摘要:飞机维修过程中涉及的标准件螺栓修理数量庞大、规格多,导致筛选和故检工作量大。采用基于机器视觉的机器人技术设计的标准件螺栓智能检测系统,实现了标准件螺栓的高效自动检测与分类,为航空维修标准件螺栓的修理提供了技术支持。
关键词:标准件螺栓;机器视觉;机器人;检测
0 引言
随着“工业4.0”以及“中国制造2025战略”的开展与实施,智能化机器人在航空航天、医疗卫生、汽车工业领域得到了广泛的推广应用,航空维修也从传统维修逐步向智能维修的方向发展。航空标准件螺栓,特别是高价值的钛合金螺栓,由于单机数量多、价值高,具有较高的维修价值。但因其规格多,采用人工目视检查与分拣的维修模式,会因人体生理疲劳造成分拣错误和故障误判,不仅效率低下,工作质量也无法保证。本文针对航空维修过程中标准件螺栓故障检测与分类的困难,开发并设计了一套基于机器视觉的智能化检测系统,代替人工视觉检查。在航空维修领域使用机器人技术对标准件螺栓进行分类和故障检测尚属首次,该方法解决了航空标准件螺栓修理作业效能低下的难题。
1 总体结构设计与功能
一架飞机的标准件螺栓数量庞大、规格多,其中价值较高的钛合金螺栓的数量高达5000件以上,单独按照螺栓的种类分类打包的修理成本高、管理难度大,不利于标准件螺栓的高效快速修理。常规的维修采用集中分解与修理的模式,依据头部形状和螺纹规格进行分类,分类过程中同步开展故障检查,经修理合格后最终打包提交检测。