摘要:介绍了水冷式铝合金电机壳的结构特征、应用情况和电机壳用铝合金型材挤压模的传统结构及其不足之处。提出了一种新的模具结构,新的结构采用的是由三件组成的分流模,是在传统结构基础上增加了一个前置分流板,可以降低挤压力和提高模具的强度;同时在上模中采用了子母上模进行镶嵌的结构方式,这种结构可以简化模具加工、节约材料和提高模具的制造精度。实践表明,新的模具结构消除了产品内腔出现椭圆和壳壁厚度不均匀的现象,是一种值得推广的模具结构。
关键词:水冷式电机壳;铝合金分流模;前置分流板;子上模;镶嵌
电机是一种使用最为广泛的电力装置。传统的电机外壳是采用铸铁铸造而成的,铸造的环境恶劣、生产效率低、不能实现大规模连续生产。铝合金具有延展性能良好、密度小、美观以及切削加工性能良好,用其做成的电机外壳,具有质轻、比强度高、冷却面积大、散热性能好、导热性高、体积小以及耐腐蚀等特点。采用铝合金挤压型材作为坯料加工电机壳,生产率极高,其坯料只需从型材上直接锯切下料,长度可按要求任意确定,具有很大的灵活性。电机壳铝型材具有活底角,内径可免切削或少切削,维修方便,生产过程比较环保,便于运输,避免了铸造电机壳致密度小、存在气孔和砂眼等铸造缺陷问题。因此,铝型材电机壳得到了广泛的应用。传统的铝型材电机壳是自然冷却或风冷式结构。由于电动汽车的电机在工作时转速高、启动频繁,使电机内的温度很高,传统的自然冷却或风冷式外壳不能满足其工作的要求。因此,开发先进适用的水冷式电机壳体成为一种必然。