摘要:目前对带子系统的动力包双层隔振系统子系统参数设计的研究甚少。针对这一现状,笔者采用试验的方法,分别研究了某型内燃动车动力包双层隔振系统子系统各隔振参数(隔振器总刚度、阻尼、隔振器刚度比)对其隔振性能及动态特性的影响。研究结果表明,将子系统设计成双层隔振主系统的动力吸振器,能使动力包双层隔振系统在发动机常规工况和停机或启动工况皆具备优良的隔振性能,并且隔振系统在子系统隔振器参数取较小的刚度,适当大的阻尼和合适的刚度比时能取得较好的隔振效果。
关键词:子系统; 内燃动车动力包; 双层隔振系统; 隔振性能
引 言
作为内燃动车的动力源,同时也是主要的激振源之一,车用柴油发电机组动力总成通常以动力包的形式,采用双层隔振方式悬挂于车体底部。较之典型的双层隔振系统而言,动力包双层隔振系统最主要的特点在于除了1,2级主系统外还在中间构架上弹性安装了一个本身不带激励源的子系统。回顾双层隔振理论和技术的发展史,许多学者从不同的角度作了大量的研究,提出了许多有借鉴意义的结论[1-4]。国外动力包发展地已较为成熟,并且广泛应用于铁道车辆、船舶等诸多领域。但该项技术还没有得到广泛的传播,很少见到有关动力包双层隔振的研究和报道。目前,动力包双层隔振系统的隔振技术还在初步探索和应用阶段,带无源子隔振系统的双层隔振系统隔振设计的相关文献还较少。文献[5]研究了运载火箭及其子系统的隔振设计,但并没有深入探讨两者间的耦合振动特性。文献[6]给出了当质量比小于0.1时,子系统对主系统隔振性能无影响可忽略不计的结论。基于此,孙玉华等[7-10]将主系统与子系统单独进行隔振设计,从解耦优化和模态匹配的角度,对国内首次采用的动力包进行了较为系统的研究和相关的试验测试,取得了不错的效果。文献[11]研究了子系统对双层隔振主系统固有特性的影响规律,并给出了子系统设计的几点建议。但目前尚缺少子系统对主系统隔振性能及动态特性方面的研究,尤其是这方面的试验研究。
基于以上情况,笔者将以出口阿根廷内燃动车动力包为研究对象,系统地研究子系统各隔振参数(隔振器总刚度、阻尼、隔振器刚度调配)对双层隔振系统隔振性能的影响,旨在为动力包子系统参数的设计提供参考。
