摘要: 内构件技术的开发与应用对于提高工业设备的利用效率、降低其能量损失具有重要意义。旋风分离器是用于气-固分离的工业设备,随着化工过程的发展,工艺上要求在保证分离效率的同时,能够减小压降。首先对旋风分离器的工作原理进行了介绍,分析了其减阻增效的机理。相比于结构优化和其他措施,安装内构件能够降低生产成本和缩减工程量。概述了减阻杆、导流叶片、稳涡器等几类内构件的工作原理和能够解决的流动问题。得出结论:在不改变旋风分离器结构尺寸的情况下,安装内构件能够改善旋风分离器内的干扰涡流,提高内部流动的稳定性,从而有效地实现分离器的减阻增效。此外,对内构件的发展趋势进行了展望。内构件的组合使用以及新型高效减阻内构件的开发,会更倾向于多元化、细致化、精确化、简约化,不仅能够提高分离效率,而且可以满足各种环保及工艺要求。
关 键 词: 旋风分离器;减阻增效;内构件;减阻杆;导流叶片;稳涡器
旋风分离器是利用离心力作用,进行气-固分离的工业设备。由于其结构简单、操作方便、处理量大等优点,被广泛应用于工业除尘、石油化工、煤炭发电等领域。分离效率和压力损失是衡量其性能优劣的两大指标,两者往往成正相关性[1-2],“随之增大”或“与之减小”。随着化工过程的发展,工艺上要求在保持较高分离效率的同时,能够降低压降,从而降低能耗。
国内外众多学者提出了各种减阻增效的方法和措施[3-6],主要集中在三个方面——结构优化、安装内构件和其他措施。包括校直排气管中的旋转气流,如安装导流叶片、消旋器等;改善入口结构,安装导流板,减少颗粒聚集;改变内部流场,提高其流动的稳定性,如安装稳涡器,减阻杆等;进行结构优化,开发新型高效旋风分离器,如无上排气管结构[7]等。但是,在工业实际应用过程中,若采用更换旋风分离器的方式,将会增加生产成本和扩大工程量。因此,在不改变分离器原有尺寸的情况下,通过添加内构件来提高分离性能,成为学者们研究的热点。
目前,在旋风分离器的工业应用中,通过内构件来减阻增效是一种行之有效的方法。然而,关于旋风分离器内构件的系统性分类,以及内构件技术的发展方向,研究报道尚很少见。笔者在概述旋风分离器工作原理的基础上,通过对内部流场的分析,阐述减阻增效的机理,并系统介绍减阻杆、导流叶片、稳涡器等几类内构件的工作原理和使用效果,以及内构件技术的研究进展,并展望旋风分离器内减阻增效内构件的发展趋势,以期为旋风分离器的性能改进提供参考。
1 旋风分离器的工作原理
