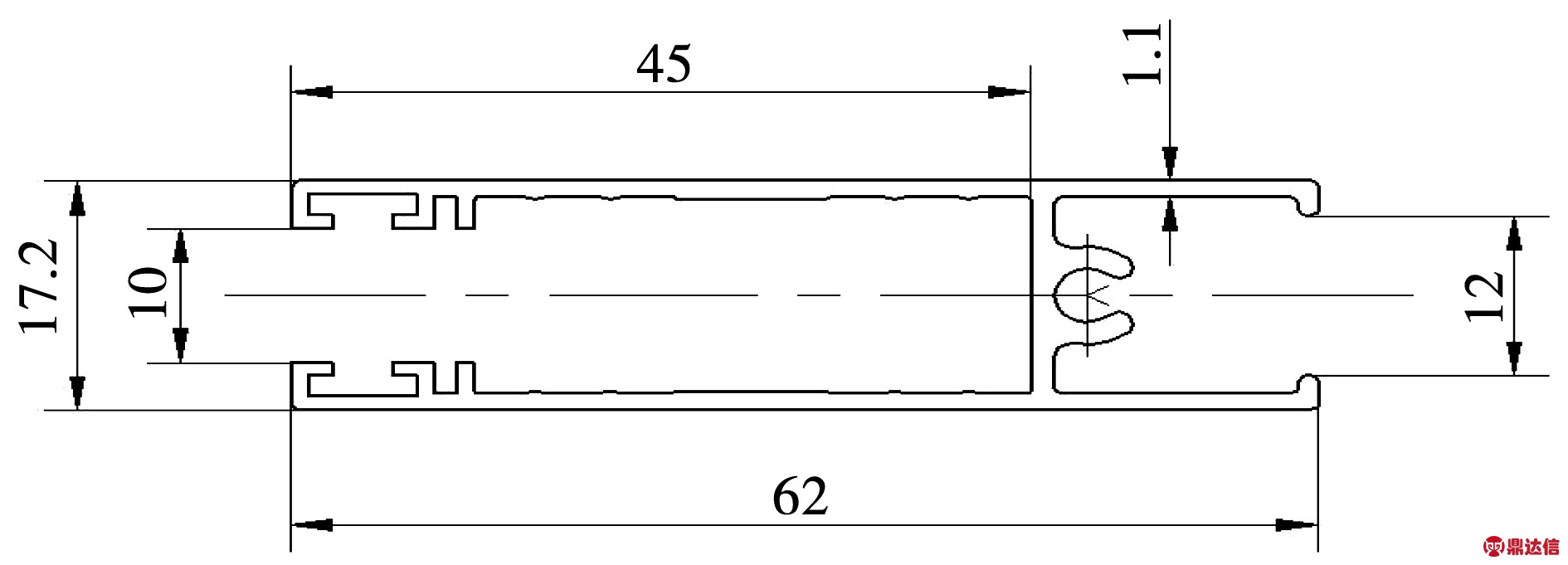
图1 一种铝门窗型材的断面图
Fig.1 Profile section of a kind of Al door and window
2.2 模孔的布置
模孔的布置一方面要有利于挤压成形,可以充分发挥挤压筒的潜能;另一方面必须有利于使模具结构简单、紧凑,有利于模具加工和节省原材料。在18 MN挤压机上挤压图1所示的型材,模孔的布置可以有二种方式,如图2所示。
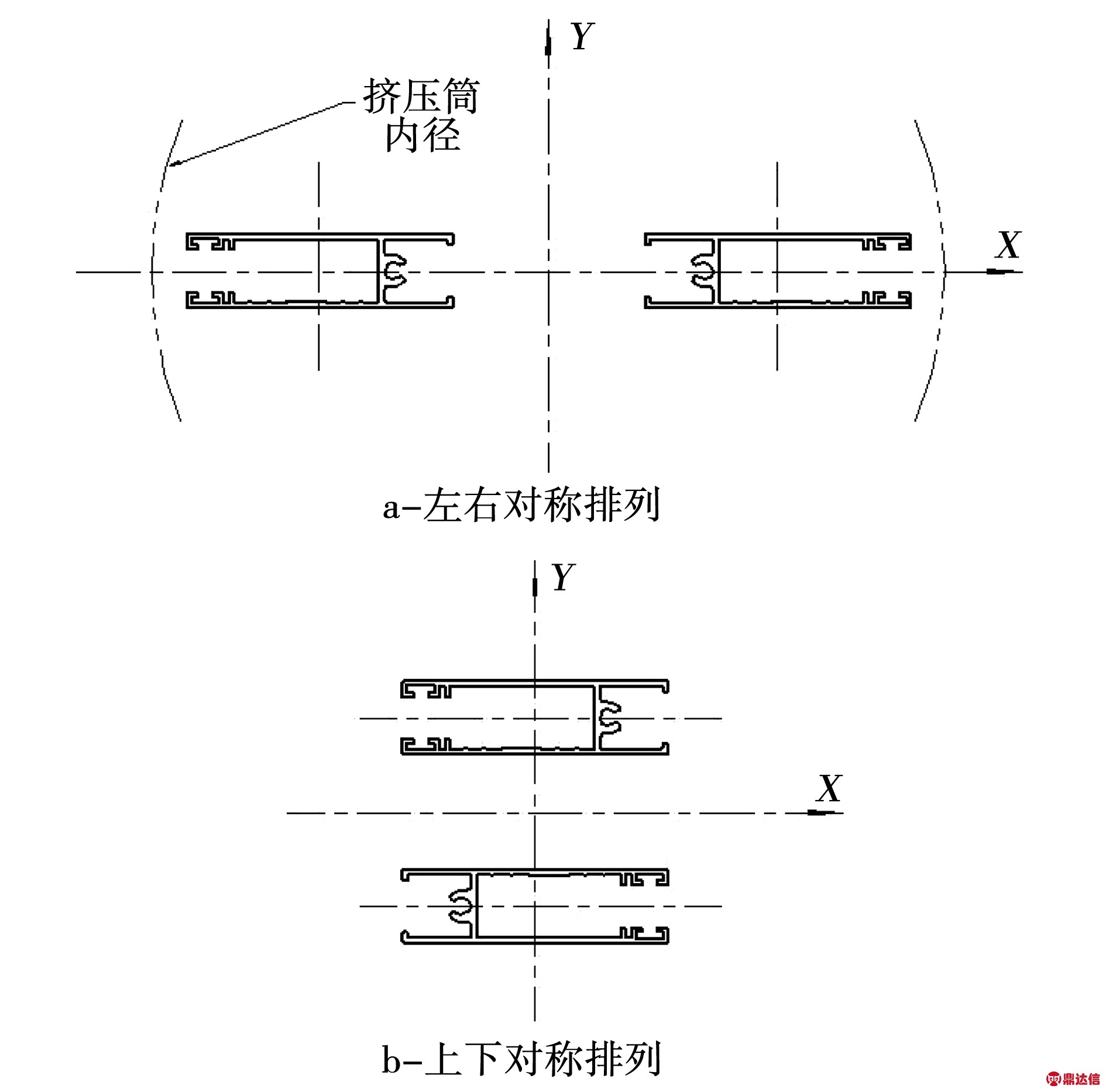
图2 模孔布置方式示意图
Fig.2 Arrangement of die holes
图2a为左右对称排列,这样的好处在于左右两根型材在挤压时不会发生表面的接触,两根型材都可与滑出工作台接触,挤压容易实现平稳顺利。其不足的是不能充分利用挤压筒的特点,因为一般地说,应使模孔各处尽可能处在中心区域,这样有利于达到挤压成形时各处金属流速容易趋于一致;模孔离挤压筒内壁边缘距离小,一方面要采用宽展的模具结构,这将增加金属流动的复杂程度;另一方面,模具的外形尺寸必须相应增加才能保证模具的强度。
图2b是采用上下对称排列,虽然上下两根型材在挤出时有表面的接触,表面可能会发生轻微的摩擦,但考虑到挤压时的自动牵引装置和型材最终的表面处理方式,这种接触对型材表面质量的影响是可以不考虑的,因此,选用图2b方式更为合适。
