摘要:针对90℃左右的高炉冲渣水有机朗肯循环(ORC)发电系统,建立了R245fa在波纹板式冷凝器中的冷凝传热数值模型,并验证了模型的正确性。借助冷凝传热数值模型,探讨了蒸汽过热度、壁面过冷度、蒸汽干度对传热系数、压降和综合传热性能的影响,拟合了适用于以R245fa为工质的ORC发电系统中波纹板式冷凝器的传热关联式。针对冷凝器冷凝液相体积分数沿板长方向的变化情况,探讨了冷凝器中间排液的可能性,并就液相体积分数给出了合适的中间排液范围。
关键词:有机朗肯循环(ORC)波纹板;冷凝器;高炉冲渣水;传热数值模型;传热关联式;中间排液
高炉炼铁产生的高温炉渣是冶金过程中最主要的废弃物,每生产1吨铁产生约300 kg、1 400℃以上的高温炉渣[1],对高温炉渣采用水冲刷将会产生大量70~90℃的高炉冲渣水。目前对于高炉冲渣水这种低温余热源,普遍的方法是自然降温或利用其显热传热进行供暖或洗浴,但采暖和洗浴有时间应用上的限制。因此,国内外科技工作者针对高炉冲渣水余热进行了有机朗肯循环(ORC)发电的研究[2-3],这种低温余热利用技术是用有机工质代替水进行有机朗肯循环,工质沸点低,能较好地在低温余热中吸收热量,然后相变为蒸汽进入膨胀机做功,膨胀机再带动发电机发电,乏汽进入冷凝器成为低温液体[4]。
应用在ORC发电系统上的换热器通常为管壳式。由于高炉冲渣水ORC发电系统中的有机工质在冷凝过程中传热温差偏小,汽化潜热也相对较小,因此需要选择较大的传热面积,这增加了投资更影响了传热性能。采用紧凑的板式冷凝器是ORC发电系统的重要方向。刘克涛[5]对ORC发电系统中管壳式和板式蒸发器进行了实验,对于高炉冲渣水这种低于100℃的低温热源,板式最大传热系数是管壳式的1.6倍且压降要优于管壳式。段钱胜等[6]指出,温度小于260℃、压力小于2.5 MPa、介质干净的情况下,ORC发电系统中应使用板式冷凝器。Zhang等[7]对ORC发电系统中不同换热器的经济性进行研究,发现翅片管束蒸发器和板式冷凝器搭配使用时电力生产成本和投资回报时间都显著低于蒸发器和冷凝器都使用管壳式换热器的情况。Chen等[8]将R245fa作为有机工质并使用板式蒸发器及冷凝器,采用5 kW轴流式透平,当蒸发温度高于一定值时,能产生高于自身耗电的电能。目前的研究针对板式换热器单相传热较多,而两相传热较少[9]。
ORC发电系统工质的选择至关重要[10]。Bianchi等[11]比较了R134a、R245fa、苯和异丁烷后指出,虽然R245fa在单位质量流量流体做功方面不如苯和异丁烷,但R245fa更安全且循环效率好于R134a。谢攀[12]基于可用势分析方法和热力学第一定律得出,R245fa性能相对其他有机工质更优越。
针对高炉冲渣水ORC发电系统中的波纹板式冷凝器建立了冷凝传热数值模型,并通过实验验证了模型的合理性。针对有机工质R245fa在波纹板中的流动和传热特性,提出了中间排液区间概念,这对合理利用波纹板式冷凝器、降低冷凝器的压差、提升整个高炉冲渣水ORC发电系统余热回收性能具有重要意义。
1 波纹板式冷凝器模型的建立
1.1 波纹板式冷凝器的物理模型
波纹板式冷凝器芯体物理模型如图1所示。换热芯体由波纹板片波峰对波峰、波谷对波谷堆叠而成,波纹板片上的小凸起在板片之间起到支撑作用。冷凝器中有机工质R245fa和冷却水呈逆流布置,均通过芯体一侧半边的进口分配到整个板间。