1 动力包双层隔振系统动力学特性分析
动力包双层隔振系统如图1所示,其中柴油机和发电机通过连接套刚性连接构成双层隔振系统的1级主系统,通过5个1级隔振器安装于构架上。构架和刚性安装于其上的水箱、空滤、消音器等构成双层隔振系统的2级主系统,通过4个2级隔振器安装于基础上。散热器通过4个隔振器安装于构架上构成双层隔振系统的子系统。
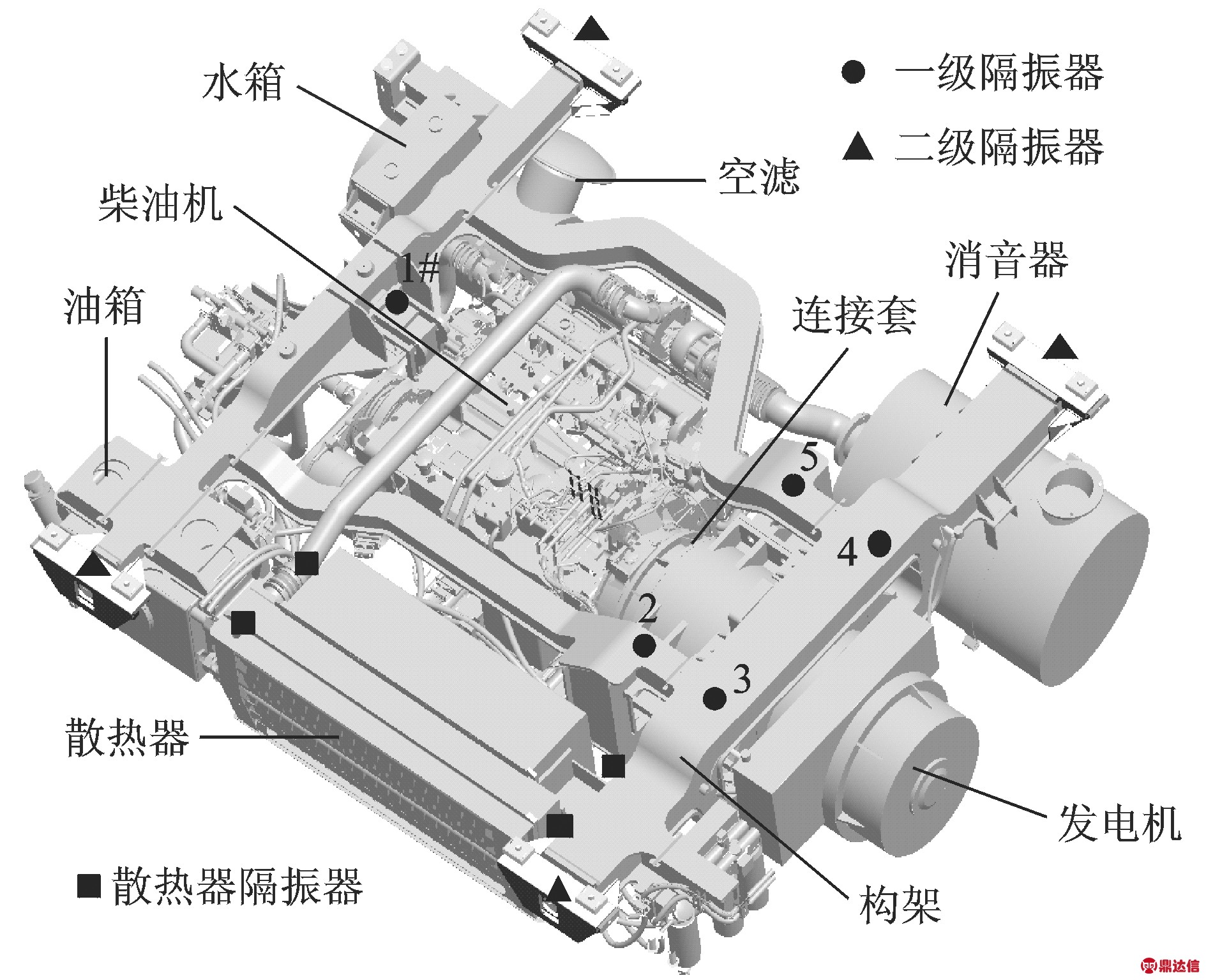
图1 力包双层隔振系统实物图
Fig.1 Physical diagram of powerpack double-layer isolation system
以柴油发电机组的质心为原点,建立含子系统的双层隔振系统的18自由度动力学模型,如图2所示。
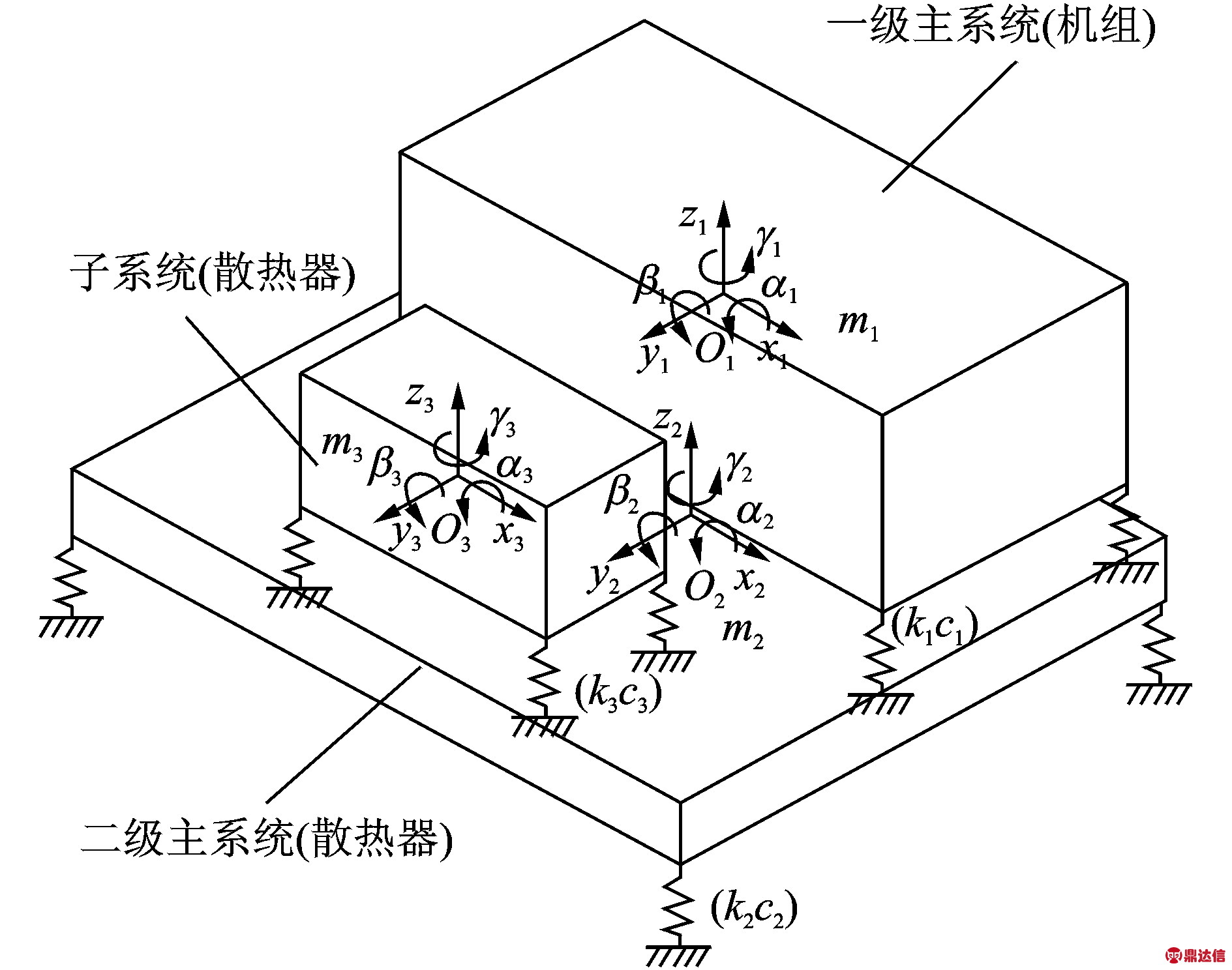
图2 内燃动车动力包双层隔振系统动力学模型
Fig.2 Dynamic model of diesel railcar powerpack double-layer isolation system
图2中:O,O1,O2,O3分别为参考坐标原点和机组、中间构架、散热器的质心;O-XYZ和(α,β,γ)为参考坐标系及其惯性主轴;O1-x1y1z1,O2-x2y2z2,O3-x3y3z3和,(α1,β1,γ1),(α2,β2,γ2),(α3,β3,γ3)分别为机组、中间构架和散热器的局部坐标系和惯性主轴;M0为柴油的倾倒力矩,方向为α1向;(m1,m2,m3),(k1,k2,k3),(c1,c2,c3)分别为机组、中间构架和散热器的质量、刚度和阻尼。
隔振器阻尼和刚度关系式[6]为
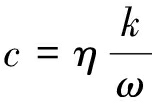
(1)
其中:η为橡胶隔振器的结构阻尼比。
系统的动力学方程[9]可写成如下形式

(2)
式中的质量、阻尼和刚度矩阵均为18阶方阵,与之对应的加速度、速度、位移量也是18维的,具有下列形式
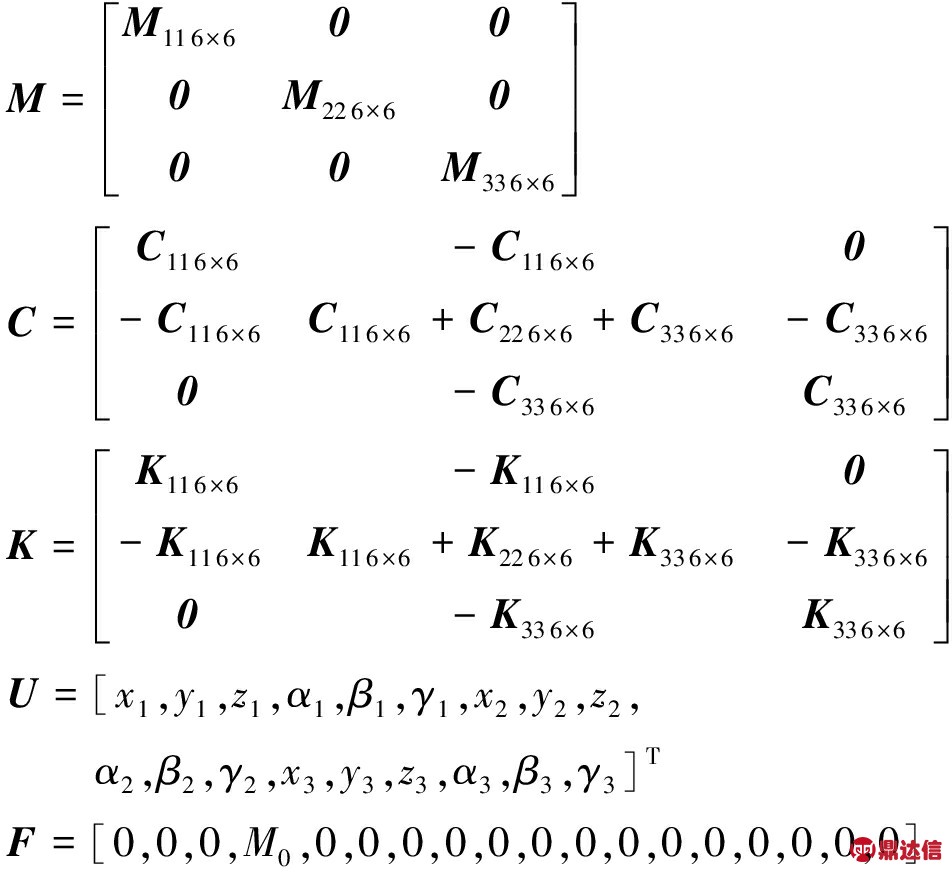