a)硬件结构部分。单片机应用系统一般包括硬件设计和软件设计两大部分。硬件是基础,软件是灵魂。没有硬件基础,无从谈软件编程。硬件部分一般包括单片机引脚及功能、存储器配置、特殊功能存储器配置、定时器计数器、中断系统、I/O口等,这些内容教材一般都包括。但从近年来学生学习此门课程的效果来看,可以对教学内容进行增添和删除,保留必要部分,去除繁琐用处不大的部分。
2.3 分流孔的布置
分流孔的布置包括确定分流比、分流孔的大小及分流桥的结构等。这是一模双孔模具的关键之处。根据图2b模孔的布置进行设计。第一步根据个人经验,借助CAD软件设计出初步的方案,较成熟的有两种分流孔布置的方案,如图3所示。第二步是将这两种方案在UG软件环境下建立三维模型,并保存为固定的格式。第三步是将建立的三维模型导入挤压模拟软件HyerXtrude中进行模拟运算和观察。最后是对结果进行分析和对比,并结合个人的经验进行必要的修正后再模拟、分析和对比,得出最佳方案。
通过模拟发现,图3a的分流孔布置方案金属流速调整较为困难。主要是分流孔S1、S2、S3的比例关系较难确定。可以预测,由于制造上的误差致使修模的工作量会增大。另外,虽然分流模的上模中心部位能将悬臂全部遮盖起来,但悬臂的端部因对应分流孔S2,模拟发现悬臂的变形程度较大,分流孔S2面积的变化对悬臂变形有明显的影响。
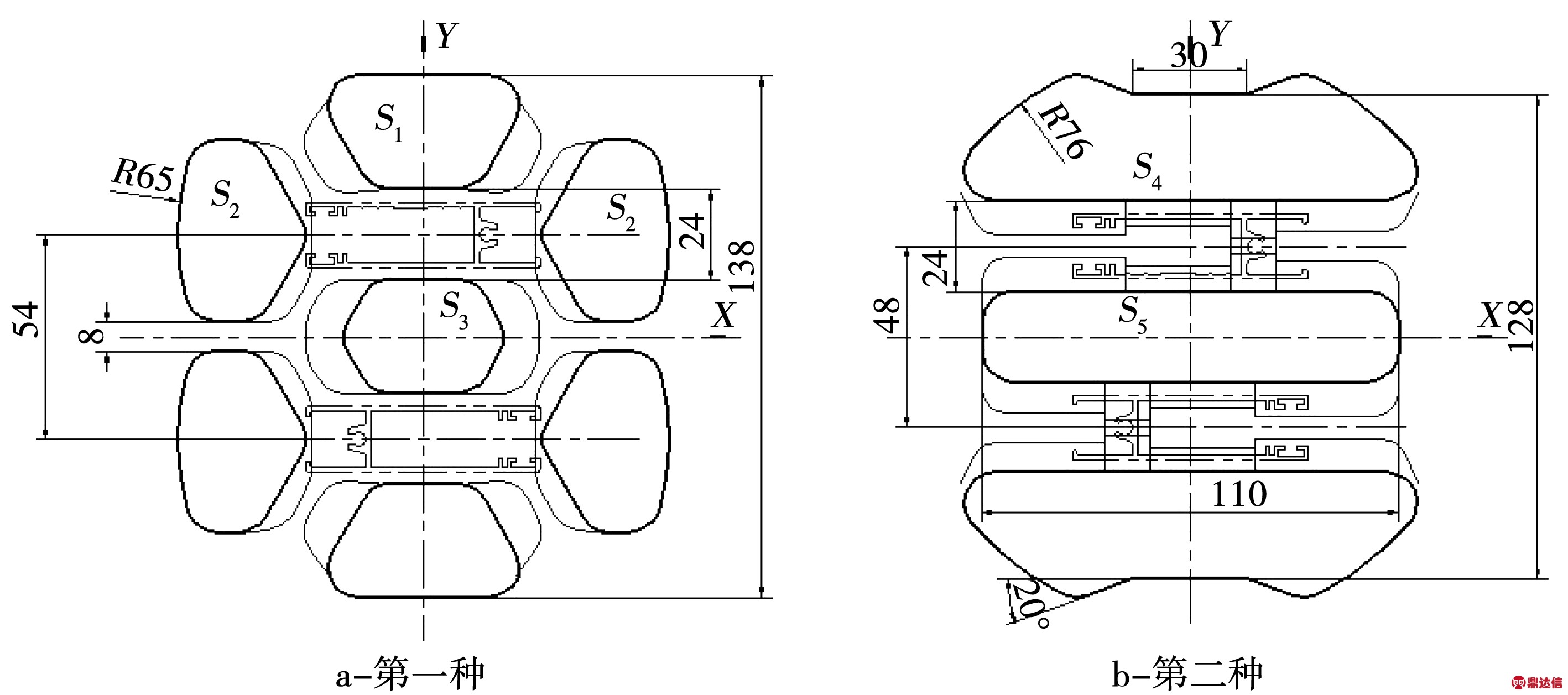
图3 两种分流孔布置方案示意图
Fig.3 Two kinds of layout of feeder portholes