水冷式电机壳的结构要比传统的复杂很多,但生产水冷式电机壳挤压型材的关键在于模具。经调查了解,目前用于新能源电动汽车的水冷式电机在工作时,噪音大、故障频率高、寿命短。究其原因是电机壳的挤压型材质量低劣,这与模具结构密切相关。模具问题会使电机壳挤压型材的内孔出现椭圆现象,内孔偏心造成产品局部壁薄,在使用过程中容易发生穿孔漏水现象。因此,研发模具是解决水冷式电机壳一系列问题的关键,而模具的关键又在于设计。本文作者对一款传统的水冷式电机壳型材的挤压模结构进行剖析,提出一种子母式镶嵌结构,可使模具加工大大简化,制造精度大为提高,并可改善金属流动的状况,可有效解决因型材质量低而造成铝合金壳体电机在工作中噪声大、使用寿命短的问题。
1 水冷式电机壳型材的结构特征
图1所示为一款典型水冷式铝合金电机壳的断面。目前该电机壳型材广泛用于新能源电动汽车、矿山设备和大型通信设备中,具有良好的散热功能。该型材的断面面积为11 803.8 mm2,断面的电机壳内孔直径为Φ198 mm,最大外径为Φ242 mm,型材包含内外共13个空腔,内腔(中心)是最大空腔即内孔,是安装电机定子与转子等部件的功能部位,此内腔的尺寸精度特别是圆度和扭拧度要求高;外层则有12个较小的空腔,是起冷却作用的过水槽孔,要求其内、外两侧的壁厚均匀一致,否则容易在水压作用下发生穿孔漏水现象;在断面的外侧有12处螺丝孔,其作用是便于电机的安装固定。从型材的断面可知,虽然型材具有对称性,但形状较复杂,主要体现在最大与最小空腔的面积差异过大。
