摘要: 随着激光增材制造基础理论研究和设备水平的提升,激光增材制造技术越来越多地应用于大型复杂结构的生产制造。激光增材成形过程中形成的应力会导致成形件变形、开裂,因此应力变形的控制是激光增材制造过程亟待解决的关键问题。本文总结了激光增材制造残余应力形成机制、应力变形测试技术和应力变形调控措施等方面的研究现状,提出了激光增材制造应力变形调控存在的主要问题及以后的研究方向,为高性能金属构件激光增材制造“控形”研究提供指导。
关键词: 高性能金属材料;激光增材制造;应力变形检测;应力变形调控
激光增材制造技术作为一种新兴的制造技术已改变现有工业零部件的设计生产制造方式。激光增材制造技术利用计算机将零件三维CAD模型进行分层切片,以高能量密度激光束为热源将材料熔化凝固,逐层堆积形成实体零件。激光增材制造技术可以实现多种材料、复杂结构零件的致密成形,综合力学性能优于铸造件,可以显著缩短制造周期,适用于新产品的开发、复杂零件的定制生产。激光增材制造技术主要包括同轴送粉式激光金属沉积(laser melting deposition, LMD)技术[1]和铺粉式选区激光熔化(selective laser melting, SLM)技术[2]。目前,激光增材制造技术已实现铁基合金、钛合金、铝合金、镍基高温合金、钴基合金、铜合金、钨、金等金属材料的加工[3-5]。随着激光制造装备技术的快速发展,激光增材制造技术已广泛应用于航空航天、医疗器械、汽车制造和模具制造等领域。
在金属激光增材制造过程中材料快速熔化凝固形成均匀致密的零件,材料将经历非平衡凝固、多层多道循环加热及冷却、固态相变过程,在非均匀温度梯度和约束作用下,零件内部将形成较大的热应力。同时,由于固定基板的约束和复杂零件成形过程中的支撑约束,变形受到限制而产生机械拘束应力。针对高性能合金材料,特别是高性能合金钢,因其合金成分多样、凝固与固态相变过程复杂,凝固组织存在复杂的非平衡相和组织转变,容易产生复杂的组织相变应力。残余应力较大时将影响零件尺寸和拉伸、疲劳性能,严重的将导致零件产生变形和开裂,见图1[6-7]。
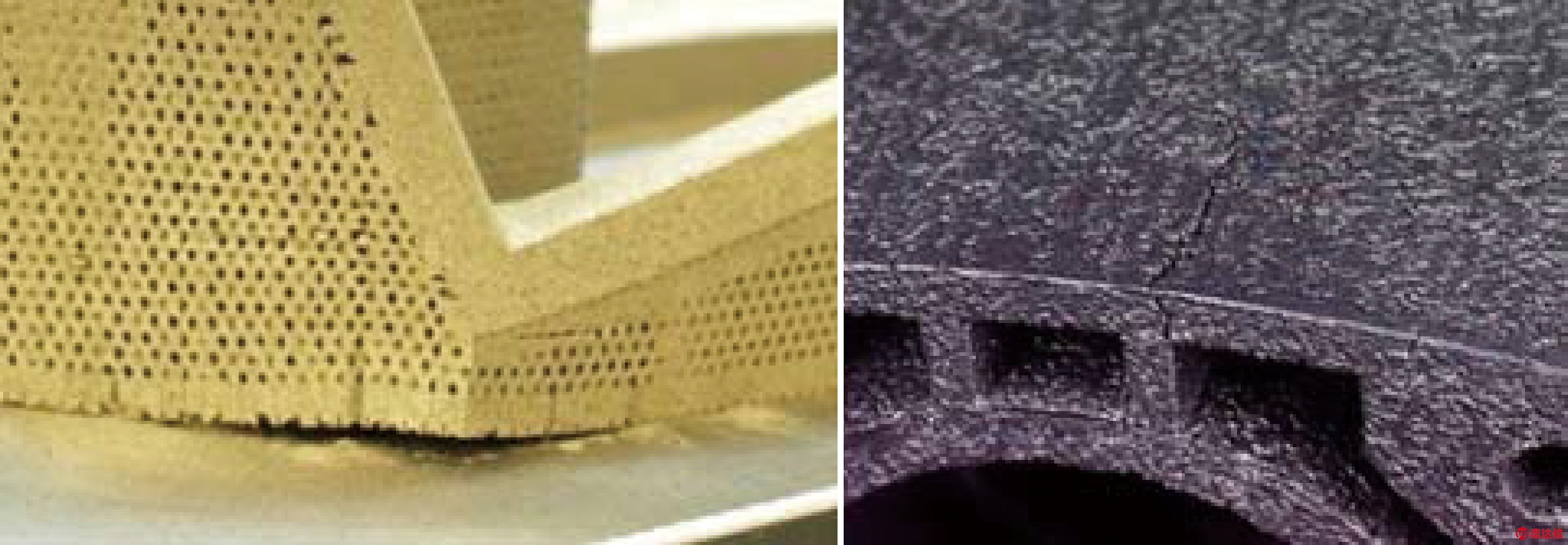
图1 激光增材制造结构变形、开裂缺陷[7]
Fig.1 Structural deformation and cracking defect in laser additive manufacturing[7]
目前激光增材制造过程中的应力变形控制主要依靠经验、可重复性差,特别是高端装备领域对大型复杂构件的高精度、高质量成形具有迫切的需求,因此,残余应力导致零件变形开裂的“控形”问题是激光增材制造过程中亟待解决的问题。本文将针对高性能金属构件激光增材制造技术应力变形的研究现状、检测方法、调控技术等方面的最新研究进展进行系统总结,提出目前存在的主要问题和今后的研究思路。
1 高性能金属构件激光增材制造应力变形的研究
1.1 激光增材制造过程应力变形的产生
金属激光增材制造过程中,应力的产生和演变规律与焊接过程相似,但由于激光增材多层堆积过程形状结构、支撑结构、环境温度的差异会使冷却过程不同,热过程差异造成应力演化、分布更加复杂。由于激光增材制造是一个极快速的熔化、凝固过程,且熔池尺寸较小,温度、应力变化过程较快,采用常规的测试方法无法对其过程实现实时的精确测量。目前,研究者们多采用有限元仿真结合实验的方法来研究激光增材过程残余应力和变形的产生、演变规律。