图3b所示方案,分流孔数量少,仅调整分流孔S4、S5二者的面积关系即可,在确定分流孔S5的面积的前提下,很容易调整分流孔S4的面积就可以使各处的金属流速趋于一致,而且分流孔面积的变化对悬臂不产生影响,这是最关键的。同时,分流孔面积和调整可以对分流桥不进行修正或改变,悬臂也完全置于分流桥的保护下,特别是悬臂的端部不承受直接的金属正面压力,因此,悬臂的强度是最好的。经分析比较,采用图3b的方案更合适。其主要参数如下:
(1)通过对所制得的吸附剂的比表面积的测试,可以得出比表面积最大的就是复合材料,其次是硅胶,再就是硅酸镁吸附剂,比表面积值最小的就是硅酸钙吸附剂。
1)分流比K=17.3。取挤压比的25%~30%;
库区入渗除查找出逸点是重要工作之外,逆向验证水流通道寻找入渗点不容忽视。本项目试验再次证明,绕坝渗流监测布置应包含全部坝体与岩体衔接的部分,此举对于判定坝肩水体来源意义重大。
2)分流桥的宽度为24 mm,厚度为85 mm;
3)分流孔之间的面积关系为S5=0.81S4;从模拟发现,当S5=(0.75~0.85)S4时,各处金属流速调整较容易趋于一致;
4)分流孔最大外接圆直径为Φ152 mm;
5)分流桥结构是结合下模相对应的悬臂突起部分进行设计,其结构如图4所示。
2.4 下模焊合室结构与工作带
对于一模双孔挤压模,为了消除模具制造误差对挤压时两根型材同步性的敏感影响,以及消除在两个模孔相邻的中心部位产生金属流动的死区(刚性区)而使型材表面出现粗晶和光亮带现象,必须设计成两个独立的焊合室,使模孔间的成形互不干涉和影响。焊合室之间的隔墙宽度取6 mm~8 mm,焊合室深度根据挤压的能力取18 mm,隔墙高度取10 mm。
