摘 要:软体驱动器是软体机器人的重要组成部分。针对传统的设计方法难以设计具有特定功能的软体驱动器问题,提出一种基于主应力线的软体驱动器的设计方法,可以实现基于目标功能的设计。该方法基于给定的目标功能参数,通过预仿真计算主应力线方向,并沿着主应力线方向环绕气动腔室生成框架约束结构。最后,使用启发式的方法调节框架约束结构的材质参数以及腔室的气动压力。基于该软体驱动器设计了软体气动抓手,并进行了抓取实验,验证了所提设计方法的有效性。
关键词:软体气动抓手;弯曲变形;主应力线;材质优化;软体机器人
0 引言
软体机器人是一类新型仿生机器人,其设计灵感来自于自然界中各种软体动物,以软体材料为主,具有无限自由度与连续变形的能力,不仅可以灵活改变自身的形状,还具有一定抵抗冲击的能力,被广泛应用于生物医疗、人机交互、工业生产等领域[1]。
软体驱动器是软体机器人的核心部分,其设计工作具有一定挑战。软体驱动器通常由电活性聚合物[2]、形状记忆合金[3]、水凝胶[4]、人工气动肌肉[5]、超弹性材料[6]等构建。通过电刺激、流体压力、化学反应等实现驱动,其中流体驱动方式具有能量密度高、成本低、制造简单的特点,被广泛应用。Mutlu等[2]结合机电动力学模型使用基于优化的逆向运动学方法准确地估计电活性聚合物驱动器(Electro-Active Polymer,EAP)驱动器的整体形状偏差。Lin等[3]使用形状记忆合金设计了一种具有多种运动模式的新型滚动机器人。Lee[4]等根据水凝胶膨胀引起快速屈曲的特性设计了跳跃式机器人。Liu[5]提出一种由人工气动肌肉驱动的多关节双足机器人模拟人体运动,其中每个关节均由一对对抗肌肉驱动,通过控制肌肉内的压力来调节关节顺应性。文献[6]利用设计的pneu-net架构并使用硅橡胶材料制造了可由气压快速驱动的软体驱动器。
在设计理论方面,主要分为3类:
(1)分析建模的方法
