摘要:多个锂电池串并联工作后,容易导致电池间容量不均,引发安全问题。为了更可靠管理电池组,设计了一种模块化的电池管理系统。系统采用半分布式结构和基于双向反激的主动均衡设计,电路中使用了LTC6803-1芯片采集电压、温度信号,磁耦隔离通信模块实现与上位机的SPI通信,LTC3300芯片驱动控制双向反激电路。实验表明管理系统可完成参数精确采集及SOC预估,快速高效地减小电池间容量差异,实现电池组管理和控制。
关键词:电池管理系统;绝对值电路;双向反激;模块化
太阳能、风能发电量逐年上升,但发电间歇性与不稳定性,以及外部不确定因素,都会使该类能源并网时遇到阻碍。解决该问题往往通过配备大型储能装置,平抑发电系统固有的间歇波动后再逆变并网。大容量储能装置的合理应用能有效解决我国中西部某些经济欠发达地区的发电量不足的问题,大大缓解了国家电网的压力,也为新能源的存储提供了有效途径。目前,大容量储能装置大都通过单节电池串并联后组成。成组后电池因其固有差异及使用过程中形成的所有微小的变化,会导致电池性能不一致。电池性能不均一与离散容易使得电池组失去均衡,如不加以补偿管理,长此以往,势必在电池组使用时带来安全问题[1]。所以大型储能装置配备了电池管理系统,可以补偿差异、实现均衡,为电池组正常运行提供保障。
电池管理系统(Battery Management System,BMS)的主要功能:建立可以准确描述电池特性的系统模;准确估算电池剩余电量状态;有效评估电池健康状况;实现有效的电池性能均衡控制系统等[2]。
电池管理系统从与电池组结合的安装布局及结构上可分为集中式、分布式和半分布式。集中式是一组电池配有独立的电池管理芯片,它成本低,但扩展性较差,只能适用于单体数量较少的电池组;分布式是每个电池模块都配备独立的管理芯片,延展性和适用性较好,但成本过高;半分布式是在电池组中不同模块上根据需要配置管理芯片,部分模块有独立的芯片,部分模块共用一个芯片,由于这种配置结合了上述两者的优点,成为当今电池管理系统主流技术。
均衡电路分为主动型和被动型。被动型均衡电路虽然简单、低成本,但能耗大、散热困难。所以近年来主动型均衡电路成为研究热点。
早期的主动型均衡电路利用电感、电容作为储能元件。这种电路均衡速度慢,控制不方便,结构复杂,且能量传递仅能单向转移[3];新一代以集中控制变压器的方式对电池进行能量转换的主动型均衡电路,均衡速度块,效率高,但变压器设计难度大,漏感问题较难解决,每个电池都必须配备,成本较高[4-5]。