由于采用的遮盖式结构,悬臂要向上突起,突起的部分与悬臂模孔间的尺寸关系如图5所示。原则是突起部分边缘距离悬臂模孔边缘2 mm~3 mm。同时,由于悬臂突起部分与上模必须保持一定的应力间隙,为便于加工,间隙取在下模悬臂顶部表面,从模拟中发现,取0.5 mm~1.2 mm,均对悬臂不产生力的作用,所以取1.0 mm。
但是要注意的是在充填工艺的应用过程中,应该注重对充填工艺应用中的充填材料应用浓度控制,如果充填材料的浓度过高,其对应的充填效果就会出现阻碍,影响整体的矿产开发。应该选用浓度较低的材料作为充填工艺应用中的重要性材料去应用,保障在材料的应用中,能够为矿产开采的充填技艺应用奠定基础,促进其整体的开采技能提升。因此通常情况下选用低浓度的尾矿砂,冶炼水淬渣作为矿产充填工艺应用中的集料,保障在其应用中,能够发挥出矿产开采充填工艺应用的效果。按照其对应的充填材料应用步骤,将其对应的充填工艺运行图进行了设计,具体设计如下图1所示:
采用视频内窥镜检查管材内部缺陷存在一些问题:探头焦距范围太小,清晰成像的区域较窄,容易造成检验人员眼睛疲劳导致漏检。在确认工业视频内窥镜检查效果和不足之后,通过分析一般管材所处作业条件和目前的内窥镜技术,引进不同规格探头直径用于不同规格锆合金管材的内表面检测,取得了较好的效果。
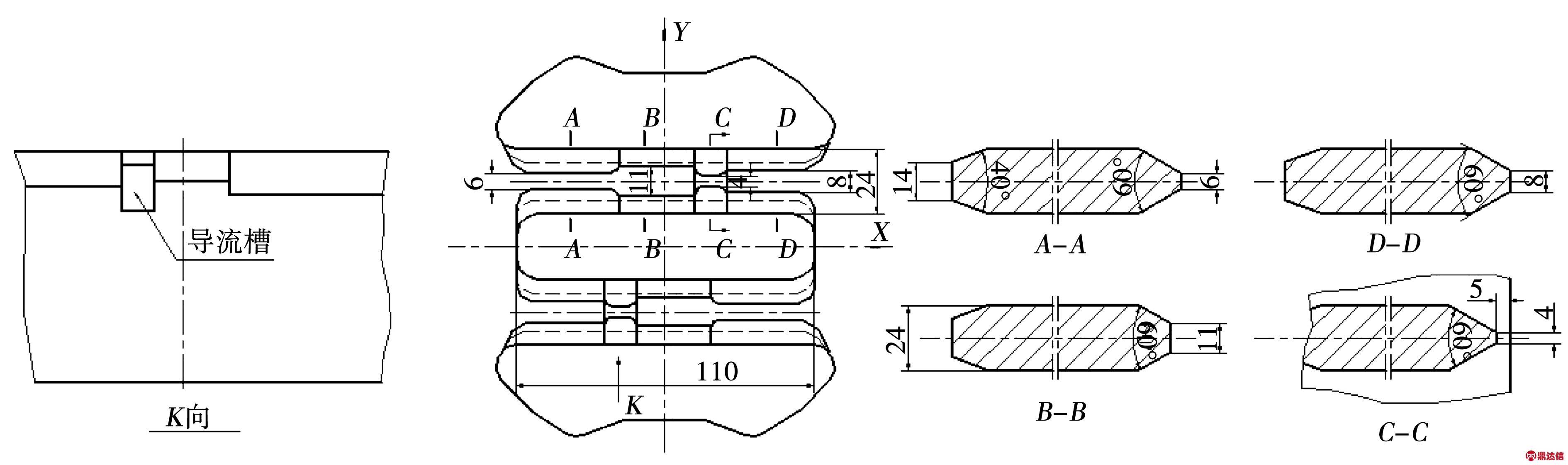
图4 分流桥结构示意图