该方法研究软体驱动器的建模和表征[7-8],并取得了一定进展。Singh等[9]构建了一个基于最大体积约束的简单等周问题的模型,分析了具有不对称性和任意纤维方向的驱动器的变形,显著降低了分析中涉及的数值复杂性。Jones等[10]利用改进的D-H(Denavit-Hartenberg)模型和几何分析建立了适用于一类软体驱动器的运动学关系。Polygerinos等[11]提出了纤维增强型软体驱动器的分析模型。Wang等[12]采用影响系数法建立柔顺构件等效系统的动力学模型。然而,这类设计方法局限于研究主要的基本运动,设计周期长,计算成本较高;
(2)优化的方法
该方法主要通过各类优化算法进行设计优化。Rieffel等[13]使用进化算法优化设计,但是由于孤立了制造过程,使得难以对软体驱动器进行制造。Hiller等[14]使用基于体素表示的进化算法进行设计优化,但是体素表示的方法导致模型表示精度较低。
(3)分析建模与优化相结合的方法
该方法能够实现具有特定输出功能的软体驱动器的设计。Connolly[15]通过研究纤维增强型驱动器的纤维方向与产生的输出功能之间的关系建立了软体驱动器基本运动的分析模型,并将目标运动轨迹分解成基本的运动单元轨迹,从而实现基于目标轨迹的纤维增强型软体气动驱动器的自动设计。该方法实现基于目标运动轨迹的软体驱动器的自动化设计,拟合运动轨迹的效果较好,但是分析模型比较复杂,且仅限于运动轨迹的拟合。Ge[16]根据抓取物体的特点,设计了一个由3个亚毫米级软体气动驱动器组成的夹持器,并基于投影微立体技术,利用数字光处理(Digital Light Procession,DLP)打印设备实现了快速且高精度的气动驱动器的制作。该方法设计的软体驱动器可以很好地实现抓取的功能但无法针对不同设计目标做出改变。Hasse等[17]设计了一种结合超材料和柔性集成驱动的新型主动弯曲软体驱动器,利用非对称的泊松比来调节管状结构的周向应力或应变,从而实现可控的弯曲性能。