经调查走访发现,目前生产此型材存在的问题主要有两个:一是模具的成本较高,因为模具的加工难度较大,传统设计使模具的模芯必须采用铜电极利用电火花进行加工,部分分流孔、进料孔也必须采用电火花方式加工,这样电极材料消耗大,且经电火花加工后的模具抛光研磨量大;二是模具在挤压过程中产品的成形性差,各部位的金属流速难以一致,这是因为模具结构设计所导致的内层分流桥难以加工成易于金属流动的水滴形,从而影响了处于分流桥下部位的金属供应和金属流速,型材内孔容易出现椭圆以及型材壁厚不均匀的现象。此外,还存在模具寿命短,容易出现早期失效的现象,模具失效后部件的可重复利用率低,互换性能差,因而造成巨大的材料浪费,使其生产和使用成本高。
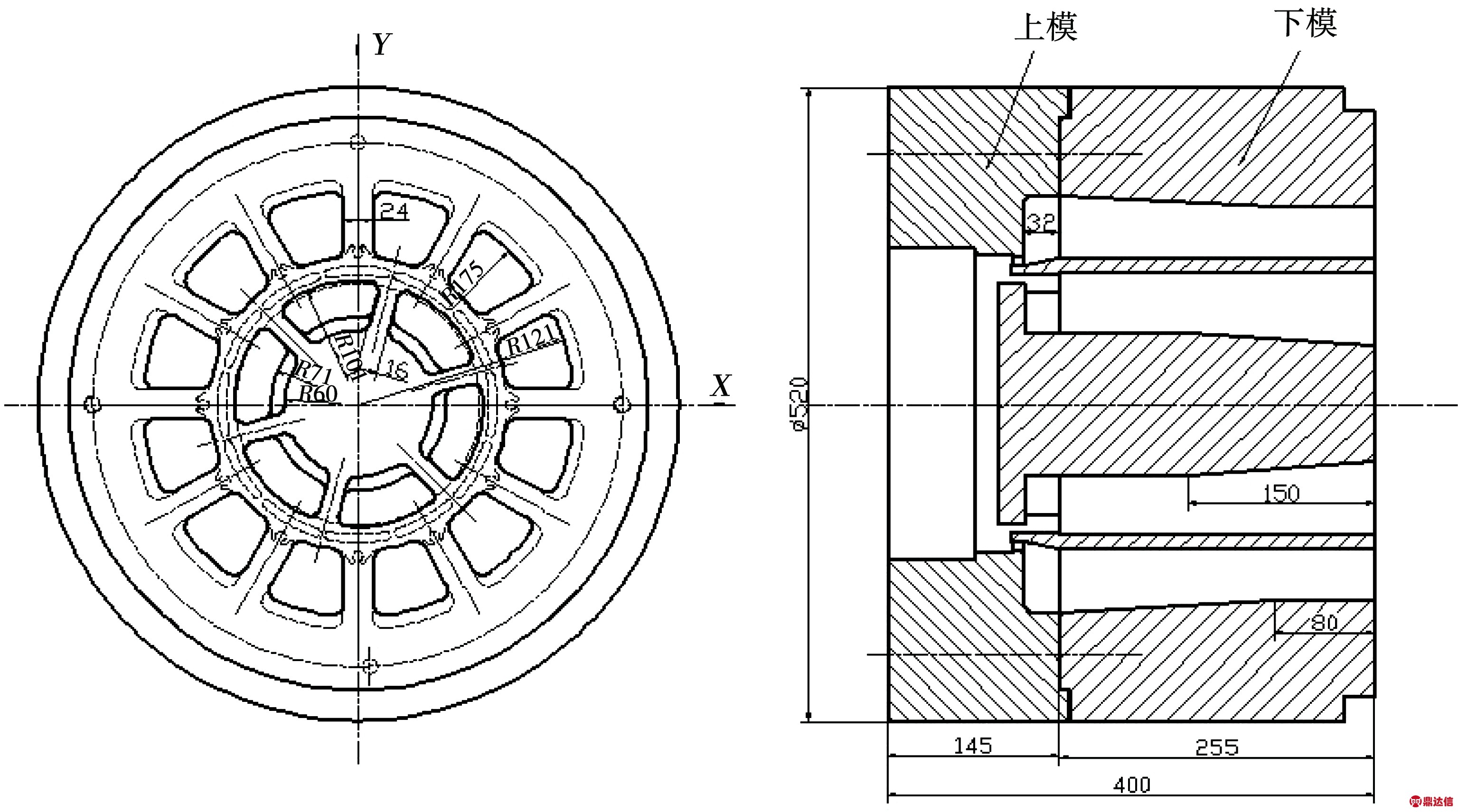
图1 水冷式电机壳型材断面示意图
Fig.1 Section of water-cooled motor housing
2 传统的模具结构
根据型材的结构特点,同时考虑其变形程度以及模具的成本,传统的模具在挤压机能力和模具尺寸规格的选择方面都是合理的。挤压机能力为40 MN,选用的挤压筒内径为Φ365 mm,模具尺寸规格为Φ520 mm×400 mm。经计算,挤压系数为8.9。采用的模具结构为传统的二件式分流模,模具由上模与下模组成,如图2所示。