只考虑系统的强迫振动的稳态响应,系统的解可设为u=Acosωt+Bsinωt,将其代入式(1),则A,B可由式(3)求出

(3)
定义系统的力综合传递率为隔振前后系统传递给基础的总力之比
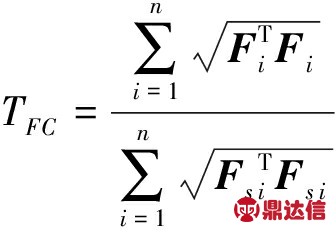
(4)
其中:Fi为与基础相连第i个隔振器的三向力动反力;Fsi为隔振器短路时第i个隔振器的三向力动反力。
由式(3)求出二级隔振器的位移,进而根据隔振器刚度、阻尼和激振频率,分别求出动力包在散热器弹性安装(隔振器取设计刚度)、刚性安装和不安装散热器情况下的综合传递率曲线如图3所示。
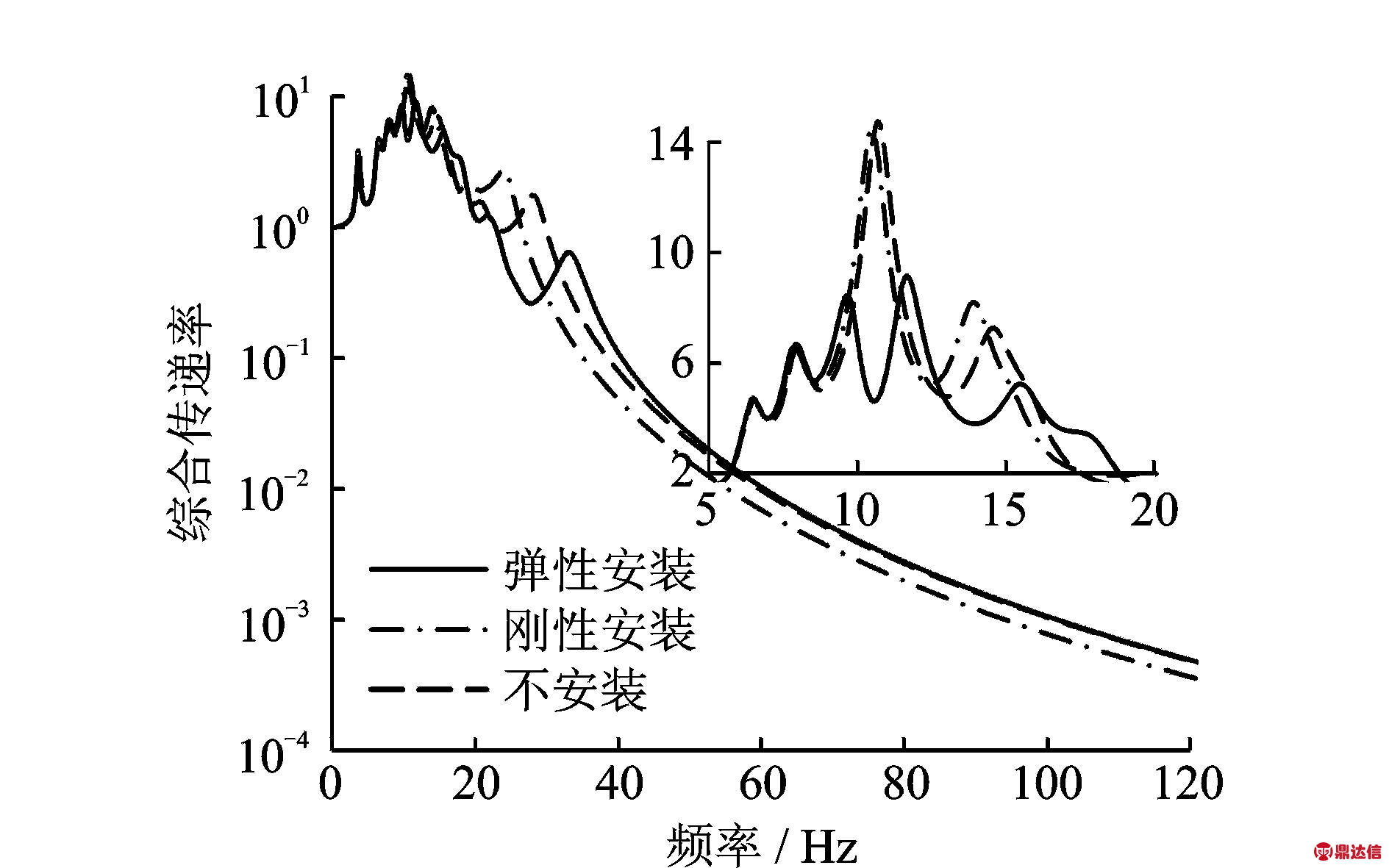
图3 3种不同安装方式下的力综合传递率曲线
Fig.3 Force comprehensive transfer rate under three different installation method
从图3中可以看出,散热器刚性安装时系统的共振峰较其他两种情况向低频移动,系统高频隔振性能略微提高。散热器采用设计刚度时,构架α2向模态对应的共振峰往高频移动,但系统的高频隔振性能基本不变。系统α1向(激振力方向)模态频率对应的共振峰,分化成两个峰值相等的共振峰且峰值大幅度减小,系统低频隔振性能大为提高。分析系统的模态能量分布情况可知,此时散热器的y3向(横向)模态对系统α1向模态起控制作用,散热器充当系统的动力吸振器。此时,动力包双层隔振系统既具备普通双层隔振系统优良的高频隔振性能,又能克服传统双层隔振系统低频隔振性能不足的缺点。此时,动力包双层隔振系统在发动机常规工况(高频)和停机或启动工况(低频)皆具备优良的隔振性能。可见子系统参数的合理设计,能很大程度地提高动力包双层隔振系统的综合隔振性能。
2 试 验
2.1 测试系统
本次试验,基于比利时LMS公司的SCADAS测试系统完成的所有测试工作,该系统主要由朗斯三向加速度传感器,LMS SCADAS测试系统,微机测试平台组成。试验中机组、构架和散热器的振动烈度测点皆根据铁标TB/T3164-2007进行选取。为了分析系统的传递特性和隔振器的动反力,在1,2级隔振器上下也布置了相应的测点。图4给出了散热器、动力包2级隔振器上、下,1级隔振上、下,和隔振器处测点的照片。