为了准确高效地预测激光增材过程的应力变形,学者对激光增材制造过程温度场、应力场的模拟做了很多研究。Wang等[8]采用有限元模拟和实验对比研究了激光选区过程工艺参数和扫描策略对应力的影响,并对残余应力的形成机制进行了讨论,结果表明:应力的形成主要是由于不均匀的温度梯度分布和高温下材料强度降低,引发塑性变形形成残余应力,多层温度累积会减小底层残余应力。Heigel等[9]采用原位温度、变形实时测量方法,结合有限元热-应力顺序耦合模型,对TC4钛合金激光沉积成形制造的热-应力演化过程进行研究,对比分析了不同层间停留时间的温度、应力结果,结果表明较大的温度梯度会形成大的残余应力和塑性变形。
钛合金、钴基合金和合金钢等材料激光增材过程中,在一定的冷却速率下组织转变会发生固态相变。固相晶体结构发生转变会引起体积变化、屈服强度变化和相变塑性,同时相变过程释放的相变潜热会对温度产生影响,热过程-组织转变-力学性能之间的交互作用都会对残余应力产生影响。Fang等[10]研究了马氏体不锈钢激光沉积过程固态相变各相性能差异、体积改变和相变塑性对残余应力的影响,结果表明:固态相变过程对应力的演变有显著的影响,可以显著减小纵向残余拉应力。Denlinger等[11]通过原位温度、变形测量和应力测试,结合有限元模拟结果对比分析了激光沉积成形Ti-6Al-4V钛合金和625镍基合金固态相变过程对应力的松弛作用,结果表明:由于镍基合金无固态相变转变,模拟结果与实验拟合较好;钛合金激光增材制造过程不考虑固态相变应力,模拟结果误差较大,考虑固态相变对应力的松弛作用可以更准确地模拟残余应力。大量研究结果表明:数值计算中若不考虑固态相变的影响会使残余应力的计算结果与实测值存在较大差异,因此为提高数值模拟的准确性需要阐明材料相变过程对应力应变的影响规律。
激光增材制造过程中成形零件是在基板上堆积成形,因此基板、支撑结构对成形体的约束作用会影响应力变形的分布。廖英岚[12]对比研究了不同厚度基板对激光选区成形应力的影响,材料在熔化凝固过程中,成形层的收缩会受到基板的约束作用,大厚度的基板对成形件的约束作用大,在成形层形成的残余拉应力也较大。其次研究了不同支撑结构对应力的影响,由于不同支撑结构对成形件的约束作用不同,上层实体在冷却收缩过程受到的限制不同,形成的残余应力也会有较大的差别。Zeng等[13]从传热角度分析了支撑结构对激光选区成形过程温度场的影响,支撑结构的形状、各向异性和独特的导热性能会影响热传导行为,通过优化支撑结构可以获得较均匀的温度场,有助于减小温度梯度引起的残余应力和变形。综上所述,激光增材制造应力变形调控过程中需要考虑基板拘束和支撑结构设计,通过此方法可以减小变形量。
1.2 激光增材制造应力变形仿真预测现状
金属激光增材制造过程残余应力变形的形成、演变过程机理的相关基础理论研究已逐渐完善,为了实现激光增材过程中应力变形的调控,目前的研究主要集中在激光增材应力变形仿真预测分析,基于此为后续的应力变形调控提供指导。有限元模拟计算对激光增材制造过程的应力计算有巨大的优势,但是当零件的尺寸较大时,有限元计算面临计算量过大而无法满足实际需要的情况。为了显著提高有限元模拟的计算效率和准确性,针对大型复杂结构激光增材过程应力变形主要采用自适应网格、固有应变法、多尺度仿真分析等方法对其进行研究。