综合以上因素,本文设计了一种模块化半分布式结构的电池管理系统,采用均衡效率较高的双向反激拓扑电路作为均衡电路,采集速度快、精度高,具有一定的可扩展性。
1 系统设计
电池管理系统主要由主控制器模块、主动均衡模块、采集模块、保护电路模块和显示模块组成。具体如图1所示。
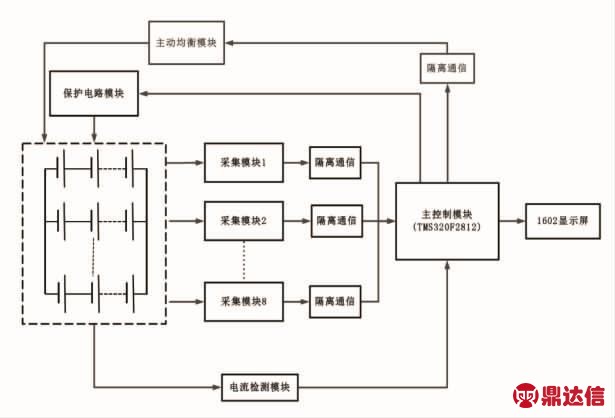
图1 硬件系统组成框图
1.1 采集模块
采集模块用ADI公司电池监测芯片LTC6803-1,芯片内置具有噪声滤波器的ΔΣ转换器和12位ADC,最多可以同时对12只串联的锂电池进行电压和温度采样,采样周期13 ms,最大总测量误差不超过0.25%,外围电路简单,抗干扰能力强。
LTC6803-1具体外围电路搭建如图2所示。

图2 LTC6803-1基本外围电路
通过集成芯片对工作中的电池组进行电压采集,数据放置在采集芯片的寄存器中。最终由上位机读取相应寄存器,通过转换公式得到当前的电池组各节电池电压[6]。
LTC6803-1所测量的单块电池输入电压计算公式:

式中:VLSB取值1.5 mV;DOUT为十进制整数。
为保证测量的数据不被尖峰干扰,需要在芯片的每个测量口加入一个低通滤波器电路,同时为防止电池反接对采集芯片造成损害,在每块电池前加入一个稳压二极管进行保护,见图3所示。由于LTC6803-1芯片是一种常用于实现数模转换功能的芯片,它能提供一个基本是0.5 ms转换窗口的平均值的转换结果,这就表明可以使用一个500 kHz频率下具有30 dB衰减的低通滤波器。根据100 Ω,0.1 μF的参数设计,可以组成一个16 kHz低通滤波器,且提供30 dB的噪声抑制[7]。
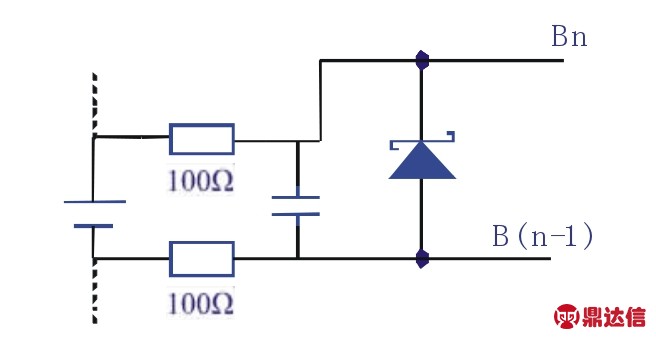
图3 低通滤波器电路与稳压二极管
1.2 隔离通信
LTC6803的供电电压为5 V,但主控制芯片的供电电压为3.3 V。为保护MCU正常工作,需要在SPI通信时采用基于iCoupler磁耦隔离技术的通用型四通道数字隔离器来隔离通信芯片ADUM1411。相较于光电耦合器的不稳定电流传输率、非线性传输的问题,磁耦隔离能在寄存器通信时达到可靠、高速率的传输。具体电路如图4所示。