旋风分离器结构形式复杂多样。根据进气形式来分,常用的旋风分离器有两类,切流反转式和轴流反转式,如图1所示。含有固体颗粒的气流由入口沿直线进入旋风分离器,受圆筒形壁面的约束,转变为绕壁旋转的圆周运动,沿着壁面螺旋向下,形成“外旋流”。受旋转产生的离心力作用,密度较大的固体颗粒被甩向壁面。颗粒一旦与壁面接触,便依靠入口速度产生的动量和重力的沉降作用,沿壁面下落,最终进入灰斗。外旋流向下到达圆锥体部位后,壁面的收缩使转速显著提高,并且随着直径的减小,外壁压力不断增加,在锥体的中间区域形成低压区。在高压区的作用下,气流向中心靠拢,并在底部由下向上返转,继续做螺旋运动,直至经排气管排出,此即为“内旋流”。部分在下行流区域未被分离的颗粒会被甩向外旋流区重新进行分离,另一部分未被捕集的细小颗粒则从排气管逃逸。

图1 旋风分离器的结构示意图
Fig.1 Structure of cyclone separator
(a) Tangential flow reversal cyclone separator;(b) Axial flow reversal cyclone separator
2 旋风分离器减阻增效的机理
虽然旋风分离器结构简单,但其内部流场却为复杂的湍流流场。其中,外旋流对颗粒的捕集起到积极的作用,而内旋流对颗粒的捕集不起作用,属于消耗性能量[8]。除内旋流和外旋流外,还存在若干干扰涡流。这些干扰涡流在不同程度上影响分离效率和压力损失。其中,环形空间的纵向环流使颗粒聚集形成“顶灰环”,排气管下口附近的短路流使颗粒逃逸,锥体下部排尘口附近的偏心环流使颗粒返混,对分离效率影响较大。据此,旋风分离器内减阻增效的机理可以总结为:提高外旋流区的旋转强度,抑制内旋流区的发展,降低干扰涡流的能量损失,从而提高分离效率。
3 旋风分离器内构件的分类及研究现状
在工业实际应用中,若采用新的旋风分离器替代原有分离器,会使成本和工程量变大。在不改变旋风分离器结构尺寸的情况下,采用添加内构件的方法是一个节约、简单的方案。根据结构形式和解决的工业问题分类,笔者主要介绍减阻杆、导向板、减阻框、中置物和导流叶片等几类内构件的工作原理和使用效果,并概述其工程应用研究现状。
3.1 减阻杆
减阻杆,通常是一根特定形状的刚性杆件,安装在旋风分离器内适当位置,起到降低压力损失,稳定涡流的作用。减阻杆形状不同,所形成的绕流尾涡形态不同,对流场的影响也不同。减阻幅度与减阻杆的迎风面积、背风面曲率半径以及插入深度有关,安装示意图如图2所示。安装减阻杆,可以形成绕流尾涡与原流场中的涡流相互作用,能够抑制内旋流的旋转强度,降低湍流脉动,使内旋流的湍流能量耗散大幅减低。Wang等[9]、Gong等[10-11]在旋风分离器内添加减阻杆,发现能够大幅减低旋风分离器内的阻力,引发了国内外专家对减阻杆的机理和优化的研究[12]。