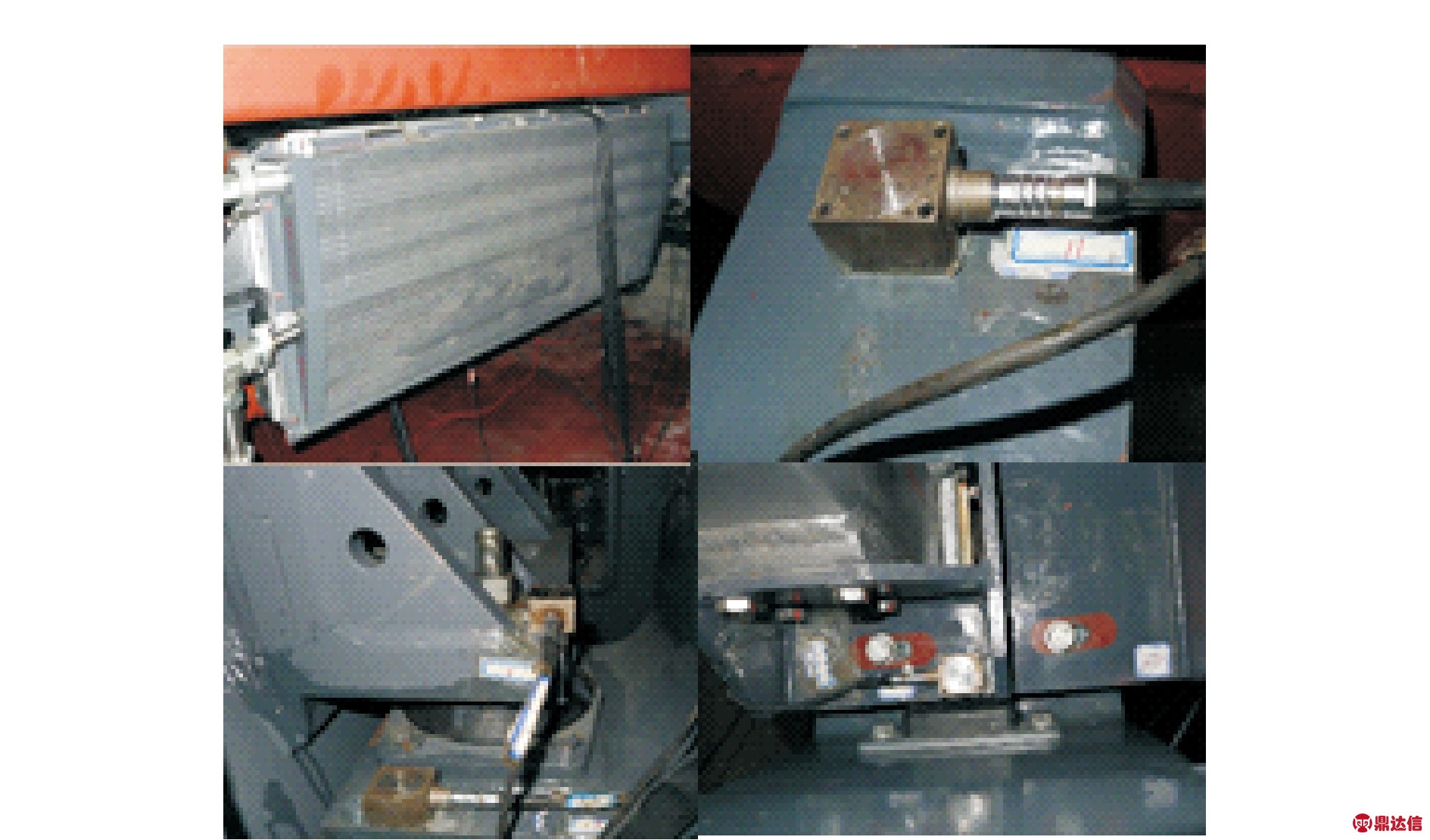
图4 动力包振动测试照片
Fig.4 Photos of vibration measurement test for powerpack
2.2 试验方案及工况
为了研究子系统各隔振参数对双层隔振系统隔振性能及动态特性的影响,确立了以下目标:a.研究隔振器刚度对系统隔振性能及动态特性的影响;b.研究隔振器阻尼对系统隔振性能及动态特性的影响;c.研究隔振器刚度调配对系统隔振性能及动态特性的影响。根据以上3个研究目标,制定子系统的4种不同的刚度方案:①子系统按原设计方案安装;②保持散热器总刚度与方案①一致,将左右两隔振器的刚度比由1∶1变为5∶1;③将方案②的隔振器结构阻尼比由0.1增大到0.2;④将方案①的隔振器刚度增大到原来的两倍。两者的对应关系如表1所示。
表1 研究目标及刚度方案的对应关系
Tab.1 Corresponding relationship between the research target and stiffness scheme

本次试验柴油机的运行工况完全模拟内燃动车各工况档位及柴油机实际运行工况,分别为1 000,1 200,1 400,1 650,1 800 r/min 5个稳定工况和柴油机900 r/min怠速停机工况,一共6个工况。
3 试验结果分析
通过以上分析可知,本次试验所用动力包除了具备良好的高频隔振性能,能较好地隔离柴油发电机组常规工况的激振力;还具备较好地低频隔振性能,能较好地隔离柴油发电机组在停机工况的激振力。基于动力包双层隔振系统的以上隔振特性,本次试验将分别在这两种工况下展开,以求更加全面客观地反映子系统各隔振参数对双层隔振系统隔振性能的影响。本次试验,各测点采集的原始数据均为测点处的加速度信号,采样频率为1 kHz,采样时间为30 s。