Fig.4 Structure of feeder bridges
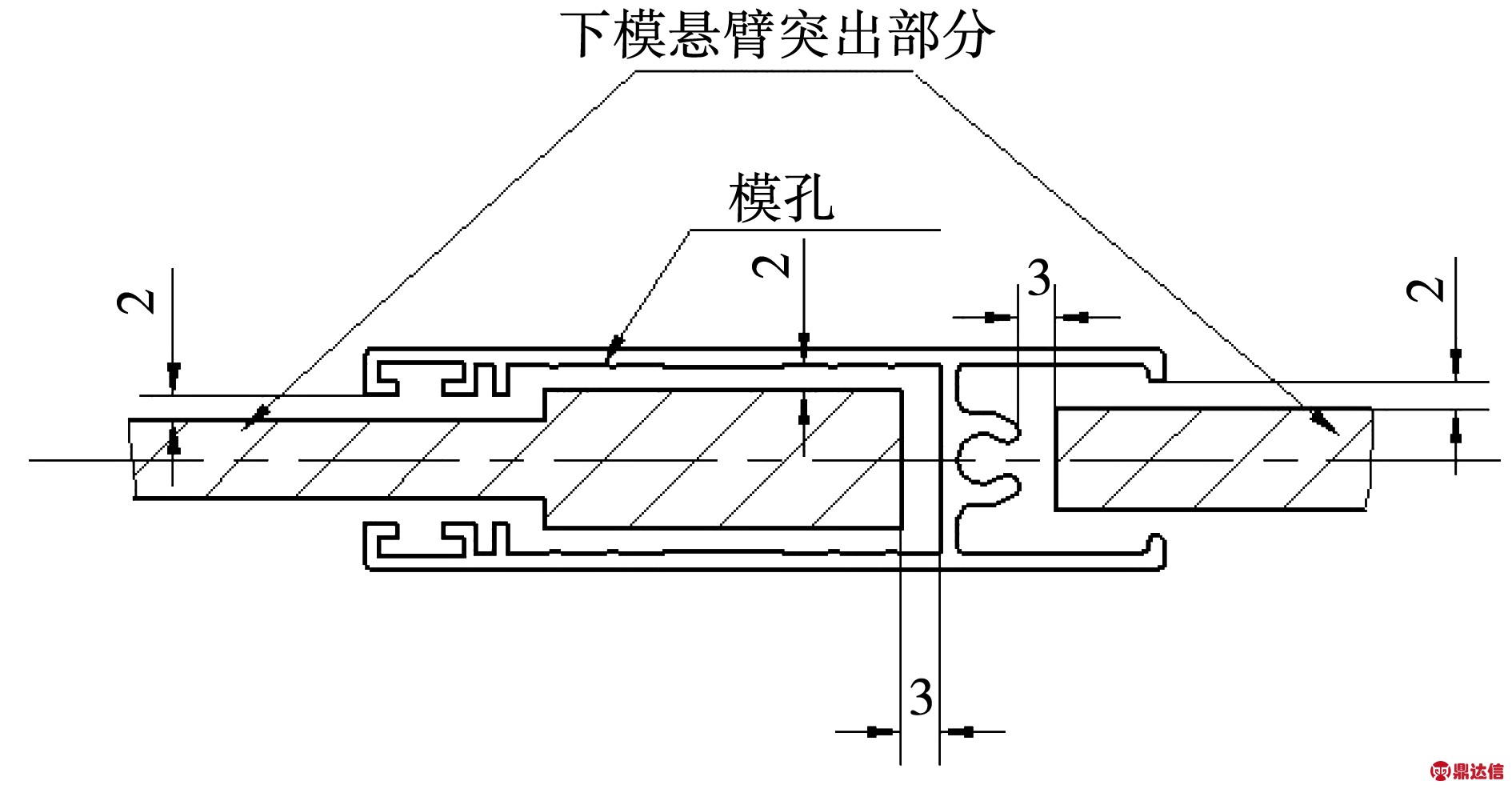
图5 下模悬臂突出部分示意图
Fig.5 Cantilever protruding part in female die
对于工作带的选择,可依照单孔模的原则进行。选定一个模孔的工作带则另一个与之相同。下模焊合室结构与工作带如图6所示。
由于果树的枝条较为繁茂,合理的对果树的树枝、树冠进行修剪,在很大程度上增加了果树吸收光的面积。此外,合理的修剪果树,不但有效的提高了果树的光合效率,而且还不会对树叶面积以及总生产造成任何影响。保证果树繁多的叶子能够更好的吸收阳光,进行光合作用,将其获得较多的养分传输给果树的根系,进而进一步促进果树的快速成长。
2.5 模具结构组成
模具由上模与下模组成。从模具强度和模具成本考虑,选择模具的尺寸外径×厚度为Φ250 mm×160 mm。模具结构如图7所示。
3 模具强度的校核
在挤压过程中,模具是承受拉和压交变循环应力的作用。因此,对分流模强度的校核在实践中主要是针对分流桥进行安全系数的计算,以确定模具的强度。对于双孔模,只要对一个模孔对应的分流桥校核即可。
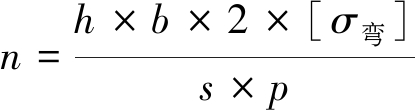
式中:
n—安全系数(分流模大于3,平模大于2);
陈山利的铁哥们恭建兵、牛力军,暗暗替陈山利捏着一把汗,将担忧的目光投向他。甚至在内心暗骂:呆子,不晓得捂紧话岔,偏要逞能讲出来!惹火上身了吧?