Liu等[13-14]利用激光多普勒测速仪(Laser doppler velocimetry,LDV),对比测试了安装减阻杆与否对旋风分离器内流场的影响,结果表明,安装减阻杆会使速度梯度减低,湍动耗散减弱,压力损失减小。敖龙等[15]、王政威等[16]对直径为150 mm螺旋形旋风分离器进行实验,发现减阻杆直径为30 mm时减阻幅度最大可达26.68%;减阻杆直径大于80 mm时,不仅不能减阻,压降反而增加。总的来说,安装适宜的减阻杆能够降低内旋流的能量耗散,稳定涡流,从而达到减阻、节能与增产的效果。
3.2 导向板
导向板,通常安装在入口处,抑制压缩现象的发生,改善入口处的流动。压缩现象是指含有固体颗粒的气流沿切线方向进入旋风分离器,因环形空间轴向作用产生的上行曳力较大,部分气流在旋转1周后斜向吹到随后进入的气流上,导致入口进气偏向筒壁,产生挤压,形成压缩作用。压缩现象不仅使壁面处颗粒的流速增大,增大了壁面摩擦力,形成冲蚀作用,而且严重时会造成颗粒聚集,形成“顶灰环”,导致压力损失增大,分离效率降低。安装导向板,可以使旋转1周后的气流呈小曲率半径旋转向下,抑制了压缩现象,从而有效地提高分离效率。导向板的安装技术简单方便,对传统分离器的改造以及提高其分离性能具有重要的意义。
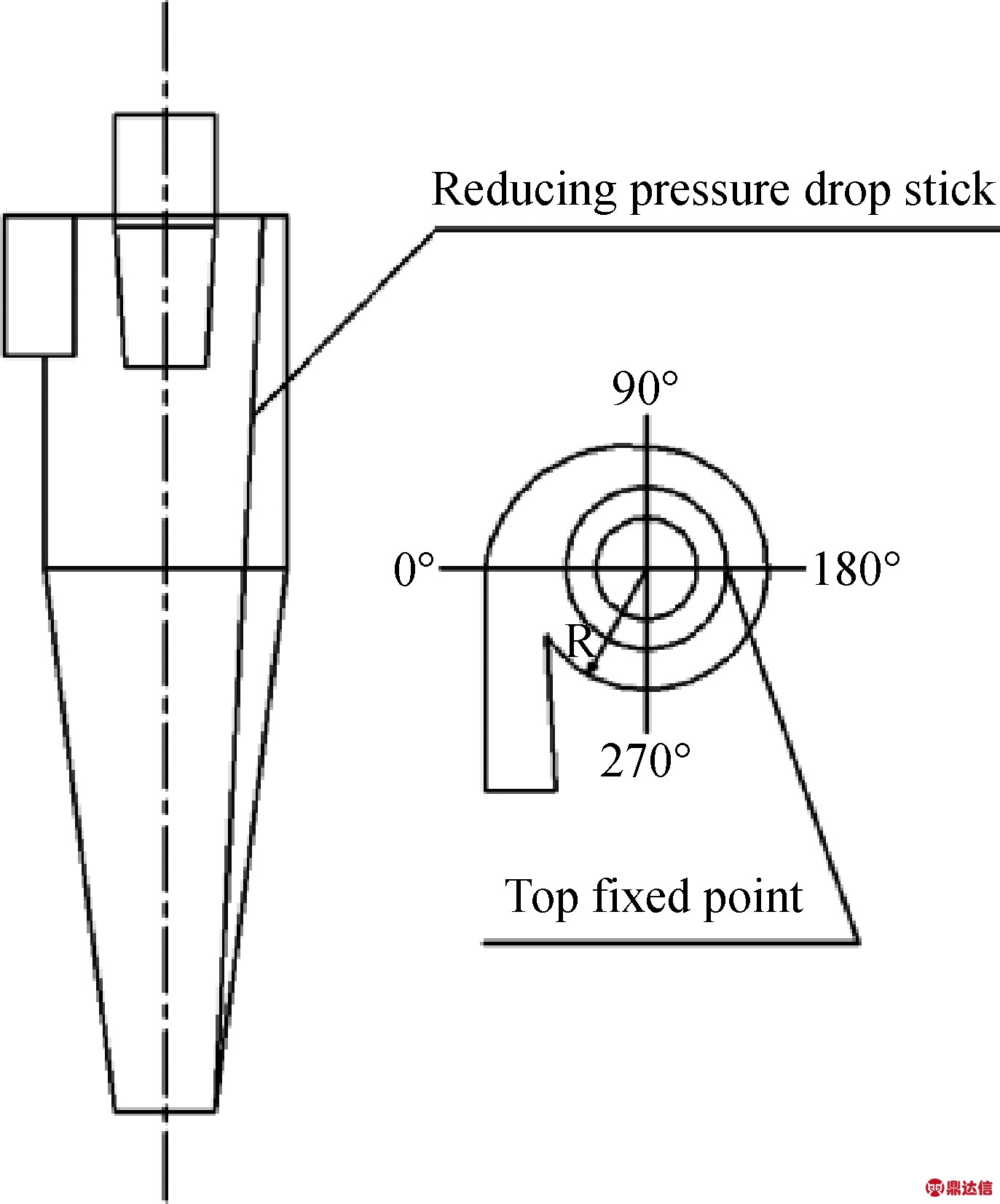
图2 旋风分离器减阻杆的安装示意图
Fig.2 Schematic diagram of pressure drop mitigationstick in the cyclone separator
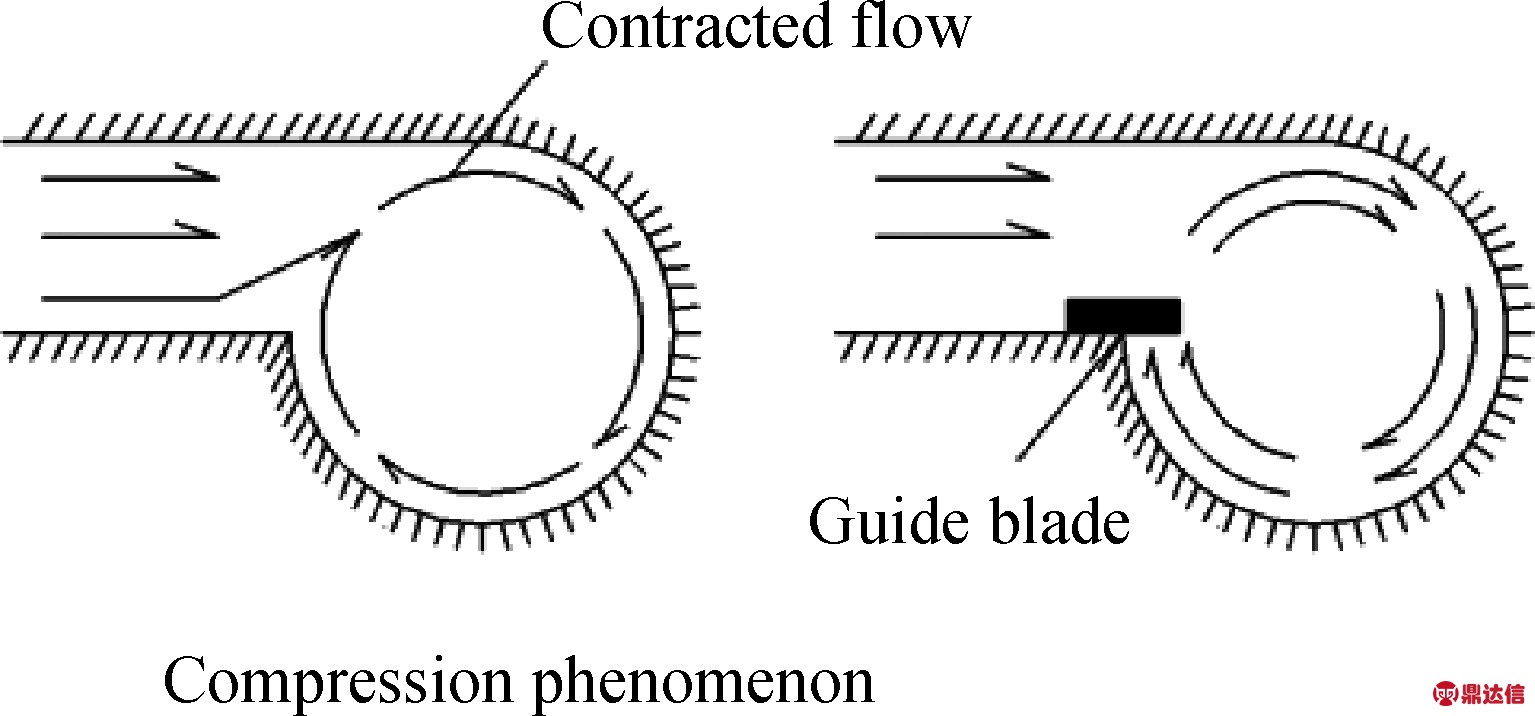
图3 压缩现象及导向板安装位置示意图
Fig.3 Compression phenomenon and location of guide blade
图3为压缩现象及导向板安装位置示意图。李利等[17]对不同尺寸的导向板进行研究,发现适宜的导向板能够减少“顶灰环”现象,证明了导向板可以降低压力损失,提高分离效率。祝立萍等[18]研究表明,导向板能够规整旋风分离器内部的涡流状况,对涡流有导流、引流的作用,可以降低10%~40%的阻力损失。Silvac等[19]、刘文欢等[20]在入口处增设不同形式的导向板并进行对比分析,发现相对于方形导向板,弧形导向板的综合效果更佳。导向板的形状和尺寸大小[21-23]不同,对分离效率和压力损失影响不同。只有适当的形状和尺寸,才能既降低压力损失又提高分离效率。
3.3 中心体结构