但该方法不仅依赖于所定制的超材料且没有考虑材料轴向性能的变化,因此不能实现无限的变形路径。Decroly等[18]利用硅胶材料,设计并优化了一种可操纵导管的微型柔性流体弯曲驱动器。该方法首先根据实验结果对设计模型进行验证,从而识别驱动器的关键设计参数,在此基础上利用数值模型进行优化研究,虽然很好地再现了预定的设计目标,但涉及到的数值模型较为复杂且无法根据任意设计目标进行数值优化。
上述设计方法中,分析建模与优化相结合的方法能够实现具有目标输出功能的设计,但是过于繁琐,且针对性强。因此,本文提出一种基于主应力线的软体驱动器的设计方法,具有更大的设计空间,不但可以应用于各种气动驱动器,如拉伸、弯曲和扭转驱动器,而且相比于传统分析建模与优化相结合的方法,本文方法适用面更广,可根据不同目标模型在气动压力下的变形特点生成相应地框架约束结构,从而在气动系统的控制下达到预定的设计目标。由此,本文的方法适用于各种复杂结构的气动软执行机构的设计。软体驱动器由气动腔室、框架约束结构以及软材料所组成的驱动器的本体部分组成。气动腔室用于驱动软体驱动器的运动,框架约束结构用于控制驱动器的变形方向,软体材料构成的驱动器的本体部分用于传递驱动器的运动。在航空航天领域,对外形不规则目标的抓取需求越来越旺盛,需要软体驱动器的设计可以针对不同零件的抓取特点而做出相应的优化。因此,本文主要对框架约束结构进行设计和优化,从而更好地控制驱动器的变形,实现目标弯曲功能。
1 基于主应力线的软体驱动器设计
通过基于主应力线的软体驱动器的设计,得到驱动器的几何结构部分,包含气动腔室以及环绕气动腔室的框架约束结构。
1.1 技术路线