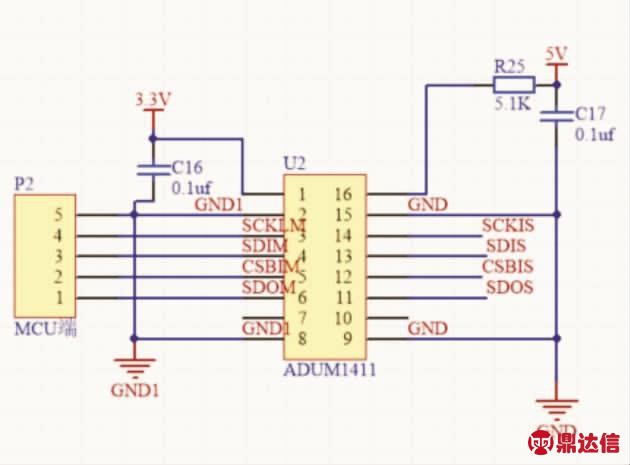
图4 隔离通信模块
1.3 保护电路模块
将采集得到电池组的总电压和初始设定的一个基准电压进行比较。若总电压小于基准电压,便向主控制器传输一个信号,控制器将执行电池组的关断操作,避免电池组因过放引发安全问题。过流、欠压保护电路见图5。
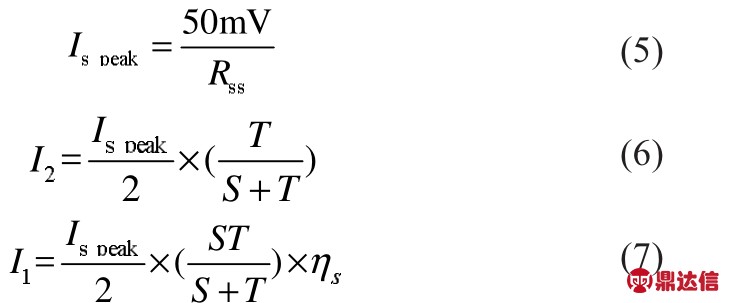
图5 过流、欠压保护电路
同理,将检测得到的电流与阈值进行比较,若电流过大,主控制器将对电池组进行关断操作。通过模拟信号可以更快实时响应当前电池组电流过大或电压不足情况。基准电压可通过改变电阻进行调整,实际大小根据当前工作的电池组数量而定。
1.4 均衡模块
本文采用基于双向反激的主动均衡的方式对电池组进行均衡。如图6所示,每个变压器原边连接一个单体电池,副边连接电池组。变压器两端选择反激式控制。
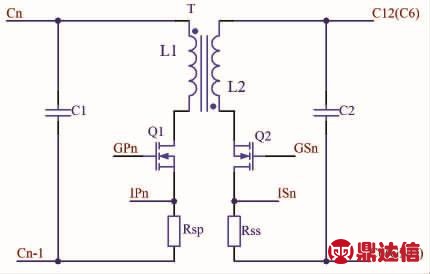
图6 第n节电池均衡电路原理图
双向反激的隔离型结构的控制策略简单,控制算法易于实现。只需选择控制变压器原边的MOS管占空比便可实现对副边恒压或恒流充电。均衡过程只需要依次选择少数出现过充单体作为原边进行能量均衡,每步均衡只需控制原边一个MOS 管即可[8]。
当第Cn节电池电压过高,主控模块发送均衡控制命令,Sn1导通,电流流过变压器Tn原边直到InP引脚检测流过的电流达到编程峰值电流时,Sn1关断,变压器初级断开,Sn2导通以最大度的减少能量转移期间的损失,直到InS引脚检测的电流为零。重复以上操作,直至均衡完成。
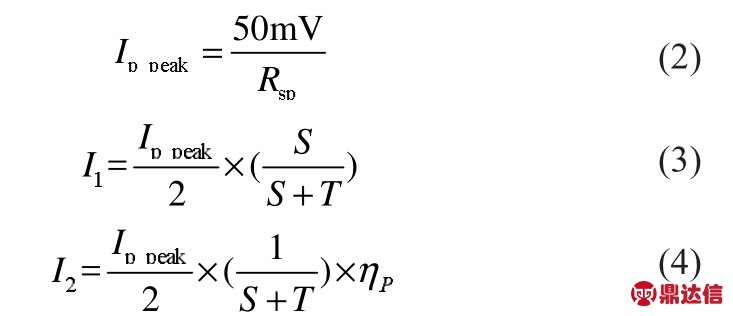
式中:Ip_peak为原边设定的最大电流;Rsp为原边的采样电阻;I1原边回路电流;I2为副边回路电流;ηP为电池放电对电池组充电的电荷转移效率;S为副边连接电池总数目,T是变压器的次级/初级的匝数比。
同理当第Cn节电池电压过低,使Sn2导通,电流通过变压器副边直到InS引脚检测流过的电流达到编程峰值电流时,Sn2关断,变压器次级断开,Sn1导通以最大度的减少能量转移期间的损失,直到InP引脚检测的电流为零。
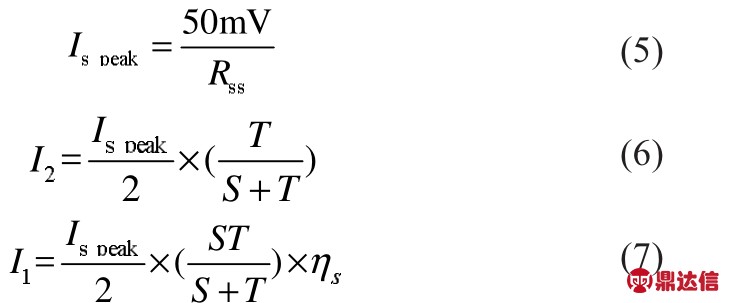
