摘 要 油井管作为油气田开采过程中的基础设施,随着油气田的不断深入开发,油气井的实际开采环境越来越恶劣,其接头螺纹连接处的腐蚀失效问题日益突出和严重。为保障井筒完整性,提高油井管的使用寿命,对几种典型的油井管接头螺纹腐蚀类型进行了介绍,详细分析和综述了其腐蚀机理和影响因素。针对文中介绍的腐蚀类型,对其腐蚀防护技术进行了系统性的总结。并对油井管接头螺纹腐蚀的发展方向进行了探讨,认为多种因素耦合作用下的油套管腐蚀防护研究是未来主要的研究方向。
关键词 油井管; 接头螺纹; 缝隙腐蚀; 应力腐蚀; 防护
伴随着经济的持续高速发展,对于石油天然气的需求日益增加。而石油天然气的开采需要大量的油管和套管,它们通过螺纹接头连接的方式形成管柱,是油气运输的通道,油井管能否安全稳定的运行是油气井顺利开采关键,但随着越来越多超高压、超高温、超高产油气井的出现,油井管的安全性面临巨大挑战。近年来,因油井管失效造成的开采事故层出不穷,其中以油井管接头螺纹的腐蚀失效最为普遍,如肯尼亚克某油井在进行维护时出现原油泄漏,从起出的油管发现,其中有29根油管接箍处腐蚀变形,8根腐蚀穿孔,其余油管接箍处都有不同程度的腐蚀痕迹[1]。方培林等[2]调查统计在2013—2017年渤海某油田的油井管柱情况,发现油井管管柱腐蚀穿孔14井次,其中分离器腐蚀断裂7井次。根据美国石油协会(American Petroleum Institute,API)统计,油井管连接处的腐蚀失效占油井管腐蚀失效的80%[3],因此油气管材螺纹连接处的腐蚀失效一直是石油天然气工业中所关心和研究的热点之一。为保障井筒的完整性,减少因油井管腐蚀造成的生产安全事故和环境污染的风险,针对油气田开发过程中油井管接头螺纹的主要腐蚀类型,介绍油井管螺纹腐蚀机理及其控制方法的研究进展,并提出未来油井管接头螺纹腐蚀与防护的研究方向。
1 接头螺纹缝隙腐蚀研究进展
缝隙腐蚀是指在金属与金属或非金属之间的缝隙中,由于介质的迁移受到阻滞引起缝隙内金属的加速腐蚀。缝隙腐蚀是常见的局部腐蚀之一,无论是在酸性、碱性、中性的腐蚀性介质中,只要金属或合金由于焊接、铆、螺纹连接等存在缝隙,都有可能引起缝隙腐蚀。
1.1 缝隙腐蚀机理
目前,大部分相关学者认为局部腐蚀和环境差异是引起油井管螺纹缝隙腐蚀的主要原因。缝隙腐蚀的闭塞电池模型是目前较为主流的对金属缝隙腐蚀的解释。该模型中缝隙腐蚀的产生共有两个部分,这里结合碳钢在中性介质中发生缝隙腐蚀阐述其机理。在缝隙腐蚀的初期,腐蚀在缝隙内、外金属表面共同进行。
阳极溶解反应为
FeFe2++2e-(1)
阴极还原反应为
O+2H2O+4e-4OH-(2)
经过一段时间的腐蚀反应后,缝隙内的氧气很快被耗尽,缝隙内外氧气含量相差过大从而在宏观上形成了的氧浓度差电池,因此缝隙内金属被优先腐蚀。同时腐蚀产物在缝隙口产生并堆积,氧气很难通过缝隙口进入缝隙内,缝隙内的还原反应终止,另一方面,缝隙外金属表面反应持续进行,缝隙内外金属表面的差异形成了闭塞电池。缝隙腐蚀的加深和扩大是从形成闭塞电池开始的,此时缝隙口被腐蚀产物阻塞,缝隙内介质处于滞留状态,金属阳离子Fe2+难以向外扩散,随着金属离子的堆积,造成缝隙内正电荷过剩,促使缝隙外Cl-向缝隙内迁移以保持电荷平衡,并在缝隙内形成金属氧化物。缝隙内金属离子发生反应[4]为反应使腐蚀介质酸化,在Cl-的富集和酸化介质的共同作用下缝隙内金属加速腐蚀,所以闭塞电池的自催化作用是造成缝隙腐蚀加深的根本原因。在油气田开采过程中,大部分油井管螺纹发生的缝隙腐蚀都符合闭塞电池的自催化理论。