3.1 子系统隔振器刚度对系统隔振性能的影响
子系统取不同刚度时动力包双层隔振系统2级隔振器动反力随发动机转速的变化如图5所示。从图中可以看出当子系统隔振器刚度增大时,在转速低于1 800 r/min的工况系统动反力变大,隔振性能变差,此时,子系统刚度的增大会使构架在激振力方向(α2)当量扭转刚度增大,模态共振峰向高频移动,高频隔振性能变差。两种刚度方案,在1 000~1 600 r/min的区间内动反力随转速变化的趋势一致,而转速在900和1 800 r/min附近时动反力随转速变化的趋势正好相反,这是因为两种方案下系统在以上两个转速工况附近的运行模态振型不同的原故。由图6可知,在发动机常规工况子系统隔振器刚度的变化对机组振动烈度的影响较小,而对散热器本身的振动烈度影响较大,增大散热器隔振器刚度,散热器振动烈度变大。对比构架和散热器的振动烈度可知,取小刚度时隔振器能更好地隔离构架传递给散热器的振动,这可以通过单自由度位移传递率曲线来解释。散热器与构架振动烈度随转速变化的趋势基本一致,这是因为在发动机常规工况激振力的频率位于动力包双层隔振系统的过共振区,此时构架局部结构振动对振动烈度贡献量较小,系统整机振动振幅大小基本随激振力频率单调变化。图7为柴油发电机组停机工况下动力包各级系统3.0阶位移振幅曲线。从图中可以看出,与预测相符机组、构架的位移振幅在200 r/min(10 Hz)左右各有一个幅值较小的共振峰。散热器第1个峰值较小,第2个峰则非常大,说明在系统频率接近第2个峰值频率时,由机组输入的很大一部分振动能量转移到了子系统,从而减弱了构架(2级主系统)的振动,同时也间接的抑制了机组的振动(1级主系统),子系统充当双层隔振主系统的动力吸振器。增大子系统隔振器刚度,子系统不再能对主系统起到吸振作用,1,2级主系统最大峰值增大,子系统最大峰值减小。
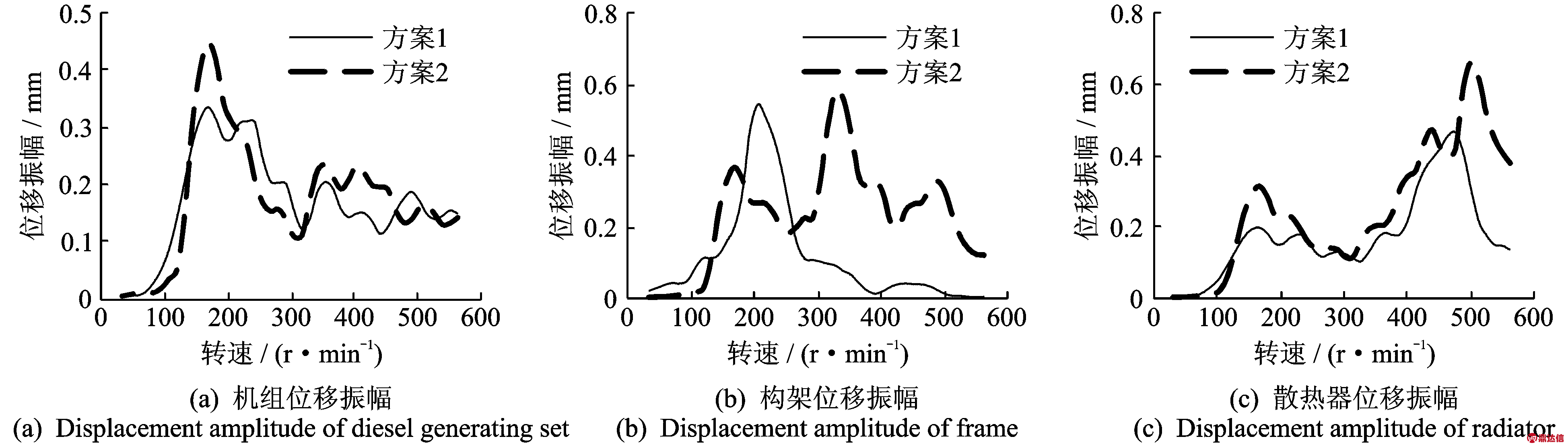
图5 2级隔振器动反力对比
Fig.5 Comparison of the second stage isolator reaction force