Denlinger等[11]采用自适应网格实现激光选区增材过程的快速数值模拟,通过对熔池局部区域细网格的划分可显著减少网格数量,对比可知采用自适应动网格计算速度可以提高432倍,同时温度计算误差小于5%,采用该方法可以实现激光增材过程的快速仿真计算分析。倪辰旖等[14]为解决激光选区成形热弹塑性有限元计算效率低的问题,采用固有应变法预测零件的变形,通过对热源模型的校准,建立热源-局部-结构件递进模型,可以较准确地实现变形的预测,同时大幅度提高计算效率。Afazov等[15]采用结构有限元分析方法预测了激光选区成形大结构部件的变形规律,并与成形结构3D光学扫描进行变形量对比,结果表明:采用该方法可以准确、快速的预测大结构的变形。Li等[16]通过建立多尺度有限元模型预测结构件的残余应力变形,微观尺度的激光热源导入到粉层模型中,通过等效计算得到宏观模型的温度循环过程,结果表明多尺度模拟结果与实测结果拟合良好。随着金属增材制造需求的增加,已有多款商用有限元分析软件(Simufact Additive, ANSYS Additive, ABAQUS Additive, Autodesk Netfabb, ESI等)可实现应力变形的仿真分析。MSC公司基于固有应变方法开发了金属3D打印仿真软件MSC Simufact Additive,该软件运用经验公式得出固有应变值,并逐层施加在成形件上,得到零件的应力变形结果,可以进行支撑优化,预测热处理、基板支撑去除对应力变形的影响。ANSYS公司开发了ANSYS Additive激光增材制造应力变形分析软件,基于固有应变法可以实现大结构激光选区成形应力变形预测、支撑结构优化、变形补偿,减少打印过程的错误。
目前激光增材应力变形的仿真分析主要是基于热应力和热应变的分析,熔池内部复杂的物理冶金过程及相变行为对增材过程温度场、应力场有显著影响,需要进一步考虑微观冶金过程的影响,完善现有的仿真技术。激光增材制造过程缺陷的形成模拟及其对成形件变形和开裂的影响,也需要在激光增材控形中进一步考虑。同时,大尺寸结构应力变形的仿真效率和准确度仍需提高,应不断完善多尺度仿真技术,满足大结构激光增材结构应力变形的预测。
2 高性能金属构件激光增材制造应力变形检测技术
残余应力及变形控制一直是困扰大型结构件激光增材制造成形的一大问题,残余应力和变形的测量技术对应力演变、变形开裂行为的分析有着非常重要的意义。目前,测量残余应力主要的有损方法(DT)为:分割全释放法,逐层切削法、电化学腐蚀剥层法,钻孔法及基于钻孔法的云纹干涉法和全息干涉法等;无损测试方法(NDT)有:X射线衍射法、磁性法、超声法、中子衍射法等,各种方法的特点及应用范围如表1所示[17-23]。变形量的测试方法主要有:位移传感测量、曲率法、全息成像技术、三维光学动态应变测量、全场应变测量系统(DIC)等方法。
Denlinger等[11]为对比研究激光沉积成形钛合金、镍基合金过程层间保温时间对应力变形的影响规律,采用激光位移传感器测量了激光沉积成形过程中的变形情况,采用钻孔法测试了最终成形件的残余应力值。Salmi等[17]采用钻孔法研究了热处理和喷丸处理对铝合金激光选区成形件残余应力的影响。采用有损方法可以对激光制造成形件残余应力进行准确测量分析,但是会对激光成形件造成一定程度的破坏,因此此类方法适用于实验室研究中,不适用于激光增材成形件残余应力的实际生产检测。
表1 金属材料残余应力测试方法对比[17-23]
Table 1 Comparison of the residual stress testing methods of metal material[17-23]
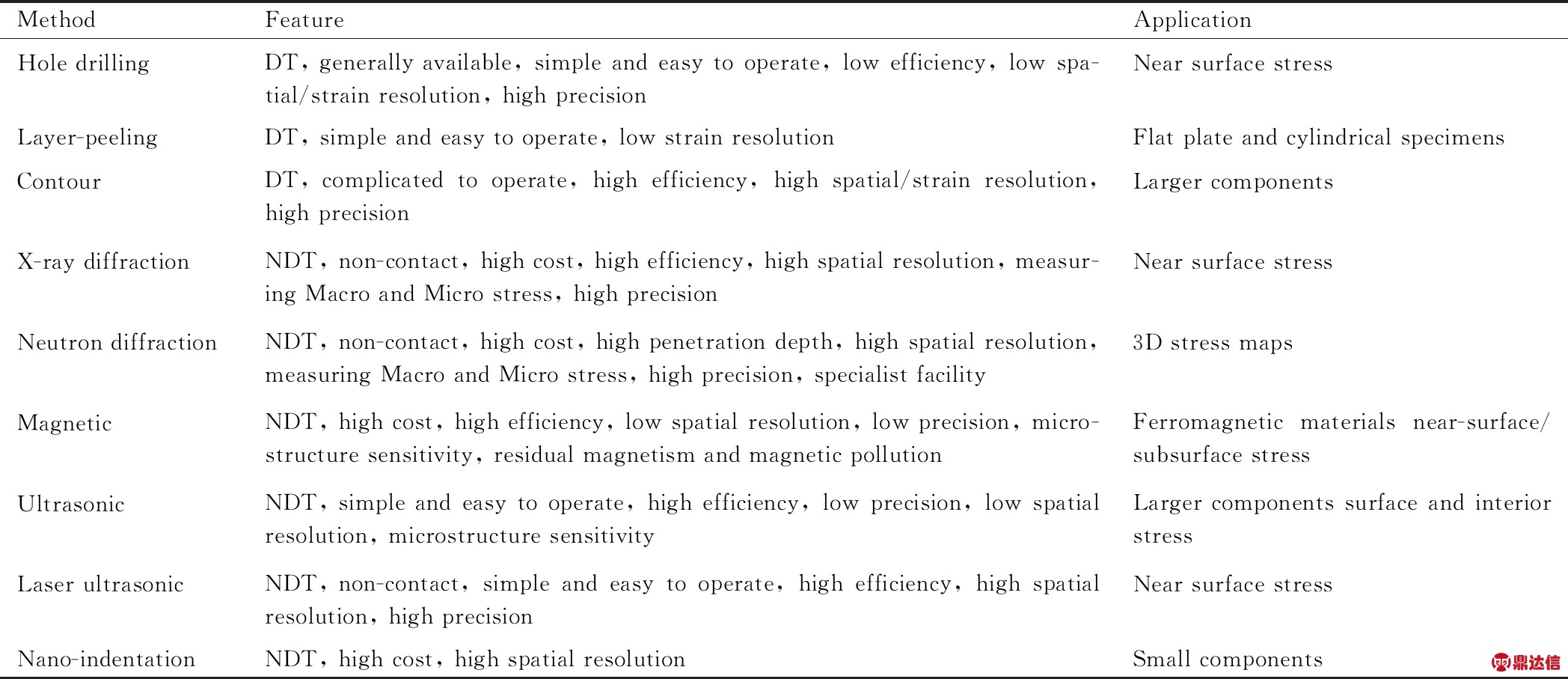