本文提出的基于主应力线的软体驱动器的设计主要包含两个部分:①框架约束结构设计;②框架材质优化与气动压力调节。具体思路(如图1)为:给定一个三维对象的初始形状S与目标形状So(图1a);通过仿真计算并提取仿真结果计算主应力线的方向,沿着主应力线方向生成框架约束结构(图1b);基于目标形状对框架约束结构的材质进行优化(图1c);最终得到优化后的模型,使用铸造的方法制造驱动器的本体部分,并通过3D打印框架约束结构,得到软体驱动器(图1d)。
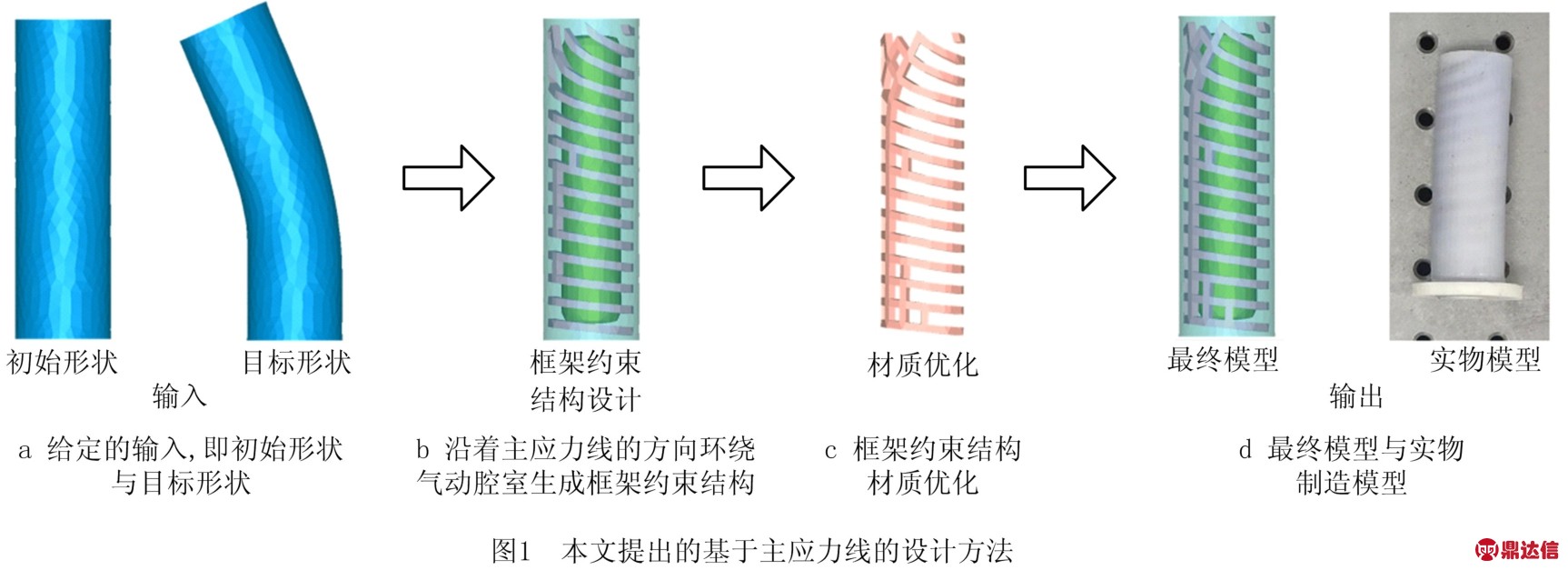
1.2 框架约束结构设计
1.2.1 主应力线方向的计算
图2a为软体驱动器的本体部分,此处设壁厚为d mm。在软体驱动器中,框架约束结构用于控制驱动器的变形方向,不同的变形方向对应不同的框架约束结构。为了保证框架约束结构可以很好地环绕气动腔室,首先环绕气动腔室插入框架约束结构生成面,并基于目标变形使用有限元仿真计算;根据仿真结果计算框架约束结构生成面的主应力线方向。
(1)通过偏置的方法得到框架约束结构生成面。将气动腔室向外偏置off-dis mm 得到框架约束结构生成面(如图2b)。根据初始形状表面网格S、气动腔室与框架约束结构生成面,使用约束四面体网格划分的方法得到四面体网格模型。根据得到的四面体网格模型,通过有限元仿真将初始形状S变形到目标形状So,并提取出框架约束结构生成面变形后的位置。由于此处有限元仿真的目的是为了得到变形后的框架约束结构生成面的变形情况,使用均一的超弹性材料,并使用Neo-Hookean模型作为材料变形准则。Neo-Hookean弹性模型定义如式(1)所示:
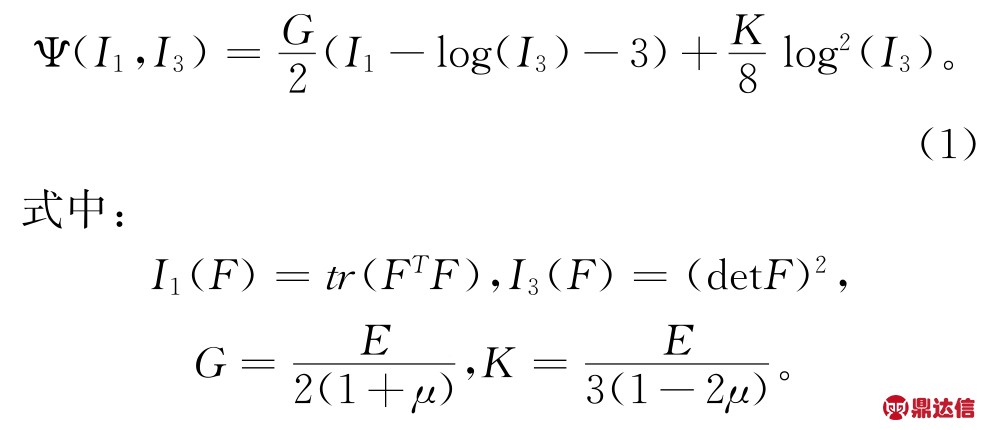
其中:F 是变形梯度,G 为剪切模量,K 为体积模量,E 为弹性模量,μ为泊松比,tr(·)用于矩阵的迹的计算,det()表示行列式计算。
(2)根据提取出的框架约束结构生成面变形后的位置,计算框架约束结构生成面(图2b)的主应变的方向,即主应力线的方向。首先计算框架约束结构生成面中每个三角面片的主应变方向,得到框架约束结构生成面的主应变场(如图2c)。计算方法如式(2)所示:

式中:vi1,vi2,vi3是框架约束结构生成面变形前每个三角面片的顶点坐标;vo1,vo2,vo3是对应的变形后的顶点坐标;A 是线性变换矩阵也就是变形梯度;T是平移矩阵。由于需要计算框架约束结构生成面的变形情况,需要根据变形前后每个三角面片的顶点坐标计算出线性变换矩阵A,即框架约束结构生成面上的每个三角面片的变形梯度。对得到的每个三角面片的变形梯度A 进行奇异值分解,其最大奇异值对应的特征向量方向即为三角面片的主拉伸方向(如图2c中的竖直矢量方向为主拉伸方向)。每个三角面片的主拉伸方向与垂直于主拉伸的方向共同组成了框架约束结构生成面的主应变场Field-principle-strain(如图2c)。
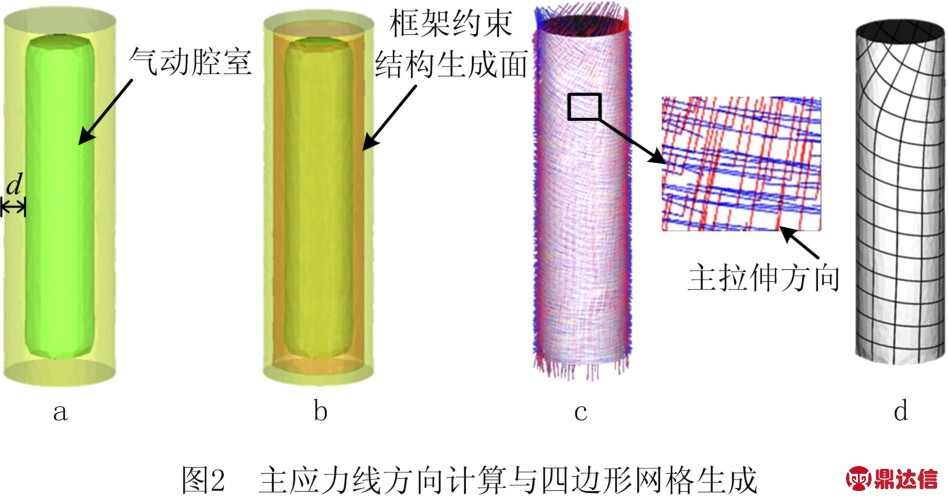
基于上述得到的框架约束结构生成面的主应变场,使用场引导[19]的方法生成四边形网格Quad-mesh(如图2d),作为实体框架结构生成的基础,此处假设四边形网格的边长为edge-length mm。
1.2.2 实体框架结构生成
基于生成的四边形网格Quad-mesh (如图2d),通过图3所示的方法生成如图4所示的实体框架结构,其中四边形网格的厚度为edge-thick mm。
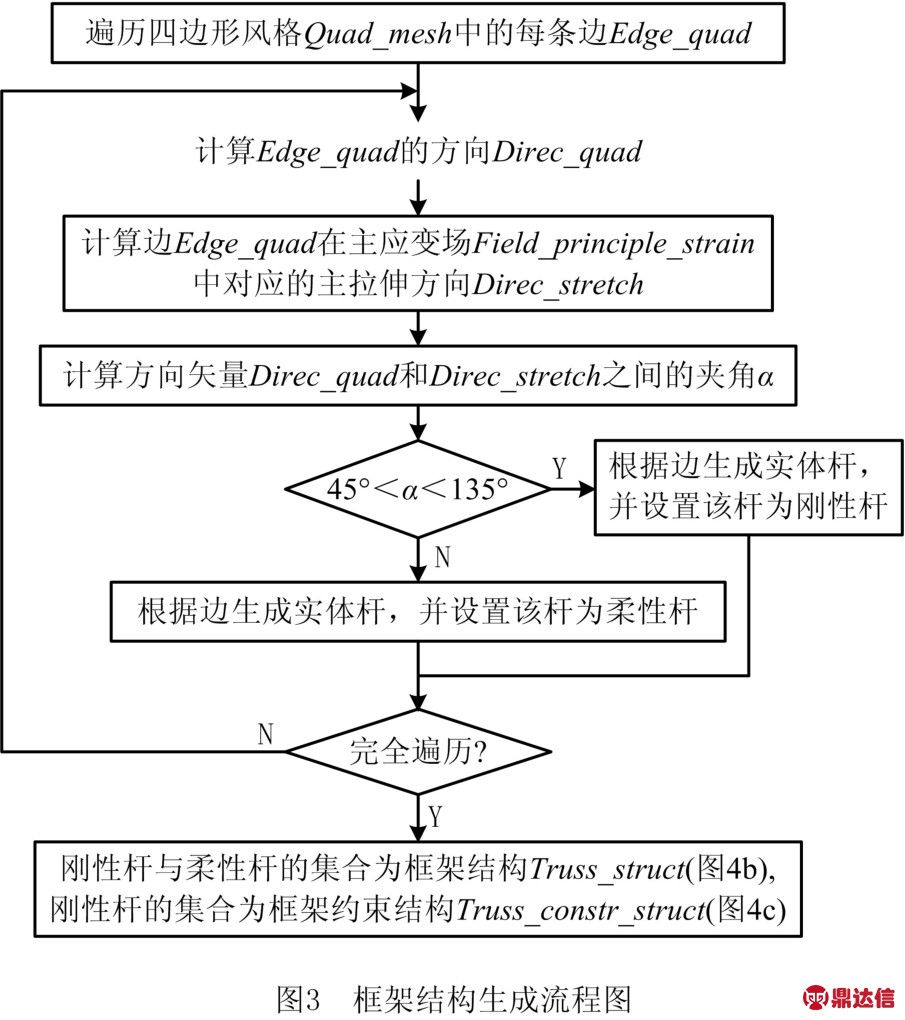
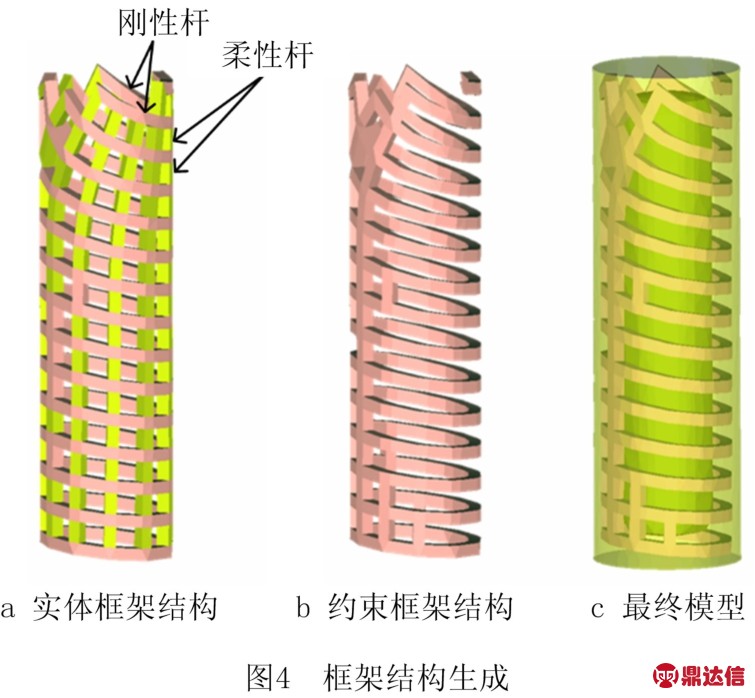
1.3 框架材质优化与气动压力调节
通过1.2节中的框架约束结构设计,得到驱动器的几何结构部分,包括气动腔室、框架结构。根据初始形状表面网格S、气动腔室与框架结构,使用约束四面体网格划分的方法得到四面体网 格 Tet-optimize。