式中:Is_peak为副边设定最大电流;Rss为副边的采样电阻;I1为原边回路电流;I2为副边回路电流;ηs是电池组放电对电池充电的电荷转移效率;S为副边连接电池总数目;T是变压器的次级/初级的匝数比。
1.5 电流采集模块
本文采用CSM025B型霍尔电流传感器作为电池组电流检测传感器。CSM025B能够在电隔离的条件下测量直流、交流或脉冲电流。CSM025B的原边额定输入电流为25 A,原边测量电流值范围为-50~50 A,副边额定输出电流为25 mA,匝数比为1∶1 000,使用-12 V或+12 V进行供电,测量精度为0.7%,测量频率为0~100 kHz响应时间小于1 μs,可满足本设计的需要。
动力电池组在工作过程中,CSM025B的测得的输出电流I为 -0.025~0.025 A,对应的输出电压为 -1~1 V。而TMS320F2812的ADC转换口输入电压的范围是0~3.3 V。因此必须对采样电压进行调理,以便能输入到TMS320F2812的ADC测量引脚。
电池组在放电状态与充电状态时的工作电流方向相反,电池采集时需要在采集端配合绝对值电路进行工作,如图7所示。
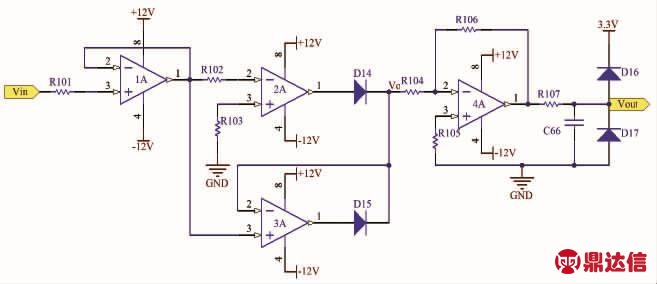
图7 绝对值计算电路
当电池组的工作电流经过传感器后,以电压的形式输出,所以在绝对值计算电路中以Vin作为输入。当Vin为正时,运算放大器A3的输出电压为正,二极管D15导通,二极管D14的两侧加上了反向电压而被强制关断,此时运算放大器A3作为电压跟随器,输出电压Vo=Vin;当电压Vin为负时,运算放大器A2的输出为正,运算放大器A3的输出电压为负,则二极管D14导通,二极管D15因为两端加了反向电压而被关断,运算放大器A2作为反相器,此时Vo=-Vin。这样就实现了绝对值的运算。
运算放大器A1作为输入电压跟随器,并作为缓冲级及隔离级,其原因在于电压放大器的输出阻抗一般比较高,通常在1 kΩ到100 kΩ,如果后级的输入阻抗比较小,那么信号就会有相当的部分损耗在前级的输出电阻中。在这个时候,就需要电压跟随器进行缓冲,起到承上启下的作用。采用电压跟随器的另外一个好处是提高了输入阻抗,这样输入电容的容量可以大幅度减小,为应用高品质的电容提供了前提保证。
电流传感器CSM025B的输出电压Vin先经过电压跟随器,再经过绝对值计算电路,最后在Vo上的输出数值与Vin完全相同的电压,最后运算放大器4作为常规运放进行使用。根据运算放大器虚断,可以得到:

根据运算放大器虚短,可以得到:

最终可以得到:

由于Vo输出1 A时,工作电流为最大值25 A,所以取R105=8.2 kΩ,R106=3.3 kΩ。
2 系统软件流程图
图8为系统工作流程图。当电池管理系统工作时,MCU通过定时中断的方式与采集芯片进行通信,获得电池组当前状态的电压、温度信息,并分析判断电池组内的各节电池电压与平均电压差是否大于阈值。若电压差超过设定阈值,则执行均衡操作,工作15 min后再次进行信息采集,直到电压差处于正常值。此时,整个电池组工作良好;若电压差大于警戒值,电池组将被强制关断,直到电池组重新维护后,电池组与电池管理系统重新工作。
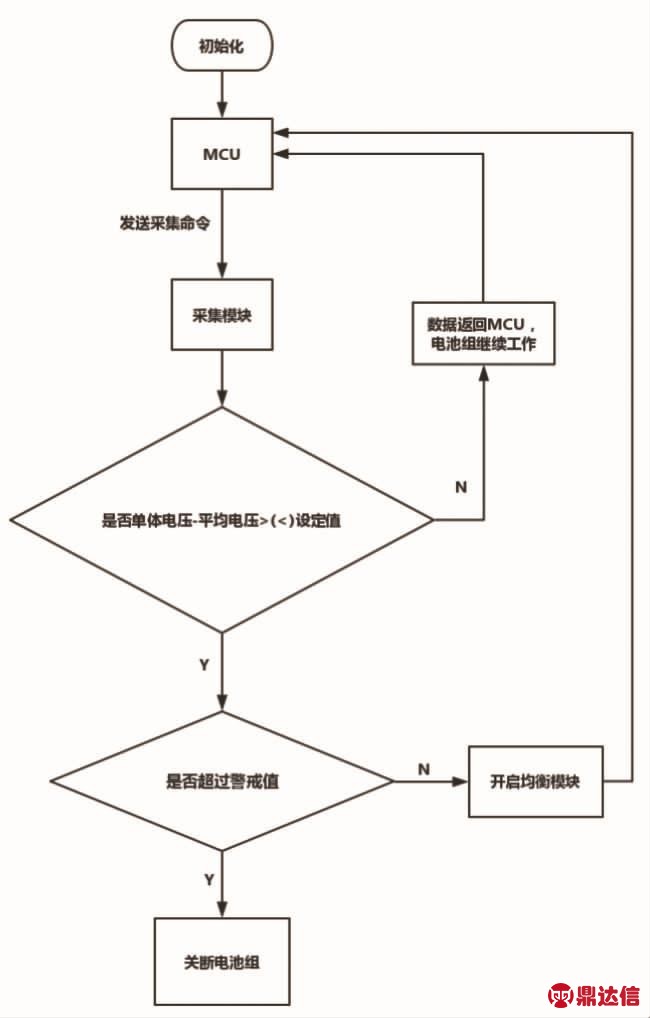
图8 系统工作流程图
3 实验测试结果与分析
通过艾德克斯IT5100电池测试仪采样记录锂离子电池(18650)的真实状态,与本系统寄存器中的采样值进行比较。将统一规格的电池充至满电状态,以0.3C放电0.5 h后,再以0.6C放电0.5 h,采集电池组信息,18650锂离子电池实际测量值与系统采样对比见表1。
通过表1数据,可以发现本组的电压采集误差最大仅为0.009 V,满足LTC6803的精度误差范围0.25%。
将放电后的12只锂电池,进行不同程度的充电,通过均衡模块进行主动均衡试验,分别测量均衡前后电压的数据。
对电池组执行30 min主动均衡,实际结果如图9所示。电池组的单体间电压不平衡程度得到了明显改善。总体电压由42.516 V减小为42.436 V,均衡模块消耗电压0.086 V。
表1 18650锂离子电池实际测量值与系统采样对比 V
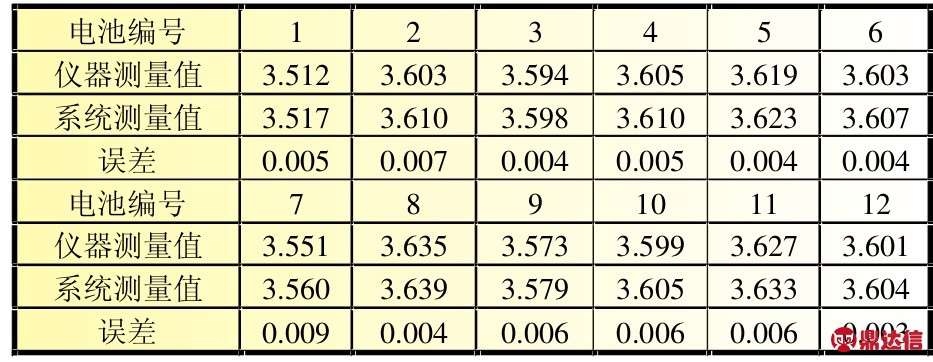
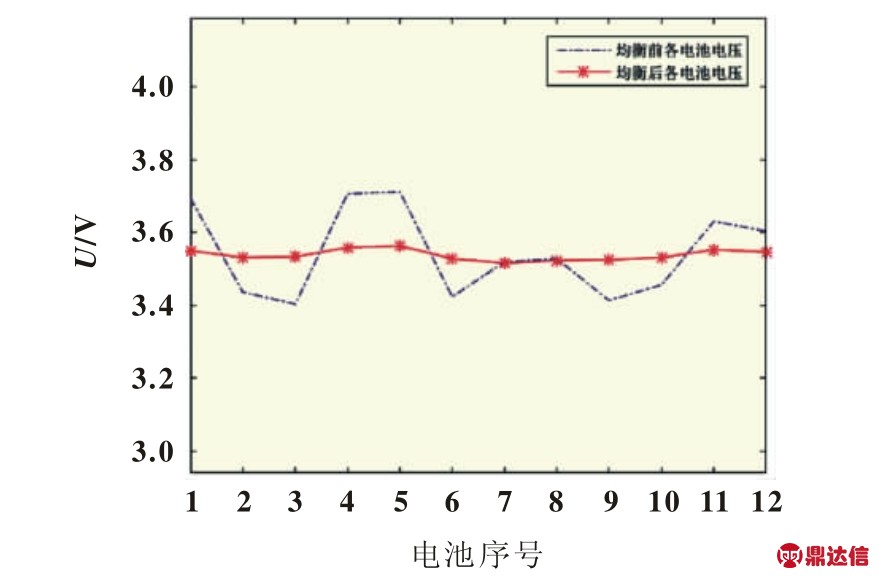
图9 执行均衡前后电池电压
4 结束语
本文在总结相关电池管理系统研究工作的基础上,提出了一种模块化的电池管理系统,完成了对电池组的电压、电流等参数的精确采集,实现了主动均衡。经实验结果表明,采集模块的最大误差不超过10 mV,满足3.7 V电压的0.25%的精度误差要求。主动均衡模块能对电池组内的电压不一致的电池进行有效的均衡操作。