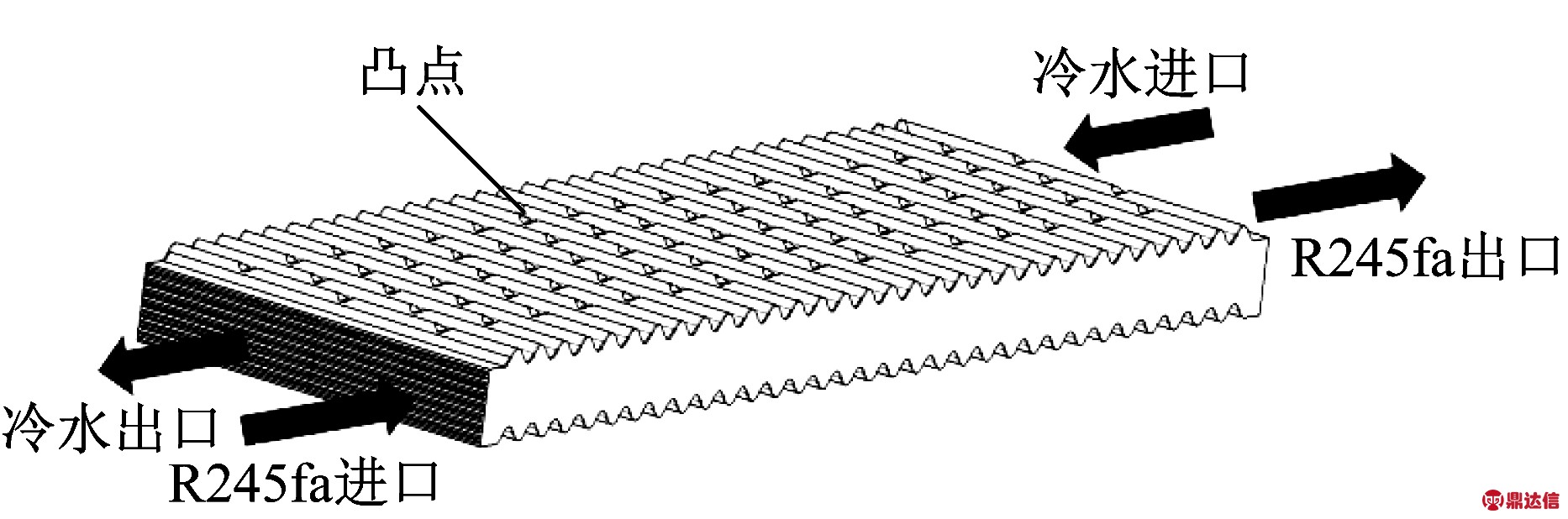
图1 波纹板式冷凝器芯体结构
Fig.1 Core structure of corrugated plate condenser
1.2 数学模型的建立
为建立有效的模型,结合波纹板式冷凝器的流动和传热特点,作出如下假设:①通道内流体是不可压缩的牛顿流体;②气相和液相热力平衡,气相和液相具有相同的饱和压力和温度;③热辐射可以忽略不计;④忽略外界空气与波纹板外侧壁面的对流传热,即接触空气的波纹板的固体表面与周围环境绝热;⑤换热器边界条件和外部环境可忽略不计;⑥通道中冷热流体的流量分布均匀;⑦忽略波纹板传热表面结垢的影响。为简化计算,选取一组换热单元冷热通道进行分析,几何尺寸、材料物性如表1和表2所示。使用Fluent软件进行相变模拟,但冷侧板间通道仅为单相水,故分别对冷热通道进行两相流和单向流模拟。
表1 波纹板尺寸
Tab.1 Size of corrugated plate
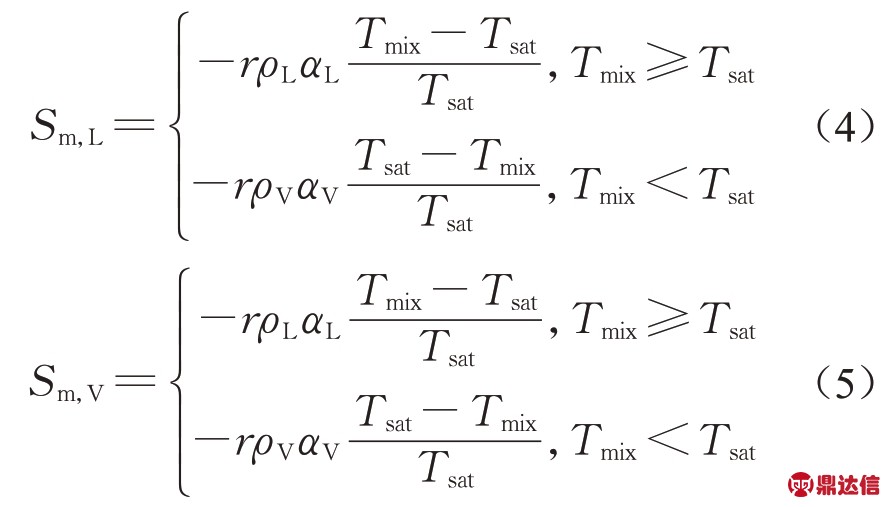
表2 材料物性
Tab.2 Physical parameters of material

流体在波纹板中流动受到波纹和凸点的扰动,故流体域的流态为湍流。控制方程包括流体的连续性方程、能量方程、动量方程以及板片的导热微分方程。采用RNG k-ε模型,RNG k-ε模型在ε方程中增加了一个附加项,对流场精度更高,并考虑了旋转效应,故能够模拟分离流、二次流,解决了流线弯曲程度较大及应变率较高的流动。对于板式换热器内的复杂流动和传热特点,具有相对较高的准确度[13]。对于不可压缩无内热源的流体,RNG k-ε方程[14]如下所示:
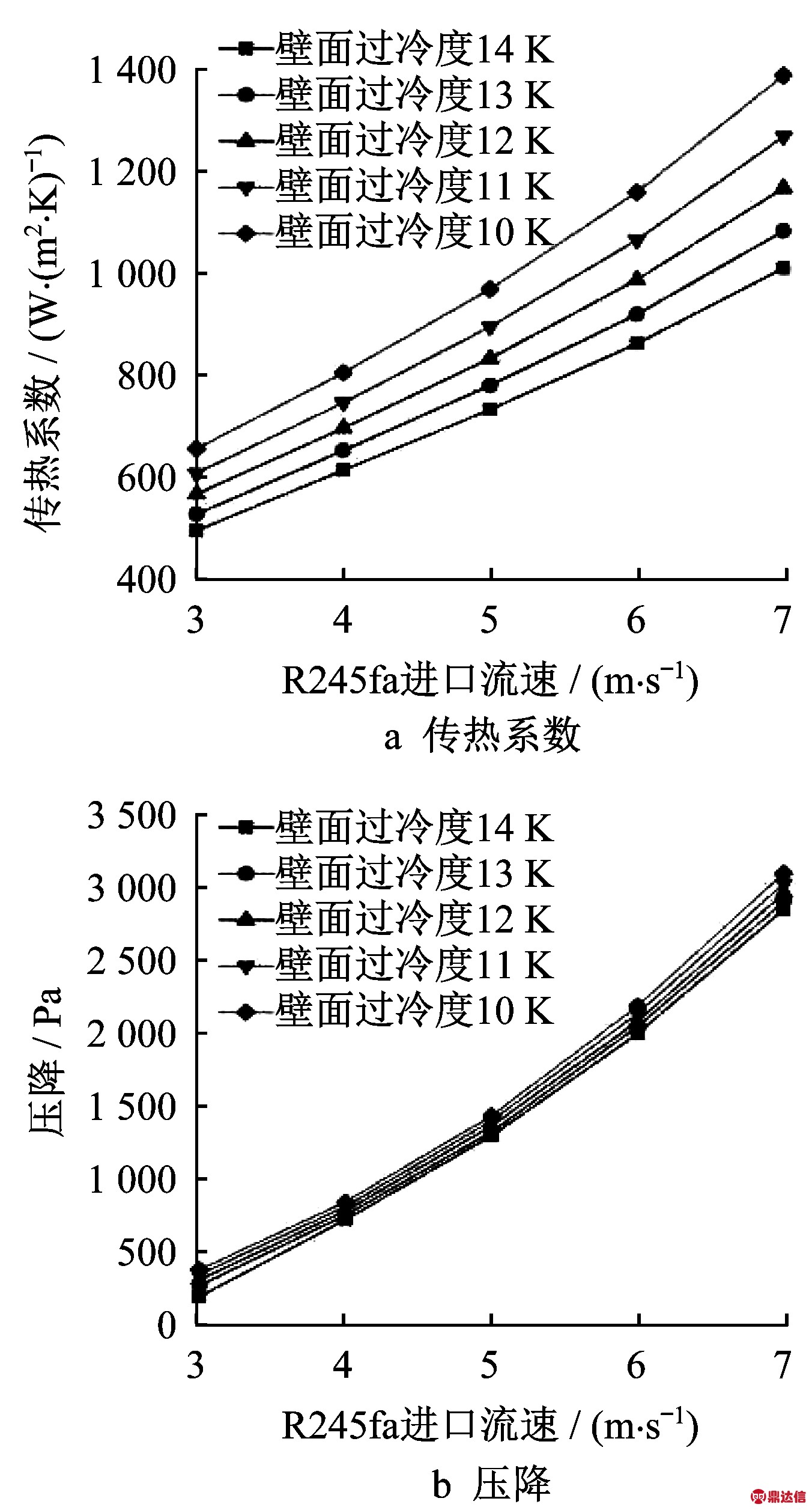
式中:t为时间,s;ρ为密度,kg·m-3;ui为流体在x方向上的流速,m·s-1;ε为脉动耗散率,m2·s-3;k为湍流动能,m2·s-2;Gk为由层流速度梯度产生的湍流动能,kg·(m·s3)-1;G b为由浮力产生的湍流动能,kg·(m·s3)-1;μeff=μ+μt,Pa·s,其中μ为流体黏度,μt为 湍 流 黏 度;C1ε、C2ε、C3ε为经验常 数,C1ε=1.42,C2ε=1.68,C3ε=1.72;αk、αε分别为k方程和ε方程的湍流Pr数,αk=αε=1.39。
对于不可压缩无内热源的流体,连续性方程、动量方程和能量方程如下所示:

式中:Γ为广义扩散系数;φ为广义变量,在动量方程和能量方程中分别代表速度ui、uj、uk和温度T,连续性方程中φ的值为1。
相变传热的模拟难点是两相界面的传热传质问题。本研究中采用蒸发和冷凝的简化模型——Lee模型[15],该模型中冷凝和蒸发时非饱和相温度和饱和相温度的差是相变的主要推动力,相变速率和温度的差值成一定比例。假设两相界面为饱和温度,若气相温度低于饱和温度,气相向液相传质传热,若气相温度高于饱和温度,则液相向气相传质传热,其形式如下所示:
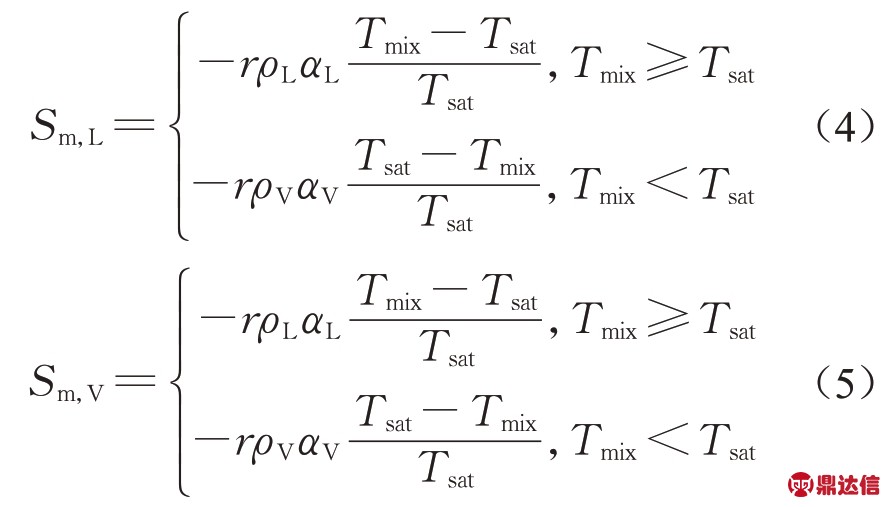