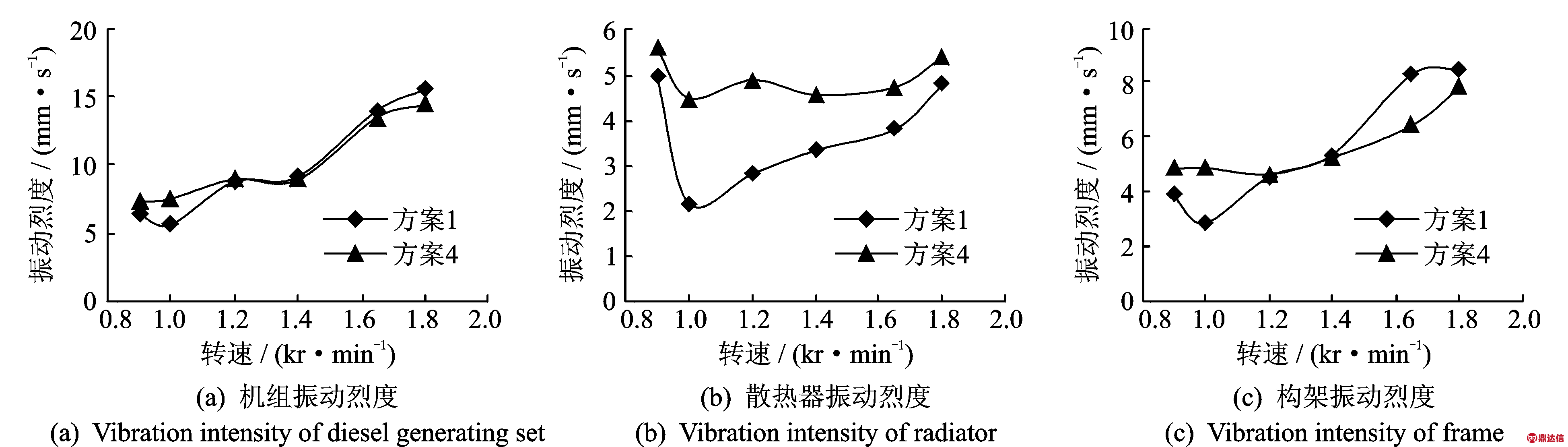
图6 动力包各部件振动烈度对比
Fig.6 Comparison of vibration intensity of powerpack parts
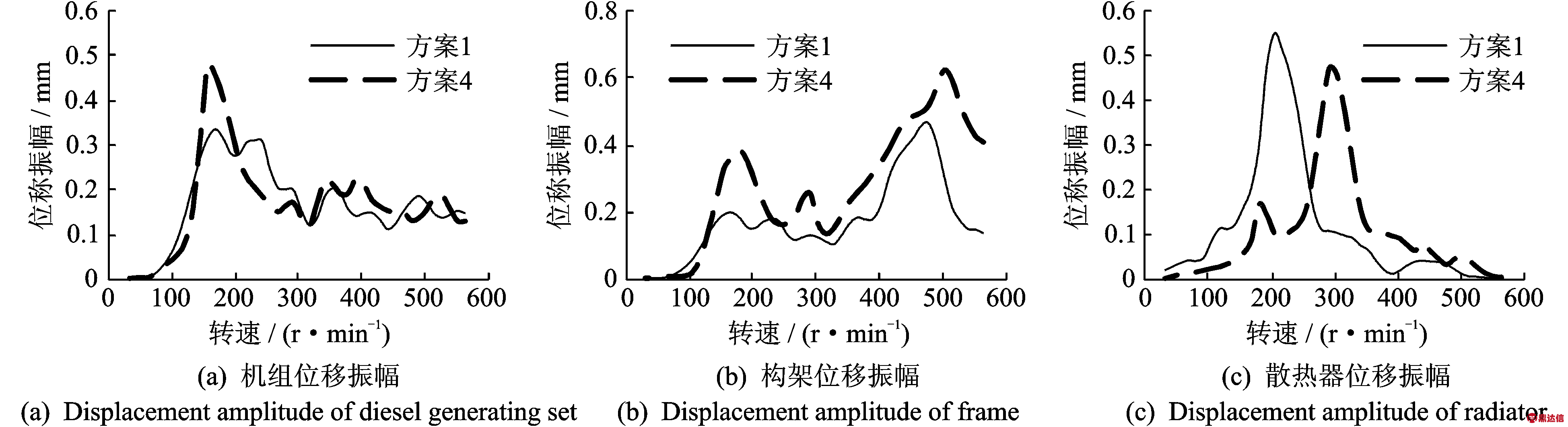
图7 动力包各部件停机工况3.0阶位移振幅曲线对比
Fig.7 Comparison of 3.0 order displacement amplitude in shutdown condition
3.2 子系统隔振器阻尼对系统隔振性能的影响
隔振器阻尼是影响隔振系统隔振性能的一个重要参数,在多自由耦合隔振系统中,隔振器阻尼参数不仅能影响系统响应的幅值和相位,还能影响系统的振型。图8给出了子系统隔振器取两种结构阻尼比时,发动机常规工况下2级隔振器的支反力对比。从图中可以看出,在低转速时(小于1 000 r/min)增大隔振器阻尼能有效地减小2级隔振器的动反力提高系统的隔振性能。而在高转速时(大于1 400 r/min),因为系统大阻尼时系统高频隔振性能差的原故,增大阻尼反而会使动反力变大,隔振性能变差。动力包各部件在发动机常规工况的振动烈度随发动机转速的变化曲线,如图9所示。从图中可以看出,子系统阻尼变化对机组在发动机常规工况的振动烈度影响不大,而对散热器本身的振动烈度存在较大影响。子系统隔振器阻尼的增加,会增大构架的振动烈度,但同时又会使自身的振动烈度变小。两种阻尼下,散热器和构架振动烈度随转速变化的趋势基本一致,大阻尼时最大峰值出现在转速较低的工况,这是因为阻尼的增大使隔振系统振型发生改变且固有频率变低的原故。图10为柴油发电机组停机工况下动力包各级系统3.0阶位移振幅曲线。从图中可以看出,阻尼的变化对机组位移振幅影响不大,但能有效地减弱散热器本身和构架在机组停机工况的振幅,其原因是系统在低频大阻尼的情况下具有较好的隔振性能。
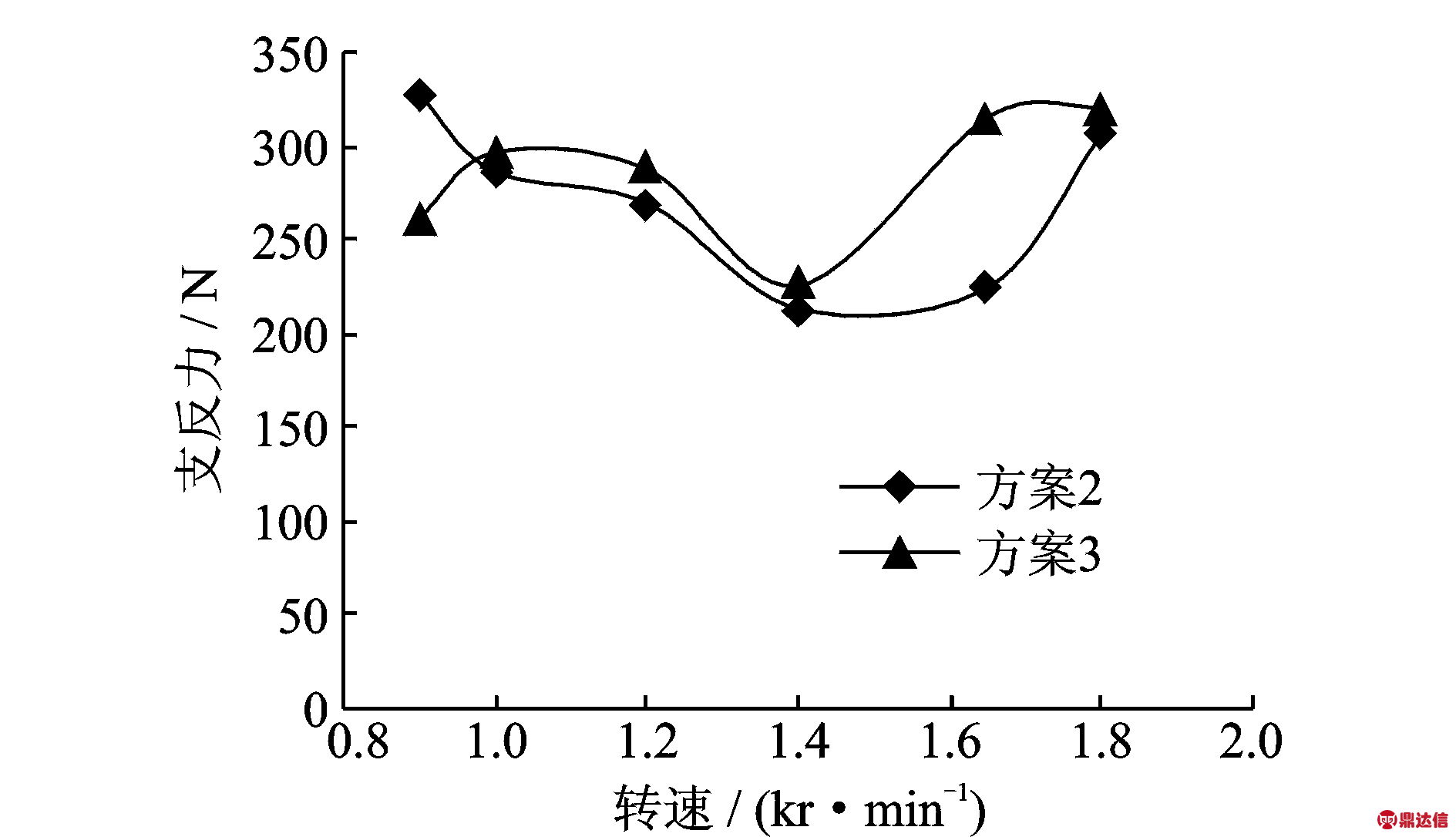
图8 2级隔振器动反力对比