这种结构的不足之处在于,一是13个内腔形成的13个模芯集中在1个上模中,导致外层12个模芯与中心的大模芯之间形成的间隙或壁厚必然有部分处于分流孔之间(即分流桥底下),该部位的分流桥底部是无法像正常的分流桥那样加工成水滴状(有利于金属的流动和焊合),这样的部位数量与内层分流孔数量相同,这些部位的金属供应较困难,甚至容易出现金属充不满现象,导致金属流速严重滞后,从而造成内、外金属流速差异严重而使产品出现椭圆现象;二是采用这种结构的上模厚度达250 mm以上,分流孔的加工难度大,特别是处于内层的分流孔,均是盲孔式的加工,加工误差大,加工精度得不到根本的保证;三是13个模芯的最后加工成型要采用电极材料借助电火花机床进行加工来完成。由于空腔的面积及外形尺寸较大,所需的电极材料较多,同时电火花加工方式的制造周期长,且所加工出来的表面粗糙度大,造成模芯的抛光与研磨难度大。因模具结构的问题造成的累积误差自然大,使结构上处于对称的部位的实际精度偏差大,这是型材产生椭圆和偏心的根本原因。要解决模具的加工问题必须解决模具的结构形式问题。同时,由于上模厚度较大影响淬透性,容易使心部的韧性不足,造成模具在挤压中出现过早失效,缩短模具的使用寿命。
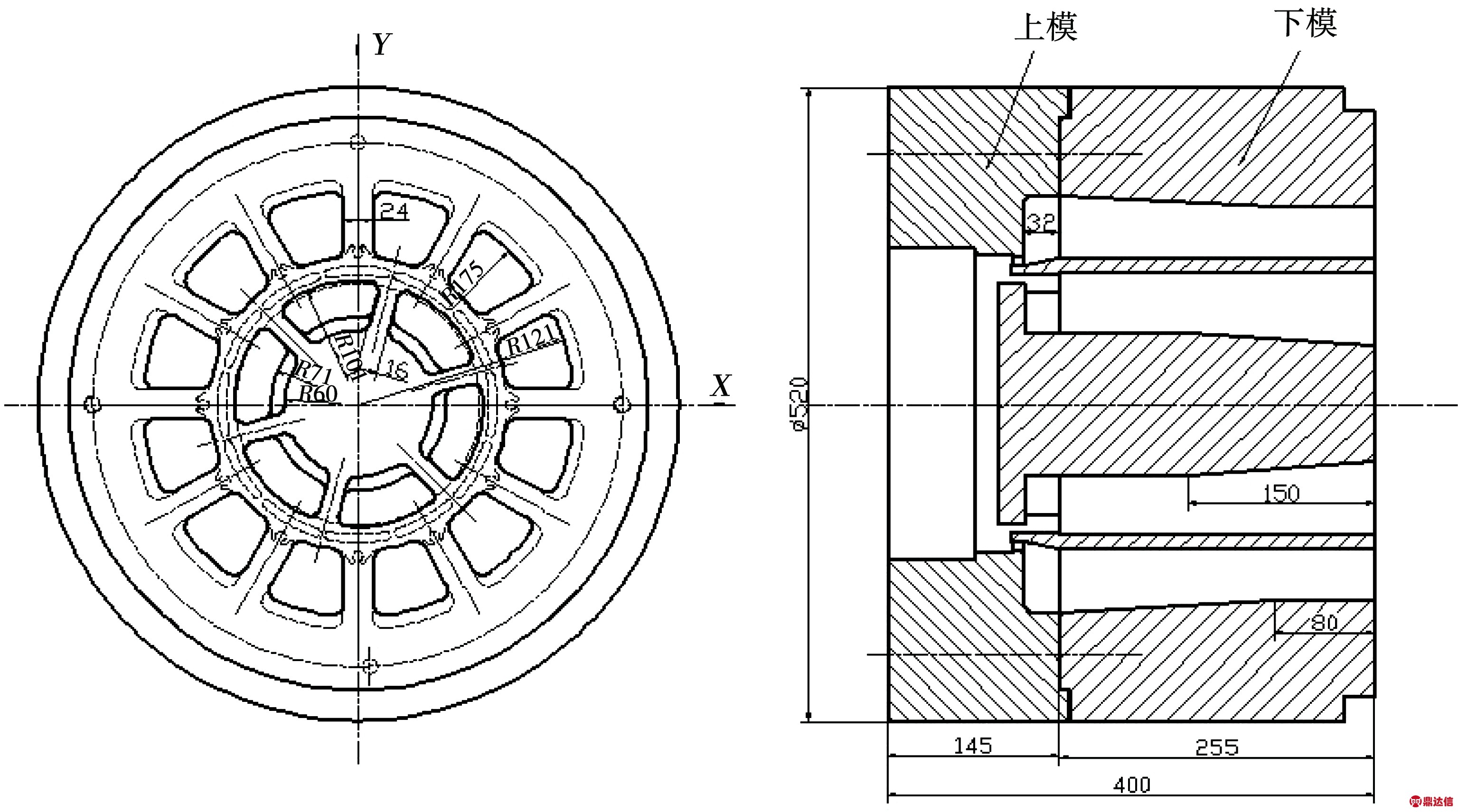
图2 传统的模具结构示意图
Fig.2 Traditional die structure
传统模具结构的主要技术参数如下:
1)分流比为3.95。
2)分流孔数量共18个:外层12个,内层6个。分流孔最大外径为Φ350 mm。
3)上模厚度为255 mm,下模为145 mm。
4)外层分流桥宽度为24 mm,内层分流桥宽度为16 mm。