FeCl2+2H2OFe(OH)2↓+2HCl(3)
1.2 影响螺纹缝隙腐蚀的因素
近年来,相关学者通过对油井管腐蚀行为研究发现,引起油井管接头螺纹发生缝隙腐蚀的主要与油井管的材料、所处环境和缝隙尺寸等因素有关。
1.2.1 材料的影响
油井管螺纹接头耐缝隙腐蚀性与其本身的合金材料有最为直接的影响。相关研究表明,在材料中添加适量的Cu、Cr、Mo、N等能抑制材料缝隙腐蚀的发生。Oldfield等[5]通过对比同种类不锈钢的耐缝隙腐蚀性,发现的Mo和N能显著改善材料耐蚀性,延缓缝隙腐蚀的蔓延。而且不同材料引起的缝隙腐蚀,其相应的腐蚀机理也各不相同,张耀等[6]研究了同等条件下TP140和HP-13Cr的缝隙腐蚀行为,结果表明TP140以均匀腐蚀的腐蚀特征为主,缝隙腐蚀机理符合闭塞电池的自催化理论,HP-13Cr以点蚀的腐蚀特征为主,其腐蚀机理符合IR(I为电流, R为电阻)降机理。刘丽等[7]采用了腐蚀失重电化学测试方法,研究了FeCl3溶液中油管钢和接箍钢的缝隙腐蚀敏感性,结果表明:油管钢的耐缝隙腐蚀性明显弱于接箍钢的耐缝隙腐蚀性,油管和接箍接触处的腐蚀主要以油管的缝隙腐蚀为主,缝隙内呈现点蚀的特征。这有利于油套管台阶面腐蚀的研究,为探讨台阶面产生腐蚀的原因奠定了基础。赵柏杰等[8]研究发现,相比于金属与其他材料接触,金属与金属接触面下腐蚀形貌宽度最大,深度最浅,蚀坑横向发展,腐蚀溶液横向扩散更容易。这对深入了解油井管螺纹缝隙腐蚀发生的过程具有重要的现实意义。Rajendran等[9]通过研究钛合金的缝隙腐蚀行为,发现钛合金中的Mo能改变其表面的氧化膜,与纯钛相比,Mo使钛合金的抗缝隙腐蚀能力大幅度增强。
1.2.2 环境的影响
油井管所在环境中的Cl-含量、温度、腐蚀介质的pH对缝隙腐蚀的产生和发展都有影响。Dastgerdi等[10]发现由于Cl-扩散速度快,容易与钝化膜产生相互作用,降低钝化膜的稳定性,抑制钝化膜的生成,导致材料的点蚀电位降低,腐蚀敏感性增加。徐秋发等[11]通过对碳钢的缝隙腐蚀行为研究发现,当腐蚀介质中Cl-含量较少时,缝隙内聚集的Cl-会形成金属氯化物,从而抑制缝隙腐蚀的发生,但随着Cl-的含量不断增高,过多的金属氯化物会溶于水,导致模拟溶液成分发生变化,从而加剧缝隙腐蚀的产生。虽然没有深入讨论Cl-含量的临界点,但仍为后续研究Cl-对缝隙腐蚀的影响奠定了基础。Hu等[12]研究了X52钢在二氧化碳饱和溶液下的缝隙腐蚀行为,发现缝隙腐蚀发生后,缝隙内腐蚀介质的pH和Cl-含量变高,因此他们认为pH和Cl-的浓度变化是引起缝隙腐蚀的主要原因。杨军征等[13]通过腐蚀模拟评价实验发现溶解氧对油井管缝隙腐蚀有很大的促进作用。温度对缝隙腐蚀的影响较为复杂,不仅影响缝隙腐蚀电位,还影响钝化膜生成速度和结构以及腐蚀介质在缝隙内的扩散速度[14-15],但总体来说,温度越高,材料越容易发生缝隙腐蚀,一般用临界缝隙腐蚀温度(critical crevice corrosion temperature,CCT)来表示缝隙腐蚀发生的倾向。陈建波[16]研究了温度对P110油井管钢缝隙腐蚀的影响,得到在不同温度下的缝隙腐蚀速率图,如图1所示。结果表明,随着温度的升高,P110油套管钢的缝隙腐蚀速率逐渐上升,这可能是由于随着温度的升高,较多的腐蚀产物堆积在缝口,造成缝隙内闭塞效应加剧所导致。