Fig.8 Comparison of the second stage isolator reaction force
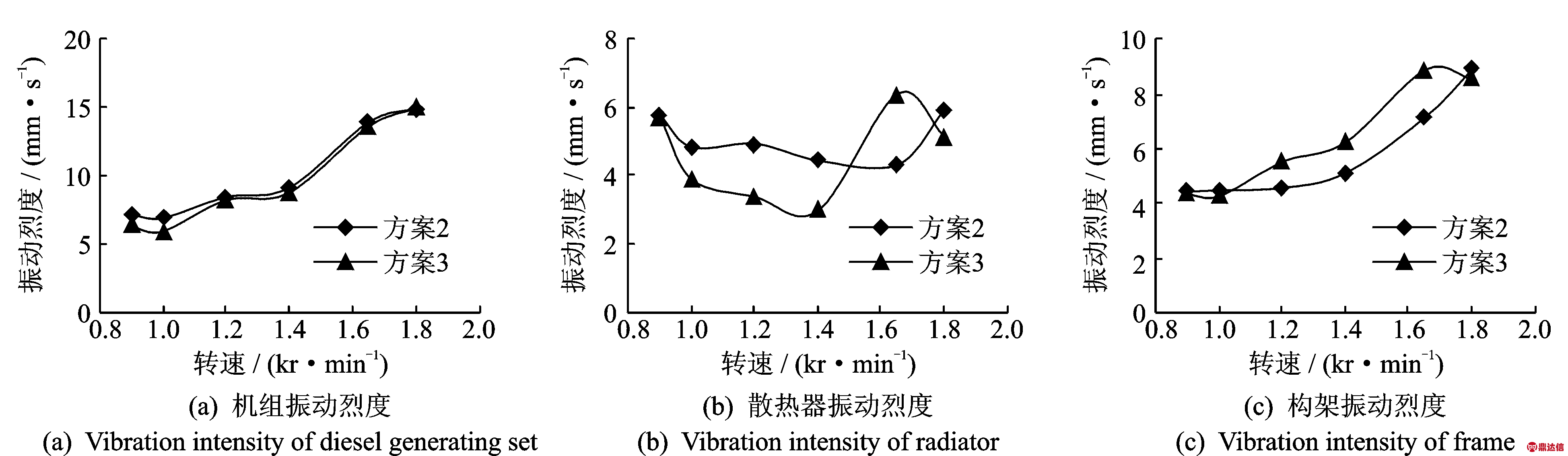
图9 动力包各部件振动烈度对比
Fig.9 Comparison of vibration intensity of powerpack parts
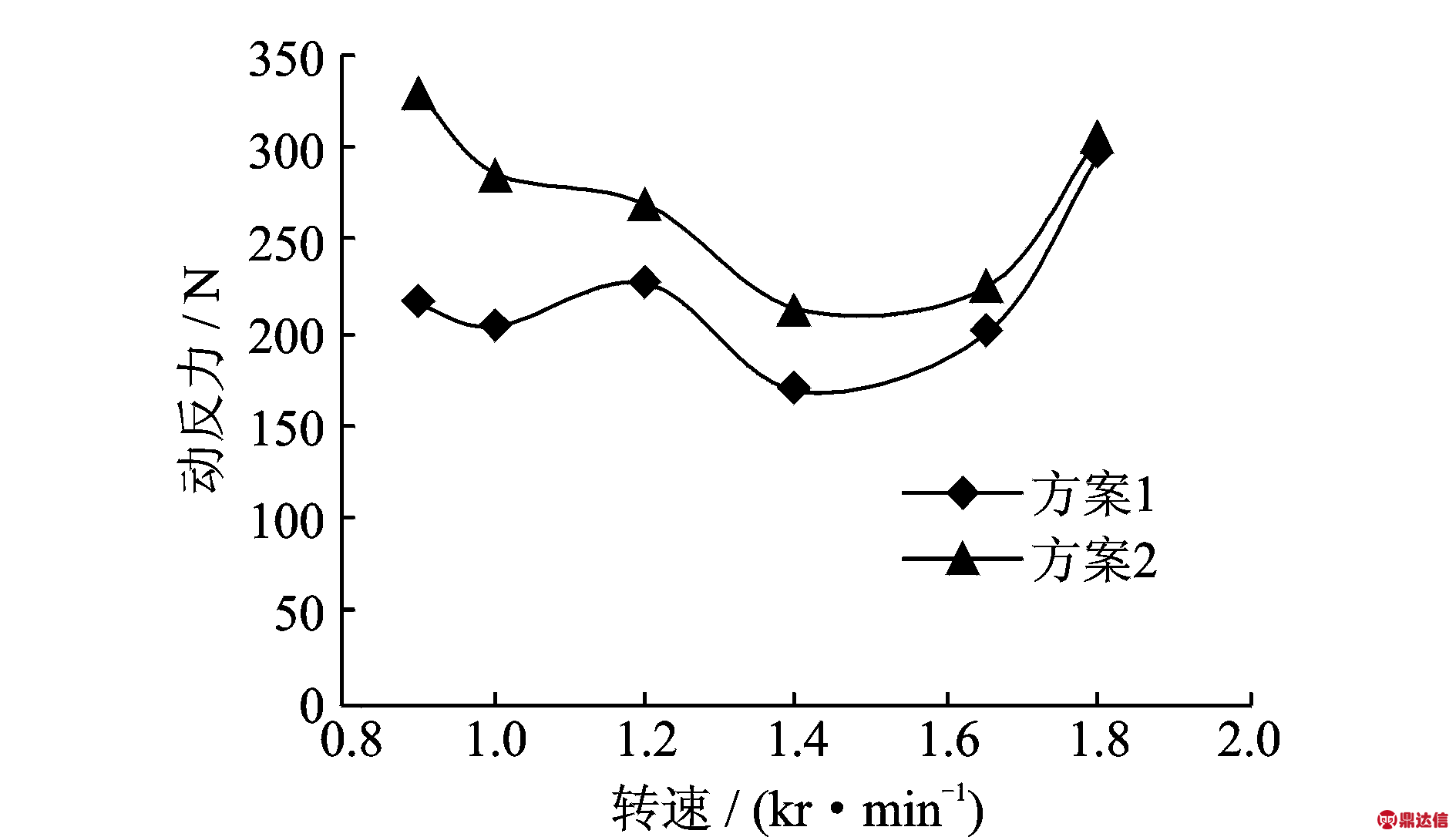
图10 动力包各部件停机工况3.0阶位移振幅曲线对比
Fig.10 Comparison of 3.0 order displacement amplitude in shutdown condition
3.3 子系统隔振器刚度调配对系统隔振性能的影响
子系统隔振器之间刚度的比例关系(隔振器刚度调配),决定了子系统本身的解耦度以及其与主系统的耦合程度和耦合关系。图11给出了隔振器刚度取两种不同比例的情况下,2级隔振器支反力,在柴油机常规工况下的对比。由图可知,调整隔振器刚度比后,2级隔振器动反力在柴油机常规工况下皆有所增大,系统隔振性能变差,这是因为改变刚度比使系统综合解耦度变差耦合振动更为强烈的缘故。图12为动力包各部件停机工况3.0阶位移振幅曲线,由图可知动力包各部件在10 Hz(200 r/min)附近的两个峰值相差较大,散热器不能起到较好的吸振作用,其在200 r/min附近的振幅也相应有所减小,究其原因是因为隔振器加工误差导致散热器隔振器刚度略有偏大。并且因为系统综合解耦度变差,各部件在发动机停机工况的振动与设计方案相比更为剧烈。隔振系统在发动机常规工况的振动烈度随发动机转速的变化曲线,如图13所示。从图中可以看出,散热器隔振器刚度比的变化对机组振动烈度的影响不大,但对散热器本身和构架的振动烈度影响较大。调整隔振器刚度比后,散热器解耦度变差,与机组和构架的耦合更为严重,其振动烈度也随之变大。在调整隔振器刚度比后,构架的约束模态发生了频移,系统在90 Hz附近不再出现共振。观察构架2级隔振器处的位移振幅可知,与方案1不同,方案2在90 Hz(分别对应900 r/min的6.0阶次和1 800 r/min的3.0阶次)的位移振幅与其他转速工况6.0和3.0阶次的位移振幅幅值相差较小。此时,构架振动烈度随发动机转速单调递增,但与方案1相比振动烈度变化不大。