5)下模焊合室深度为32 mm,模孔工作带长度为7 mm。
3 改进后的模具结构
针对传统模具在挤压过程中存在的问题,采用一种三件式和子母式模芯的分流模结构。
3.1 模具的结构形式
突破传统的结构方式,采用三件式的分流模结构,将传统的上模厚度分解,在上模的前面设计一个前置分流板,即金属经过前置板分流变形后再进入上模,这样模具由前置分流板、上模与下模组成。同时在上模中采用子母式镶嵌结构,如图3所示。这样的好处在于,上模的有效厚度减小了,可降低加工的难度和提高模具在热处理过程中的淬透性,这无疑是对模具的强度有利。
3.2 前置分流板的设计
设计一个前置分流板,目的是使金属经过前置板进行一次预成形分流,分流比比较大,同时可以减少分流桥的数目,大大降低金属挤压过程中的最大挤压力,这是基于分流比与挤压力成反比的原理。前置分流板结构如图4所示。
前置分流板采用了内、外两层共7个分流孔布置,外层4个分流孔是主要提供型材外部及12个小模芯之间的金属供应;内层的3个分流孔提供12个小模芯与1个大模芯之间形成的壁厚间隙的金属流量供应。经计算,金属经过前置分流板的分流比为4.8,为挤压比的54%。为了确保各个部位最终成型时的金属流速趋于一致,内、外分流孔的面积关系应合适,考虑到挤压筒在径向上存在压力梯度的影响,经数值模拟并结合经验数值确定两者的关系如下:
S1=(1.4~1.8)S2
(1)
式中:
S1—外层单个分流孔面积;
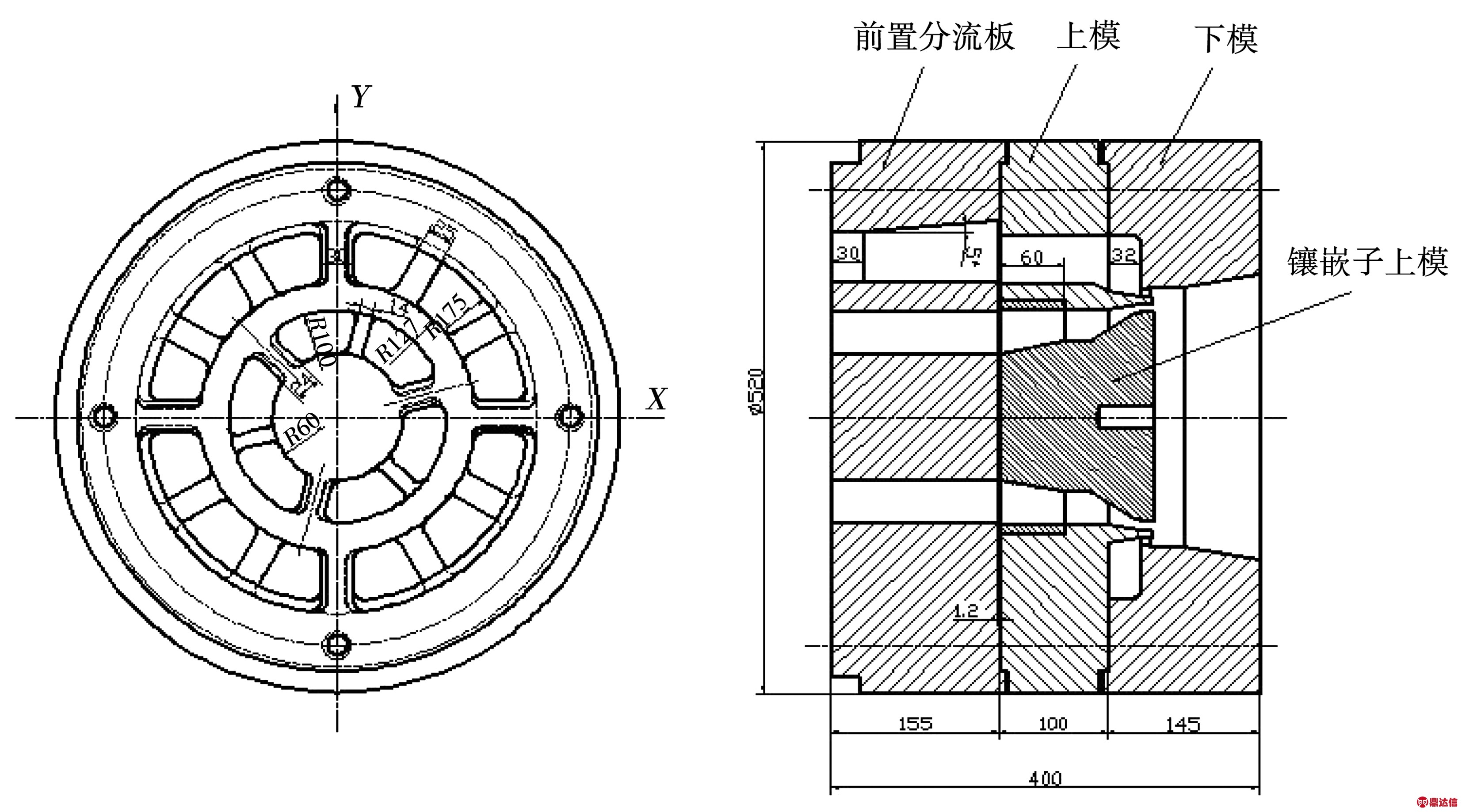
图3 改进后的模具结构