式中:r为控制相变发生率的经验系数,s-1;αL、αV分别为液相和气相的体积分数;T mi x、T sat分别为工质温度与饱和温度,K;L为相变潜热,J·kg-1;S m,L为连续性方程中的质量源项,表示液相对气相的质量传递,kg·(m3·s)-1;S m,V为气相对液相的质量传递,kg·(m3·s)-1;S e为能量方程中的能量源项,J·(m3·s)-1。
采用Mixture模型,将冷凝传热过程质量与能量传递源项UDF进行编译后导入Fluent软件,对UDF进行编译。通过查询物性,将R245fa、液态水和不锈钢加入Fluent软件。主项设置为蒸汽,第二项设置为液体,液滴最小直径为10-6 m。在Cell Zone Condition选项中的Source Terms选项卡添加UDF定义过的气液两项质量源项。在混合项中同样选中Source Terms选项卡添加UDF定义过的能量源项。
1.3 边界条件及网格
模拟工况为:R245fa蒸汽进口速度为3~7 m·s-1,进口温度为303~319 K,板壁温度为289~293 K,湍动强度为5%,水力直径为3.902 mm,换热器材料为不锈钢板材304。进口边界为速度进口,出口边界为压力出口,湍流指定方法为回流湍流强度和回流水力直径;内部壁面恒温,外部壁面绝热。为判定蒸汽冷凝的稳定状态,对出口截面的质量流量和体积分数进行检测。采用双精度、压力基求解器以及时间为非稳态的计算方法,沿工质流动方向考虑重力,压力耦合方案采用压力耦合方程组的半隐式算法(SIMPLE算法)。为使计算结果收敛,除volume fraction采用一阶差分外,其余使用二阶差分。松弛因子和残差保持默认,开启残差监视器。单个换热通道示意图如图2所示。
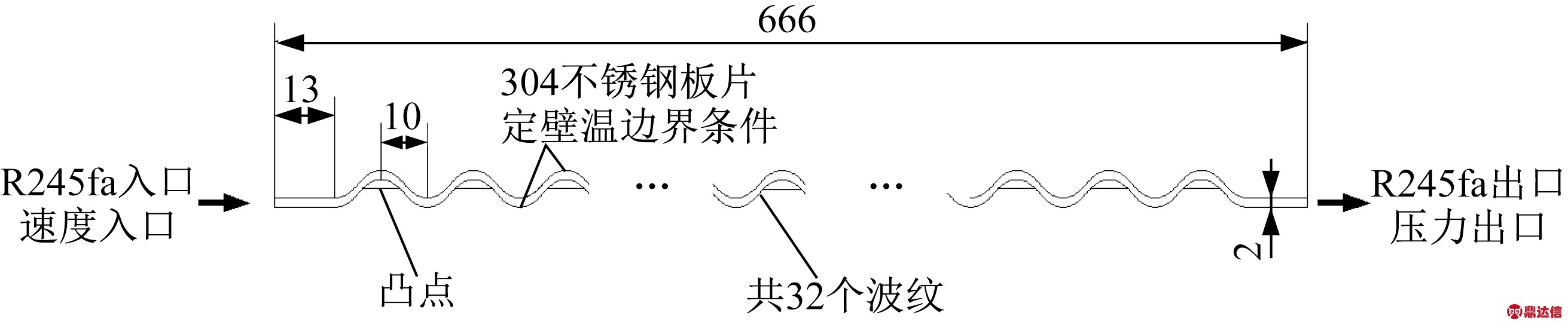
图2 单个换热通道示意图(单位:mm)
Fig.2 Schematic diagram of single heat transfer channel(unit:mm)
采用网格划分软件GAMBIT默认的六面体网格,选取蒸汽进口速度为3.73 m·s-1、蒸汽进口温度为310 K,设置板壁温度为293 K,工作压力为R245fa在饱和温度303 K时的冷凝压力;在模拟计算中,把工质温度沿板长方向变化作为网格独立性检验的检验变量。不同网格尺寸下工质沿板长的变化如图3所示。当网格尺寸为1.0 mm时,板上各点温差很小,故所有数值模拟网格尺寸为1.0 mm。
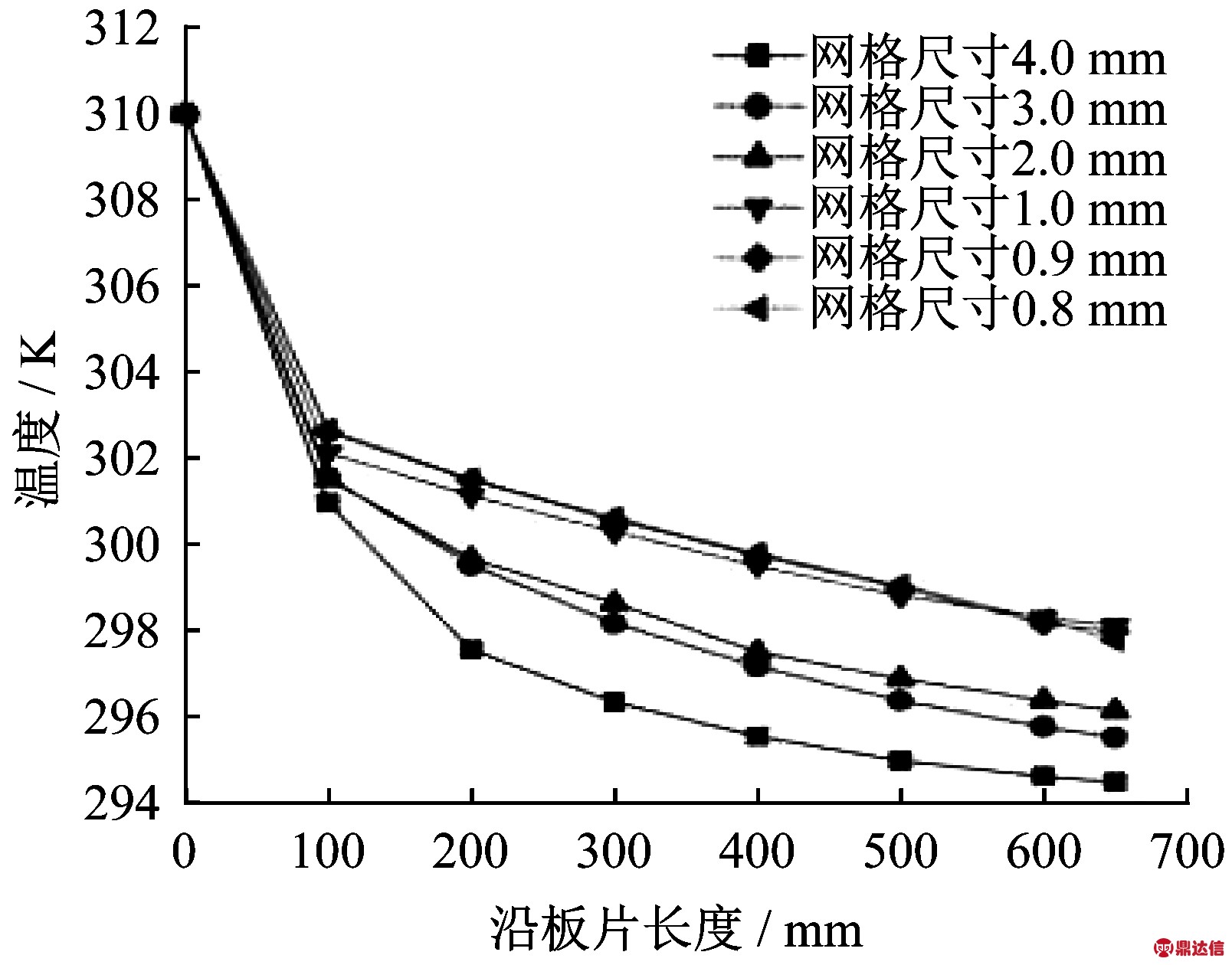
图3 不同网格尺寸下工质温度沿板长的变化
Fig.3 Temperature of working medium along plate length under different mesh sizes
2 波纹板式冷凝器模型的实验验证
ORC发电系统实验平台示意图如图4所示。实验系统由热源回路、有机工质回路和冷源回路三部分组成。热源回路模拟高炉冲渣水,通过热水泵向板式蒸发器提供90℃左右的热水来加热蒸发器中有机工质;有机工质回路搭建了一个简易的高炉冲渣水余热回收发电系统,即有机工质R245fa受热相变后进入膨胀机做功,经测功仪测得输出功率在39.65~46.65 kW波动,然后经过油气分离进入波纹板式冷凝器冷凝;冷源回路通过冷却水带走有机工质的热量。
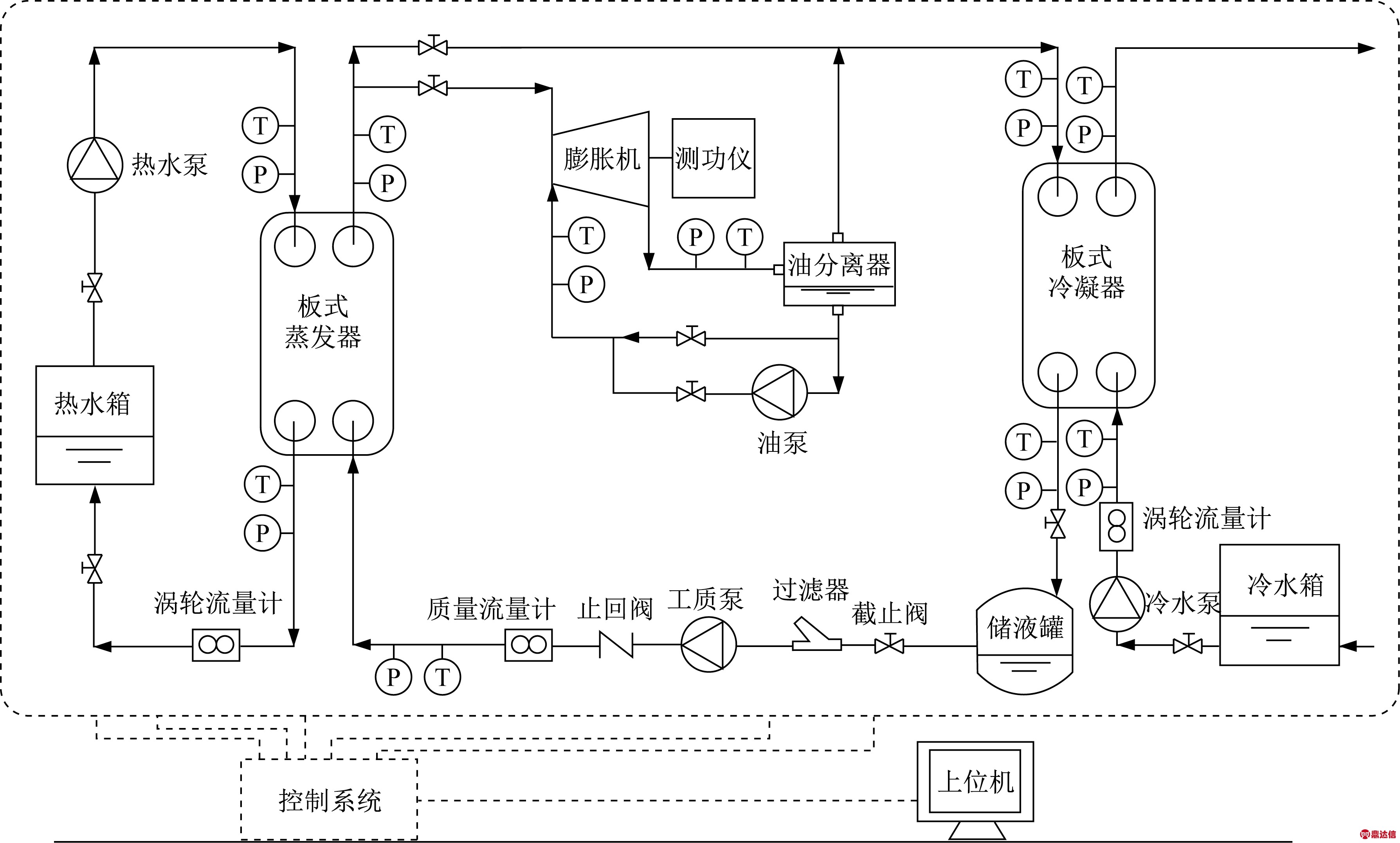
图4 实验平台示意图