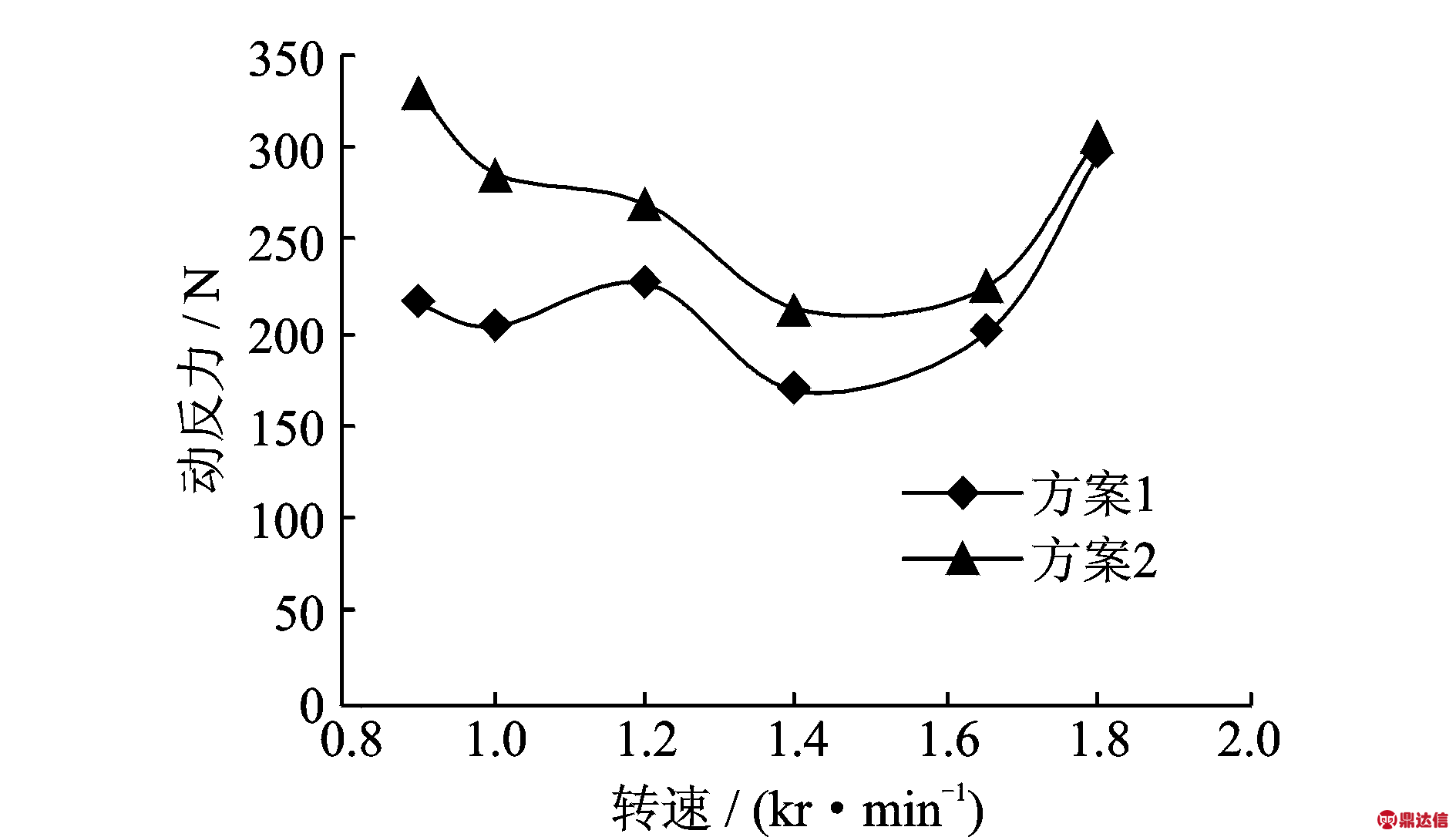
图11 2级隔振器动反力对比
Fig.11 Comparison of the second stage isolator reaction force
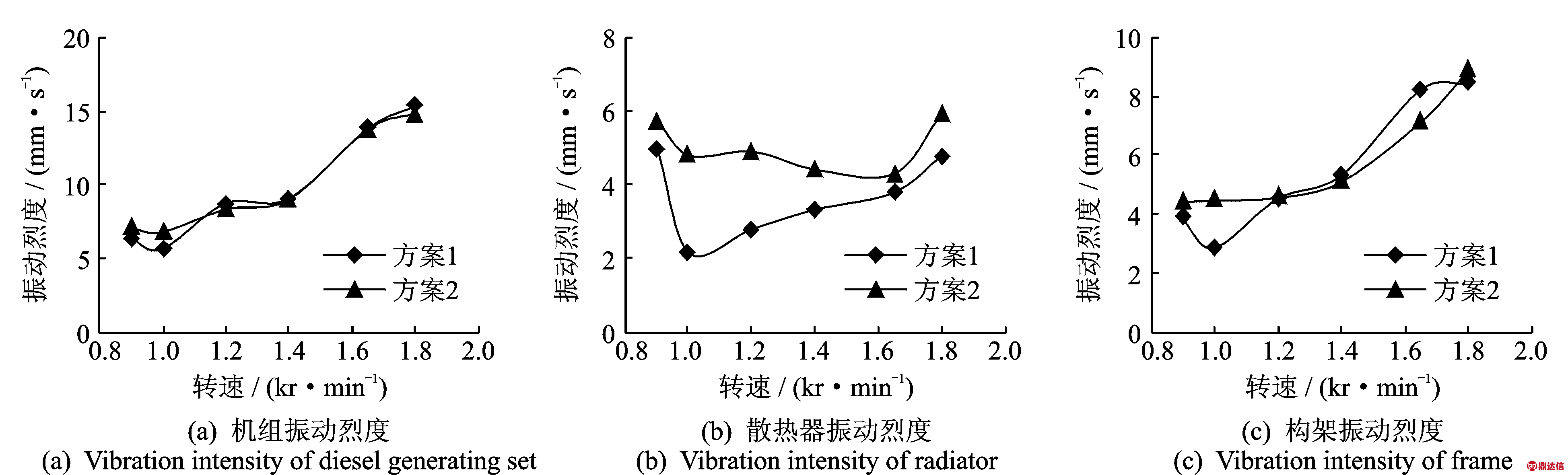
图12 动力包各部件振动烈度对比
Fig.12 Comparison of vibration intensity of powerpack parts
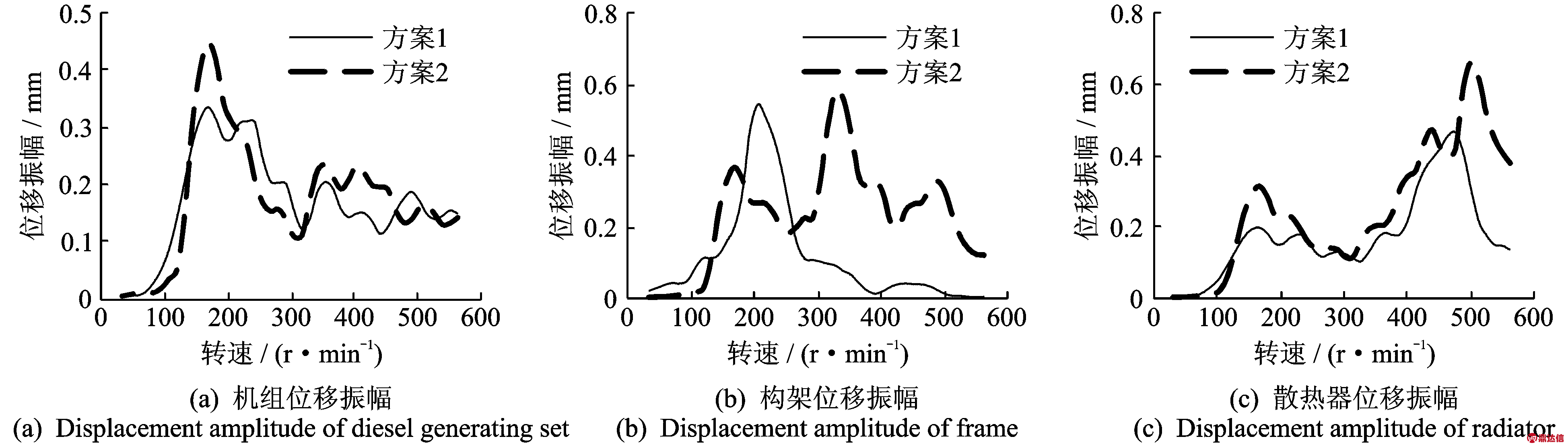
图13 动力包各部件停机工况3.0阶位移振幅曲线对比
Fig.13 Comparison of 3.0 order displacement amplitude in shutdown condition
4 结束语
将散热器子系统充当动力包双层隔振系统的动力吸振器,可使系统同时具备优良的高频隔振性能和较好低频隔振性能。此时,动力包双层隔振系统在发动机常规工况和启停机工况皆具备优良的隔振性能。在设计刚度的基础上增大散热器子系统隔振器刚度,2级隔振器动反力和散热器振动烈度变大,机组振动烈度基本不变,子系统不对主系统起减振作用,系统在停机工况振动更为剧烈,隔振性能能变差。
增大散热器子系统隔振器阻尼,能有效减小低转速工况下二级隔振器的动反力和散热器的振动烈度,但又会增大高转速时的动反力,增大构架的振动烈度,而对机组的振动烈度影响不大。总体而言,适当增大散热器阻尼能提高动力包双层隔振系统的隔振性能。
增大子系统与主系统的耦合度,二级隔振器动反力和散热器振动烈度变大,机组振动烈度基本不变。系统在停机工况振动更为剧烈,系统传递给基础的支反力变大。总之,尽量提高散热器除起吸振作用的模态以外的其他主方向模态与主系统的解耦度有利于提高动力包双层隔振系统的隔振性能。