残余应力的无损检测将为改进激光增材制造工艺、减小应力后处理措施提供重要支持。X射线法主要用于材料表面二维应力的测量,由于设备结构较简单,因此可实现大型复杂结构表层应力的测试分析。Liu等[18]用X射线衍射法测试分析了316L不锈钢激光选区成形的残余应力,探讨了热输入和扫描策略对横向纵向残余应力分布的影响。超声波法是利用超声波波速与应力之间的关系来测量残余应力,具有穿透能力强、无损、快速等特点。董世运等[19]以激光熔覆再制造试样为研究对象,采用超声瑞利波结合静载拉伸实验,研究了内部组织和初始应力状态对激光熔覆层应力的影响,经过应力校准后超声应力测试结果在可接受的范围。超声波法存在超声波易受环境温度、组织缺陷(包括织构、位错密度、晶粒尺寸等)和微观缺陷的影响,因此需要对其进行修正处理才能保证测量精度。中子衍射法由于其穿透能力强,因此可测定材料内部的应力获得三维应力分布。An等[20]针对激光粉床成形625镍基合金叶片,采用中子衍射技术测试叶片的整体应力分布,结果表明成形叶片顶部和底部为拉应力,中部为压应力分布。Wang等[21]采用原位中子衍射方法分析了激光增材成形镍基合金高温退火过程的应力演变规律,随着时间的增加残余应力逐渐减小,一定时间后达到稳定状态。但是,中子衍射仪成本较高,在一定程度上限制了其使用范围。此外,随着测试仪器技术的发展,也有一些新的测试方法用于残余应力的测量。纳米压痕应力测定法是借鉴盲孔法的应变测量思想,基于应力场干涉理论进行残余应力的测量。Zhu等[22]采用纳米压痕法测试了激光熔覆铁基涂层全厚度的残余应力,结果显示随着深度的增加残余应力逐渐增大。纳米压痕法对测试表面平整度有一定的要求,同时其测试准确性受到材料塑性变形能力的影响,因此该技术仍需要不断完善理论计算模型提高测试准确度。激光超声波法利用激光作为激发源产生剪切波和纵波来测量材料的残余应力,具有无损、可测任意深度应力、空间分辨率高等特点。Zhan等[23]采用激光超声波法测试了合金钢焊缝的残余应力分布,测试结果与钻孔法结果一致,该方法具有较好的应用前景。
激光增材过程中成形件的变形将影响铺粉均匀性以及后续成形的尺寸精度,所以变形量的检测和控制也需要特别关注。Sabine等[24]通过对表面形貌进行扫描测量,基于梁形曲率法计算可以得到表面尺寸偏差,实现激光选区成形件变形量的准确测量。Peter等[25]采用全息成像技术实现了激光熔化不锈钢表面过程的实时变形检测,测试精度可达微米级。Lundbäck等[26]采用三维动态光学应变测量系统实现整个沉积成形过程中的变形测量,通过反馈控制可实现成形过程沉积体积和成形形状的控制。Biegler等[27]采用全场应变测量系统(DIC)实现激光沉积成形过程变形的原位测量,结合数值模拟可实现复杂结构变形的预测。
以上残余应力变形测试方法各有优缺点,应根据实际情况选择一种或多种测试方法进行测量研究。由于激光增材制造的残余应力、变形是一个逐渐累积、重分布的过程,对其过程的实时监测进而实现工艺参数反馈控制将是未来研究的主要方向。金属增材制造制件的组织和缺陷特征也与传统制件不同,主要表现为组织的不均匀性以及明显的各向异性,加之主要缺陷类型及分布特征均与传统制件差异较大。因此,必须针对金属增材制造成形件的特殊性开展相应的检测方法及规范标准的研究。
3 高性能金属构件激光增材制造应力变形调控技术
激光增材制造过程中由于温度梯度较大且凝固行为复杂,较大的热应力是引起成形结构变形、开裂的主要原因,其次复杂的材料成分、凝固过程、材料组织形态、力学性能等均对应力开裂行为有较大的影响,因此为了解决激光增材过程中温度梯度大、材料易开裂等问题,研究人员已开发多种方法用于控制激光增材成形件的应力变形问题。
3.1 粉体材料设计调控应力变形