Fig.3 Improved die structure
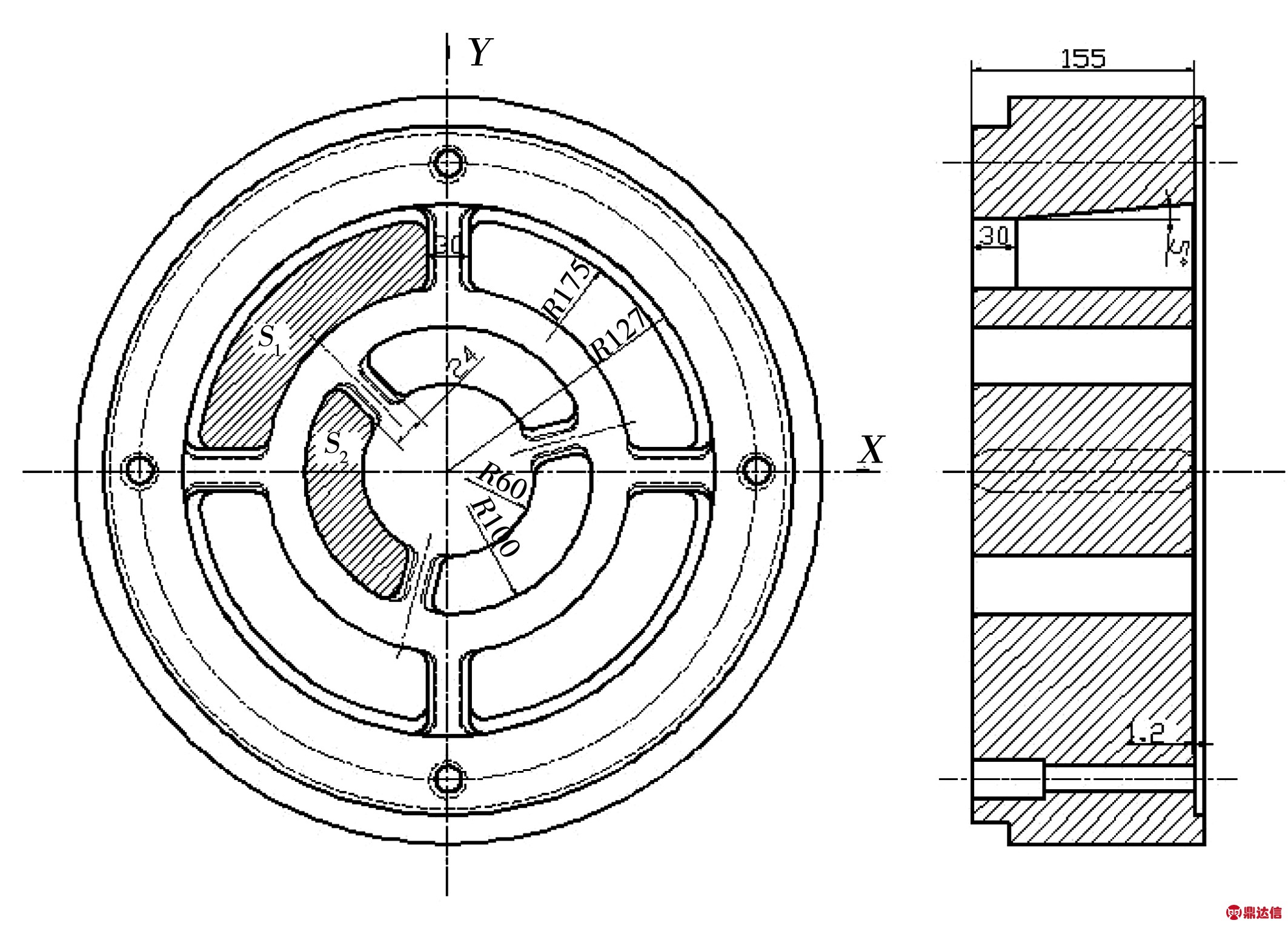
图4 前置板结构示意图
Fig.4 Structure of front splitter plate
S2—内层单个分流孔面积。
这样得到的结果比较理想。
3.3 应力间隙的设计
在上模与前置分流板之间设置0.8 mm~1.2 mm的应力间隙,间隙在前置分流板上。这样的目的是,在挤压过程中,前置分流板首先接触金属,只要前置分流板的强度足够,模具的受力将主要由前置分流板承担。应力间隙减轻或避免了前置分流板将其所受的力传递到上模的端面,从而降低了上模中心分流桥的受力,因而可以降低上模在挤压中的变形或弹性挠度,提高了模具的刚性和强度,这样就可以减小或避免型材的壁厚变化。
3.4 上模的结构设计
上模采用18个分流孔布置形式,分别为外层12个和内层6个。即前置分流板外层的4个分流孔对应上模外层的12个分流孔,当外层的4个分流孔的金属进入到上模后将进行二次分流,前置分流板的每个分流孔的金属将分流成三股金属分别进入对应上模的3个分流孔中;同理,前置分流板内层的3个分流孔进行二次分流时则每个分流孔分成两股金属进入上模中,3个分流孔的金属分成6股金属进入上模内层的6个分流孔中。金属的二次分流是为了使金属分配与流动更加均匀,可以使分流桥的宽度减小,这特别有利于金属的焊合和各处金属的流速趋于一致。经验表明,分流桥的宽度越小,分流桥下的金属流速与相邻部位的差异将越小,当分流桥宽度小于16 mm时,这种差异可忽略不计,这点对于中心圆孔的圆度保证是相当重要的。上模内、外层的分流桥宽度分别取16 mm和14 mm。