Fig.4 Schematic diagram of experimental platform
获得的原始数据如表3所示。将冷凝器出口温度的实验值和模拟值进行对比,结果如图5所示。平均绝对误差(MAE)计算式如下所示:
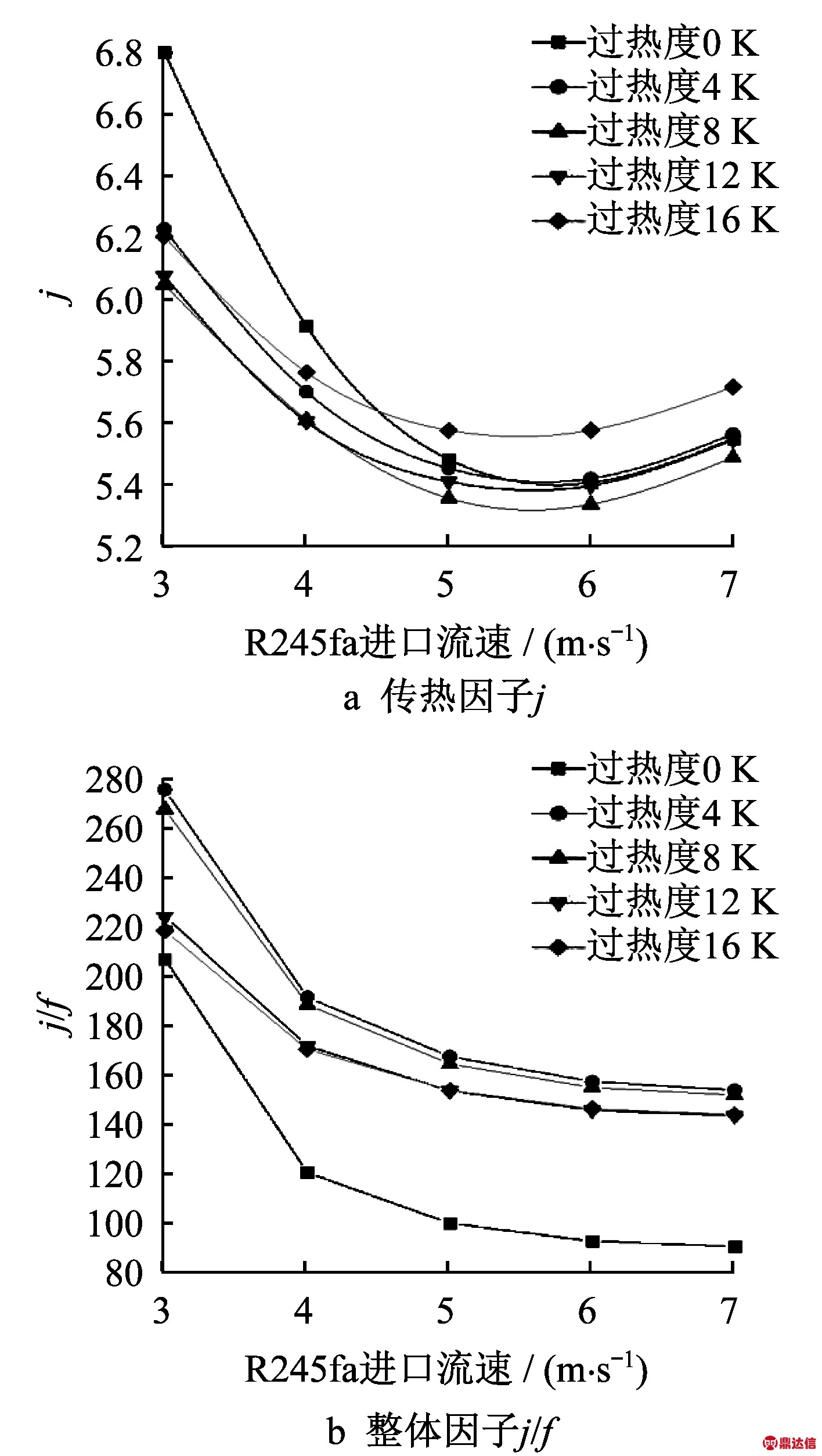
图5 冷凝器出口温度实验和模拟结果平均绝对误差分析
Fig.5 Mean absolute error analysis of experimental and simulation results for outlet temperature of condenser

式中:X exp为实验值;X sim为模拟值。根据式(7)得到r MAE的值为13.97%。对表3中工况1蒸汽侧压降较低的情况,发现平均绝对误差低于平均值,故对于蒸汽侧压降较低的情况模拟结果将更加精确。因此,认为数值模拟的结果是可信的。
表3 波纹板式冷凝器实验数据
Tab.3 Experimental data of corrugated plate condenser
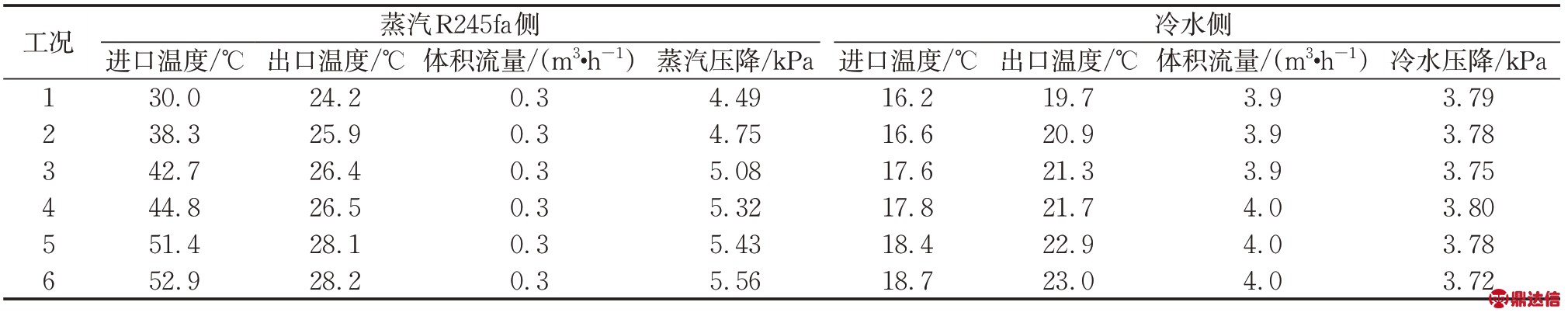
3 波纹板式冷凝器传热特性讨论
本节中讨论进口过热度、进口干度以及壁面温度对波纹板式冷凝器传热系数和压降的综合影响。
3.1 蒸汽进口过热度对传热系数和压降的影响
将蒸汽进口流速设置为3~7 m·s-1,蒸气进口温度设置为303~319 K,相应的过热度设置为0~16 K,并修改流体相应的物性参数,计算结果如图6所示。
由图6可见,过热度越高传热系数越小。过热度高时蒸汽的冷凝分为过热、相变、过冷三段,即总传热温差变大,但冷却水所能提供的传热量是固定的。从传热机理看,过热工质为汽水传热,传热系数较低,将大大降低总传热系数。对同一过热度,蒸汽流速越高,蒸汽扰动和剪切的作用越大,冷凝液膜越不容易形成,因此传热系数也变大[16]。压降随过热度升高而增大,是因为蒸汽温度的升高降低了工质密度,工质在板内的流速变大,流速变大又增大了摩擦系数,因此摩擦导致的压降变大,增大总压降。
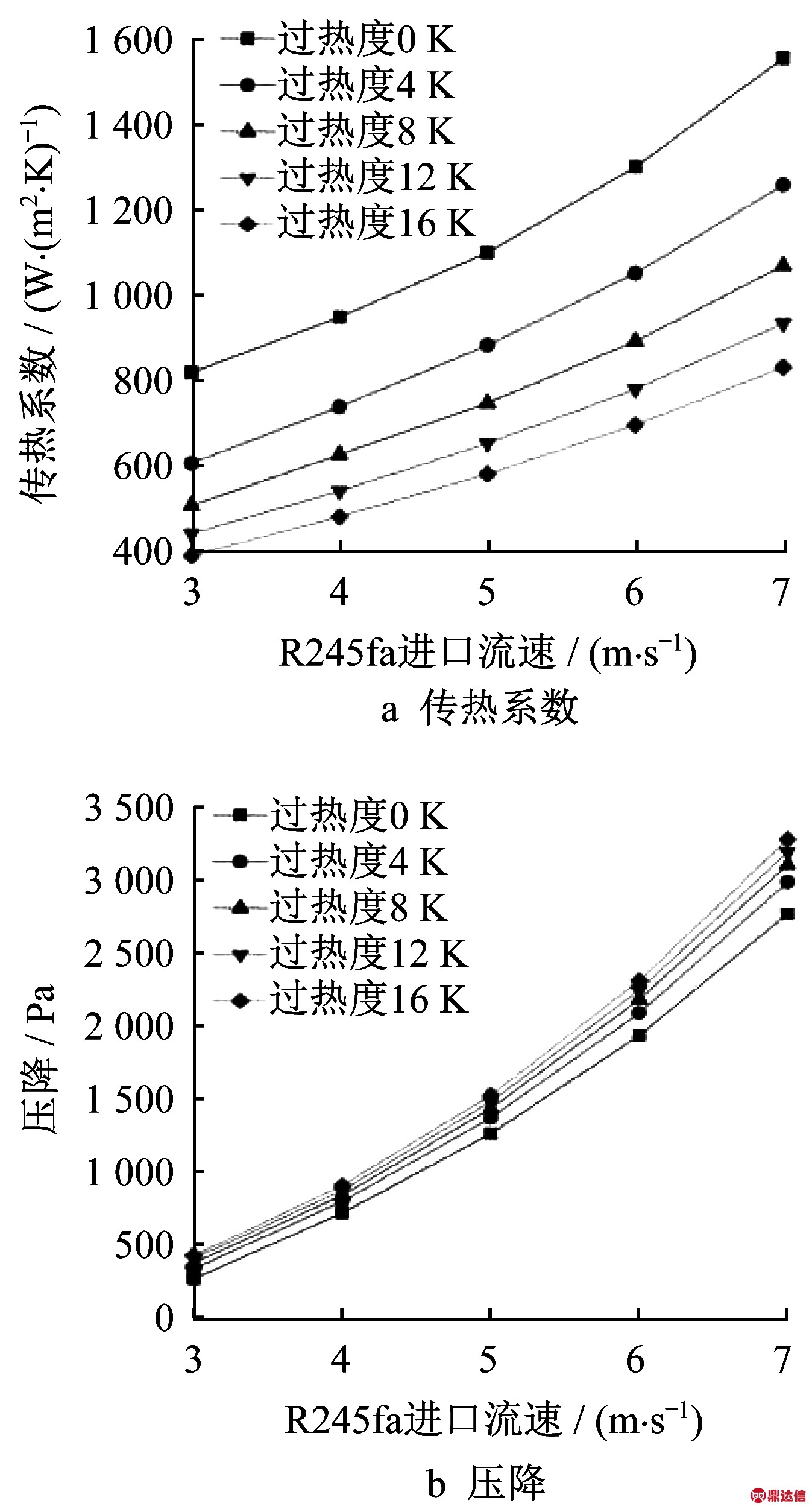
图6 不同过热度下传热系数和压降随进口流速的变化
Fig.6 Variation of heat transfer coefficient and pressure drop with inlet velocity at different overheats
传热系数和压降是换热器评价最重要的指标,对于换热器而言,研究者希望有较好传热效果的同时阻力不应过大,往往两者并不呈现正相关关系,因此需要一个综合评价指标兼顾传热特性与流动阻力。采用j-f因子分析法(j为传热因子,f为阻力因子[17])来评价比较直观,j/f的值越大,换热器的综合传热性能就越强[18-20],计算式如下所示:
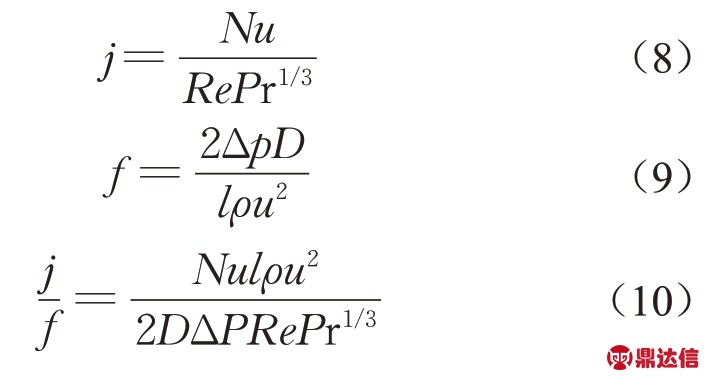
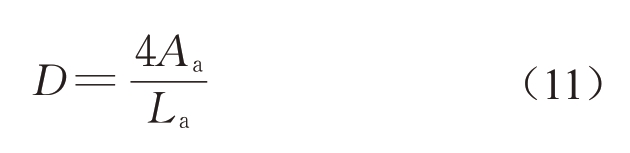