中心体结构,又称内筒、芯筒,通常放置在中心轴处,分离内外旋流,有效地消除内外旋流相互交叉、掺混、碰撞摩擦产生的能量损失[24-25]。中心体结构形式多样,对压力损失和分离效率的影响各有不同,中心体结构及分流型芯管的结构示意图如图4所示。赵萍等[26]提出具有内外双筒结构的分离器能够降低压降,更有利于颗粒的分离。Griffiths等[27]发现,中心体结构的直径为筒体直径的0.6倍时,能够最大程度地降低压降。中心体结构不仅能够保证外旋流的旋转强度,减弱气流旋进涡核(Precession vortex core,PVC)运动,减少内旋流的能量损失,而且可以有效降低排气管内气流的旋转强度,提高分离效率。
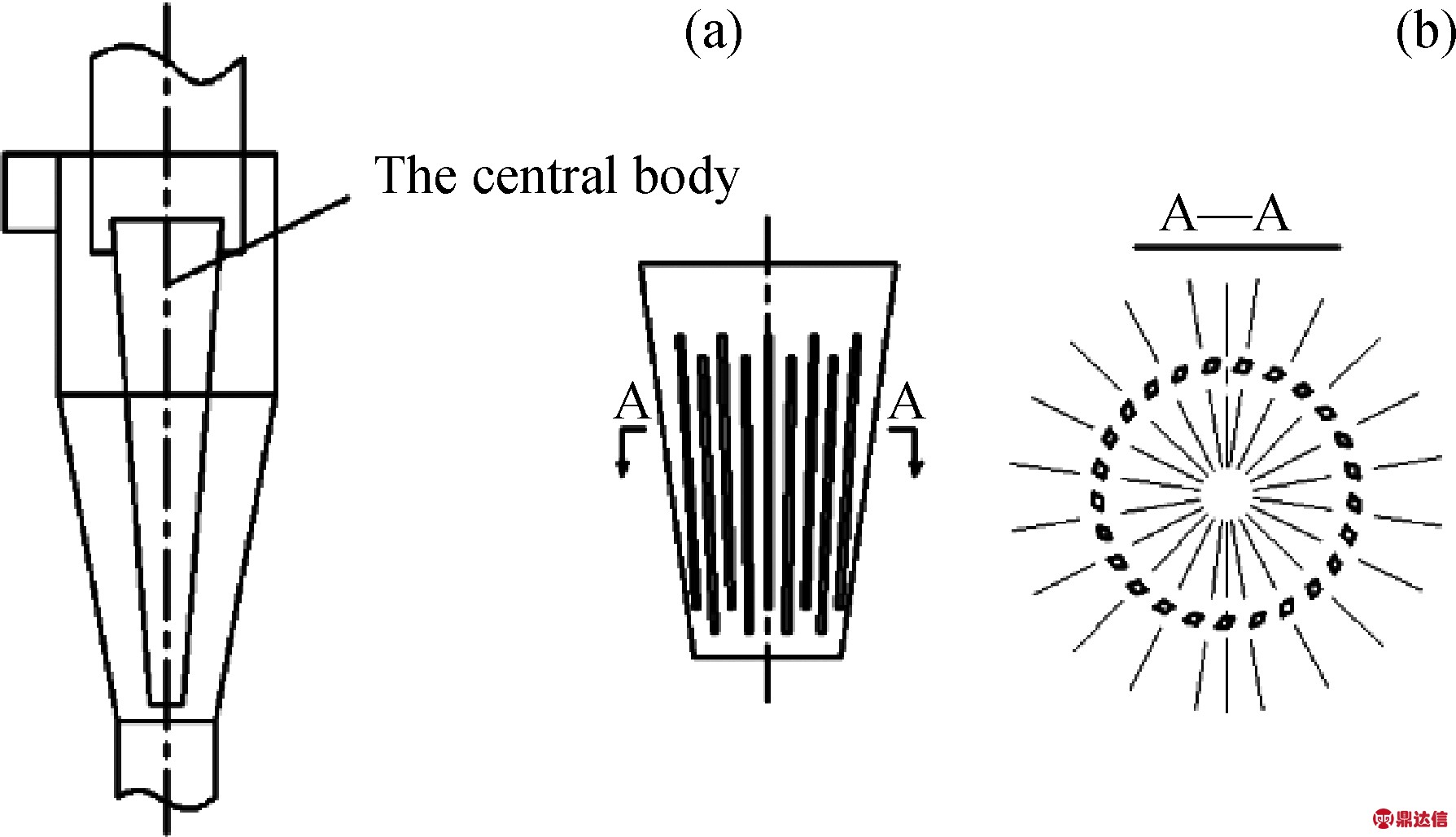
图4 中心体结构及分流型芯管的结构示意图
Fig.4 Structure of central body and split coretube in the cyclone
(a) Structure of central body; (b) Structure of split core tube
目前,毛羽等[28]、陈建义等[29]开发的“分流型芯管”在工业上得到广泛应用,结构如图4(b)所示,将其安装在排气管下端,既可防止粗颗粒因弹跳而被带出,又能有效地提高细粉的捕集效率。Li等[30]、金有海等[31-32]在PSC旋风管内添加分流型芯管,发现可以有效地抑制排气管下口的“短路流”,降低颗粒在排气管下口被“短路流”夹带的概率。Xiong等[33]、王建军等[34]对分流型芯管不同开缝位置(如图5所示)进行研究,发现开缝能够使压降在不同程度上降低,上部开缝时压降最低,下部开缝能提高分离效率。在旋风分离器内安装中心体结构,可以减弱内旋流的旋转强度,降低旋进涡核运动,达到减阻效果。如果优化中心体结构和安装导流叶片,分离效果更佳。
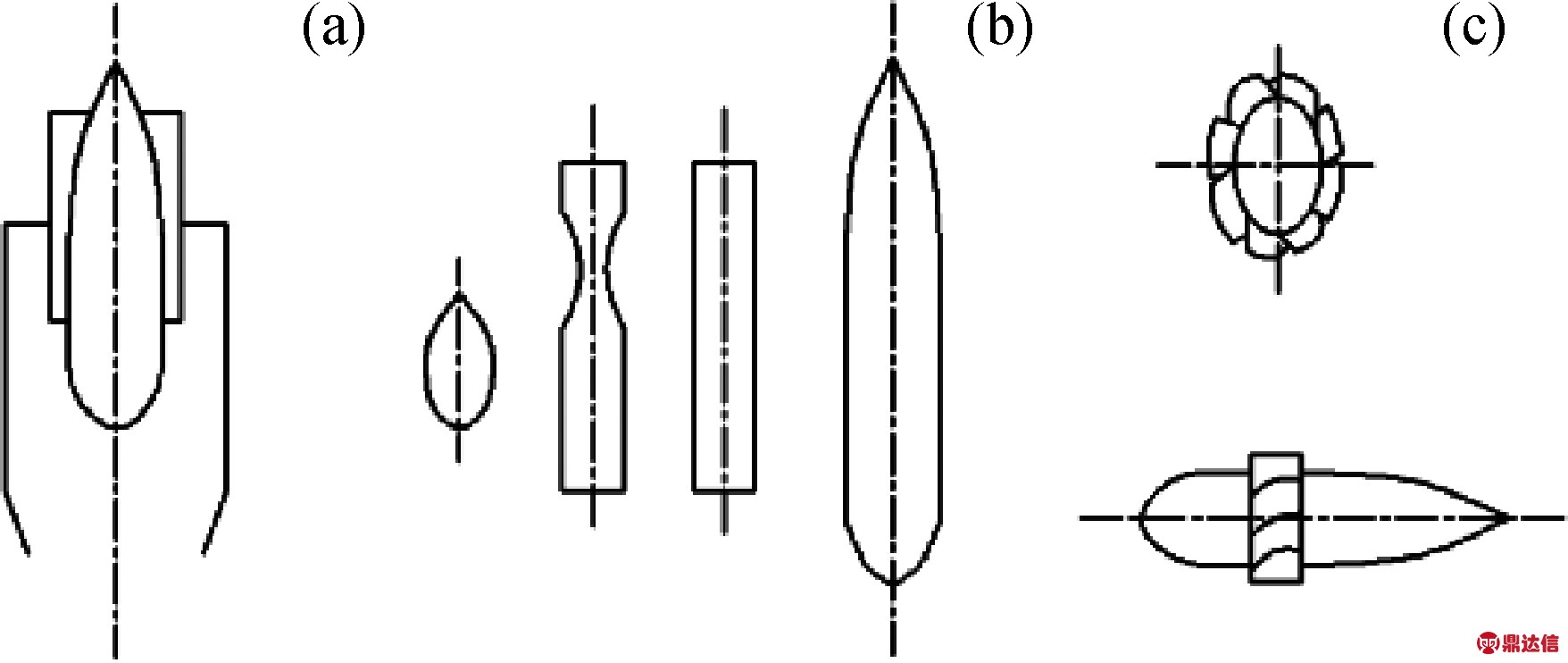
图5 开缝位置示意图
Fig.5 Location of open seam
(a) No seam; (b) Global seam; (c) Top seam; (d) Bottom seam
3.4 减阻框
减阻框,多用于轴流式旋风管[35],通常安装在排气管下部,用于降低排气管内气流的旋转强度,减弱“滞流”、“倒流”、逆压梯度等耗能流动。安装减阻框,对分离空间内的气流流动影响较小,能够保证分离效率。常见减阻框型式有栅格减阻框、直杆减阻框和锥形减阻框3种,如图6所示。杨建国等[36]用由4根圆杆(直径为8 mm,杆长200 mm)组成的直杆减阻框进行实验,将其安装在排气管内。结果表明,安装减阻框后,排气管内气流脉动减弱,阻力特性曲线明显向下偏移,相同流量下压降降低。后经大量实验表明,平均减阻幅度可达9%。