考虑到检测螺栓的规格多、检测内容杂,整个智能化检测系统包含的功能相对较多、结构相对复杂,因此,螺栓的分类预判与故障检查工作由机器视觉完成,分类摆放的动作由机器人辅助完成。
1.1 系统功能
系统采用视觉检测方法,对多规格混杂的螺栓外形尺寸以及头部、螺纹部位磨损程度进行检测,从而判断螺栓的损坏程度及螺栓的具体规格,最后根据检测的螺栓规格对螺栓进行分类存放。系统主要功能为:
1)根据设定的规则对螺栓进行分类,螺栓主要特征参数如表1所示。
2)对螺栓表面缺陷进行检测,可以检测的部位包括螺栓的头部和螺纹部位。头部检测是检测十字槽或一字槽的槽型损坏程度;螺纹检测是检测螺纹损坏程度。
表1 螺栓特征参数
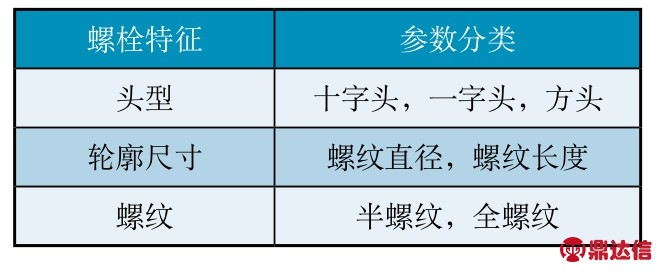
1.2 系统结构
按照功能分类的要求,系统主要由整列分料系统、夹持系统、视觉检测系统、存料系统、工控机、电控部分等构成。系统结构示意图如图1所示。
1)整列分料系统
螺栓稳定检测的前提是螺栓具有稳定的姿态,但是螺栓规格种类较多、形状各异,因此在视觉检测前需要对螺栓进行有序排列。考虑到供料的稳定性和及时性,采用机械振动盘对螺栓进行整列处理。振动盘用于整列螺栓,性能可靠,但用一个振动盘整列这么多种规格的螺栓,振动盘需要单独设计。根据螺栓的具体尺寸,振动盘设计了两条滑道,适合规格尺寸相近的螺栓,以保证后续螺栓逐一分料的可靠性,如图2所示。