式中:Nu为努塞尔数;Re为雷诺数,其中特征长度取式(11)中的当量直径D,m;Pr为普朗特数;ΔP为换热器进出口两端的压降,Pa;ρ为密度,kg·m-3;u为速度,m·s-1;l为流动通道长度,m;A a为单层空气流道进口面积,本研究对波纹板式冷凝器单个板片进行模拟,其流道进口面积为2 mm×80 mm;L a为单层空气流道进口总周长,本研究中单个板片流道进口总周长为2×(2 mm+80 mm)。不同过热度下传热因子与整体因子随进口流速变化如图7所示。
如图7a所示,j随进口流速的增大呈现先减小后增大的趋势,制冷剂在板束通道内的进口方式为半侧进口,进口流速不断增大导致进口处回流加剧,使得进口处的冷凝量增加,液膜在板片进口处变得更厚,因此在3~5 m·s-1流速状态时,板片的传热效果随着进口流速的增大而降低。然而,进口流速继续增大对径向速度的影响更大,动量交换更加剧烈,液膜急速减薄,从而降低了传热热阻,增强了传热,提升了传热效果[21]。
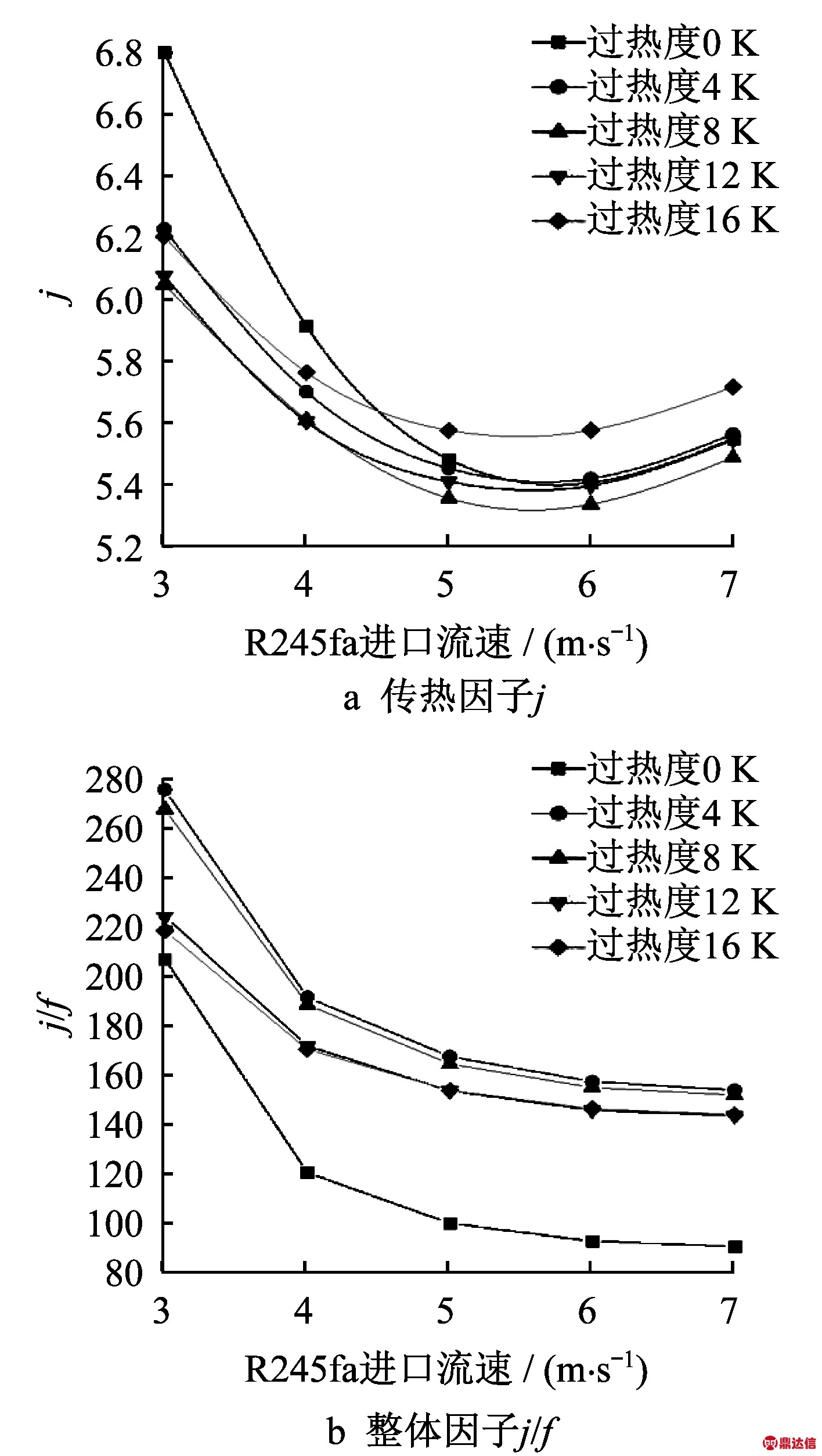
图7 不同过热度下传热因子和整体因子随进口流速的变化
Fig.7 Variation of heat transfer factor and overall factor with inlet velocity at different superheats
由图7b可见,相同过热度下,工质侧j/f在3~7 m·s-1时随着流速的增大先急剧减小后趋于不变。在3~5 m·s-1内j/f随着j的急剧下降而急剧下降,在5~7 m·s-1内j/f趋于不变是由于f在此范围内逐渐增大,抵消了j在此范围内的增加,使j/f趋于不变。在同一流速下,工质过热度的增加降低了工质侧的传热效果,并且当过热度为4 K以上时,工质侧随着过热度的减小,j/f增大,综合传热效果逐步增强;过热度在0 K时,j/f在各种流速工况下都达到最低值,传热效果弱于其他工况,而过热度在4 K时工质R245fa侧传热效果最佳。从综合传热效果来看,并非过热度越高传热效果越好。在该过热度变工况模拟中,当流速为3 m·s-1、过热度为4 K时,传热效果达到最佳状态。
3.2 壁面过冷度对传热系数和压降的影响
将蒸汽流速设置为3~7 m·s-1,板壁温度设置为289~293 K,相应壁面过冷度设置为14~10 K,并修改流体相应的物性参数,计算结果如图8和图9所示。
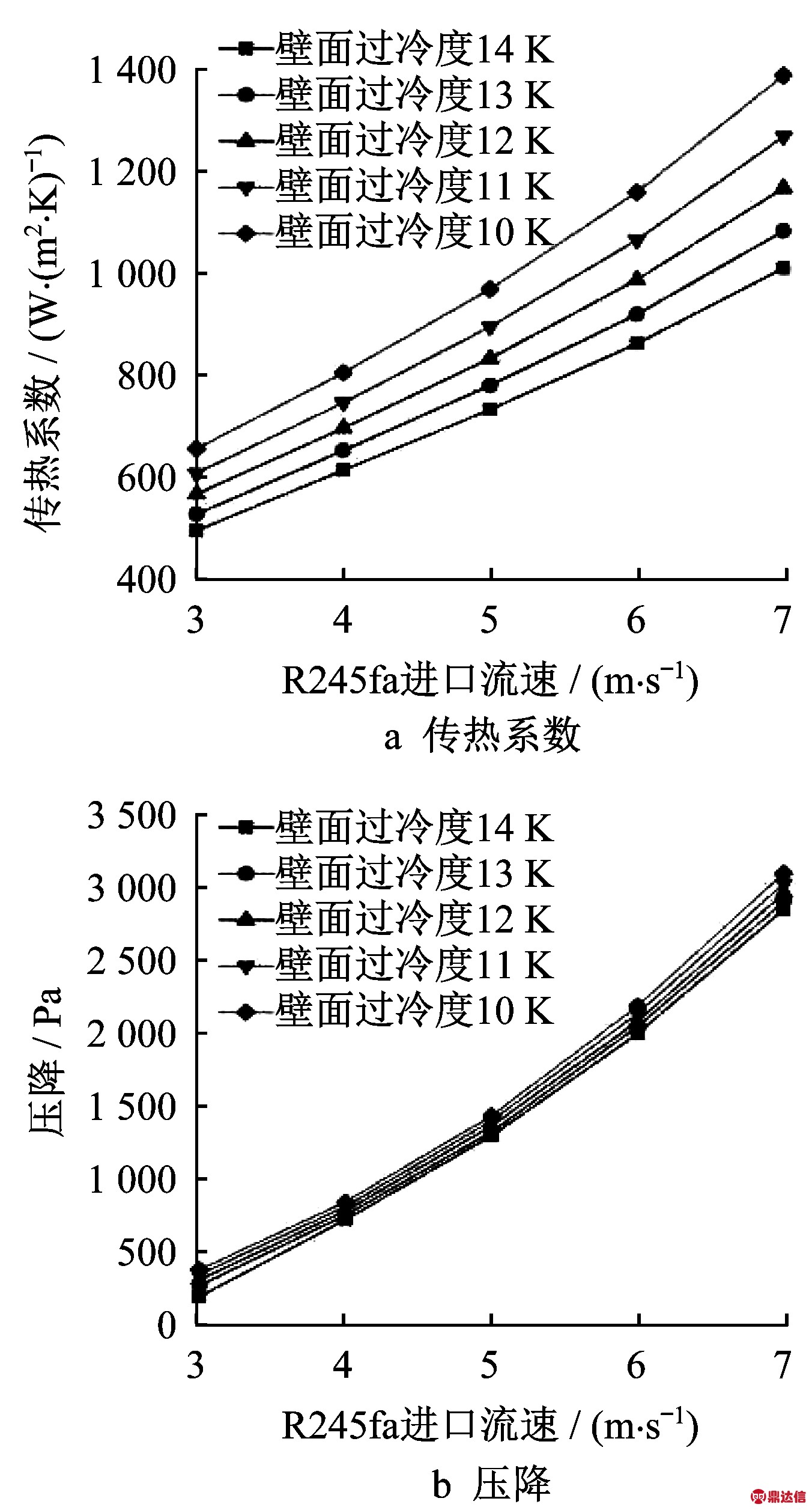
图8 不同壁面过冷度下传热系数和压降随进口流速的变化
Fig.8 Variation of heat transfer coefficient and pressure drop with inlet velocity at different wall undercoolings
由图8可知,壁面过冷度越低,传热系数和压降都越高,这是因为壁面温度升高会增大工质侧的流体湍流程度,使冷凝液更频繁脱离壁面。相反,壁面过冷度升高会增大传质的动力从而使凝结液膜增厚,增大了传热热阻。相比蒸汽流速带来的压降,壁面过冷度导致的压降变化并不明显。