马庆磊等[37-40]对比分析了3种减阻框结构,发现安装栅格减阻框、直杆减阻框均能不同程度降低压降,减阻幅度大小不同,直杆减阻框减阻幅度最大为26.56%,而栅格最大可减阻7.28%;但是安装锥形减阻框,压力损失反而会有一定程度的升高。随后,金有海等[31,40]对减阻效果明显的直杆减阻框展开流动分析,发现直杆减阻框能减小气流的切向速度峰值,使气流旋转强度降低,从而使排气管内能量耗散减少;改善了轴向上的压力梯度,降低了压力损失;对下行流影响不大,能够削弱排气管中心区域的滞流与回流。这些因素都有利于旋风管内颗粒的分离,能够提高其分离效率。
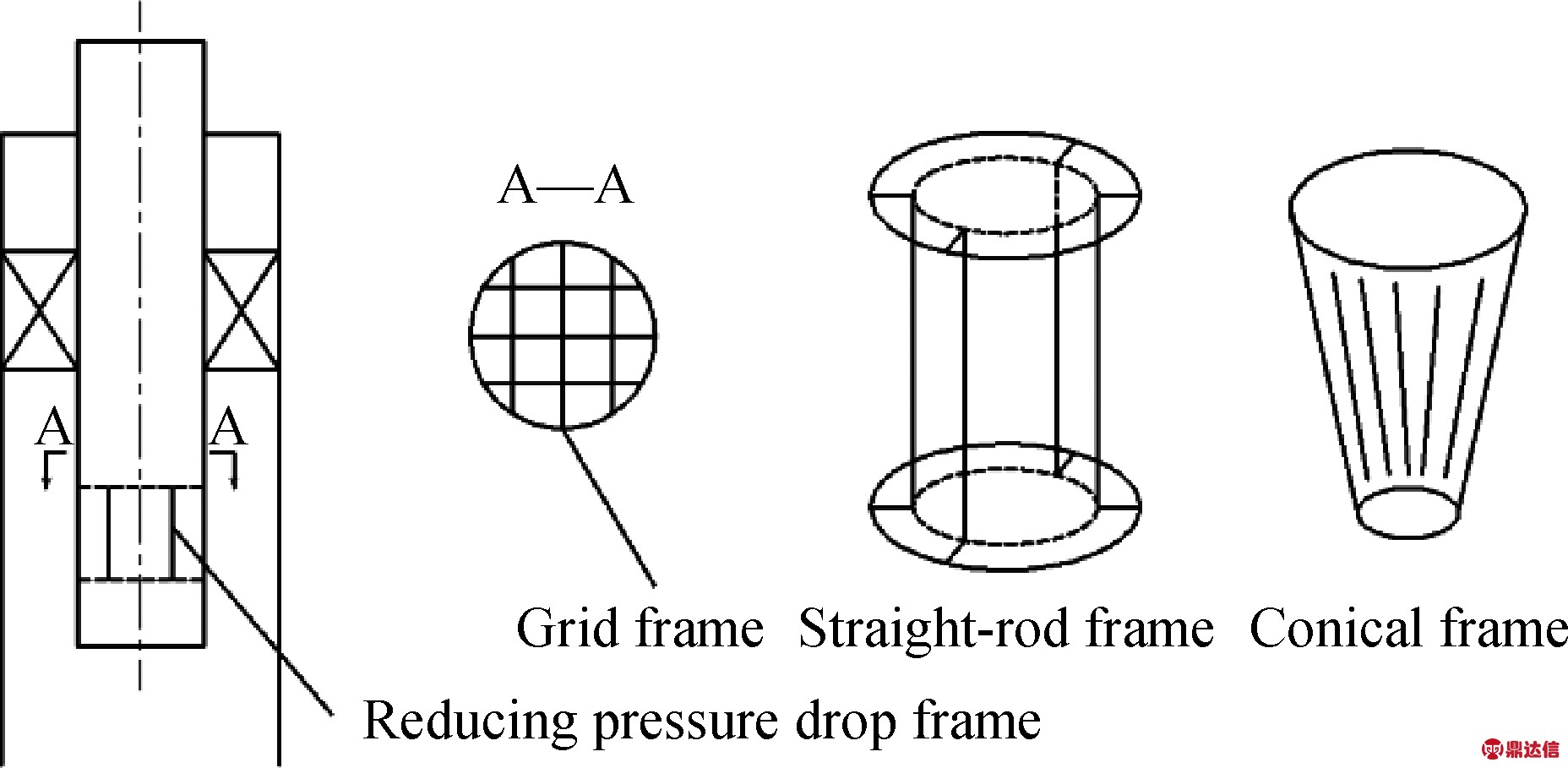
图6 减阻框及其安装位置示意图
Fig.6 Structure and location of reducing pressure drop frame
3.5 中置物
中置物,形式复杂多样,如图7所示。安置中置物,能够填堵轴心区域的高负压区,改变压力梯度分布。此外,中置物一般只对内旋流区起作用,对外旋流影响较小。这样就保证了对分离起决定作用的外旋流的旋转强度,因此对分离效率几乎没有影响[41]。然而,中置物形状和尺寸不同,对流场的影响不一。若中置物选择不当,不仅不能减阻增效,反而会增阻减效,所以选取合适形状和尺寸的中置物是非常关键的。刘金红等[42]在旋风分离器轴心及出口区域放置各种形状的减阻物,分别测量了分离器内三维速度及压力分布,分析分离器内各部分的压力分配情况,结果显示,导弹形减阻器效果最佳,可使分离器压降降低27.9%,效率提高28.2%。Ogawa等[43-44]发现将中置物设计成椭球体,能够防止边界层分离,若其后设计成锥形,类似“子弹头”,则形成简单扩压器,能够将动能转化为压力能。能够解决工业问题的中置物才是合适的,中置物的结构形式与安装与否应根据分离器的具体结构和实际工业应用而定。
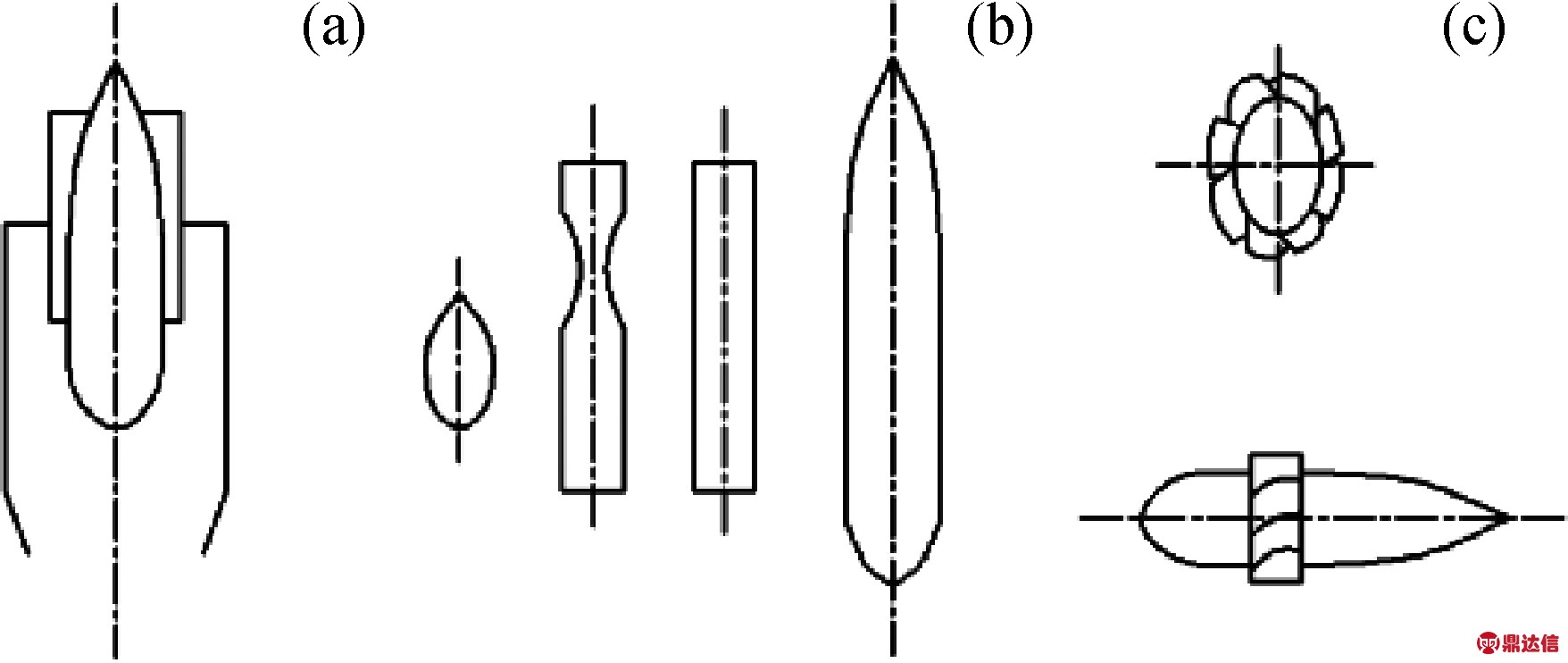
图7 不同形状中置物及其安装位置示意图
Fig.7 Different shapes and installationpositions of middle objects
(a) Installation positions of middle objects;(b) Different shapes of middle objects;(c) Position and shape of vane
3.6 导流叶片