这样的分流孔布置设计解决了金属流量的供应和分配问题,但并没有解决模具加工简化而提高模具精度的问题。传统结构的上模模芯加工难度大。根据型材的特点,上模采用镶嵌式结构,这样既解决了模具加工困难问题又增加了模具的互换性。考虑到中心模芯的面积大,将上模内层的6个分流孔与中心模芯从上模整体中分割出来形成一个子上模,这样母体上模就留下12个小模芯,这将使加工大为简化,模芯加工主要以车削方式就能完成,而且这12个小模芯均可设计成锥台式,大大提高了模芯的刚性。母体上模结构如图5所示。
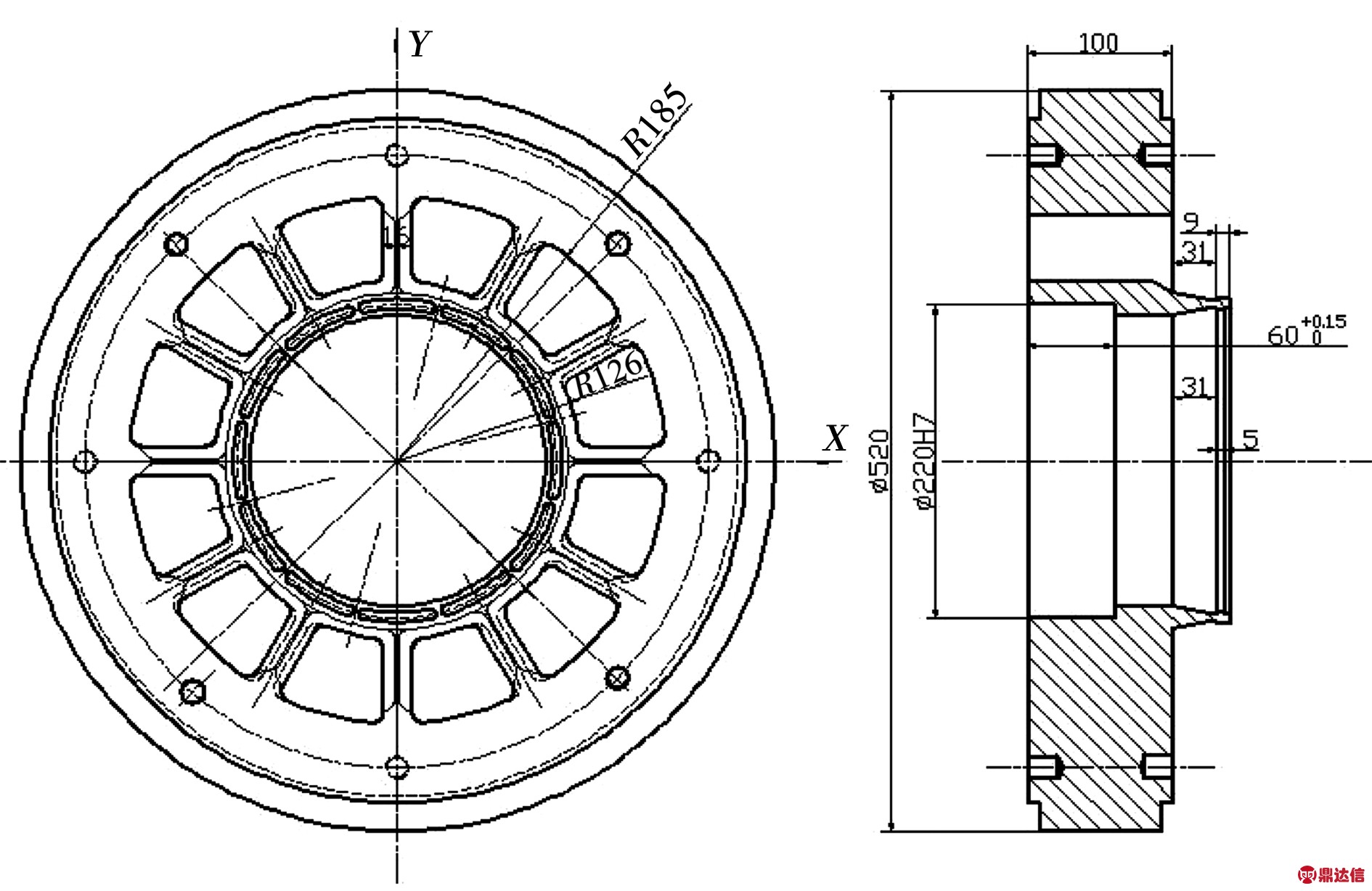
图5 母体上模结构示意图
Fig.5 Structure of the mother male die
同样,子上模的加工也大为简化,就像正常的上模一样进行加工,模芯完全采用车削的方式,特别是分流桥可以加工成水滴形。同时,由于镶嵌的需要,使得子上模的模芯在镶嵌后对应的焊合室深度增加,从而使中心部位可容纳的金属量增加,因而可以改善金属流动的状态,提高中心圆孔成型时的焊缝质量,从而提高了电机壳的力学性能。子、母上模分开单独加工完成后再镶嵌在一起组成完整的上模。子上模结构如图6所示。
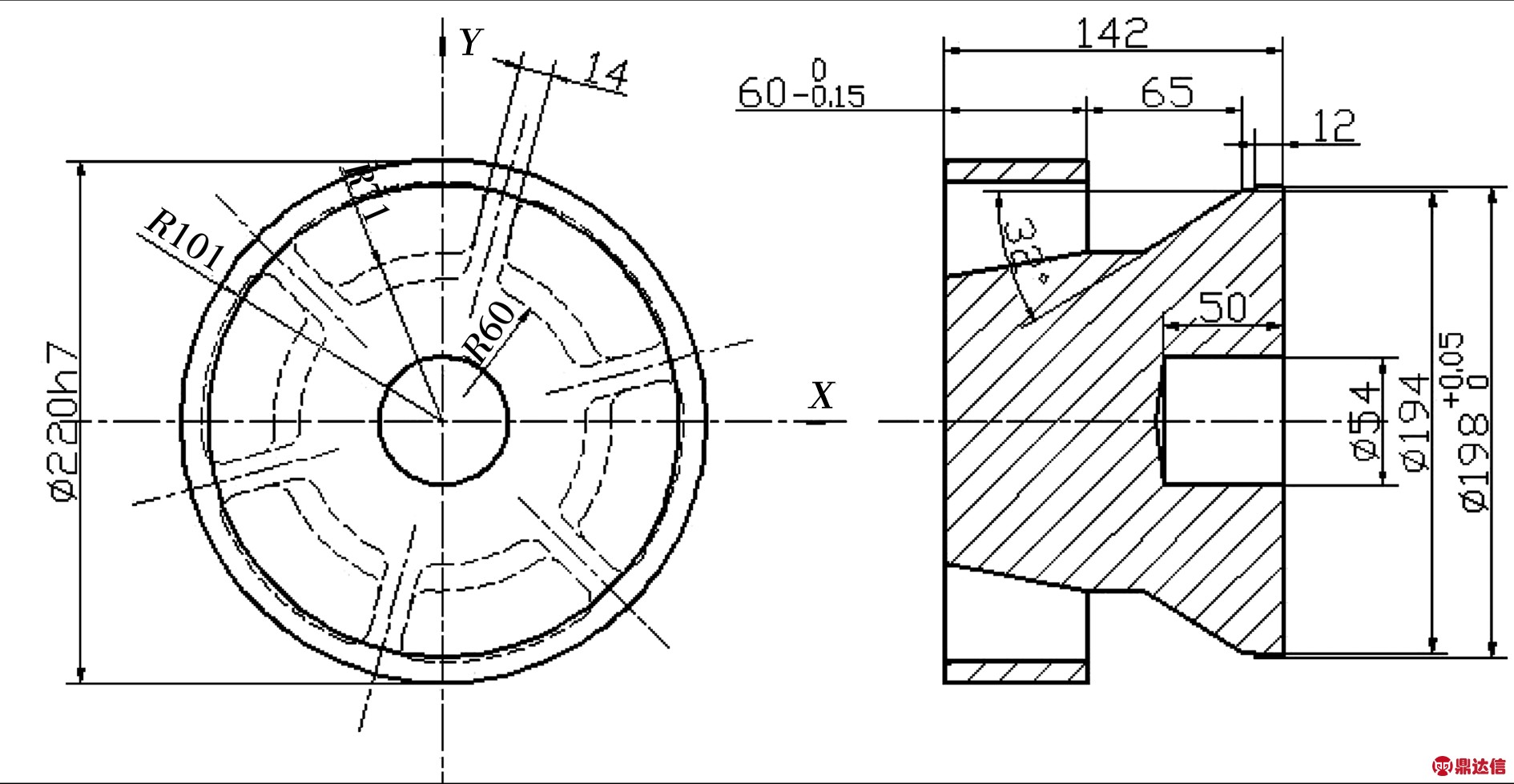
图6 镶嵌子上模结构图