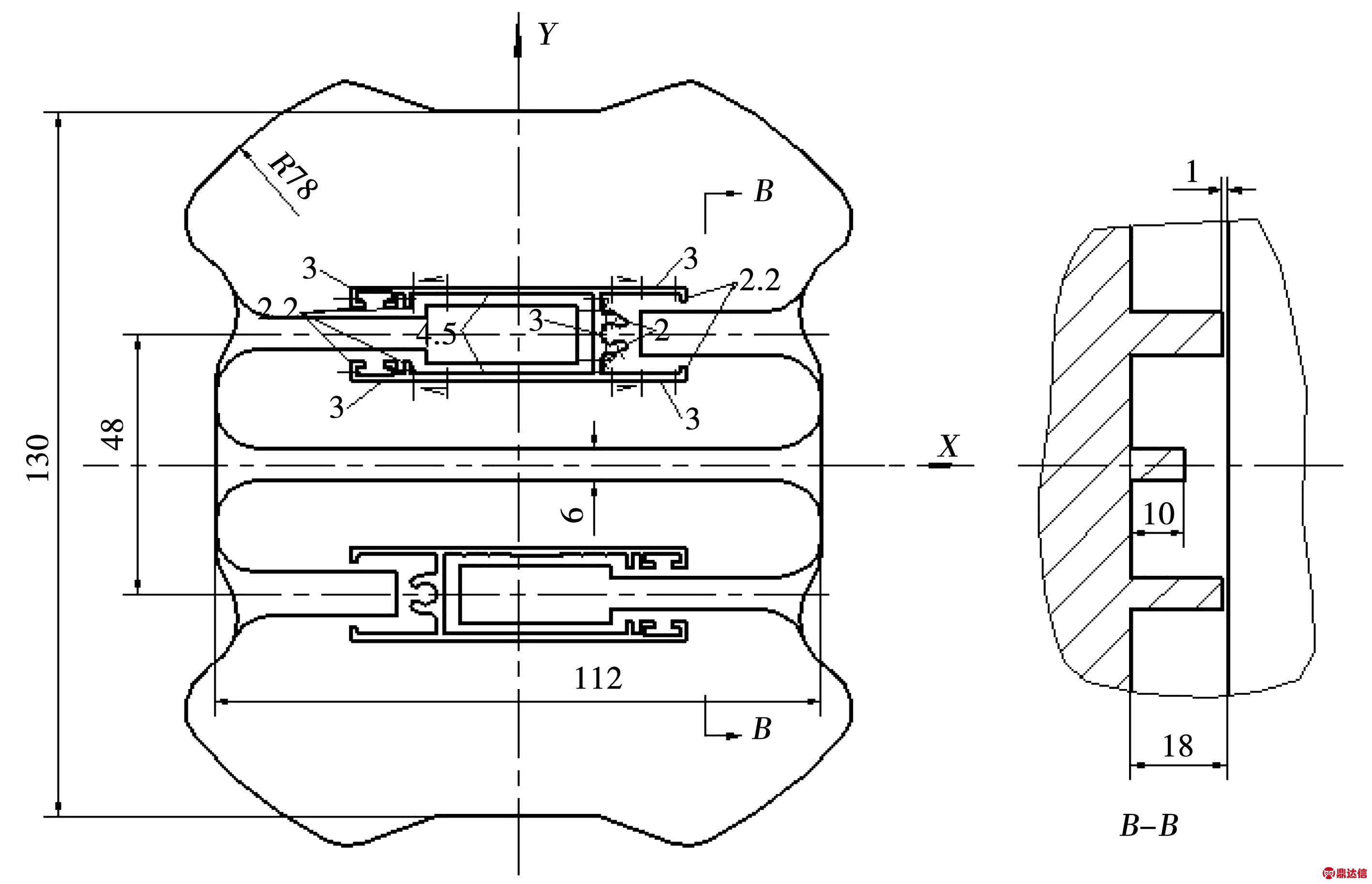
图6 焊合室与工作带示意图
Fig.6 Schematic diagram of chamber and bearing
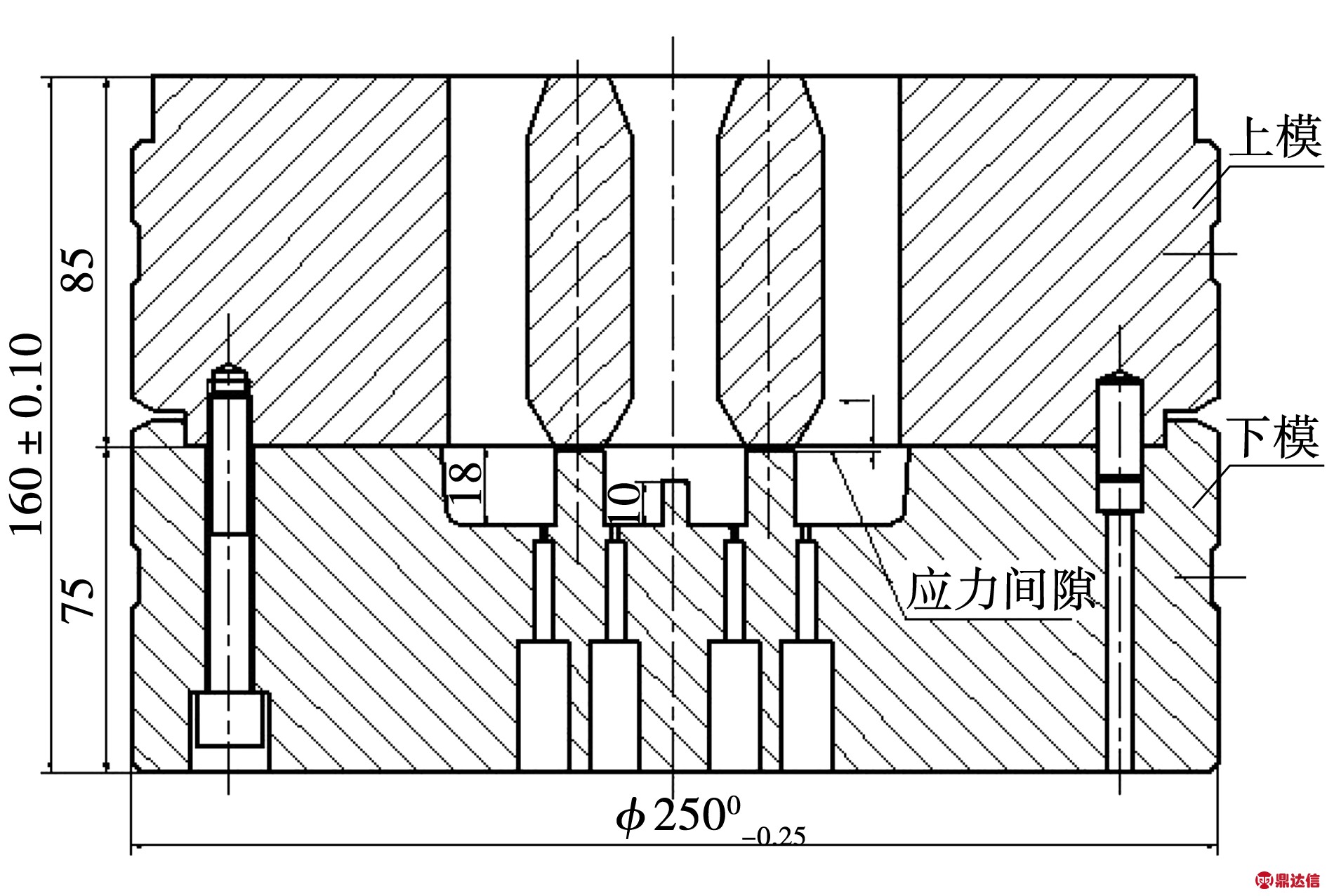
图7 模具结构示意图
Fig.7 Die structure
h—分流桥的有效厚度,mm;
b—分流桥最小宽度,mm;
S—上模分流桥受压总面积,mm2;
P—挤压机最大比压,MPa;
[σ弯]—模具材料在工作强度下的弯曲应力,MPa(模具材料为H13,取值为1150 MPa)。
笔者除了在课内、课外文言文教学方面下足功夫,而且还推出了“每日一摘”系列,到高三时,每天积累一句《论语》中的句子。例如“知者不惑”“仁者不忧”“勇者不惧”——《论语·子罕》,首先让学生翻译,其次让学生根据译文拟一个作文题目,随后进行片段式写作。
根据上述结构进行计算:

结果表明,模具有足够的强度。