设置四面体网格Tet-optimize中框架结构以外的所有四面体单元为柔性材质,框架结构中刚性杆的材质为刚性材质,框架结构中柔性杆的材质为柔性材质。基于初始化材质后的驱动器仿真模型,设置气动腔室的初始压力P=0.036 Mpa。初始化模型后,通过调节框架结构材质与腔室气动压力,使得软体驱动器在腔室气动压力的驱动下变形到目标形状。调节方法如下:
(1)由于框架约束结构沿着垂直于主拉伸的方向,具有达到目标形状的趋势,通过改变气动压力P大小实现变形到目标形状。
(2)对于压力确定的情况,在当前框架约束结构的基础上,调节框架结构中每根杆的材质从而使初始形状达到目标形状。
(3)对于复杂的目标形状,可以结合(1)、(2)中方法进行调节。具体调节方法如算法1所示。
算法1中各变量定义以及算法流程为:通过仿真计算并提取仿真结果得到表面形状网格Sc,本文使用Sc与目标形状网格So 顶点之间的欧氏距离D-SctoSo来表示距离偏差Error-distance(式(3))。同时计算初始形状S与目标形状So 之间的欧式距离D-StoSo(式(4))、初始形状S与当前形状Sc之间的欧式距离D-StoSc(式(5))以及ΔD(式(6))。若ΔD >0,则增大腔室压力,否则减小腔室压力。根据式(8)调整压力,其中ΔP=0.005。
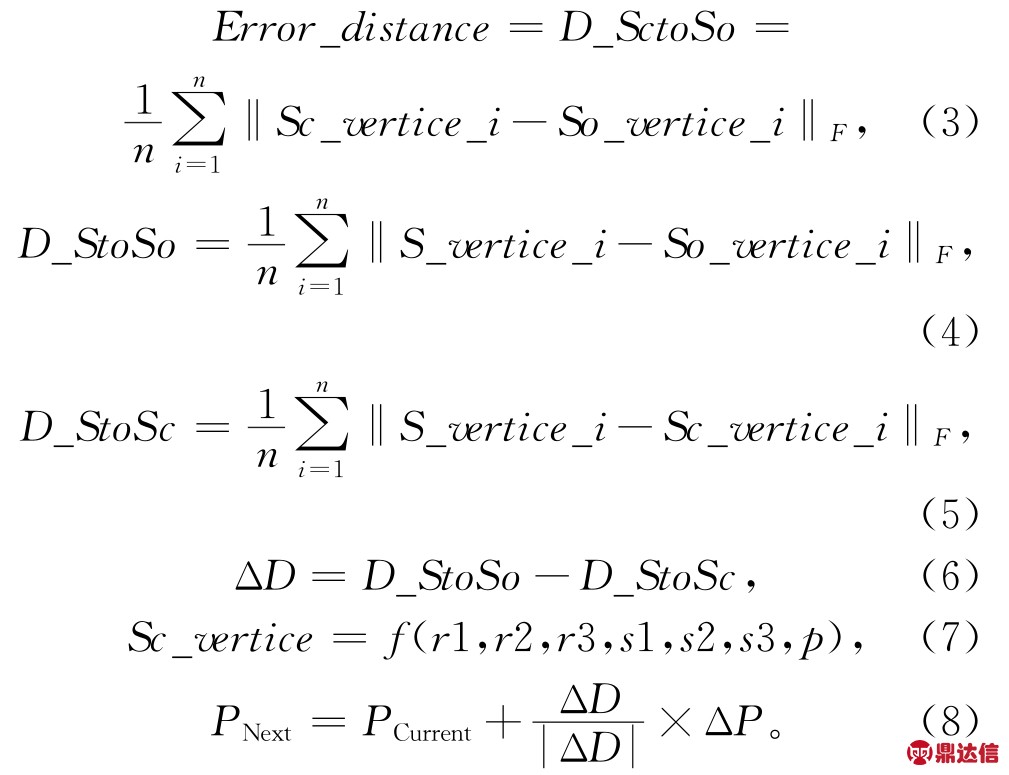
同时,将框架结构中的刚性杆和柔性杆分为两类。对于刚性杆,按照变形梯度的最小奇异值降序排列,并按序将刚性杆等分为3组,对应系数为r1,r2,r3,默认值为0;对于柔性杆,按照变形梯度的最大奇异值升序排列,并按序将柔性杆等分为3组,对应系数为s1,s2,s3,默认值为0。其中系数si,ri(i=1,2,3)对应于柔性杆和刚性杆中转变为刚性杆和柔性杆的比例大小。当ΔD >0时,使用式(9)调节;当ΔD <0 时,使用式(10)调节,其中Δsi=0.01,Δri=0.01。根据调节后的系数与压力,通过仿真分析求得变形后的形状表面Sc(式(7))。本文使用Sc与So之间的平均欧氏距离Error-distance作为目标函数(式(11)),当Error-distance <2.5 mm时,停止系数的调节,否则继续调节。