金属激光增材制造过程中的应力变形行为与材料的凝固过程、塑性变形能力、相变行为等相关,通过优化设计材料的组分,可以从根本上改变材料的凝固温度点、相变温度点,进而改变激光增材金属凝固过程热应力和相变应力的形成;此外新材料的设计开发可以改变材料的导热系数、热膨胀系数,通过改变传热行为影响温度梯度分布及膨胀收缩行为实现热应力的调控。
Pratik等[28]研究了低熔点共晶Al-Si合金激光选区成形过程的成形特性,采用混合粉末代替预合金粉末,由于低熔点共晶材料原位合金化过程温度较低,通过控制工艺参数和基板预热温度可以使熔池金属保持半固态状态,有利于应力的释放和减小变形,通过此方法可以获得低应力、无支撑结构成形。方金祥[29]通过调整合金元素配比实现了高强合金钢叶轮激光熔覆再制造过程残余应力的调控,通过调整Mo、Nb、稀土元素含量保证材料的强韧性;同时降低C含量、提高Ni含量,降低马氏体转变温度点,相变过程的相变塑性及相变体积效应使拉应力得到释放,达到降低修复过程残余应力的目的。顾冬冬等[30]开发了一种具有奥氏体-马氏体相变转换的铁基复合粉末,以WC陶瓷颗粒为奥氏体-马氏体转变控制剂,WC陶瓷颗粒的溶解及W原子的固溶将降低马氏体开始转变温度,通过改变激光选区成形的工艺参数控制冷却速率,从而促进相变诱导过程,有助于减小应力变形,同时WC增强相抑制裂纹扩展,可实现复杂薄壁铁基零件的超高精度成形。
目前通过材料成分设计进行应力变形调控的相关研究仍较少,未来随着金属激光增材制造材料体系的完善和新材料的开发,例如设计ZrC-SiC、石墨烯等增强复合材料,通过改变其传热行为、膨胀收缩行为、相变过程,减小应力与变形的累积,从材料基础上实现激光增材应力变形的调控。
3.2 工艺参数调控应力变形
激光增材制造过程是一个周期性、非稳态、短时非平衡循环过程,激光功率、扫描速率、粉层厚度、层间温度、扫描策略等参数通过影响成形件的温度历程,影响成形件应力变形的演化。激光增材制造过程通过优化工艺参数可以实现应力累积过程的控制,减小变形开裂倾向。
Wang[31]采用有限元模拟计算与实验结合的方法,研究了激光沉积成形工艺参数对残余应力的影响规律,模拟结果与实验结果拟合良好。成形件顶层残余应力随扫描速率增大、激光功率减小、送粉速率增加及预热温度升高各自呈现逐渐减小趋势。Mugwagwa等[32]研究了激光选区成形过程中激光功率、扫描速率、粉层厚度对成形件变形的影响规律,结果表明:减小粉层厚度可以减小变形量,增大扫描速率,变形量增加,激光功率对变形量的影响不显著,因此可以通过控制粉层厚度和扫描速率实现应力变形的调控。Denlinger等[11]通过激光沉积成形过程原位变形测试,分析了镍基合金、钛合金多层堆积层间停留时间对应力变形的影响规律,钛合金成形过程中减少停留时间有助于减小残余应力与变形,相反镍基合金通过增加停留时间有助于减小残余应力与变形。
激光增材制造过程中成形扫描策略会影响温度循环过程、温度梯度分布、应力累积,通过优化扫描策略可以改善应力分布、减小应力集中。杨光等[33]通过实验与有限元仿真相结合研究了不同激光扫描路径对激光沉积成形件应力与变形的影响,采用长边和短边扫描时最大残余应力出现在基体两端,长边扫描成形件变形最大;采用层间交错扫描方式残余应力较低且分布均匀,变形量较小。Cheng等[34]采用三维有限元模型分析了激光选区成形不同扫描策略成形件的温度、应力和变形分布规律,结果表明:由外向内扫描成形残余应力最大,45°线性扫描可以显著减小残余应力与变形,由内向外扫描成形的变形最大;由于模型尺寸较小,此模拟计算结果仅适用于其设定的模拟条件。Haider等[35]通过实验测试分析了扫描策略对应力及力学性能的影响规律,其中90°交替扫描策略的残余应力最小,分块扫描策略残余应力较大;采用分块扫描策略时,增大区块扫描线长度残余应力呈现增大趋势,分块扫描相邻区域改变扫描方向可以减小残余应力,扫描策略的改变对性能的影响不显著。