螺栓通过整列系统有序地进入料道,并呈一字排开,采用错位分料的方法设计分料装置(见图3),并阻挡后续的螺栓进入料道;通过分料板与分料气缸实现两条料道螺栓的分料,由夹持气缸选取螺栓。
2)螺栓夹持系统
夹持系统分为气动夹手系统(见图4)和机器臂夹持系统(见图5)两部分,分别实现螺栓头部和螺纹部位检测的精确定位。系统的机械部分准确可靠地控制螺栓的位姿,为视觉系统准确识别检测提供硬件支撑。气动夹手通过直线模组将螺栓从整列分料系统转移到指定位置,实现对螺栓头部的识别和检测判断。气动夹手具有一定的适应性,可适用于多种螺栓的精确抓取。
因需要在螺栓检测后进行分类放置,而且分类种类很多,为了降低设备机械结构的复杂程度,考虑采用一个机械臂将螺栓放置到不同的位置,同时机械臂的末端带有可旋转工作的吸盘组件,适于对螺栓螺纹部位进行旋转,实现全方位的无死角检测。通过机械臂夹持系统机械臂上的吸盘吸附气动夹手系统中的螺栓,随后介入视觉系统,检测螺栓的螺纹部位,检测完毕后通过处理器进行图像处理,经判别将螺栓按照类别放入相对应的料盒中。
3)视觉检测系统
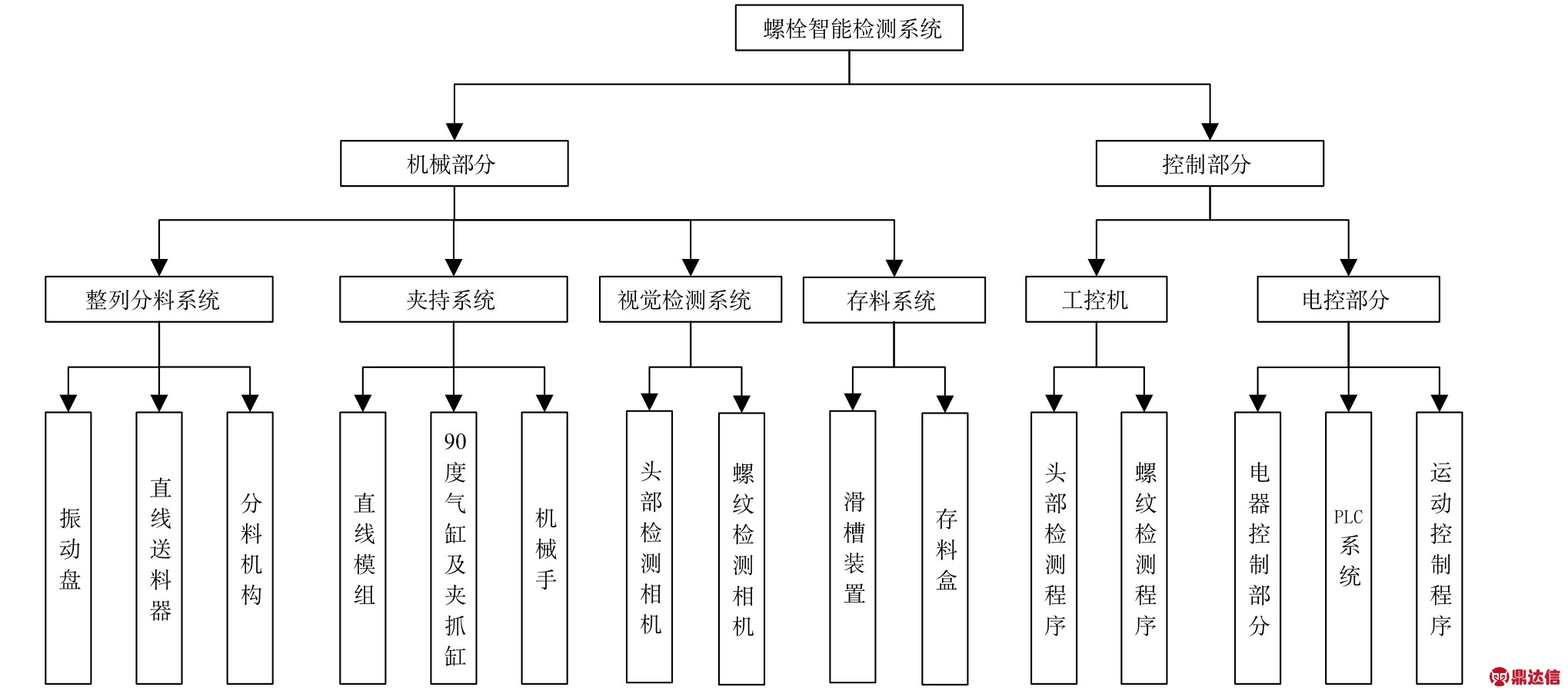
图1 系统结构示意图