从图9a可知,同一过冷度下,f随着流速的变化而增大,这与图6b中压降的变化规律基本相同,表明低流速下的阻力性能和流动性好于高流速状态,并且随着流速的增大,过冷度对f的影响在逐渐减小;当流速从7 m·s-1降到3 m·s-1时,f最大降幅达62.2%;同一流速下,蒸汽壁面过冷度越高,阻力因子就越小。原因可能是:随着壁面过冷度的增大,壁面温度逐渐降低,管内工质温度与管壁之间的温差加大,冷凝传热的驱动力越大,液膜越容易形成,液膜较壁面更加光滑,因此压降变低。由图9b可见,同一壁面过冷度工况下,冷凝器工质侧j/f随着流速的增大而逐渐减小。在同一流速下,当进口流速低于3 m·s-1时,较高壁面过冷度能提升综合传热效果,但是当流速高于3 m·s-1时,冷凝器工质侧j/f随着壁面过冷度的提升,强化传热综合效果逐步减弱。
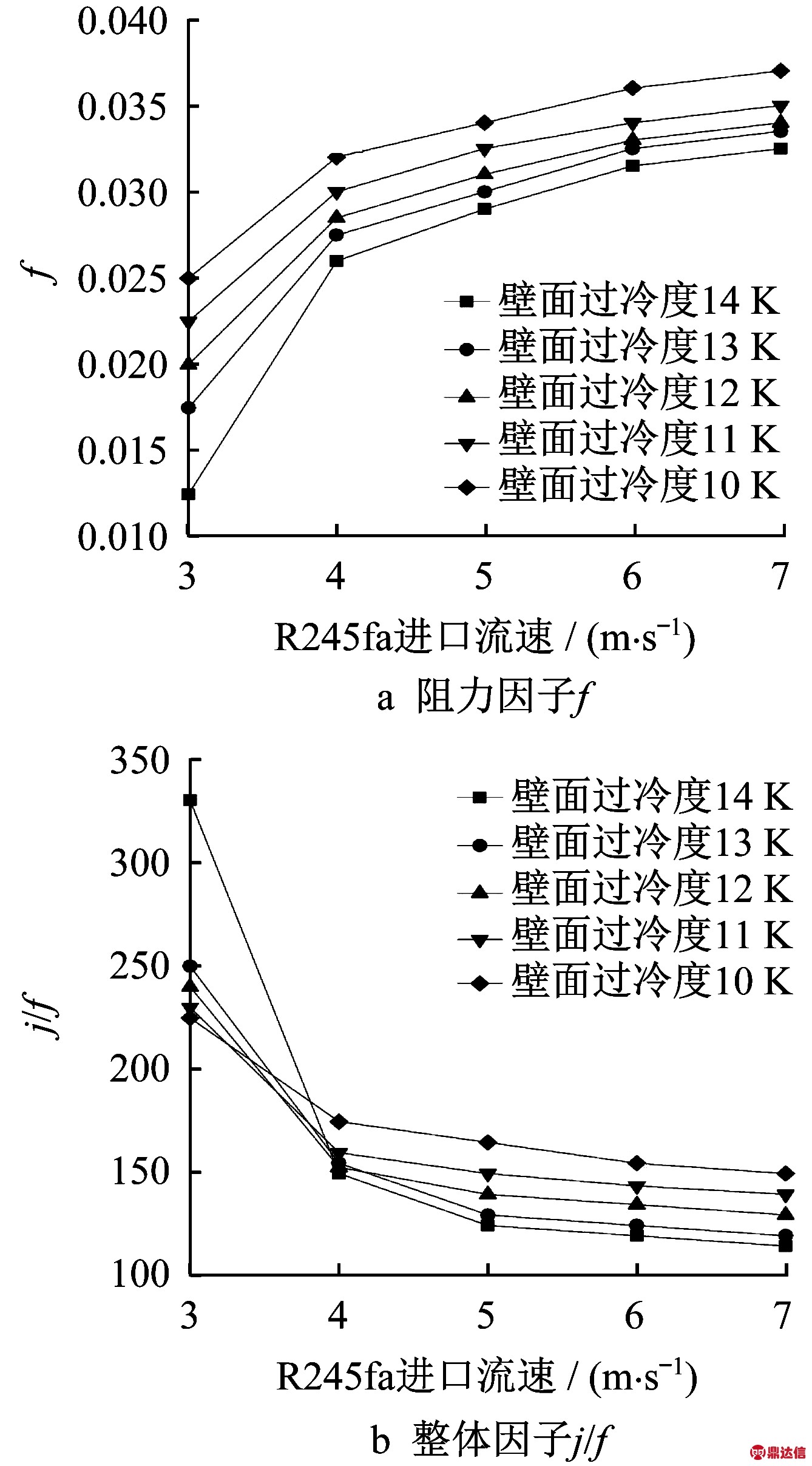
图9 不同壁面过冷度下阻力因子和整体因子随进口流速的变化
Fig.9 Variation of resistance factor and overall factor with inlet velocity at different wall undercoolings
3.3 蒸汽进口干度对传热系数和压降的影响
将蒸汽流速设置为3~7 m·s-1,蒸汽进口干度分别设置为0.1~1.0,并修改流体相应的物性参数,经过模拟及计算分析得到相关数据,如图10和图11所示。
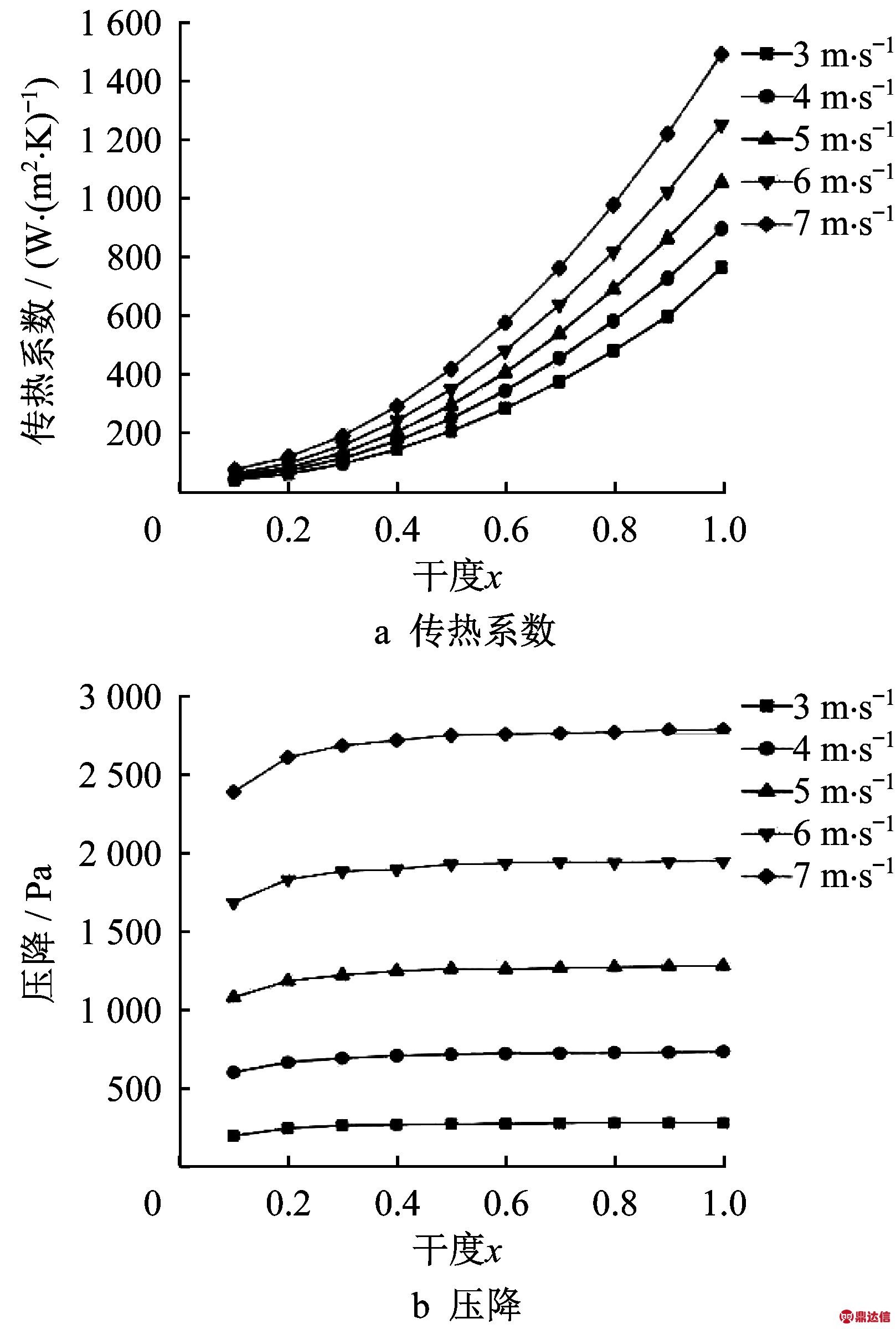
图10 不同蒸汽流速下传热系数和压降随进口蒸汽干度的变化
Fig.10 Variation of heat transfer coefficient and pressure drop on with inlet steam dryness at different steam flow rates
进口干度是指工质经过膨胀机出口管路段进入冷凝器前的干度,模拟过程中通过改变进口蒸汽液相的体积分数来调整干度的变化。由图10a可见,蒸汽进口干度越高,传热系数越大,可能因干度增加而导致两相流密度降低,速度则增大,两相之间切应力增大,从而增强了湍流强度。来流干度增大后壁面液体呈分散的液滴状,出现柱状凝结,干度越大形成的稳定液滴越多,液滴在蒸汽的吹动下易向前流动,维持壁面的干爽[22-23]。干蒸汽比例增加,导致气液两相相对速度也增加,两相由于流速不同而产生的摩擦压降增大。干度越小,相变传热程度越剧烈,汽水扰动越强,因此在0.1~0.4低干度区域内干度对冷凝压降影响较大,高于0.4后影响很小。
从图11a可以看出,当进口干度增加时,冷凝器工质侧的传热效果逐渐增强,在低干度区域0.1~0.4时,流速的增加对传热效果的影响很小,因为此时进口流体中饱和液相工质居多,而液相在速度上的轻微差距不会对传热造成较大影响。当处于高干度区域0.5~1.0时,随流速的增加,传热因子j的增加幅度也越来越大,当流速为7 m·s-1,j的最大增幅为22.5%。随着干度的增加,工质侧f也越来越大,但在高干度区域增加幅度很小,阻力性能和流动性呈现减弱的趋势,因此在高干度区域提升干度对阻力性能的影响不大。由图11b可见,在不同蒸汽流速下,板束侧j/f随干度的变化而逐渐增加。在同一干度下,流速越低,其冷凝器工质侧综合传热效果就越好;在相同蒸汽流速下,干度越高,蒸汽流速的变化对综合传热效果的影响逐渐增强,可以看到,流速为3 m·s-1时,j/f最大增幅达到124.4%,强化冷凝传热效果显著。
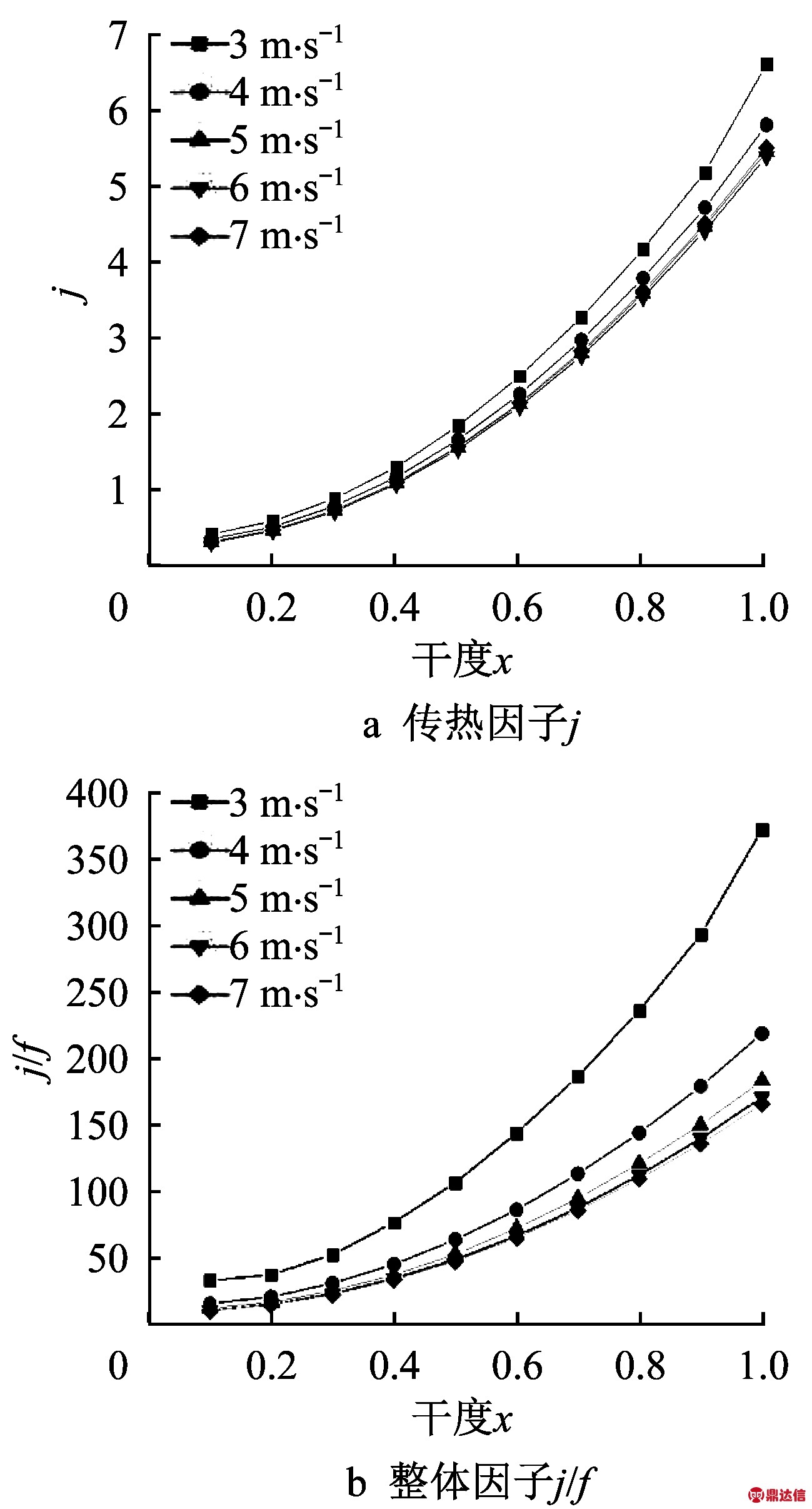
图11 不同蒸汽流速下传热因子和整体因子随进口蒸汽干度的变化