导流叶片,又称整流叶片,通常安装在排气管入口处,校直排气管内旋转气流[45]。导流叶片的形式不同,效果也不同。常见的导流叶片类型包括直螺旋叶片、圆弧叶片[46]以及倾斜平板式叶片,如图8 所示。Prandtl等[47]首先提出导流叶片的概念;Sheperd等[48-49]将导流叶片安装在排气管下方,发现导流叶片能够在保证效率的同时降低压降。陈秉林等[50]设计了一种酷似风扇叶片的导流叶片,用于CX型旋风分离器,减阻可达22.8%。Browne等[51]设计了更完善的消旋器,其结构与图7(c)所示较为类似,中心为椭球体,叶片数为8,使阻力下降了22%。Lim等[52]、李矿林等[53]针对直叶片、大圆弧叶片、小圆弧叶片等形状的导流叶片进行实验研究。结果表明,压降均有不同程度的减小,其中大圆弧导流叶片最高可减阻23%;但其没有说明分离效率的变化情况。蒋明虎等[54]、赵立新等[55]分析了叶片的结构参数对分离器内部速度场和压力场的影响。结果表明,在一定范围内,压力随角度增大而降低,适当增大角度可以减小压降和能耗。总的来说,适宜的导流叶片能够减弱排气管内气流的旋转,减少能量耗散,降低压力损失。
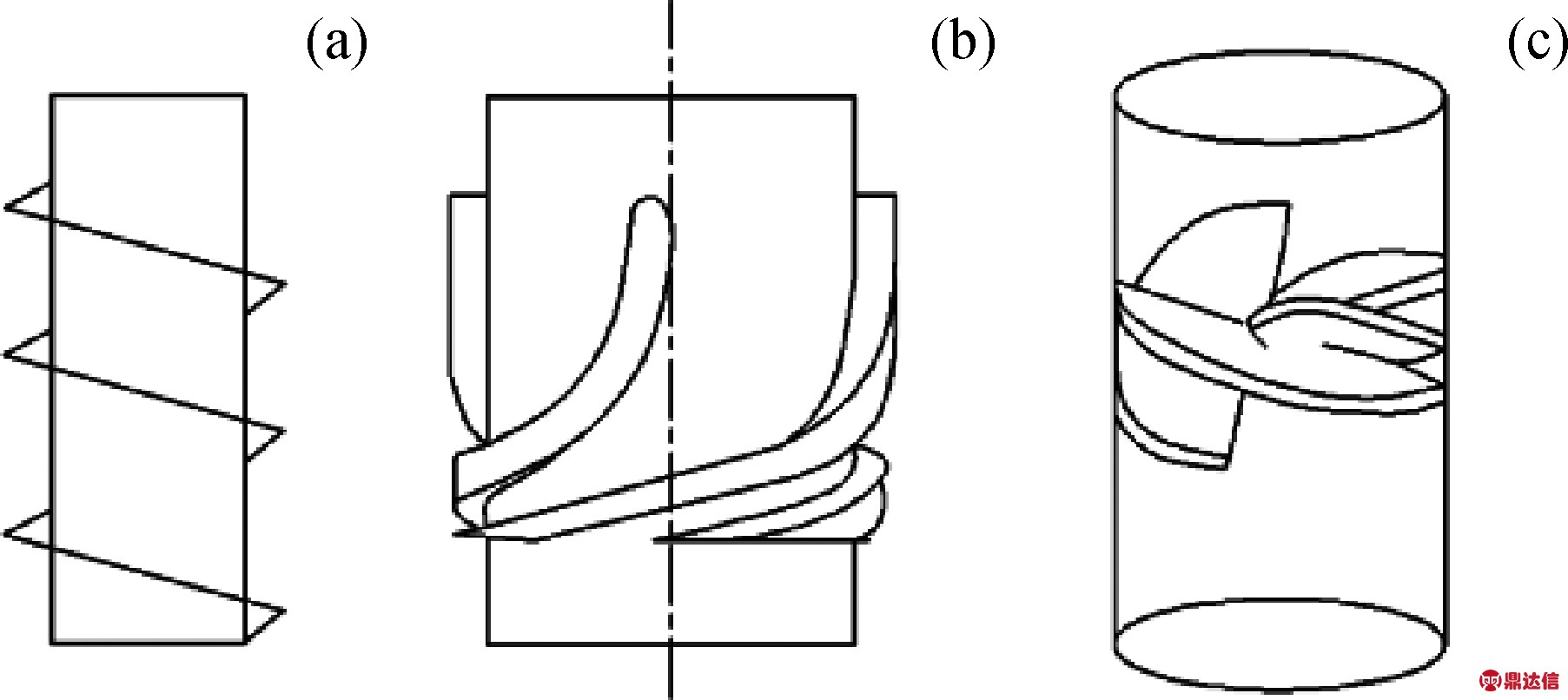
图8 导流叶片结构示意图
Fig.8 Schematic diagram of guide vane structure
(a) Straight spiral vane; (b) Circular arc vane;(c) Inclined plate vane
3.7 稳涡器
稳涡器,如防返混锥、稳涡罩等,安装在分离空间尾部或者料腿顶部(如图9所示),能够抑制料腿上方的颗粒返混,使颗粒更好地被捕集。吴小林等[56]在旋风分离器灰斗上方添加防返混锥,发现防返混锥能够大幅降低旋进涡核的强度,缩小其范围,而且能够较好地抑制已分离颗粒的返混。Dorfeshan等[57]、孙国刚等[58]研究结果表明,加防返混锥能使锥体下端切向速度有所提高,利于颗粒分离。Rafiee等[59]、吴冉[60]、吴凯等[61-62]研究发现,防返混锥虽然能够抑制旋进涡核和颗粒返混,提高分离效率,但也会增大设备的压降。Wasilewski等[63]对15种不同角度的防返混锥进行分析,发现混锥角度为85°时能最大程度抑制颗粒返混,提高分离效率;混锥角度大于100°时压降会增大。因此,安装稳涡器,能够改善锥体下部的流动状况,减弱料腿上部的偏心环流,降低内旋流的旋转强度。
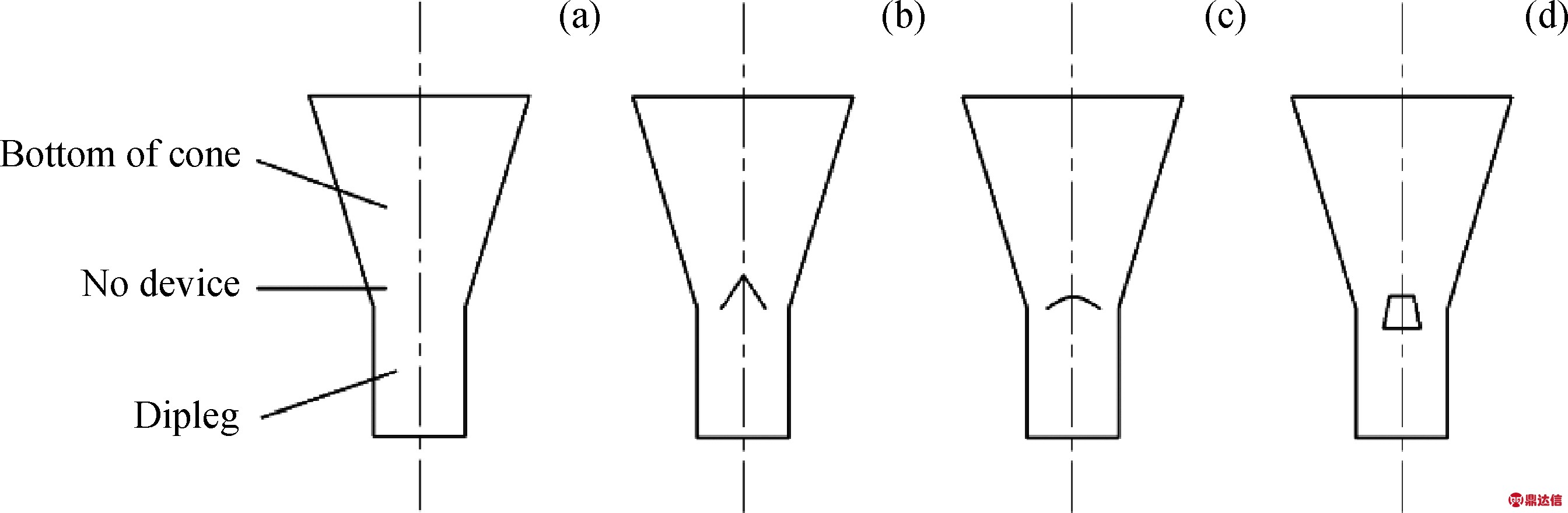
图9 稳涡器及其安装位置示意图
Fig.9 Structure of the vortex stabilizing device and its location