视觉检测分为头部检测与螺纹检测,分别拍摄螺栓头部及螺纹部位的状态,将拍摄后的图像传递至工控机,由工控机进行计算,判断螺栓的状态是否满足指定的工艺要求。视觉检测系统的结构示意图如图6所示。
4)存料系统
存料系统包括滑槽盘、滑槽和存料盒等部分。若螺栓检测后合格,机械臂将完成检测的螺栓放入该种螺栓对应的滑槽盘上,螺栓沿滑槽进入对应类型的存料盒中;若不合格直接进入损坏件存料盒中。
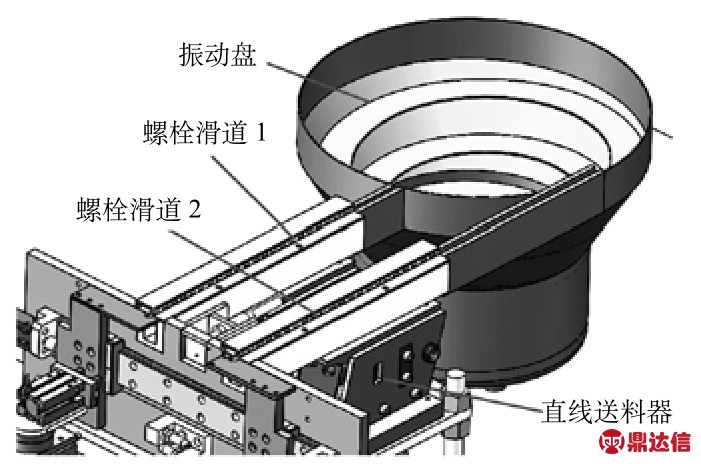
图2 螺栓整列系统
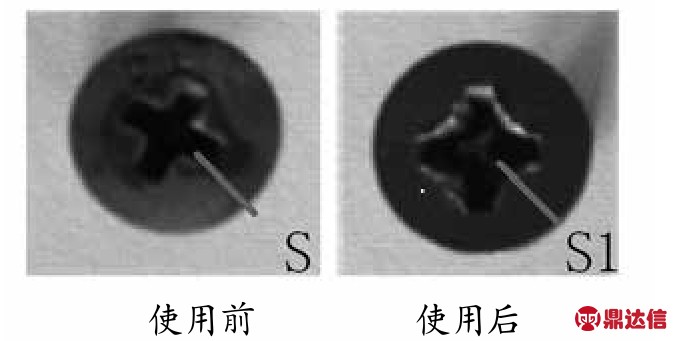
图3 螺栓分料系统
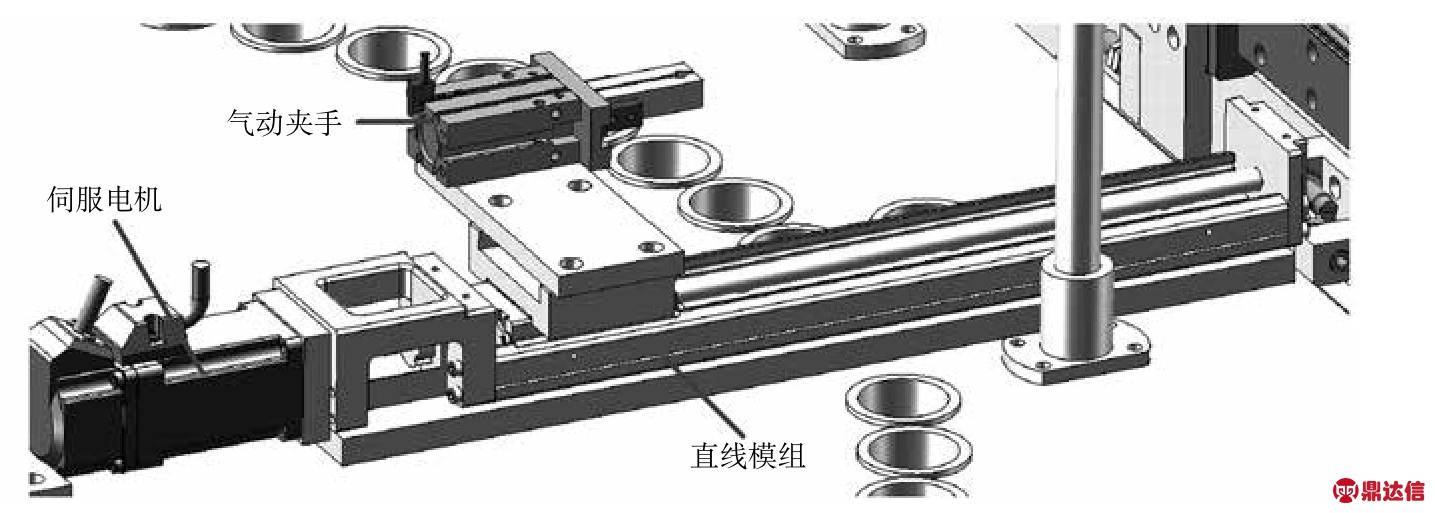
图4 气动夹手系统
2 视觉系统设计
视觉系统作为螺栓智能检测的核心执行系统,其精确度直接影响航空标准件智能检测的准确性与可靠性。因螺栓检测对象繁多(头部形状、十字槽磨损程度、螺栓直径规格、螺纹长度及磨损程度等),位置变化大,为了提高检测效率,使用两个相机同时工作,分别检测头部状态及螺纹部位状态。头部检测相机需要检测螺栓头部上表面的表面形态,选择环形同轴光源(相机和光源同轴,且处于检测物体的一侧)对头部进行打光操作,以便清晰显示出头部状态;螺纹部位检测相机需要检测螺纹部位的轮廓,采用背光源的打光方式(相机和光源处于检测物体的两侧),以便清晰显示出螺栓的轮廓,背光源的颜色为蓝色,这样可以降低打光时检测物体轮廓边缘的衍射,准确显示螺栓的轮廓。