3.3 预热缓冷及重熔调控应力变形
激光增材制造过程中热应力主要是由于不均匀的温度梯度分布和快速冷却凝固造成的,因此为了解决温度梯度较大的问题,研究人员提出了采用基板预热、成形仓体气氛预热、多光束、耦合光束、光束重复扫描等多种方法,如图2所示[36-37]。激光增材制造过程通过控制激光增材过程的温度梯度,可实现残余应力变形的调控。
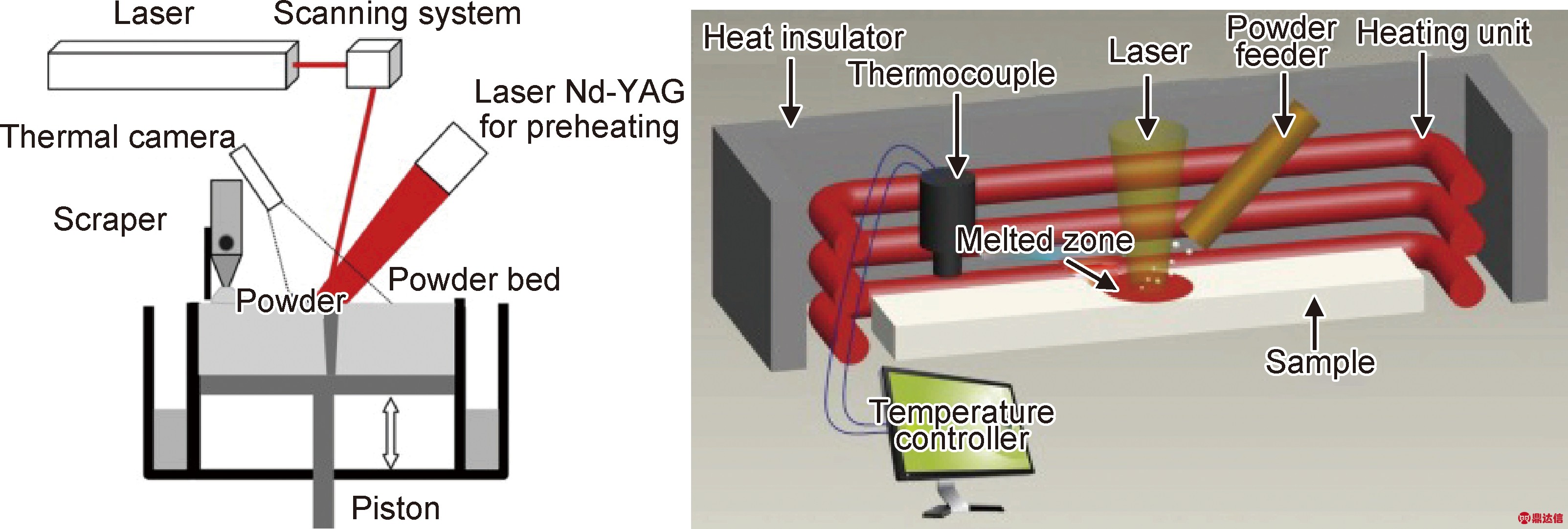
图2 激光增材制造典型预热方法[36-37]
Fig.2 Typical preheating methods of laser additive manufacturing[36-37]
卞宏友等[38]采用有限元模拟研究了基板预热对激光沉积修复高温合金的温度场和残余应力的影响,模拟结果与实验测试结果吻合较好,随着基板预热温度增加,温度梯度逐渐减小,热应力显著减小。Damien等[39]对比分析了不同基板预热温度对激光选区成形铝合金变形的影响,基板预热温度为150℃时,成形件变形量显著减小;预热温度升高至250℃时,基本检测不到变形量。Hagedorn等在激光选区成形陶瓷材料过程中采用辅助激光束局部预热粉床,预热温度达到1600℃以上,可显著减小温度梯度防止热应力的形成,最终获得高致密度、无裂纹的实体[40,36]。段宣明等[41]提出了一种新型的双波长激光选区成形方法,通过将两个波长光斑耦合为同轴共光斑,短波长光束用于选择性熔化粉末,长波长光束用于预热和后续热处理,有助于减小温度梯度,实现残余应力的控制。Liu等[37]采用闭环温度加热系统实现激光增材制造过程成形仓体温度的整体预热,可以实现陶瓷材料的无裂纹成形。Papadakis等[42]基于有限元模拟对比了激光选区成形三种预热方式(成形仓体气氛预热、成形基板预热、激光预扫描预热)的能量效率,激光预扫描预热适合于成形小体积实体,成形仓体气氛预热、成形基板预热适用于成形大结构实体。
Furumoto等[43]研究了激光选区成形过程中激光前后重熔扫描对成形件残余应力的影响,结果表明:采用激光前预热处理可以显著减小残余应力和变形;采用激光重熔扫描可以显著减小成形件表面的残余应力与变形,对结构内部的残余应力影响较小。Mercelis等[44]在激光选区成形过程中每层采用50%的能量进行重复扫描可以减小30%的残余应力。Shiomi等[45]的研究结果也表明激光成形过程中每层采用150%的能量进行重复扫描可以减小55%的残余应力。Haider等[35]研究了钛合金激光选区成形过程激光重复扫描对成形件残余应力的影响,采用150%能量密度重复扫描可以减小残余应力,但会造成表面氧化和力学性能劣化。
3.4 结构设计调控应力变形
激光增材成形过程中,由于成形基板、支撑结构、结构自身的约束作用,同时由于成形结构、支撑结构对成形过程中导热的影响,对成形实体会产生机械拘束应力并会影响整体残余应力的分布。结构优化设计主要包括结构拓扑优化改变材料分布使结构过渡均匀、支撑结构优化减小应力变形,通过结构设计来减小或改善残余应力的分布是一种新的应力调控思路。