Fig.11 Variation of heat transfer factor and overall factor with inlet steam dryness at different steam flow rates
3.4 高炉冲渣水ORC余热回收系统中波纹板式冷凝器内R245fa冷凝传热关联式
影响传热模型的主要因素有流体流动形态、流量和进出口干度等[24],关于冷凝传热的关联式,文献[24-27]给出了各自的模型,Kumar的模型包含折算后的液相流量[25],Tovazhnyanskiy等[26]及王中铮等[27]的模型考虑了气液两相的密度比[27]。邱峰等[28]基于R410A在板式换热器中修正了王中铮等[27]的模型。根据计算结果和上述文献提出以下关联式:

式中:Re为冷凝液雷诺数;Pr为冷凝液普朗特数;为出口处两相平均干度;(μ/μw)0.14为动力黏度修正项;C1、C2、C3、C4为待拟合的4个常数。根据模拟结果,出口处的R245fa基本冷凝完全,即-x为0。因在板式换热器的传热和流动过程中对流传热系数较大,板壁温度几乎接近流体温度,两者温差较小,在计算过程中可以近似认为黏度修正项的值为1。此外,参考王中铮等[27]的冷凝传热模型,式(12)中影响冷凝传热的Pr的幂取0.33。冷凝传热关联式形式可以写成如下形式:

对数值模拟的计算结果进行整理后,选取一组代表性的数据进行关联式拟合。式(13)两边取对数,即C2是斜率,ln C1是截距,拟合结果显示两者标准误差分别为0.094和0.604,并且模拟值与关联式计算值误差在±20%以内,考虑到相变模拟,认为结果比较可靠。经Origin软件拟合得C1=0.584 0,C2=0.583 4,故传热关联式为

式(14)中物性取饱和时液相的值,此式适用的范围为:280<Re<1 130,6.07<Pr<6.15。虽然式(14)的使用范围较小,但是对高炉冲渣水余热回收ORC发电系统波纹板式冷凝器已够使用,其他范围内的适用性有待进一步验证。
4 冷凝器中间排液区间的讨论
排液区间的确定与板内液相的体积分数直接相关,为得到冷凝液体积分数随板长的变化情况,在板间通道内沿板长布置6个监测点。对于R245fa进口蒸汽质量的90%以上被冷凝的工况,经过计算,液相体积分数在7.52×10-3以上时则认为完全冷凝。不同蒸汽质量流量、蒸汽过热度以及进口干度下液相体积分数随板片位置的变化如图12所示。质量流量越小,冷凝液量越大。相同质量流量下,0~400 mm内蒸汽冷凝速度较慢。进口过热度越低,冷凝液量越大,因为过热度高需要经历过热区单相传热,而饱和温度下的蒸汽直接相变,板间通道传热剧烈,所以冷凝液量的增量也逐渐增加。干度在0.6~1.0时,其大小对液相体积分数影响很小,原因可能是虽然干度在增加,但是气体仍占较大份额,干度从0.6增到1.0时,气体体积分数增加了0.503%。
两相流在水平管内的凝结过程是:板片壁面温度低于饱和温度时,凝结液出现附着,刚开始凝结液滴散落成雾状,处于高传热强度的不稳定珠状或薄液膜环状冷凝传热;当冷凝液开始聚集时,液膜开始增厚并融合,两相流依次经过弹状流、塞状流和泡状流,传热效果急速恶化[29-30]。如果冷凝传热一直保持在靠近进口处,并形成珠状或薄液膜环状冷凝传热,传热效果就会大幅提升,因此考虑采用中间排液方式。