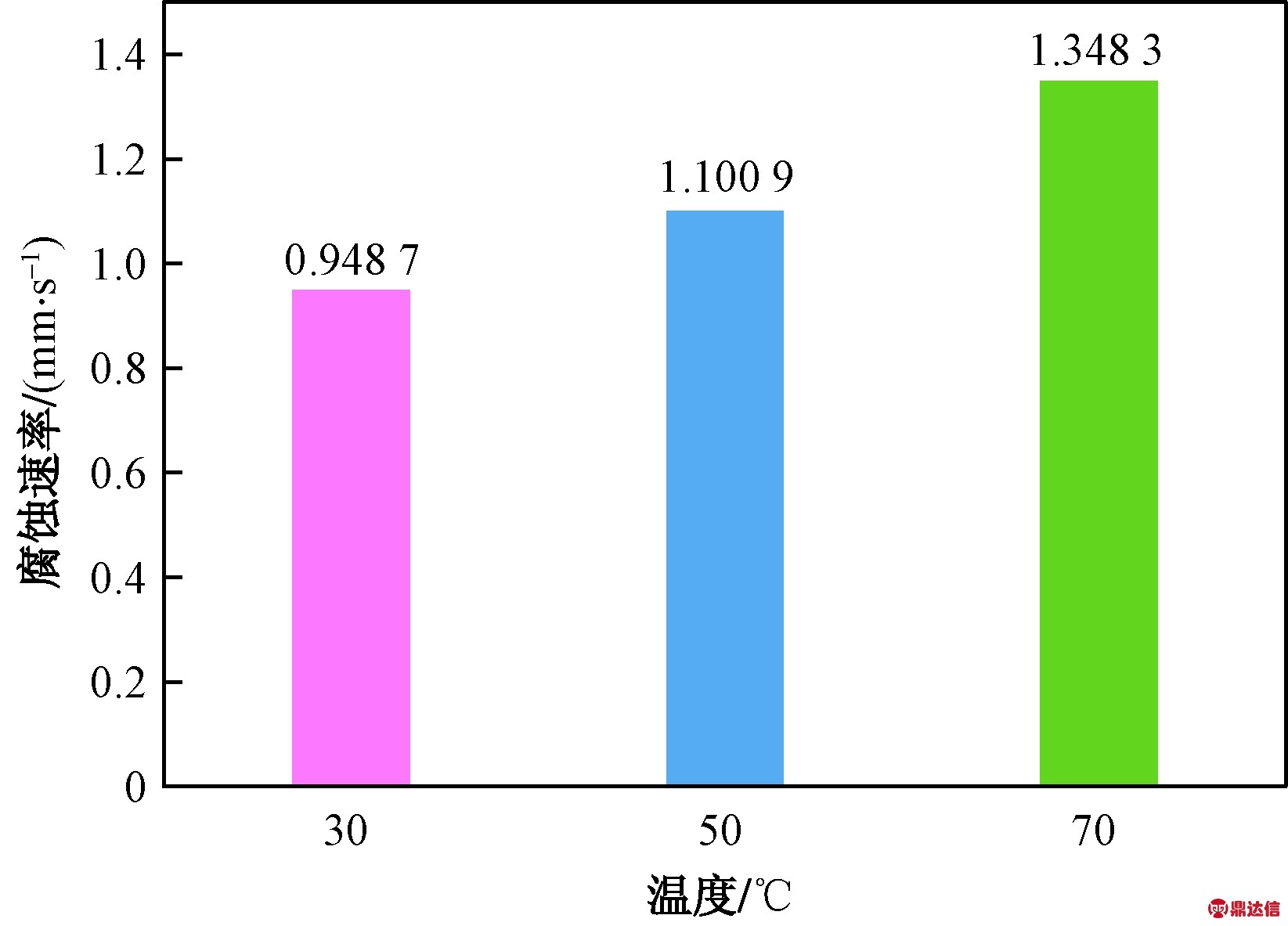
图1 P110钢在不同温度下的缝隙腐蚀速率[16]
Fig.1 Crevice corrosion rate of P110 steel at different temperatures[16]
当缝隙腐蚀发生时,缝隙内溶液pH发生变化引起腐蚀溶液化学特性改变,造成其侵蚀性增强,对钝化膜的击穿电位造成影响[17],促进缝隙腐蚀蔓延。因此,缝隙内溶液pH的变化是影响缝隙腐蚀的重要因素之一。Han等[18]研究了pH对SAF 2205 双相不锈钢(duplex stainless steel,DSS)缝隙腐蚀的影响,结果表明,溶液pH在1~8.5时材料的CCT逐步增加,当溶液pH超过8.5后,材料CCT急剧下降,他们认为是因为SAF 2205 DSS在碱性环境下生成的腐蚀钝化膜比酸性环境下生成的更稳定造成这种现象的产生。田先勇[19]通过挂片失重法研究了pH对N80油套管缝隙腐蚀的影响。研究结果如图2所示,因为在碱性环境中产生了较多的腐蚀产物,相对稳定的腐蚀产物覆盖在材料表面从而降低了腐蚀速率,导致N80油套管腐蚀速率随着pH的增大而下降。
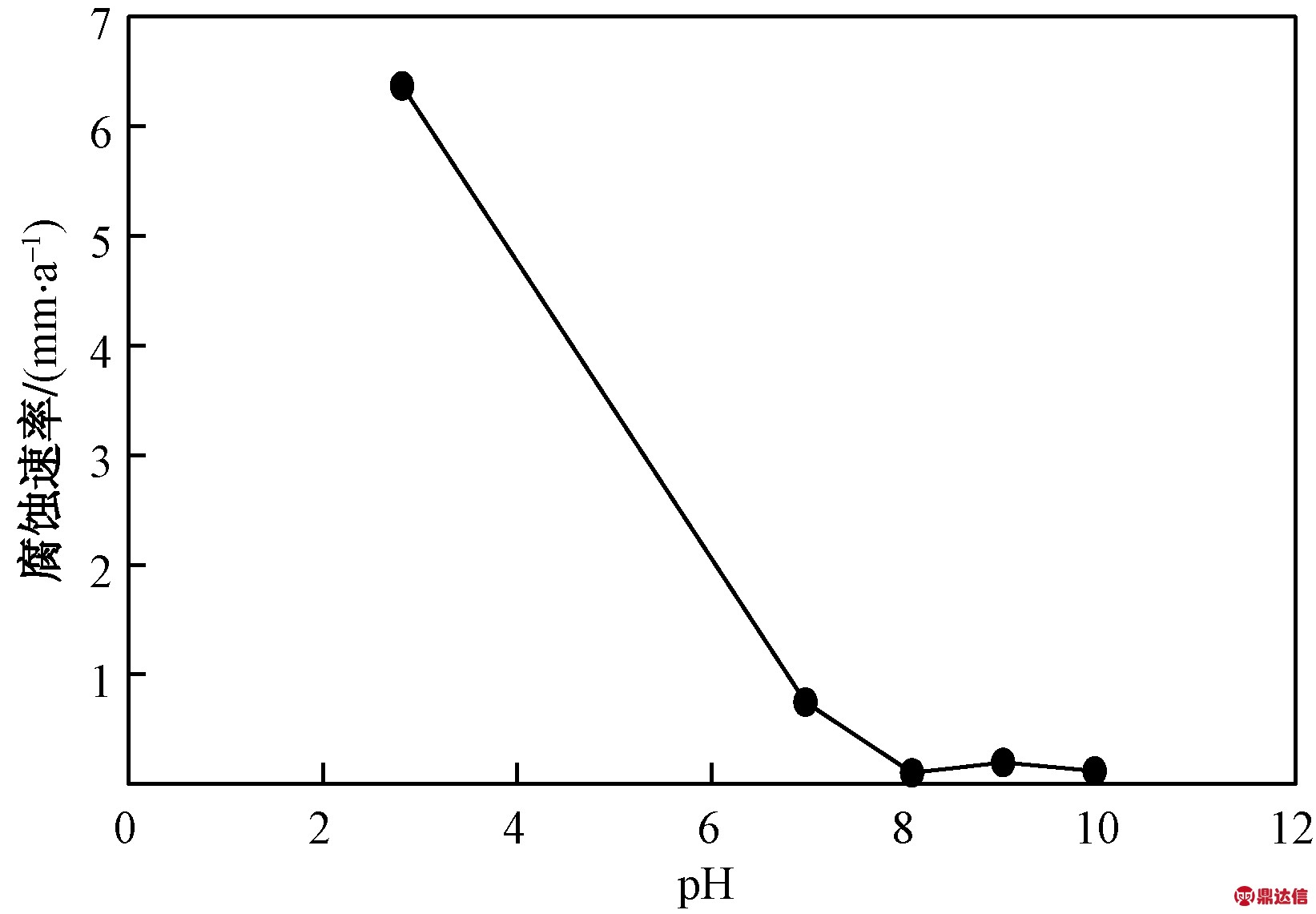
图2 pH对材料缝隙腐蚀的影响[19]
Fig.2 Effect of pH value on crevice corrosion of materials[19]
1.2.3 缝隙尺寸的影响
缝隙的宽度和深度以及缝隙内、外面积比等都是影响缝隙腐蚀的重要因素。薛娟琴等[20]模拟了高温高压的油气田环境,利用浸泡试验研究TP140高强度套管钢的缝隙腐蚀情况,研究表明:在相同的腐蚀环境中,材料是否存在缝隙对于其腐蚀敏感性影响巨大,与不存在缝隙的TP140高强度套管钢相比,存在缝隙的TP140高强度套管钢在液相中的腐蚀速率增加了200%~500%,在气相中的腐蚀速率增加了60%~120%,这表明金属本身缝隙极大地促进了缝隙腐蚀的扩展。王婷等[21]应用矩形缝隙模型研究了缝口尺寸d对缝隙腐蚀的影响。结果如图3所示,缝口较小时的电极电位明显小于缝口较大的电极电位,当缝口较小时O2进入缝隙更困难,缝隙内外形成氧浓度差,造成缝隙内金属溶解,促进腐蚀加重。
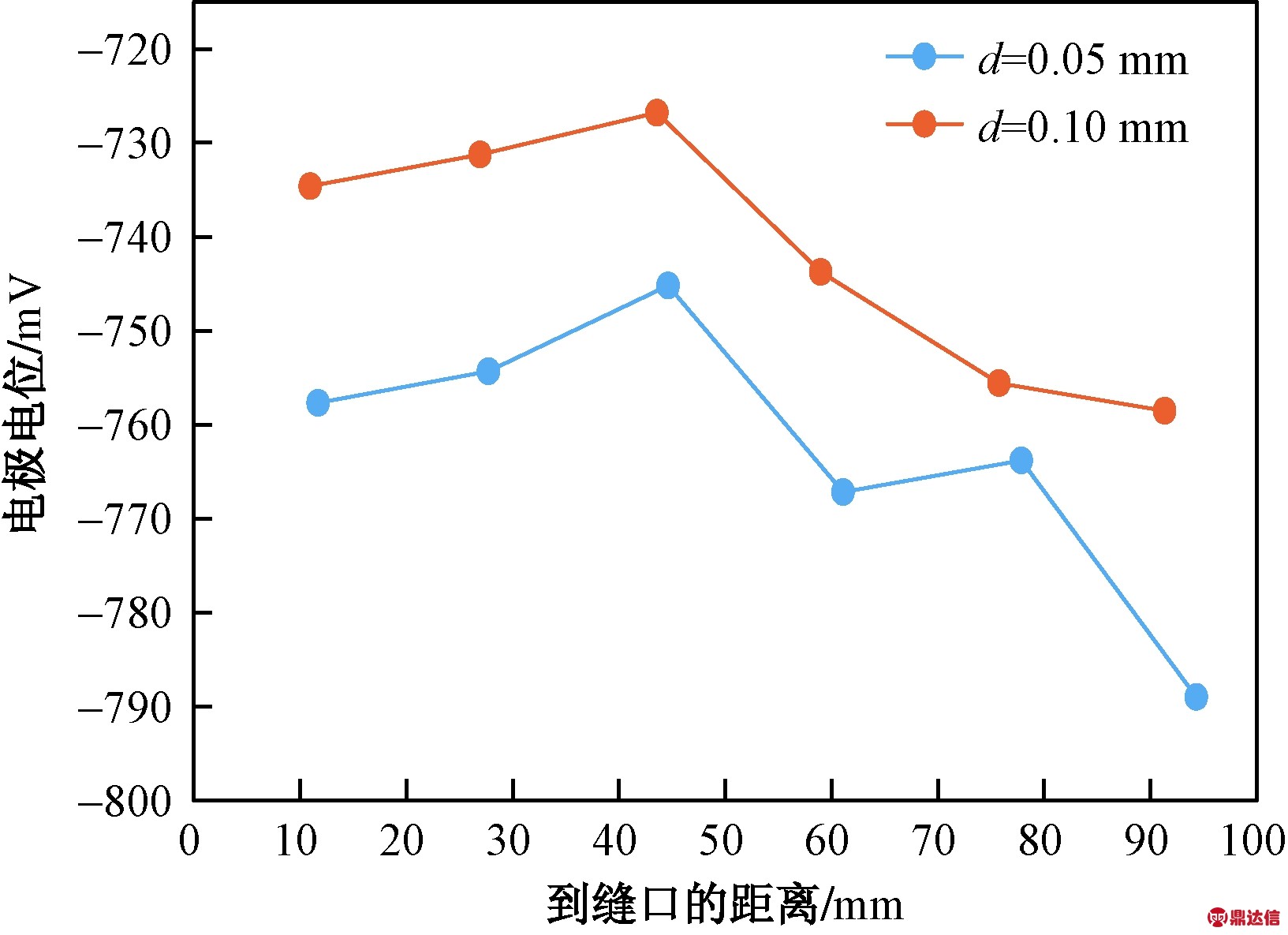
图3 缝口尺寸对缝隙腐蚀的影响[21]
Fig.3 Effect of gap size on crevice corrosion[21]
张钧等[22]通过模拟闭塞电池的方法发现材料缝隙尺寸会对缝隙内临界pH产生影响,缝隙尺寸越小,缝隙内腐蚀介质临界pH越低。Chen等[23]研究了在高温条件下材料发生缝隙腐蚀时,缝隙几何形状对腐蚀行为的影响。研究表明:不同的缝隙宽度会影响缝隙内溶解氧的浓度,并最终影响缝隙内腐蚀产物的形成,缝隙的长度则主要影响缝隙内腐蚀介质的pH。