(a) No device; (b) Conical type; (c) Elliptical type; (d) Frustum of cone
3.8 防涡器
防涡器,与稳涡器不同,通常是一块刚性板或者一个交叉的“十字形”或“米字形”刚性板,安装在料腿上部,主要用来抑制涡流的形成,消除因气流旋转对料腿产生的冲蚀,阻止其旋转。但是,防涡器会造成料腿上方产生较强的扰动,使旋转气流的切向速度大幅降低,导致分离性能下降。Arkadiusz等[64]对防涡器进行实验,结果表明,防涡器能够降低料腿内颗粒的旋转,但是也会产生绕流,导致分离效率下降。为此,除一些特定场合外,不推荐使用防涡器。
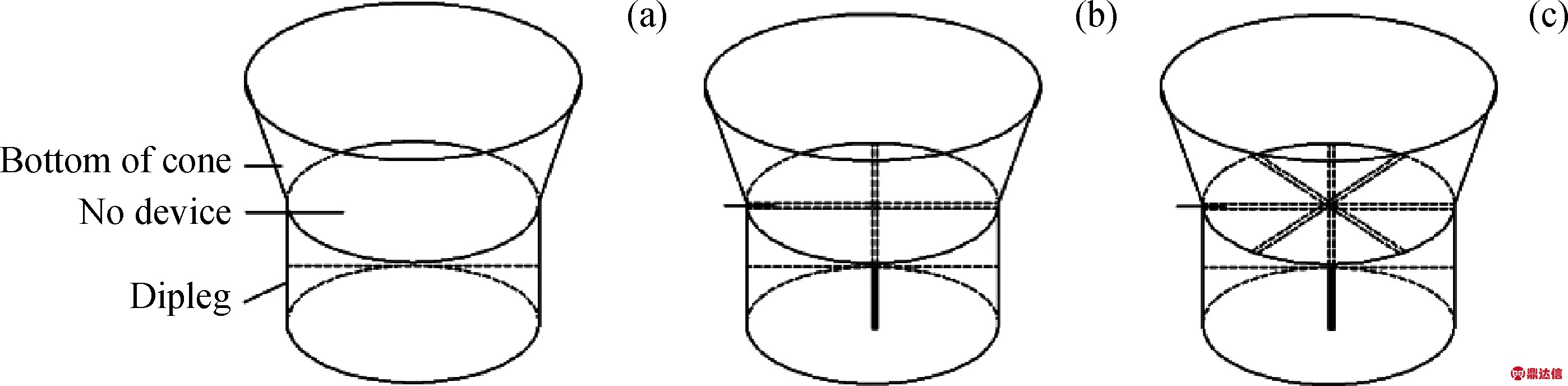
图10 防涡器及其安装位置示意图
Fig.10 Anti-vortex device and its installation position
(a) No device; (b) Anti-vortex device of Phill; (c) Anti-vortex device of Pozi
4 旋风分离器内构件技术的研究进展
4.1 内构件的组合使用
在工业运用中,内构件有时并不单一使用,而是采用多种方式结合的方法进行减阻降耗,提高分离效率。孙化鹏等[65]对子弹头减阻器进行了实验研究,发现子弹头减阻器上安装适宜的叶片,如图7(c)所示,比单一使用子弹头减阻器,更能提高旋风分离器的效率,减小总压降。Shi等[66]在入口处添加倾斜平板式导流叶片的基础上,运用分流型芯管的形式分离油-水混合物,可使油-水分离设备分离效率提高20.1%。Kosaki等[67]在添加稳涡杆的基础上,添加防返混锥,发现这种组合形式不仅能减少颗粒返混,而且提高了流体流动的稳定性。Dorfeshan等[57]发现,在筒体中心添加旋流叶片的基础上,在筒体尾端添加约140°的防返混锥,不仅能够减少颗粒返混,而且能够最大程度提高分离效率。所以,内构件的组合使用可大大提升旋风分离器内部流动空间的利用率,使分离效率在单一内构件的基础上再次得到提升,是未来旋风分离器内构件的发展趋势之一。
4.2 新型减阻增效内构件的开发
随着化工科技的发展,在工程运用过程中,还会出现各种各样的新型内构件。Luan等[68]提出,在导流叶片的出口可以连接过滤器,能够进行更加精细的分离。Sibanda等[69]在旋风分离器内安装了错流过滤原件,有效地促进了细颗粒的捕集效率。宋承明等[70]对内置涡核破碎翼旋风分离器进行颗粒分析,发现叶片形状和布置方式对流场影响较大,安装合理时既能维持较高效率又能极大程度减低压力损失。未来,伴随着新型内构件的开发与应用,旋风分离器的分离效率会进一步地提高,不仅能够降低其阻力,而且可以渐渐满足各种环保及工艺要求。