传统管内凝结的冷凝器,管壁凝结液膜随管长逐渐变厚,液膜的热阻十分影响传热。彭晓峰等[31]提出“中间排液、分段冷凝”的新思想,把分流隔板设置在联箱中的管程交接处,将冷凝液及时排走,降低液膜厚度。
结合R245fa在进口蒸汽质量90%以上被冷凝时可认为冷凝完全,则80%~90%被冷凝时,经换算后,当冷凝截面体积分数达到6.82×10-3~7.52×10-3时,适合排液处理。当质量流量逐渐变大时,理想的中间排液区间逐渐靠近板后方且区间逐渐变窄,因此若在质量流量较大的情况下使用中间排液,应适当延长板长。同理,这种情况也适用于蒸汽过热度。若不采取中间排液,该板型在质量流量26.05 kg·s-1、过热度16℃时有最佳冷凝效果。由图12可知,进口蒸汽干度在0.6~1.0时,进口蒸汽干度变化对板内液相体积分数影响可以忽略不计,故设计中间排液时可不考虑进口蒸汽干度。应当指出,对高炉冲渣水低温余热回收ORC发电系统波纹板式冷凝器的中间排液仅停留在由液相体积分数确定的区间范围的定性分析,还需结合具体排液方法进行精确模拟和实验。波纹板式冷凝器中间排液作为一种可以提高系统余热收集能力的方法,具有一定的应用前景。
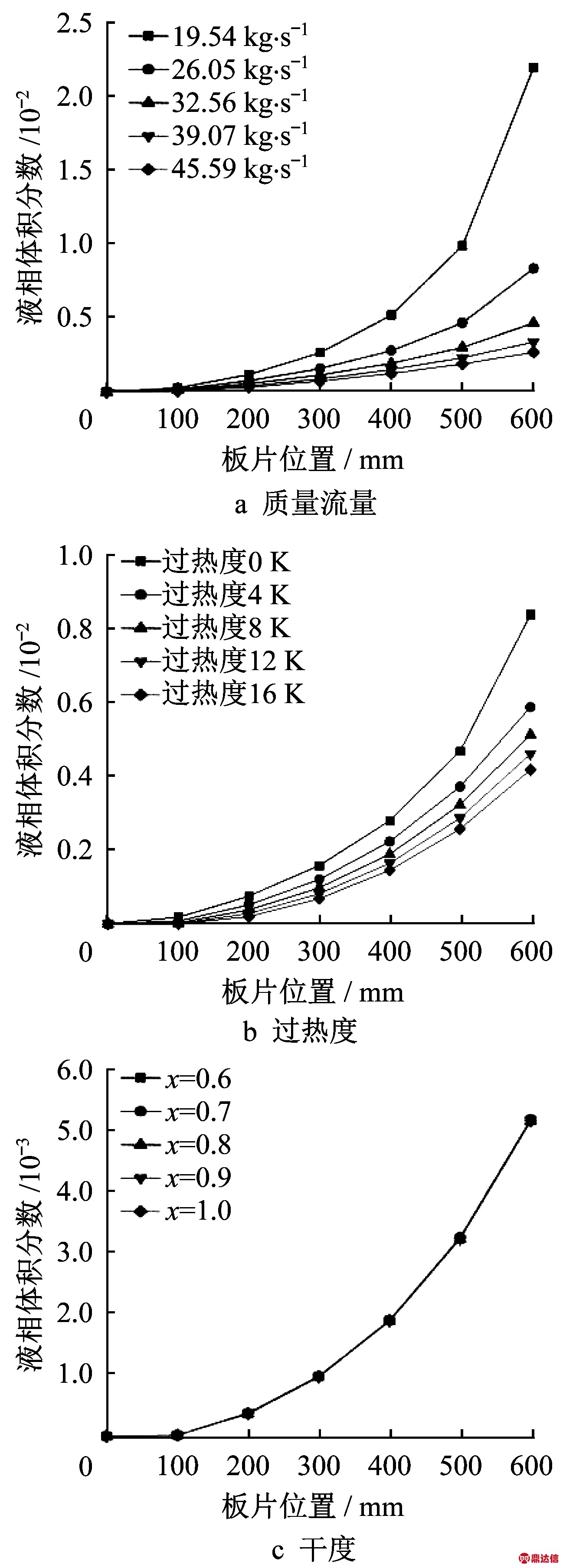
图12 不同蒸汽质量流量、蒸汽过热度、进口蒸汽干度下冷凝液相体积分数随板片位置的变化
Fig.12 Variation of volume fraction of condensate phase with plate position at different vapor mass flow rates,vapor overheats and inlet steam drynesses
5 结论
(1)讨论了R245fa在板式冷凝器内的传热特征。随蒸汽过热度的增大,传热系数逐渐越小,压降随过热度升高而增大;壁面过冷度越高,传热系数越小,壁面过冷度导致的压降变化并不明显;进口蒸汽干度越高,传热系数越大,同一蒸汽流速下,随着干度的增加,压降逐渐增加,干度到达0.5~1.0时,增加幅度越来越小。
(2)过热度不变,工质侧综合传热性能随流速的增大而减小。同一流速下,过热度的增加降低了工质侧的传热效果,当过热度超过4 K时,工质侧的综合传热效果随着过热度的减小而增大;壁面过冷度相同时,冷凝器工质侧j/f随着流速的增大而减小;在进口流速为3 m·s-1的工况时,较高壁面过冷度能提升综合传热效果,但是当流速大于3 m·s-1时,随着壁面过冷度的提升,强化传热综合效果减弱;在不同蒸汽流速下,板束侧j/f随着干度的增大而逐渐增大。在同一干度下,流速越低,工质侧综合传热效果越好。综合来看,该波纹板式冷凝器在过热度4 K、干度1.0、壁面过冷度14 K、流速3 m·s-1时有最好的综合传热性能。
(3)在低温余热回收的ORC发电系统冷凝器运行的工况下,给出了R245fa在波纹板式冷凝器中的传热关联式:Nuf=0.584 0Re0.583 4 Pr 0.33,此式适用的范围为:280<Re<1 130,6.07<Pr<6.15。
(4)探讨波纹板式冷凝器的中间排液可能性,即进口蒸汽质量的80%~90%被冷凝,R245fa在板式冷凝器内理想的中间排液区间随质量流量和蒸汽过热度变大,逐渐靠近板后方且区间逐渐变窄,但蒸汽干度对排液区间影响较小。