2 接头螺纹应力腐蚀研究进展
应力腐蚀开裂(stree corrosion cracking,SCC)是指在某种特定的腐蚀介质中,受到一段时间的远低于材料屈服强度的拉伸应力后,材料发生脆性断裂。目前研究认为,应力腐蚀开裂可以分为三个时期,及裂纹孕育期,裂纹扩展期和裂纹断裂期。由于裂纹孕育期的时间过长,导致材料的应力腐蚀开裂现象没有明显的预兆,因而往往造成较为严重的后果。
2.1 应力腐蚀机理
由于材料和腐蚀介质的不同,应力腐蚀产生的原因也十分复杂。不同的研究者根据自身的研究结果提出了相应的应力腐蚀机制,主要的应力腐蚀机制有阳极溶解型和氢致开裂型两种。阳极溶解型应力腐蚀机理认为:在发生应力腐蚀开裂的过程中,金属表面排列的错位处或滑移台阶部位,处于高应变状态下的原子先被溶解形成窄长的孔洞隧道。随着时间的推移,隧道在金属纵向不断延长,在应力作用下,隧道孔洞之间的金属发生机械撕裂,当撕裂停止后隧道仍不断加长,这个过程的持续导致裂纹的扩展,直到金属断裂失效[24]。主流的氢致开裂型应力腐蚀机理包括:氢压理论、氢降低表面能理论、位错输送理论、弱键理论等。每一种理论都是根据实验数据提出的,但没有一种理论能够解释所有的应力腐蚀开裂现象,大多数理论认为,应力能够诱导氢原子在金属基体中扩散并且氢原子倾向于在缺陷处富集,致使局部区域的金属变脆,容易发生脆性断裂[25]。
现阶段,经过长时间对金属材料应力腐蚀开裂的研究发现,无论是阳极溶解型还是氢致开裂型都无法完全解释油井管在各种复杂环境下的应力腐蚀开裂行为,因此现在大部分学者更倾向于是两种机理相互作用的结果。王峰等[26]运用电化学试验与微观分析手段,研究了13Cr油套管钢在注气井环空环境中的应力腐蚀行为,他们认为,13Cr的应力腐蚀是受到阳极溶解和氢致开裂共同作用产生的,阳极溶解为应力腐蚀开裂创造了条件,而氢致开裂导致氢原子向金属内部渗透,降低了金属的材料性能,促进了应力腐蚀开裂的发生。郝文魁等[27]通过慢应变拉伸试验研究了35CrMo钢在H2S溶液中的应力腐蚀性为。研究表明,在pH为5的H2S环境下,35CrMo钢的应力腐蚀机制是以氢脆为主,阳极溶解为辅的协同机制。孙敏等[28]发现材料在不同阳极电位下,对应的应力腐蚀机理各不相同,由此可见,很难用一种应力腐蚀机理去完全解释金属的SCC行为。
2.2 影响应力腐蚀因素
应力腐蚀主要受材料、力学和环境三种因素的影响。如图4所示,这三种因素并不是独立的,而是互相影响的。任何一个因素的变化都会诱导金属材料产生应力腐蚀行为。
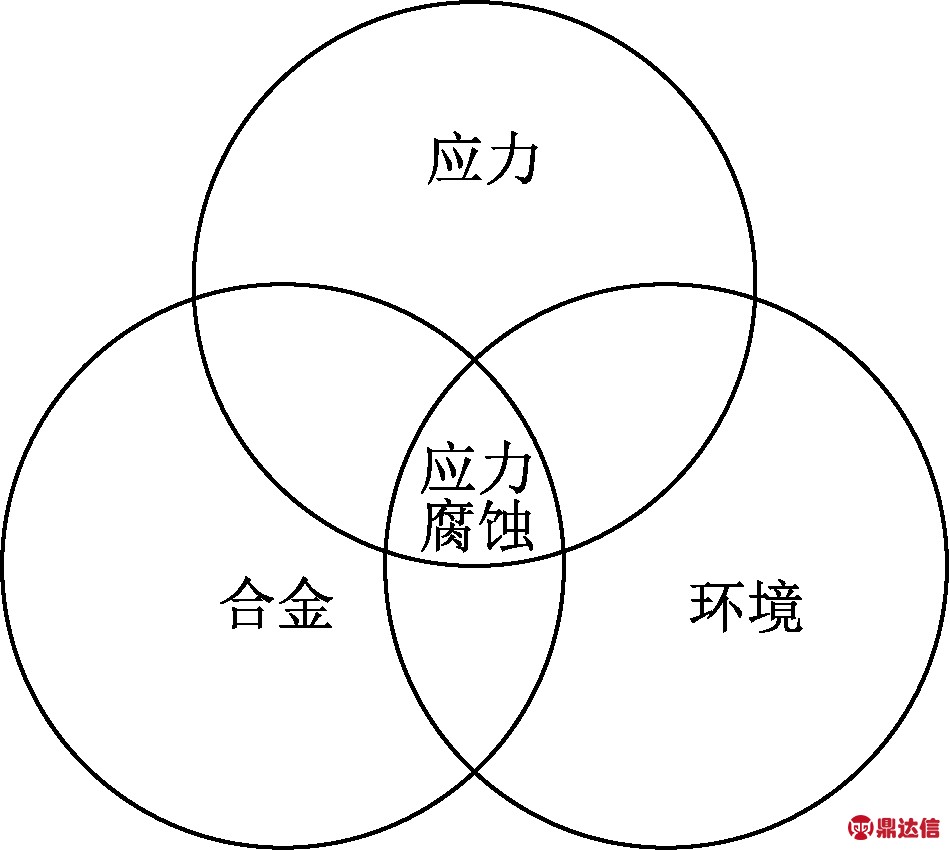
图4 应力腐蚀的影响因素
Fig.4 Influencing factors of stress corrosion
2.2.1 材料因素的影响
从20世纪70年代以来,不同级别强度的油套管均在服役过程中发生过应力腐蚀开裂。对此,中外学者对于材料的应力腐蚀开裂敏感性做了大量研究。国外学者[29-30]研究发现,在合金中添加适当的N、C和Mo能提高金属的腐蚀电位和在钝化电位,显著提高材料的耐应力腐蚀开裂性能。董晓明[31]采用电化学方法,通过对比6种不同成分P110级油套管钢中的氢表观扩散系数,结果如表1所示。发现B3中少量B原子降低了氢原子在钢中的表观扩散系数,提高了钢的抗硫化物应力腐蚀开裂性能;Cr、Mo和V等原子对氢原子在钢中的表观扩散系数影响较小,而B6中Mn原子产生的成分偏析则提高了氢原子在钢中的表观扩散系数。