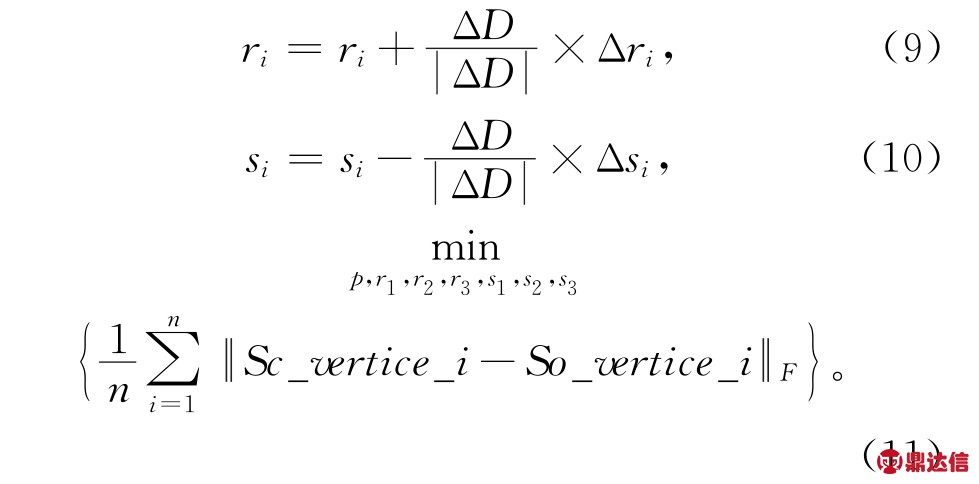
算法1
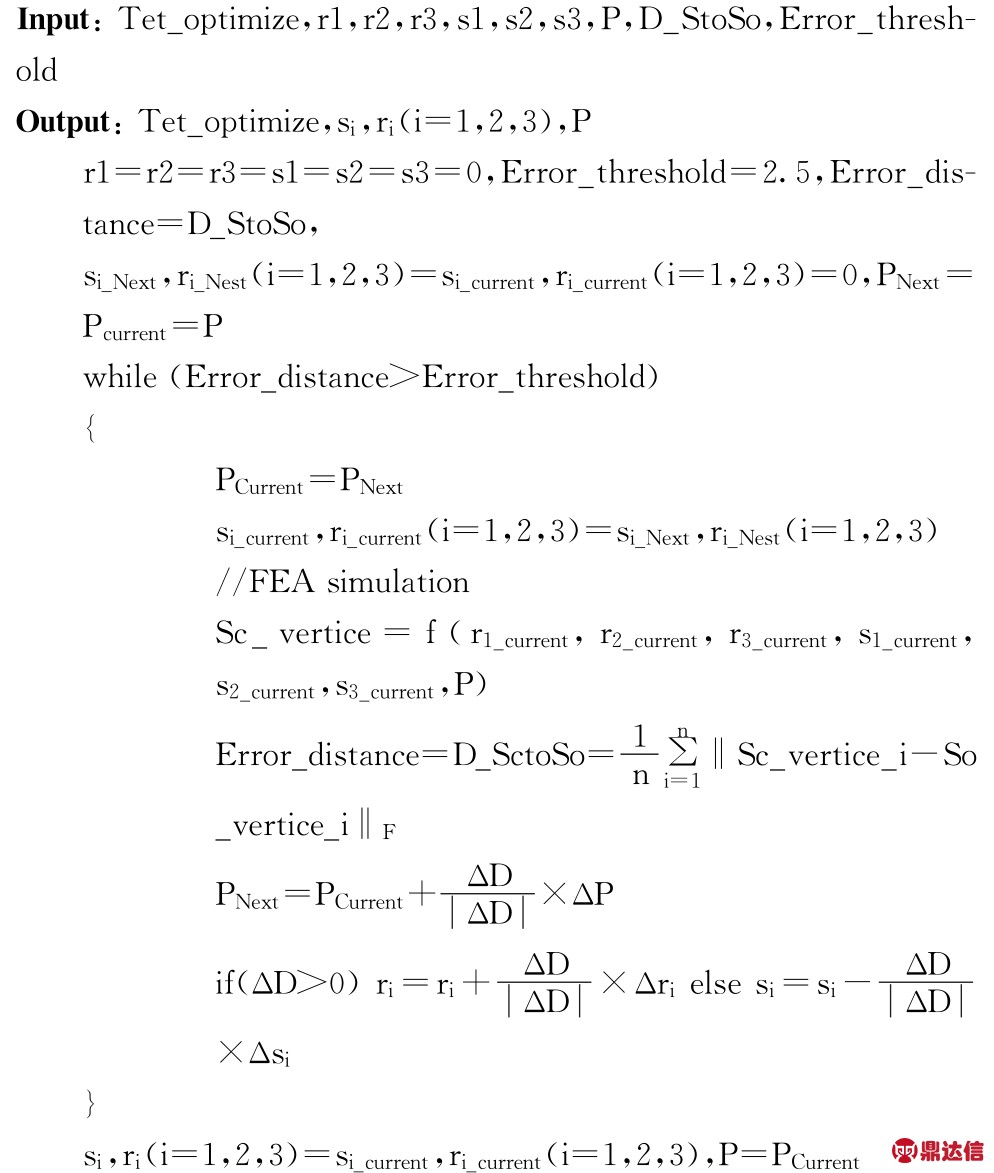
2 实验验证与分析
2.1 软体气动抓手设计与制造
本文设计了一个自适应能力较强的软体气动抓手,如图5所示,该抓手由3个软体驱动器组成,通过3个软体驱动器的弯曲变形完成各类抓取任务。
具体设计方法如下:①给定初始形状与目标形状;②基于目标形状使用以上设计方法生成框架约束结构;③对框架约束结构材质优化;④使用铸造的方法实物制造,并对3个软体驱动器以及辅助夹具装配,得到最终的软体气动抓手。
(1)为了实现抓取,软体气动抓手的每个软体驱动器在气动压力的驱动下实现有效弯曲。初始形状与目标形状如图6a和图6b所示,软体驱动器弯曲的目标设计点为P 点,当软体驱动器从初始形状弯曲到目标形状的时候,P 点的水平移动距离是16 mm,初始时3个软体驱动器的中心轴距离抓取中心o的水平距离为42 mm(如图5b)。软体驱动器对应的相关结构参数为d=4.5 mm,off-dis=2.5 mm,edge-length=5.5 mm,edge-thick=2 mm。
(2)根据(1)中的设计参数,通过基于目标变形的仿真得到框架约束结构生成面的主应变场,并在垂直于主拉伸的方向生成框架约束结构如图6c所示。选择ABAQUS/Standard求解器进行仿真计算,此处根据所使用的RTV-2 硅橡胶材料定义Neo-Hookean弹性模型材料参数:C10=0.11,D1=1.95。通过abaqus脚本处理添加相应的边界条件,将驱动器变形到目标形状。