但在实践中,对于一模双孔模具,特别是半空心铝型材的一模双孔模具,必须使用专用的支承模垫,否则,模具的寿命会大大降低。图3b方案所配合的专用支承模垫内孔结构如图8所示。专用支承模垫的厚度不应小于70 mm。
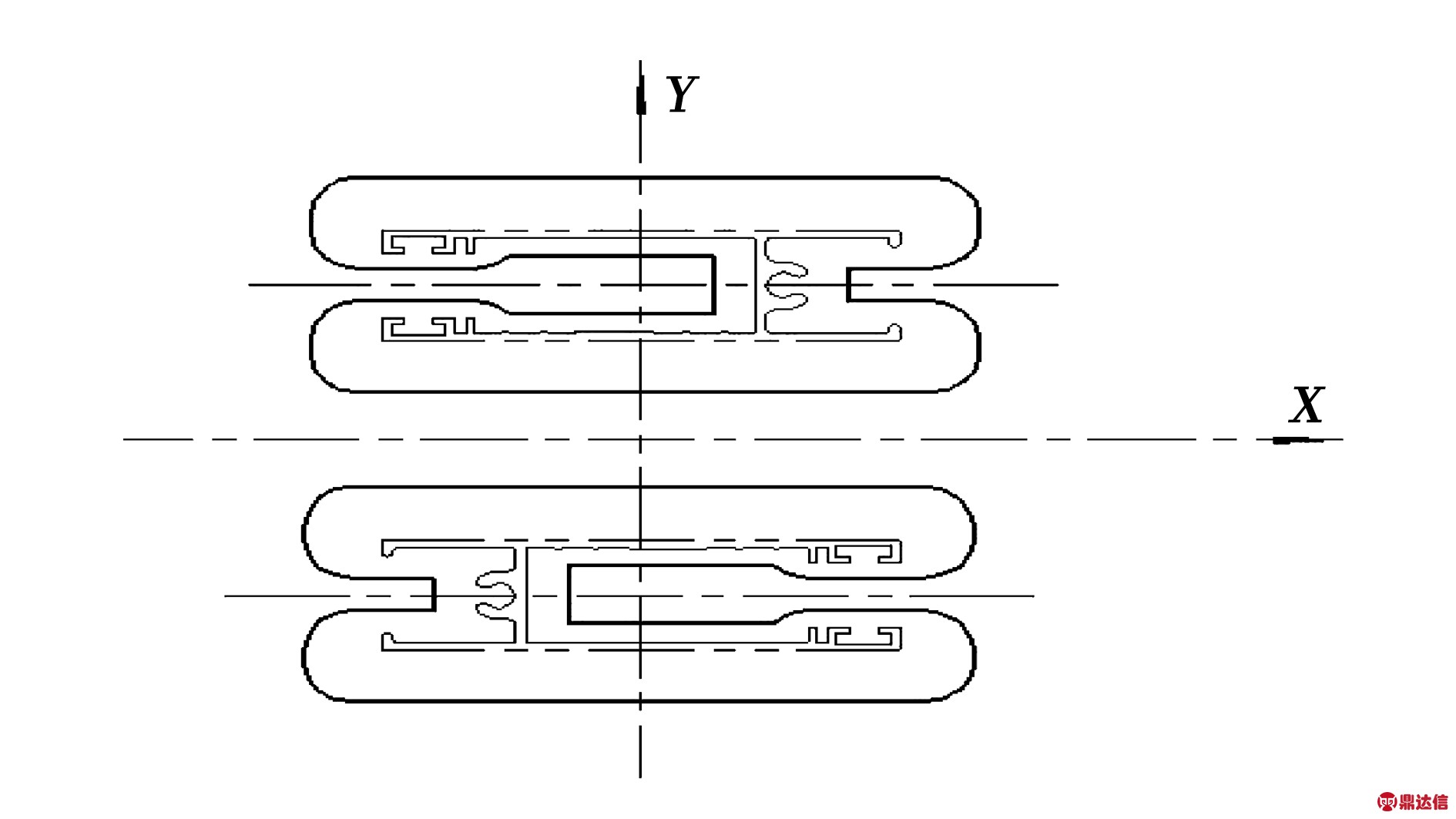
图8 专用支承垫内孔结构示意图
Fig.8 Inner hole structure of special die support
4 挤压结果对比
对图1所示铝型材采用传统的平面模、单孔切割式分流模结构和遮盖式一模双孔结构的模具进行试模与挤压跟踪,所得结果对比如表1所示。从表1数据可以看出,对于半空心铝型材采用遮盖式一模双孔分流模具有明显的优势,大大提高了模具的寿命,降低了型材的挤压模具成本。
表1 用不同结构模具挤压铝型材的结果对比
Table 1 Comparison of die structure and extrusion results