表1 6种不同成分P110级油套管钢中的氢表观扩散系数[31]
Table 1 Hydrogen diffusion coefficient in P110 oil casing steel with 6 different components[31]

热加工工艺会改变金属的金相组织,不同金相组织表现出不同的应力腐蚀行为[32],还会影响疲劳裂纹的发展方向[33],因此不同的热处理工艺也会对金属的应力腐蚀敏感性有一定影响。易敏等[34]通过对比不同热处理后低碳贝氏体的疲劳性能,发现正火+回火后的热处理后,材料的应力腐蚀敏感性显著降低。
2.2.2 力学因素的影响
外部应力和材料内部残余应力均可以促使应力腐蚀开裂失效,文献[35]通过对比不同油套管螺纹材料发现,随着内部或外部的应力增加,材料无法稳定的发生钝化,应力腐蚀敏感性增加。Ravindranat等[36]通过对L80油井管失效分析研究发现,外加应力改变了材料的物理化学性能,使材料内部晶体产生缺陷,应力在缺陷处集中,从而诱导应力腐蚀开裂的发生。钟彬等[37]通过四点弯曲实验发现弯曲加载使腐蚀坑由点状变为长条状,并聚集成更大的腐蚀坑,增加了材料的应力腐蚀敏感性。李燚周[25]在二氧化碳饱和的腐蚀介质中研究了外加应力对N80碳钢应力腐蚀行为的影响。如图5所示结果表明,外加应力使N80碳钢腐蚀电位负移,加速了金属的溶解过程,随着外加应力的增加,应力腐蚀速率越快。
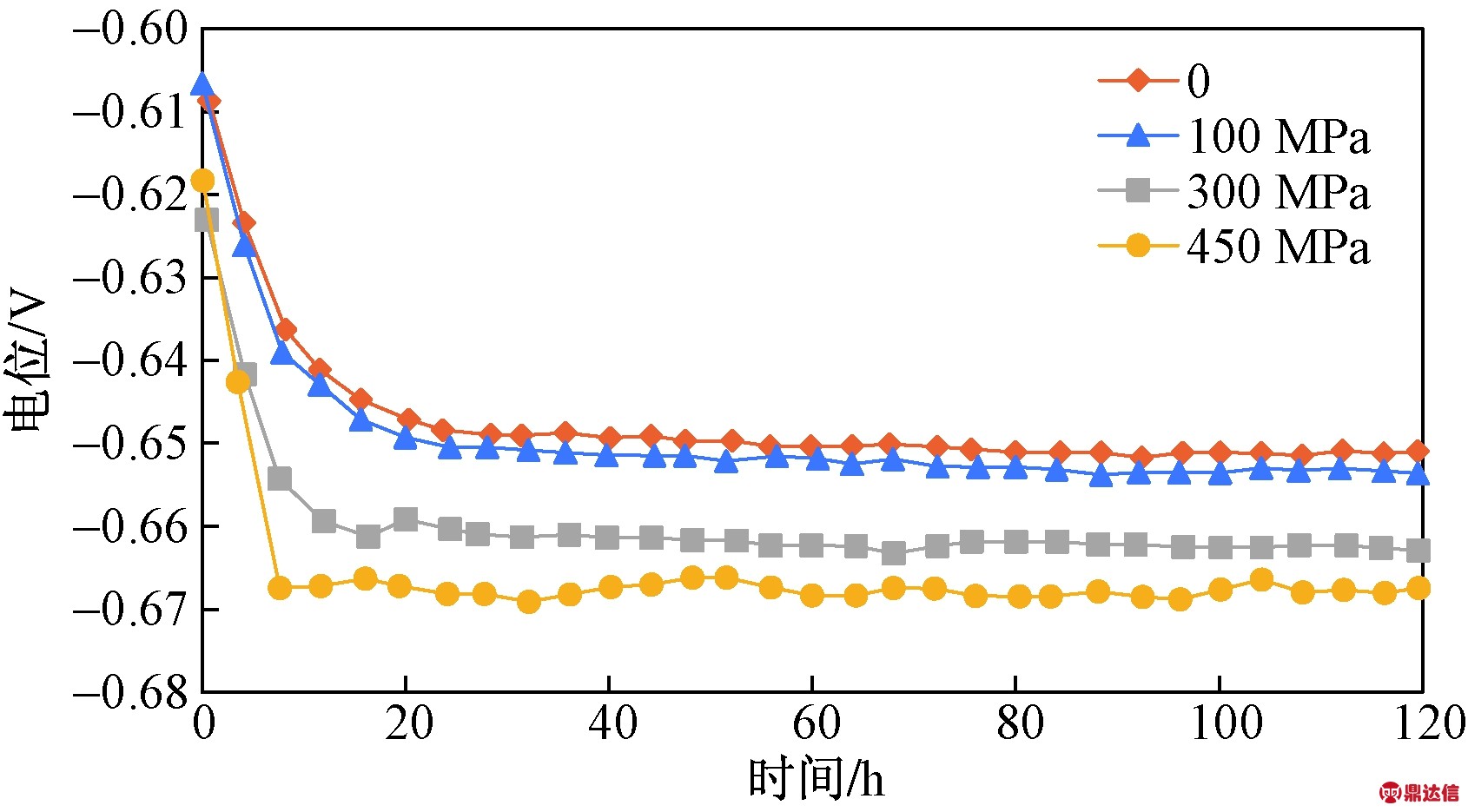
图5 不同外加应力下腐蚀电位的变化[25]
Fig.5 Change of corrosion potential under different applied stress[25]
2.2.3 环境因素的影响
由于油井管的工况是在高温高压极端环境下,所以导致油井管应力腐蚀开裂的环境因素十分复杂。文献[38]认为造成金属应力腐蚀开裂主要和环境中的H2S有关,H2S与金属反应生成物会破坏金属表面钝化膜,H2S分压会加强对钝化膜和腐蚀产物膜的破坏,导致材料的应力腐蚀敏感性增加。Chen[39]认为环境中Cl-浓度对金属的应力腐蚀行为有很大的诱导作用,Cl-会促进金属表面发生点蚀,应力在点蚀附近聚集,为裂纹萌芽的产生创造条件,从而引起金属的应力腐蚀。
刘雪光[40]认为金属抗应力腐蚀开裂性能会随着pH对环境中的氢浓度的影响而产生波动,pH下降,氢含量增加,促使金属发生应力腐蚀开裂。由于环境中pH不同,溶解在水中的H2S解离出的HS-和S2-的百分比不同,它们将影响电化学腐蚀过程腐蚀产物的组成及溶解度,改变腐蚀的反应速率,进而影响材料的抗应力腐蚀性能。艾芳芳等[41]研究了pH对油井管应力腐蚀开裂行为的影响,结果表明,存在pH临界值,油井管的SCC敏感性随着逐渐靠近pH临界值而增加,又在超过临界值后迅速下降。