付兴领等[46]研究了激光立体成形过程中基板预变形处理对成形件残余应力与变形的影响规律,结果表明:激光立体成形过程中基板预变形对成形件的变形量影响最显著;成形件堆积过程中上部的残余应力变化规律为先增大后减小;通过基板预变形可以显著改善成形件的变形,减小残余应力。Mishurova等[47]研究了镍基合金激光选区成形支撑结构对应力变形的影响规律,结果表明:与直接实体成形相比支撑结构可以有效地减小残余应力,但会在基板切除后引入较大的变形量,因此需要综合考虑支撑结构的设计添加。Calignano[48]针对铝合金、钛合金悬臂结构激光选区成形过程,通过优化设计支撑结构研究其对成形件变形的影响,通过实验优化支撑结构的主要参数:支撑齿高、齿宽、齿间距、齿底宽等参数,获得铝合金、钛合金不同的支撑结构参数,优化后的支撑结构可显著减小成形件的变形。ANSYS Additive激光增材有限元分析软件,可实现复杂结构激光成形过程应力变形的预测,同时基于变形结果进行模型变形补偿,通过结构预先补偿实现成形件的变形控制,如图3所示。
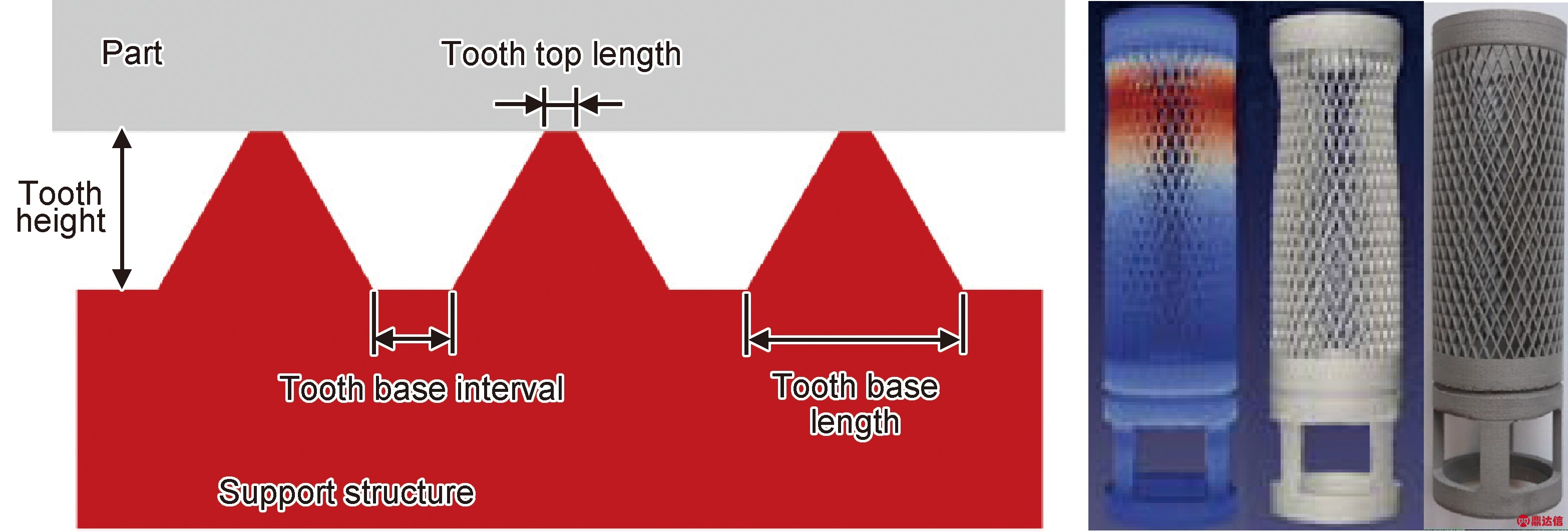
图3 激光增材制造支撑结构设计及结构优化[48]
Fig.3 Support structure design and structural optimization of laser additive manufacturing[48]
3.5 辅助外场调控应力变形
激光增材制造过程中通过控制工艺参数、扫描策略等方式只能在一定程度上改善残余应力的分布、减小残余应力,但是由于激光增材多层堆积过程应力的累积,特别是复杂大结构应力分布复杂、应力累积较大,因此结构尺寸效应极易造成成形结构的变形开裂。为了进一步控制残余应力变形,研究人员把其他物理能量场,如超声波、磁场、激光冲击波引入到激光增材制造过程中[49-55],对激光增材熔池凝固行为进行辅助干预,改变其微观组织和应力分布,实现激光增材制造应力变形的调控。
超声在材料加工中有极大的应用潜力,由于超声具有振动、空化作用,能够在一定程度上改善材料加工过程的微观组织、应力分布状态,因此可以将超声应用于激光增材制造过程中,实现对应力变形的辅助调控。钦兰云等[49]将超声引入到钛合金激光沉积成形过程中,超声振动通过影响组织凝固行为,能够显著降低成形件内部的残余应力。王潭等[50]通过超声振动辅助激光成形镍基合金,并对其成形质量、残余应力和力学性能进行分析,结果表明:引入超声振动后有助于激光熔池温度的均匀分布,降低晶界位错能量使材料处于较稳定状态,从而使残余应力均匀化、减小残余应力累积。Zhang等[51]研究了超声冲击辅助激光选区成形过程的残余应力、缺陷、组织转变规律,超声冲击后成形件内部缺陷显著减少,同时可以显著减小残余应力。
电磁搅拌是利用电磁感应原理形成电磁力场,电磁力通过对熔体进行强烈的搅拌作用,从而改变金属液在凝固过程中的温度场、溶质场、流场等,达到改善材料性能的目的,已在铸造、焊接和熔覆中得到较多的应用。孙杰等[52]采用实验测试与数值模拟相结合研究了电磁辅助激光沉积成形过程电磁场对残余应力的影响,结果表明:同步轴向电磁力可以较好地减小成形件的内部残余应力。Hitomi等[53]研究了辅助磁场对激光选区成形件表面残余应力的影响,通过处理有助于减小表面粗糙度,同时表面残余拉应力转变为残余压应力。