4.3 新材料的开发与内构件的使用寿命
旋风分离器内部流场为气-固两相流动,颗粒的运动会造成内构件的磨损,降低内构件的使用效果。对内构件使用新材料,使其耐磨抗损,能够大大增强内构件的使用寿命,在另一种意义上保证了旋风分离器的高效气-固分离。何祥义等[71]对CFB旋风分离器研究发现,含SiO2材质的耐火砖抗压强度高,在高温下有一定的韧性,材料的耐磨性好。李洪杰等[72]在旋风筒上运用组合陶瓷片,发现组合陶瓷片能够提高设备使用寿命,降低停机更换成本。因此,新材料的开发能够提高内构件的使用寿命,是未来内构件的发展趋势之一。
5 旋风分离器内构件技术的发展方向
目前,针对旋风分离器内构件的研究取得了一定的成果。但是,部分内构件很少被用于工业生产,因为内构件的应用不仅要考虑其减阻效果,还要考虑其对分离器效率的影响大小、安装难易程度、实施维修费用、使用寿命等因素。许多内构件的应用,在减阻和增效两方面有可能是矛盾的,阻力降低了,效率可能也随之下降。
21世纪是各种自然科学高度综合、相互交叉、彼此渗透的时代,在未来旋风分离器内构件的研究发展中,会更倾向于多元化、细致化、精确化、简约化。在宏观上,结构形式会趋于多样化,但以简约为主,而且将会采取多种方式相结合的方法,减阻降耗提高分离效率。在微观上,内构件的使用将使旋风分离器分离更加细微的颗粒,解决目前5 μm以下粒径颗粒分离效率低的难题。此外,环保及工艺要求会越来越高,旋风分离器内构件的研究发展想要真正达到低阻高效的目的,满足各种工业要求还需要进行更加深入的研究,才能为工业的发展和创新提供更可靠、更灵活、更高效、更经济的技术系统。
6 结 语
随着化工过程的不断发展,环保及工艺要求越来越高,工业上要求保证旋风分离器分离效率的同时能够减小压降。目前的研究主要集中在结构优化、安装内构件和其他措施3个方面。但是,在工业实际应用中,若是采用更换分离器的方式,会大大提高生产成本和工程量,此时添加内构件不失为一个经济、简便的方法。根据内构件的结构形式和工作原理,内构件可大致分为减阻杆、导向板、导流叶片等八类。由于旋风分离器的结构不同,不同内构件亦有不同程度的减阻效果。但是内构件的使用对分离效率的影响不一,部分内构件在减阻和增效两方面可能是矛盾的,阻力降低了,效率也随之下降。此外,工业上内构件的使用并不单一,多数情况下组合使用效果更佳。总的来说,在不改变旋风分离器结构尺寸的情况下,安装内构件能够改善旋风分离器内的干扰涡流,提高内部流动的稳定性,从而有效地实现分离器的减阻增效。