温度也是影响金属应力腐蚀开裂的重要因素之一,较高的温度会导致金属发生氧化反应,加速应力腐蚀的产生和发展[42],降低油井管的屈服强度[43]。熊茂县等[44]运用应力腐蚀开裂试验研究了钛合金油套管在不同温度下的应力腐蚀开裂,结果如表2所示,随着温度的升高,钛合金的腐蚀速率先减少后增大,说明钛合金套管在高温环境中的抗腐蚀性较差容易发生应力腐蚀开裂。
表2 不同温度下的钛合金腐蚀速率[43]
Table 2 Corrosion rate of titanium alloy at different temperatures[43]
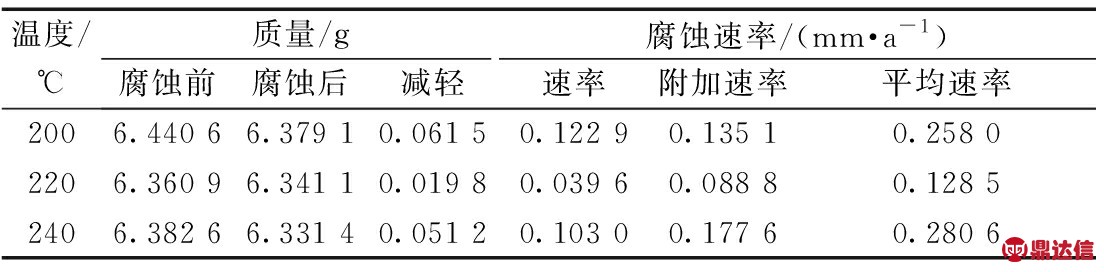
3 接头螺纹CO2/H2S腐蚀研究进展
腐蚀作为油井管失效的主要原因之一,除了缝隙腐蚀、应力腐蚀之外,还有CO2和H2S等气体对油井管造成的腐蚀。CO2作为在开采过程中的伴生气体之一,其溶于水后对金属有较强的腐蚀性,CO2腐蚀的主要腐蚀类型有均匀腐蚀和局部腐蚀。方培林等[2]对某渤海油田油井管腐蚀穿孔原因进行统计归纳。结果表明:CO2腐蚀生成的腐蚀产物是造成油管失效的主要原因。Kahyarian等[45]认为H2S的存在会对油管的CO2腐蚀行为有双重的影响,即当H2S在腐蚀介质中含量较少时,会对CO2腐蚀有抑制作用,但随着H2S含量逐渐增加,CO2腐蚀速率也会逐渐变快。顾洋等[46]研究了油井管钢在不同的回火温度后CO2的腐蚀速率,结果表明,金属的CO2腐蚀速率会随着回火温度的升高而升高。王虎等[47]通过高温高压电化学测试得出,温度的升高会导致CO2腐蚀产物结构发生变化,形成硬度更高,更致密的腐蚀产物膜。谢涛等[48]通过高温高压腐蚀试验研究了不同材质油套管钢的CO2腐蚀行为,结果如图6所示,随着CO2分压的增加,材料的腐蚀速率成逐步上升。
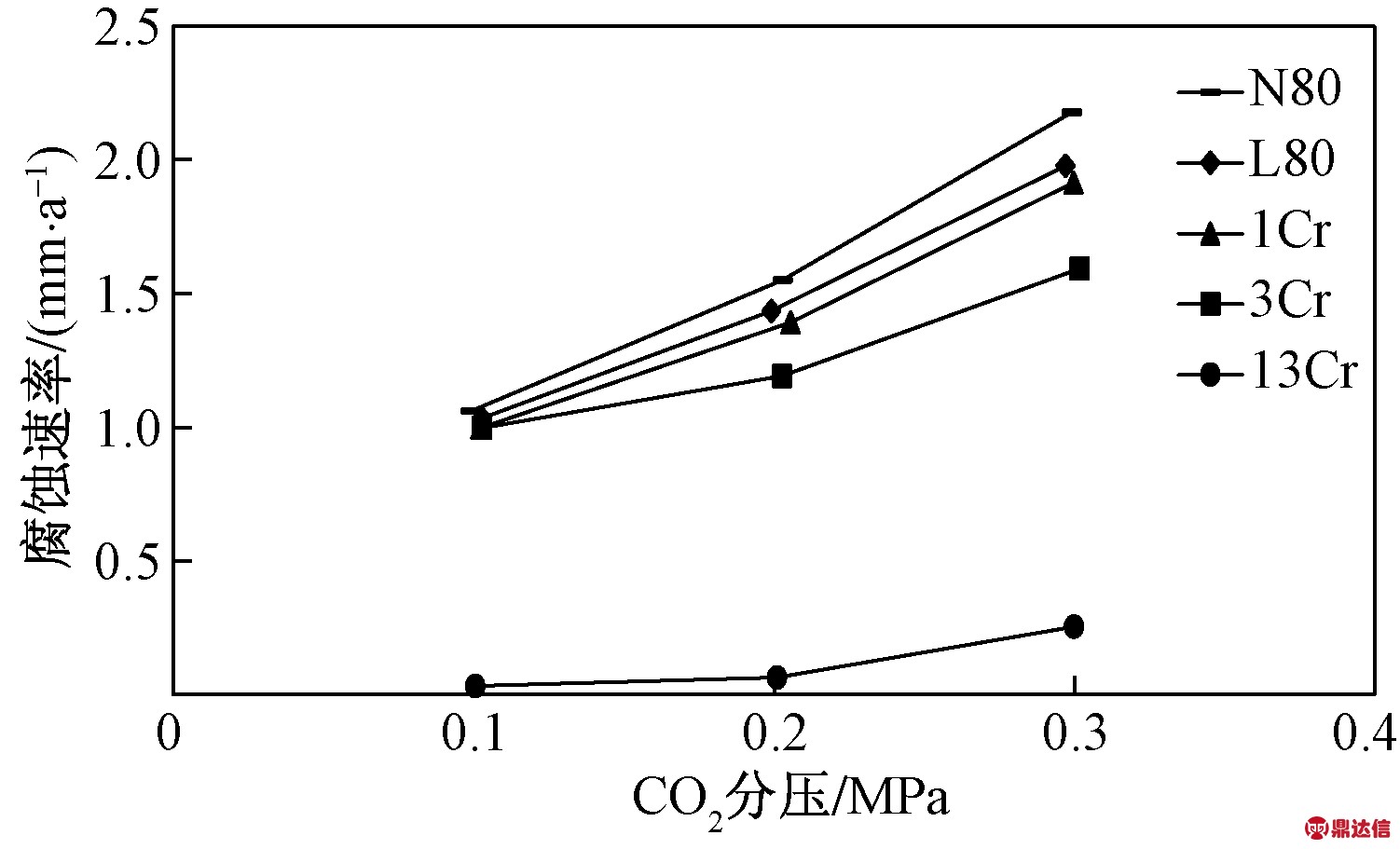
图6 不同材质随CO2分压上升的腐蚀速率变化[47]
Fig.6 Corrosion rate variation of different materials with CO2 partial pressure rising[47]
H2S腐蚀会造成油井管的穿孔,尤其是在接头连接的薄弱处,主要腐蚀形式有电化学腐蚀和应力腐蚀。Zhou等[49]研究了H2S分压对金属腐蚀的影响,结果表明,H2S分压越大,氢原子在金属内活动的越剧烈,增加了金属氢致开裂的可能性。刘艳等[50]通过模拟H2S腐蚀试验,研究碳钢在H2S环境中的腐蚀行为。结果如图7所示,存在H2S浓度临界值,当H2S浓度接近该值时碳钢腐蚀速率最大,超过临界值时碳钢表面覆盖了一层腐蚀产物,腐蚀速率开始下降。
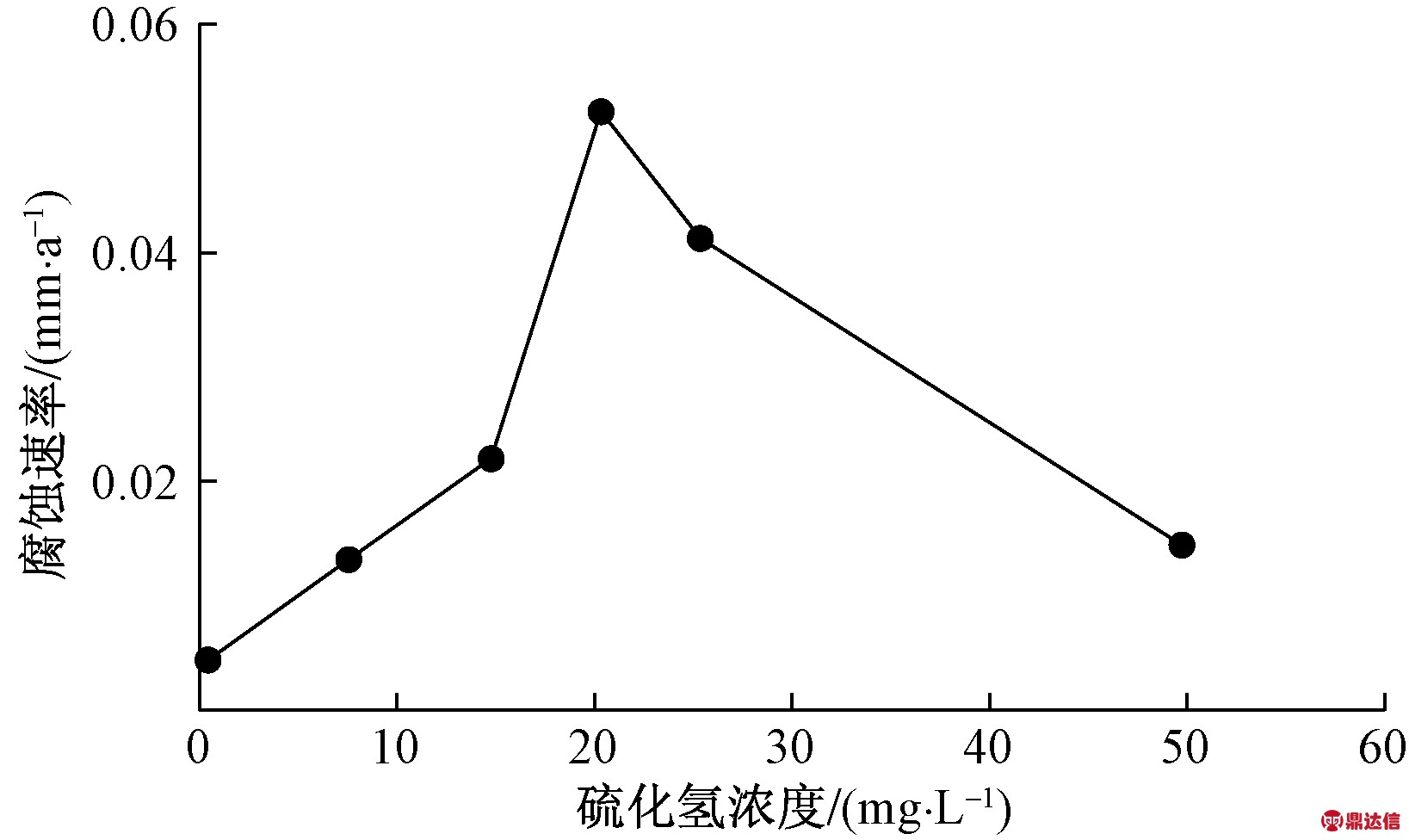
图7 碳钢腐蚀速率与H2S浓度的关系[50]
Fig.7 Relationship between corrosion rate of carbon steel and H2S concentration[50]