Fig.6 Structure of sub-male die
采用子、母上模镶嵌结构后,13个模芯的加工大大简化,完全避免了电火花加工,节省了大量的电极材料。更重要的是,提高了模具的整体精度,大大减小了误差的积累,使制造精度同样具有“对称性”,从而保证型材产品的最终精度。
3.5 下模的结构
下模的结构主要包括工作带和焊合室。焊合室的轮廓依上模的母上模进入下模焊合室前的最大分流孔的轮廓而定,在分流桥对应位置考虑支撑的桥墩,可减小分流桥的跨度从而提高模具的强度。采用等值工作带并向螺丝孔处过渡的方法,工作带长度为圆孔处取7 mm、螺孔开口处取3 mm。焊合室深度为32 mm。为了提高外表面的焊缝质量,离模孔边缘1 mm处设置阻流环,高度为4 mm。模孔的空刀采用二段分级和锥形出口的形式。下模结构如图7所示。
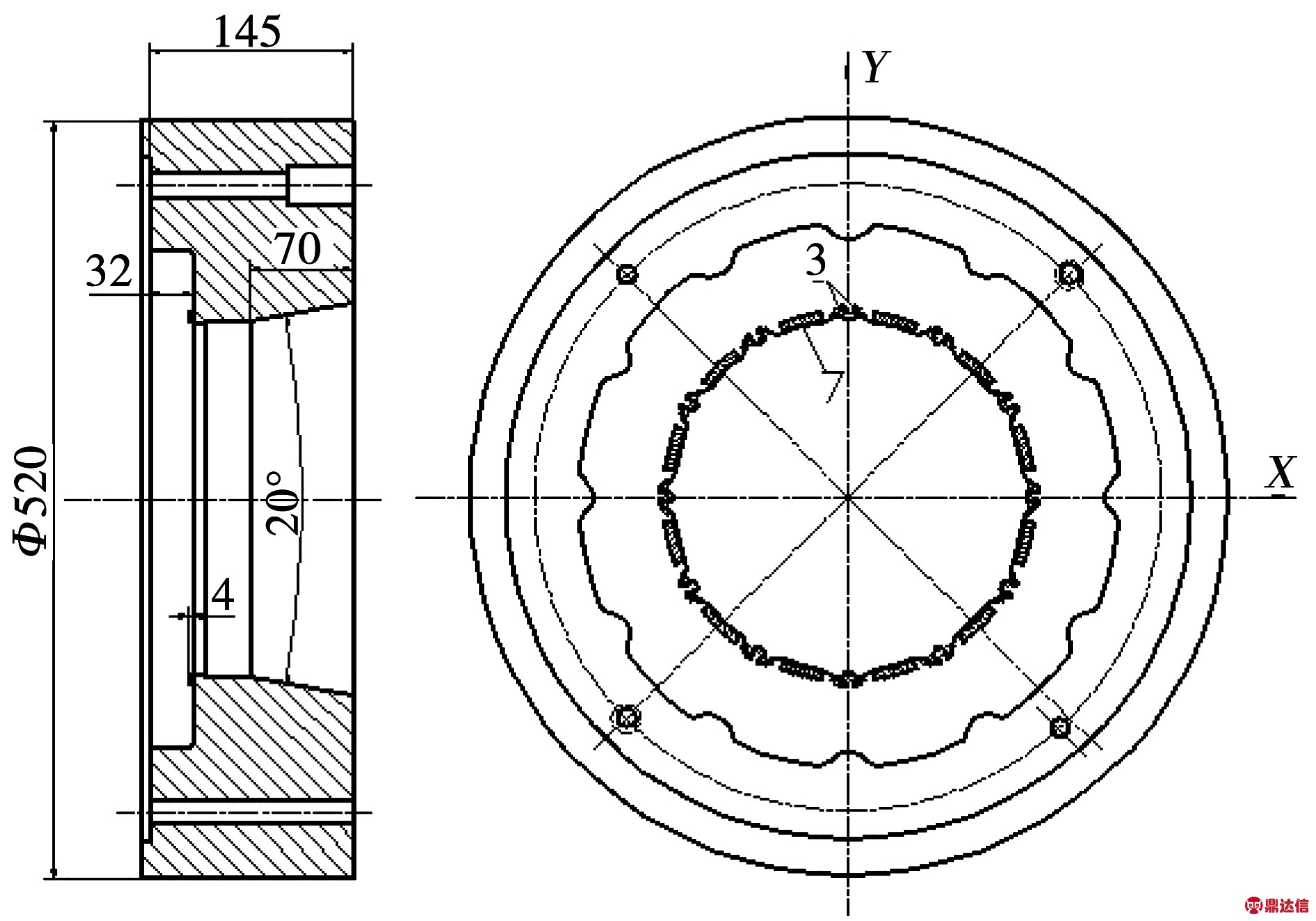
图7 下模结构图
Fig.7 Structure of the female die
4 结束语
对改进设计的新结构模具,进行实际制造、使用跟踪,记录的数据表明,新模具的制造周期大大缩短,比传统结构模具的制造周期减少15 d,制造的成本大大降低;新模具的使用寿命是传统模具的4.3倍;更重要的是,模具在挤压过程中的最大挤压力比传统的下降20%,各部位的金属流速几乎一致,挤压过程平稳顺利;挤出的型材质量大大提高,精度可达国标高精级,局部达到超高精级,避免了传统模具挤压型材出现的内腔椭圆形和壁厚不均匀现象。