激光冲击表面处理技术采用高功率密度、短脉冲的激光作用于金属表面,使金属气化形成高温、高压等离子体,等离子体继续吸收激光能量升温膨胀,然后爆炸形成高强度冲击波作用于金属表面,使材料发生塑性变形并产生残余压应力,同时大幅度提高材料的力学性能。目前已有研究人员将激光冲击技术与激光增材制造过程相结合,改善成形件的应力累积和分布。Kalentics等[54]通过改变脉冲时间和光斑大小可实现3D激光冲击强化,并将其应用于激光选区成形过程中,可形成较大的残余压应力。与传统的激光冲击技术相比3D激光冲击可以形成更大的残余压应力和压应力层深度,适用于激光增材多层堆积成形过程应力的调控。Guo等[55]研究了激光冲击强化对激光沉积成形钛合金成形件残余应力的影响,经过冲击强化以后,材料表面的拉应力转变为压应力(200MPa),且压应力层深度可达0.7mm,同时可提高材料的力学性能。
3.6 后处理调控应力变形
激光增材成形结束后内部仍存在大量的残余应力,在支撑、基板去除后成形结构会产生变形甚至开裂。为使增材结构件满足后期尺寸及使用性能要求,需要对其进行后处理减小残余应力、提高力学性能,常用的后处理技术主要有整体/局部退火热处理。后热处理工艺是目前减小激光增材结构整体残余应力最有效的措施。
卞宏友等[56-57]采用感应加热系统对激光成形修复试件进行局部去应力退火热处理,局部热处理后残余应力降低30%以上,同时由残余应力引起的端部变形量也显著减小,采用此方法可以解决大型结构整体热处理困难、效率低等问题。Song等[58]研究了真空退火处理对铁基材料激光选区成形件残余应力、组织性能的影响,经过热处理成形件的拉应力得到释放,剩余残余应力几乎为零,残余应力作为再结晶的驱动力使晶粒尺寸细化,材料的强度性能得到提升。
目前,针对激光增材残余应力变形问题,通过优化工艺参数、改变成形路径及基板预热是在激光增材制造过程中控制残余应力的最有效方法。采用激光冲击、超声冲击技术可以改善表面残余应力,但是激光冲击、超声冲击法只能用于减小表面应力,对于复杂结构内部残余应力的控制具有很大的限制。后热处理工艺是增材结构件成形后减小整体残余应力的常用措施,针对不同的材料需要详细研究其对应力及组织性能的影响。采用材料、结构优化设计改善残余应力累积及分布的相关理论技术逐渐应用于新型结构应力变形调控。多光束耦合、辅助磁场超声场等技术由于设备限制多应用于实验室中,在实际生产中的推广应用较少,未来随着相关技术的发展逐渐成熟,将有更多的技术应用于激光增材制造。
4 结束语
随着激光增材制造技术广泛应用于大型复杂结构的制造,残余应力引起的变形开裂问题将限制其广泛应用,因此,开展激光增材制造残余应力变形调控技术的研究有着非常重要的意义。今后激光增材制造应力变形调控的研究可集中在以下方面:
(1)针对高性能金属材料进一步深化研究激光增材过程热-凝固-应力变形演化行为及耦合机制,建立激光增材成形结构的开裂判据,并提出相应的应力调控方法及预防变形开裂的工艺准则。
(2)结合结构件服役需求,基于材料基因组技术设计开发新型的低热膨胀系数、高强韧的金属材料、金属基复合材料、梯度材料等;同时充分发挥激光增材可成形复杂结构的优势,在结构设计过程中考虑结构因素对结构增材制造过程应力变形及使用性能的影响。
(3)开发新型的多激光耦合技术、激光阵列成形技术、激光复合增材制造技术,在金属结构件成形过程中控制残余应力的叠加累积;同时结合过程监测控制技术实现过程应力变形检测,建立相应的调控策略,实现激光增材制造过程应力变形的实时调控。
(4)进一步完善激光增材制造残余应力变形的检测技术,提高残余应力测试精度和三维残余应力检测能力;开发激光增材制造多物理场、多尺度数值模拟技术,提高激光增材应力变形的准确性及计算效率,并应用于结构设计、材料设计、工艺预测、组织性能预测等激光增材“全链条”制造过程。