如今,随着油田的深入开发,H2S与CO2腐蚀共存情况越来越多。胡丽华等[51]探究了CO2分压对H2S/CO2腐蚀的影响,发现较高CO2分压会降低腐蚀产物膜的稳定性,增加腐蚀速率,并且H2S/CO2分对金属影响较大, H2S/CO2分压较低时,以H2S腐蚀为主,H2S/CO2分压较高时,以CO2腐蚀为主。陆原等[52]发现随着温度的升高,金属的H2S/CO2腐蚀由H2S腐蚀主导转向为CO2腐蚀为主导,因为随着温度升高,CO2腐蚀增加更加显著。范金福等[53]发现当温度在70 ℃时H2S腐蚀和CO2腐蚀的协同效应最为显著,金属表面生成不均匀的腐蚀产物,诱导点蚀的产生。
4 接头螺纹腐蚀防护研究进展
由于缝隙腐蚀是不可避免的,现阶段对于缝隙腐蚀的防护主要从采是合理的设计与施工,在金属中添加微量元素以及涂抹缓蚀剂三个方面展开。在结构设计和加工方面应尽量避免缝隙和表面缺陷,可采用焊接而不是铆接或螺钉连接,最大可能避免在结构方面形成缝隙,为缝隙腐蚀的形成创造条件。如果缝隙无法避免,在材料中添加微量元素也是直接改善缝隙腐蚀的方法。一般来说,合金中Cr、Mo含量较高,则抗缝隙腐蚀性能较好。邹佳男等[54]采用浸泡实验研究了低合金3Cr钢的缝隙腐蚀行为,研究表明,由于3Cr的Cr含量较高,可以形成较为致密,分布均匀的富Cr层,抗缝隙腐蚀性较强。但是相比于Fe,Cr、Mo等都是价值较高的金属,添加这些材料无疑会大大增加成本。而添加缓蚀剂是阻止材料发生缝隙腐蚀既经济又有效的方法。缓蚀剂可以附着在金属外表面,形成保护层,对阻止缝隙腐蚀的发生或蔓延有着重要作用。Yohai等[55]发现碳酸根离子能很好地抑制碳钢在有氯化钠溶液中的腐蚀行为。磷酸根离子能够阻止碳钢的腐蚀电位负移,与金属表面反应形成钝化膜且浓度越高钝化膜的抗腐蚀性越好。Mustafa等[56]发现咪唑啉类型缓蚀剂,能够改善高温环境下X52碳钢的局部腐蚀,并且腐蚀发生的可能性随着缓蚀剂的浓度加大而减小。李玲杰等[57]研究了水溶型、油溶型、油溶水三种类型的缓蚀剂在模拟油田中的缓释作用。研究结果表明,水溶型的缓蚀效果与含水率成正比,油溶型的缓蚀效果与含水率成反比,且缓蚀剂在液体中的剩余质量浓度越高,缓蚀效果越好,但是对于油溶水型的缓蚀效果与含水率的规律并没深入研究,找到相应规律。
因为应力腐蚀是受到环境因素、力学因素和材料因素共同决定的,所以对应力腐蚀的防护从这三个方面展开。在环境方面,刘然克[58]在研究高强度油套管刚时发现提高缓蚀剂用量、降低硫化物含量或增加环空液pH能够推迟或抑制应力腐蚀的发生。此外,脱硫剂也可以降低应力腐蚀发生的可能性,但在缓蚀剂和脱硫剂的共同作用下,脱硫剂浓度过高可能会起加剧应力腐蚀的蔓延。Chen等[59]通过研究炔丙醇(PA)对13Cr不锈钢的应力腐蚀开裂抑制情况发现,低浓度PA促进了13Cr钢的氢渗透,加速了应力腐蚀开裂,高浓度的PA可以在材料表面形成保护膜,有效抑制应力腐蚀。孟选刚等[60]通过失重法实验表明通过聚合成膜机理研制的新型缓蚀剂能够有效减小高温情况下酸性腐蚀介质对13Cr产生的应力腐蚀。在力学方面,黄惠茹等[61]通过剥层法明确了材料硬度和残余应力间的定量关系,为残余应力诱导应力腐蚀的研究提供了基础。练章华等[62]基于弹塑性力学的基础上建立了油井管在复杂力学环境中的力学模型,表明可以通过减少产量,优化伸缩管结构,加扶正器改善复杂力学环境下油井管的力学损伤。刘奔等[63]通过建立油井管螺纹的有限元模型,明确了螺纹面和锥面的力学关系,为油井管螺纹密封面的设计提供了基础。在材料方面,尽量使用含Ni、Cr、Mo、的金属,可大幅度提升金属的抗应力腐蚀能力。Cheng等[64]通过研究Sr含量对金属腐蚀性的影响发现,当Sr含量为0.2%时,金属的机械性能和耐腐蚀性因晶粒细化而大幅度增加,当Sr含量继续增加,会产生更多金属化合物,造成金属的机械性能和耐腐蚀性大幅度降低。