由于检测后的螺栓需要进行分类操作,机械结构采用的机械臂的运动占用空间较大,相机相对螺栓布置的位置较远,为了避免检测时镜头距离物体过远导致拍摄的图像发生畸变,因此选择“远心镜头”,以纠正传统工业镜头的视差,可以在一定的物距范围内使得到的图像放大倍率不发生变化,这对被测物不在同一物面上的情况有非常重要的作用。
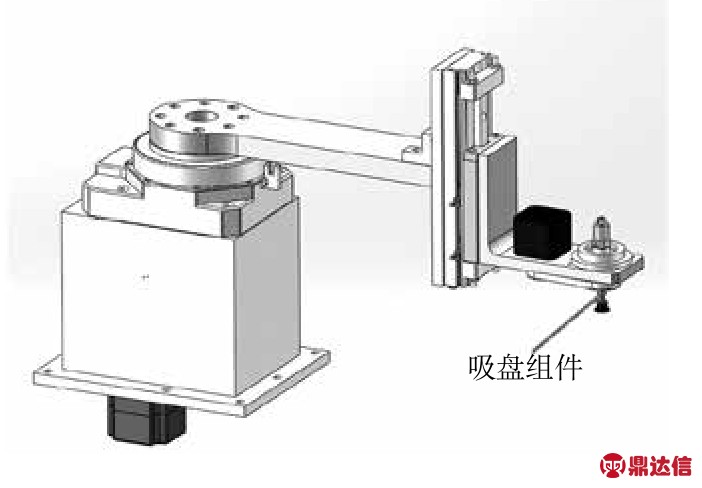
图5 机械臂夹持系统
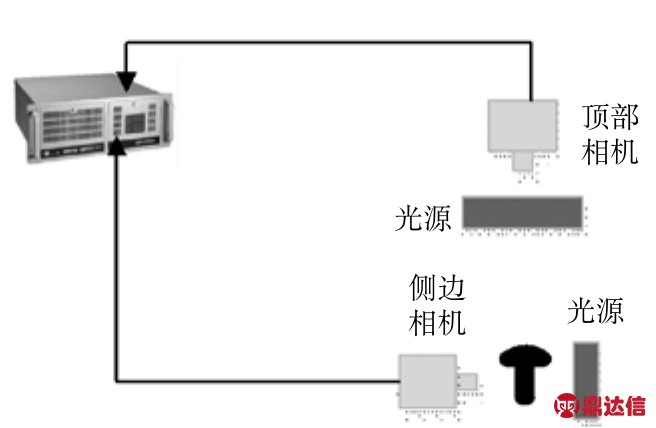
图6 视觉检测系统示意图
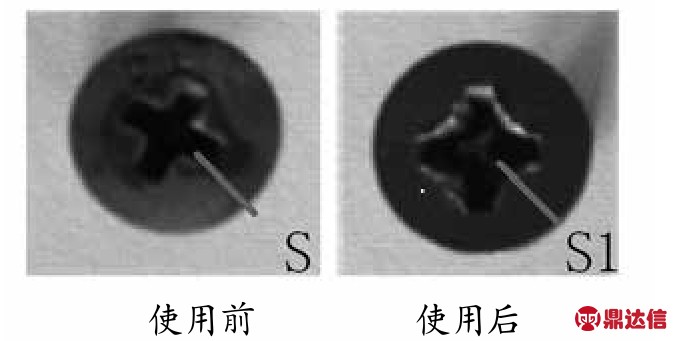
图7 十字槽使用前后对比
3 图像算法设计
视觉系统产生的图像需要通过特定的图像算法进行处理,以满足螺栓检测的工艺要求,图像算法的设计会直接影响系统的可靠性和运行效率。机械部分的运行时间和图像处理的时间应保持节拍一致,需采用一种快速的图像算法,在机械部分工作过程中完成图像处理。图像处理顺序与视觉系统拍照顺序应保持一致,首先进行螺栓头部的图像处理,随后完成螺纹部位的图像处理,分别由中控机在特定的图像算法下完成图像处理。
3.1 螺栓头部图像处理