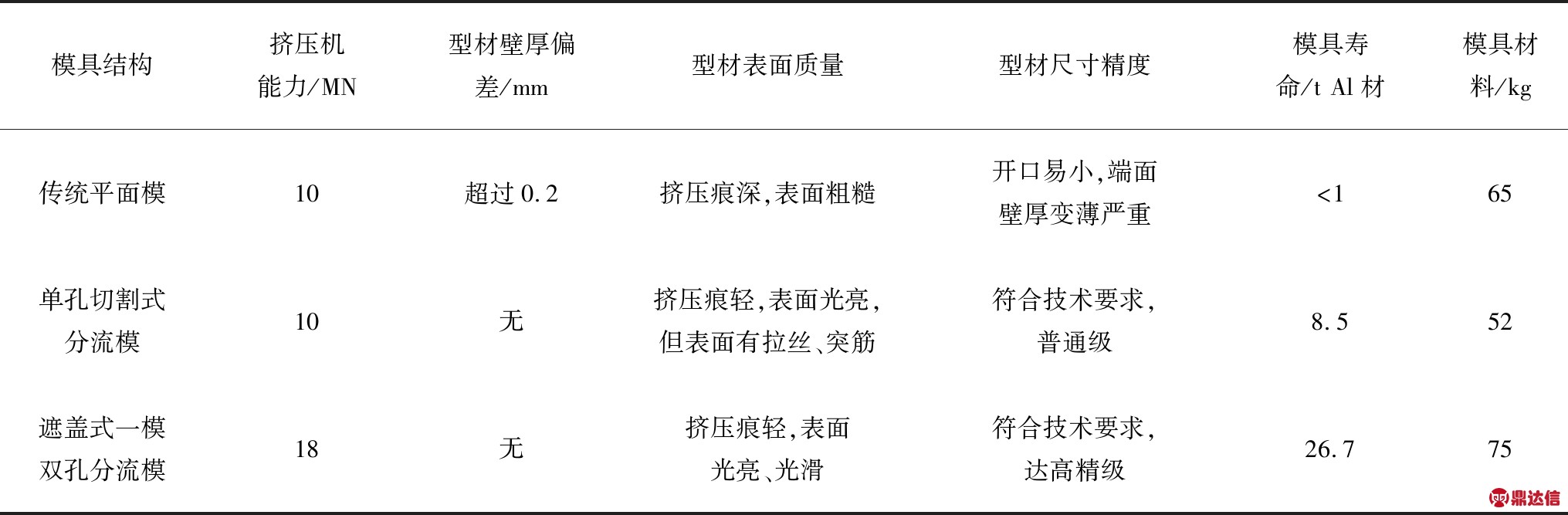
模具结构挤压机能力/MN型材壁厚偏差/mm型材表面质量型材尺寸精度模具寿命/t Al材模具材料/kg传统平面模10超过0.2挤压痕深,表面粗糙开口易小,端面壁厚变薄严重<165单孔切割式分流模10无挤压痕轻,表面光亮,但表面有拉丝、突筋符合技术要求,普通级8.552遮盖式一模双孔分流模18无挤压痕轻,表面光亮、光滑符合技术要求,达高精级26.775
5 结束语
对图1所示的半空心铝型材采用遮盖式一模双孔结构挤压模,试模和实际挤压结果表明:模具试模一次成功,模具经过氮化多次使用,挤压铝型材产量可达26.7 t。由此得出,采用这种新的模具结构可以大大提高模具的寿命,提高铝型材生产效率和降低成本。同时可以看出,模孔的布置、分流孔的设计、分流桥的结构以及下模焊合室的结构设计和工作带的选择是半空心铝型材一模双孔结构的关键。在设计过程中,借助计算机进行模拟更能提高设计的效率和准确率。