针对H2S/CO2对金属的腐蚀,龚宁等[65]在De.Waard[66]预测不同材料腐蚀速率的基础上,针对CO2的腐蚀环境,提出了一套油井管材优选方法。该方法能在保证油井管在CO2浓度较高环境中安全工作的前提下,降低油井管使用成本,保证其经济性。吴奇兵等[67]在面对CO2腐蚀导致油井管强度降低的问题时,计算了不同条件下油管的腐蚀速率,建立腐蚀产生后油管强度计算方法,并对油管的剩余服役寿命进行了预测,使油井管的生产安全得到保障。
艾志久等[68]综述了H2S对油气管材腐蚀的机理,介绍了环境、Cl-浓度和管材材料等因素对H2S腐蚀的影响,并且评价了电化学防护、缓蚀剂防护和涂镀层防护三种防止H2S腐蚀的方法,他指出缓蚀剂防护工艺比较经济,但对油气的生产有较大的影响,涂层防护工艺操作简单,对油气生产影响不大。为后续的H2S腐蚀防护研究奠定了基础。李锡伟[69]通过对比发现吡啶类缓蚀剂能够有效抑制金属的H2S/CO2的协同腐蚀。陆原等[70]通过丙炔醇改善硫脲咪唑啉类缓蚀剂的吸附能力,使其对抗H2S/CO2腐蚀能力有了显著提升。万里平等[71]通过对现有的缓蚀剂进行复配,通过电化学测试表明复配缓蚀剂对H2S/CO2协同腐蚀具有较好的缓蚀作用。
5 接头螺纹腐蚀与防护技术研究展望
近年来随着高温、高压、高腐蚀环境的油气田不断深入开发,油井管所面临的环境和受力情况越来越复杂,油井管腐蚀失效问题愈加突出,尤其是连接油井管的接头螺纹处。在油气井实际生产过程中,油井管接箍和油管之间因存在微小缝隙会导致腐蚀性介质渗入,极易在螺纹连接位置出发生严重的缝隙腐蚀。与此同时,接头螺纹在井下受到复杂应力的作用,应力将会与腐蚀介质产生协同作用,导致应力腐蚀的发生,因此,接头螺纹部位经常在应力和缝隙的耦合作用下发生严重的腐蚀失效问题。但目前研究气井管柱腐蚀力学问题时,通常是将应力腐蚀和缝隙腐蚀分别考虑,特别是实验测试中对于应力腐蚀和缝隙腐蚀两种因素的耦合作用下的金属腐蚀行为,以及应力和缝隙之间的相互影响规律尚不清楚。因此,未来对于油井管接头螺纹腐蚀防护的研究可以从这几个方面进行。
(1)设计应力和缝隙耦合作用下原位电化学测试装置,运用电化学测试技术和表面分析技术分析模拟气井环境中接头螺纹在应力和缝隙耦合作用下的腐蚀行为,讨论应力和缝隙对油井管接头螺纹腐蚀的协同效应。
(2) 探究油井管螺纹接头在协同腐蚀下的腐蚀过程和相应的腐蚀机理,分析影响协同腐蚀的主要影响因素,明确协同腐蚀过程中应力与缝隙两种腐蚀的对螺纹接头影响的主次地位。
(3)油井管接头密封接触面的接触压力除了防粘连和表面机械损伤外,还应考虑其他应力的影响,避免应力腐蚀的产生。针对应力诱导接头密封面的腐蚀行为,提出密封面腐蚀许用接触应力的概念和算法,研究减少缝隙和应力耦合腐蚀对螺纹密封面影响的表面工程技术,优化密封面结构,提高螺纹接头的防腐和密封性能,保障井筒完整性,降低油气田事故的发生。