螺栓头部十字槽的磨损面积超过20%即为不合格,低于20%的为可以打磨的零件。将未使用过的螺栓十字槽的面积设定为S,使用后的螺栓十字槽的面积为S1,当S1/S>1.2时,则螺栓不合格;当S1/S<1.2时,则螺栓合格,如图7所示。因为少数螺栓存在十字槽单个槽位损坏的情况,在图像计算过程中对十字槽采用分割处理,单独计算。
陶瓷是一种古老的塑造艺术形式,从我国仰韶文化时期陶器大量制造和使用开始,陶瓷就进入了人们的生活,并且随着社会生活的变化和人类历史的发展,不断进化和创新,从生活器皿逐渐转变为极具应用价值的生活艺术制品,深受人们的喜爱。如何展示陶瓷装饰艺术的美感,提升人们的审美感受性以及使用便利性,值得我们进行思考和探索。

图8 螺栓头部处理示意图
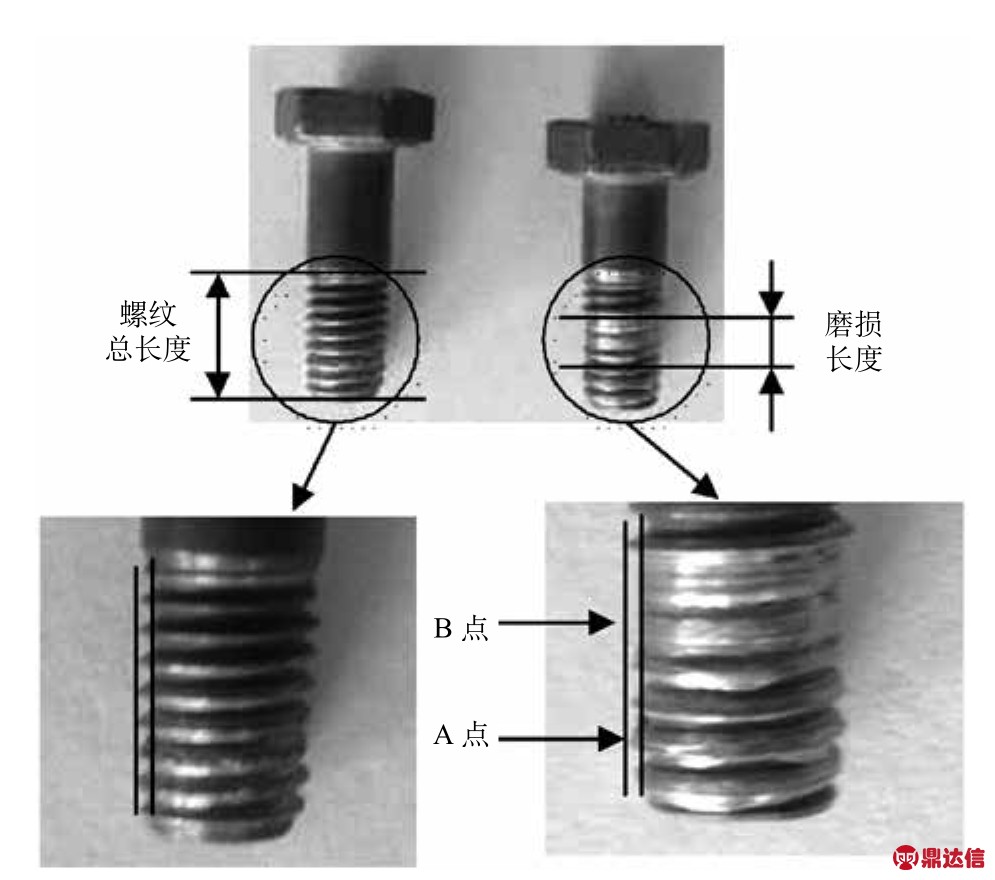
图9 螺纹检测参数描述图
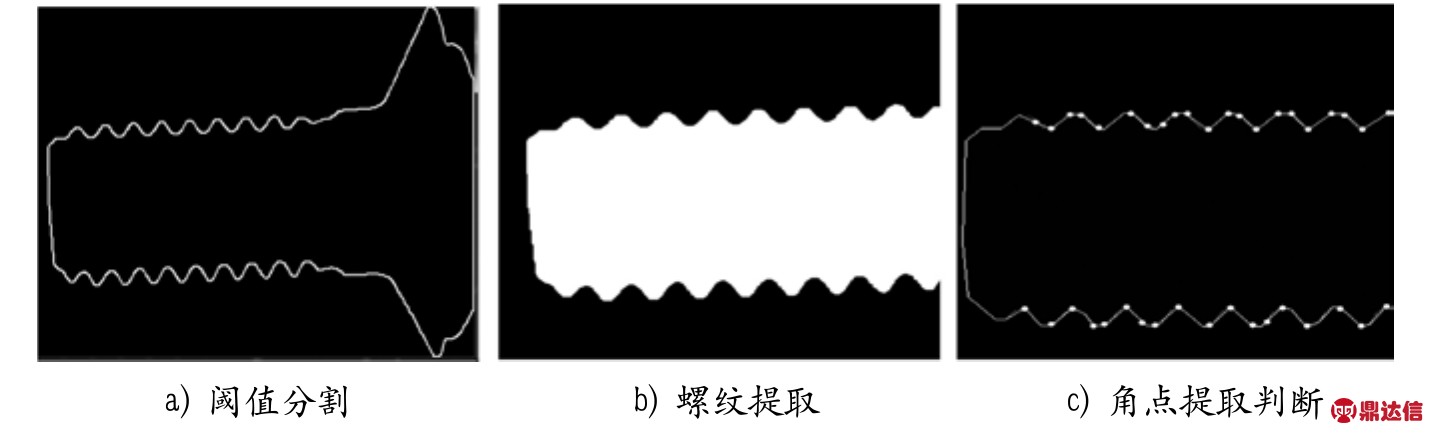
图10 螺纹图像处理示意图
螺栓头部图像处理过程如图8所示,主要包含5个步骤:
1)相机读入螺栓头部图像,经过滤波锐化和分割,提取直线以判断头部形状。
2)对应圆头螺栓,提取并旋转校正十字槽。
3)对十字槽进行膨胀腐蚀等形态学处理,消去边缘毛刺。
4)从十字槽的中心分割十字槽。5)计算十字槽的特征参数,判断十字槽是否合格。
3.2 螺纹部分图像处理
当螺纹磨损部分长度超过螺栓或螺栓总螺纹长度的1/2时即为不合格。即当螺纹某点剩余高度低于螺纹标准高度的1/2时,设定以该螺纹检测点为中心,1/4个螺纹导程内的螺纹不合格。如图9所示,A点剩余的螺纹高度超过螺纹标准高度的1/2,为合格;B点剩余的螺纹高度低于螺纹标准高度的1/2,为不合格。螺纹不合格的长度总和为螺纹的磨损长度,当磨损长度超过螺纹总长度的1/2时,则该螺栓不合格。
螺纹图像处理示意图如图10所示,主要包含以下3个步骤:
1)相机读取螺纹图像,提取图像的蓝色通道,进行阈值分割,提取螺栓部分。
2)提取直线,检测螺纹位置,提取螺纹。
3)校正螺纹,提取角点,计算螺纹参数,判断螺纹是否合格。
4 结束语
机器人技术正在大面积推广应用,可将人员从繁杂的体力劳动中解放出来。航空维修企业技术升级改造和产能提升可以通过机器代人的方法逐步实现,如采用智能故检、智能除漆、机器人辅助机械加工、智能检测、部附件智能物流等方法。本文利用机器视觉等机器人技术实现了高附加值航空标准件螺栓维修模式的变革,开发出一套针对不同规格螺栓的整列分料系统,提出了一种视觉系统和图像算法相结合的检测方法,实现了多品种、多规格标准件螺栓的智能检测与分类,生产效率得到了成倍提升。
本文的研究设计成果已在航空维修标准件修理中推广应用,并具有柔性化,可依据用户需求,对图像算法进行调整,以适应不同规则下标准件螺栓的分类与故障检测要求,可为航空维修企业在高价值标准件螺栓修理上提供参考,为航空维修企业推广智能化应用提供借鉴。