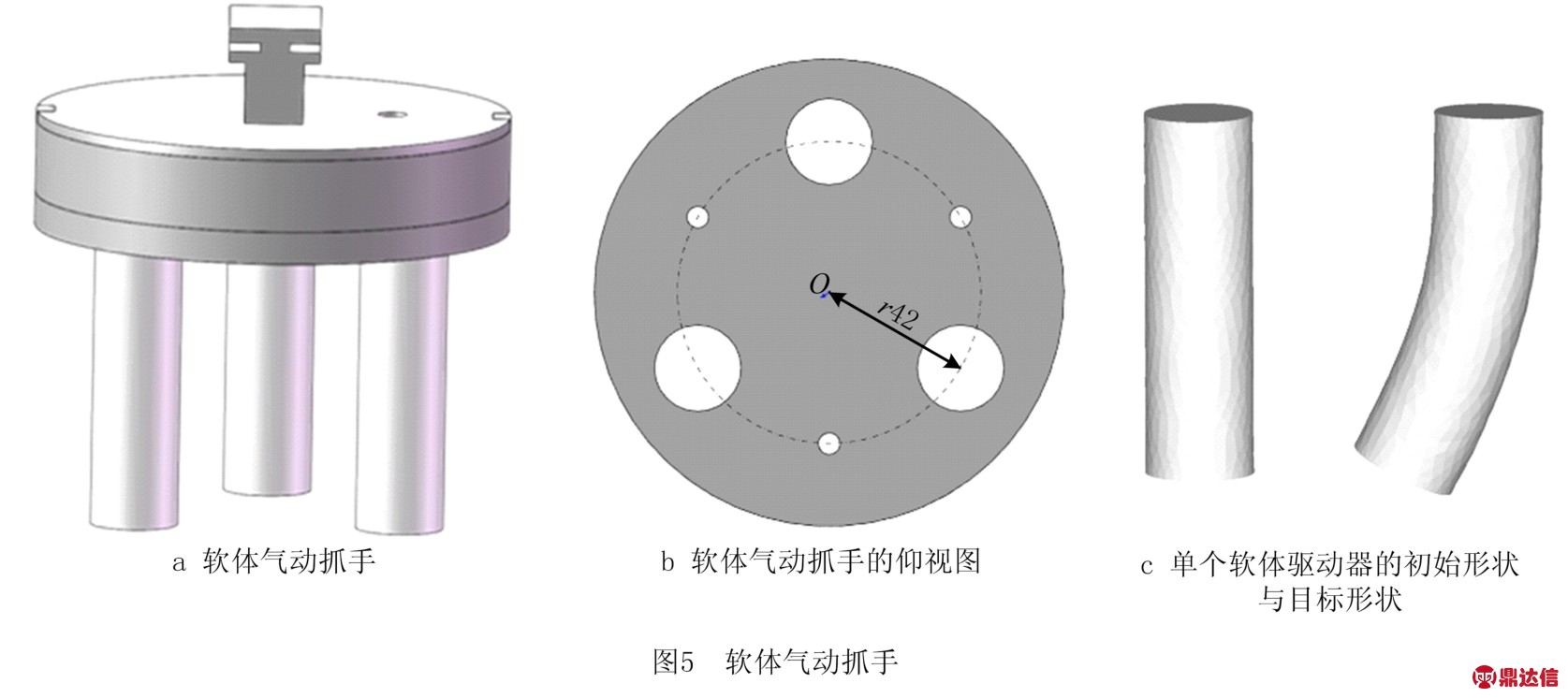
(3)通过1.2节中的框架材质优化与腔室气动压力调节的方法对框架约束结构材质与腔室气动压力进行调节(如图6d)得到最终的材质参数与气动压力,对应的气动压力和材质参数为s1=0.8,s2=s3=r1=r2=r3=0,P=0.12 Mpa。其中框架约束结构的材质为尼龙(PA12),对应的材质参数包括:弹性模量E=1 646 Mpa,泊松比μ=0.4,软体驱动器的本体材料为RTV-2硅橡胶,材料参数与(2)中相同。图6f为最终材质参数与气动压力下通过有限元仿真计算得到的变形形状。

(4)由于软体驱动器的本体材料为RTV-2硅橡胶,使用铸造的方法制作本体部分;框架约束结构需要有一定的刚度和良好的韧性,因此选用尼龙材料(PA12),并使用激光烧结(Selective Laser Sintering,SLS)的方法打印框架约束结构(如图8c)。框架约束结构生成面是框架约束结构的对称面,因此以框架约束结构生成面为对称中心,将软体驱动器分成内部和外部两部分分步铸造。如图7所示为铸造模具与框架约束结构。具体铸造步骤如图8所示。
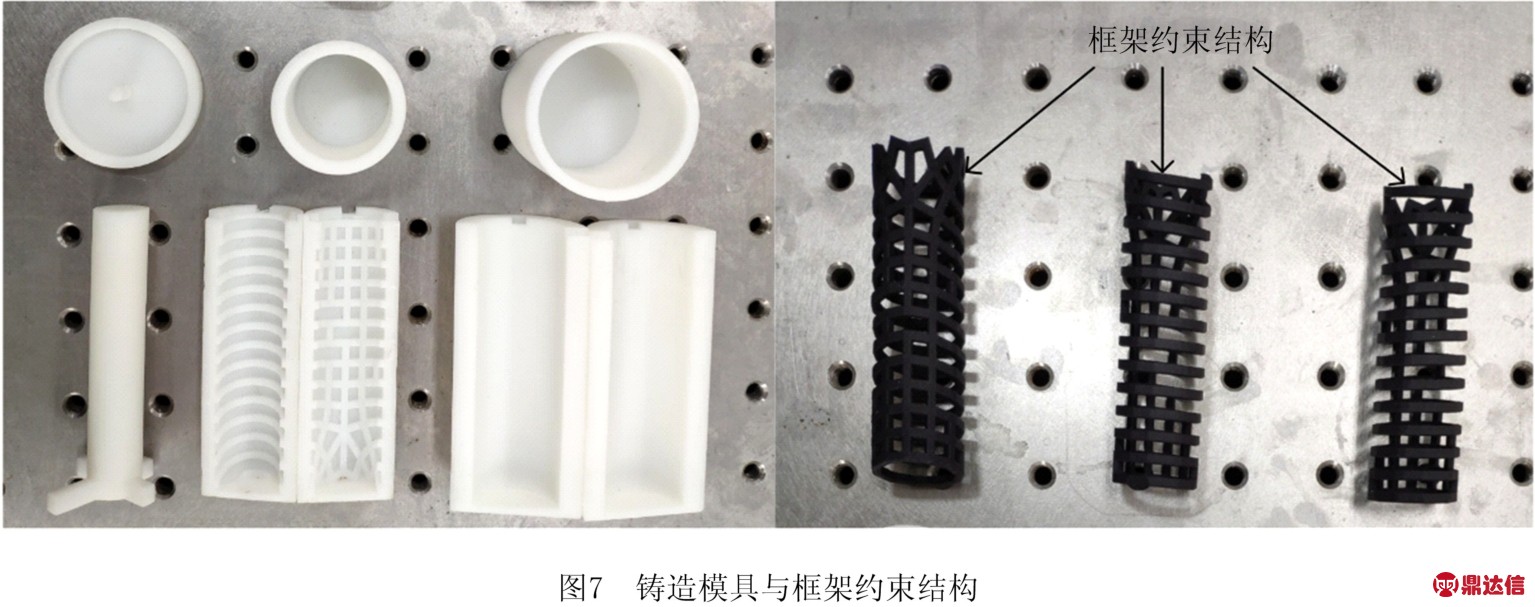
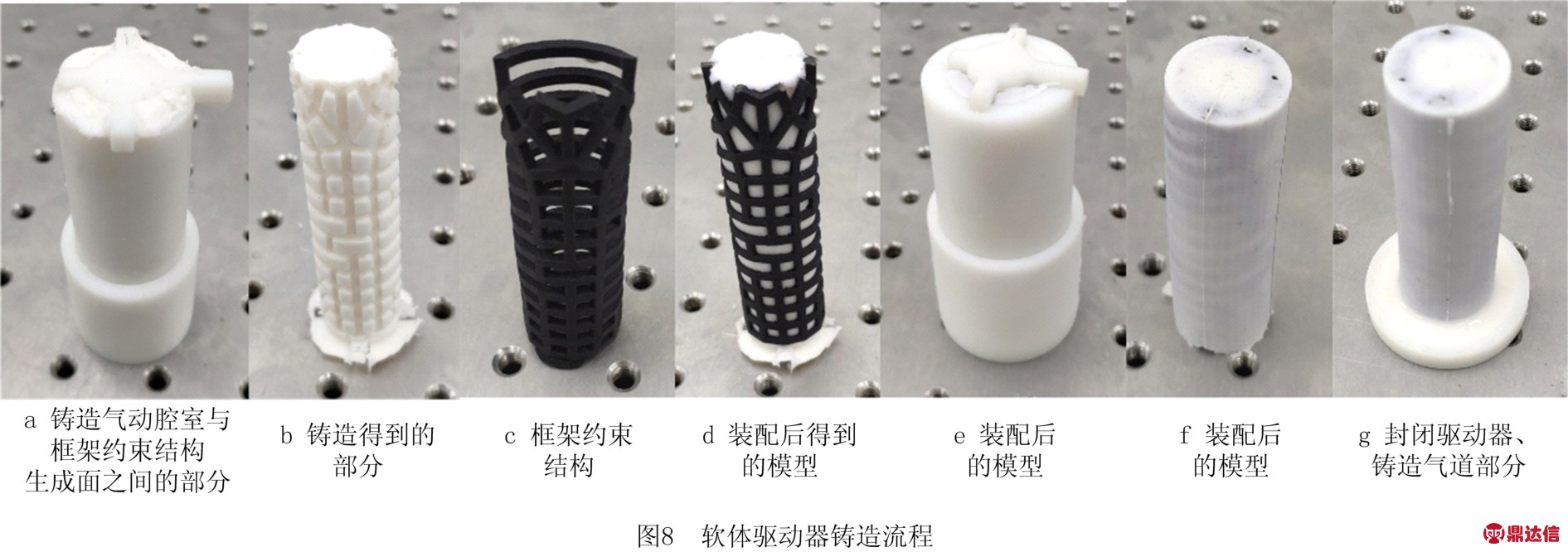
2.2 抓取实验与分析
如图9所示为软体气动抓手装配零件与单个软体驱动器的变形实验。气泵通过四通与软体气动抓手的3个软体驱动器相连接,在同一气压下,3个软体驱动器的变形相同。2.1节中,当软体驱动器的气动压力P=0.12 Mpa时,软体驱动器末端的目标水平位移为16 mm,如图9b所示为软体驱动器的初始状态,如图9c所示为气动压力P=0.12 Mpa时,软体驱动器的变形情况,末端位移为14.5 mm,与目标水平位移的偏差为1.5 mm。
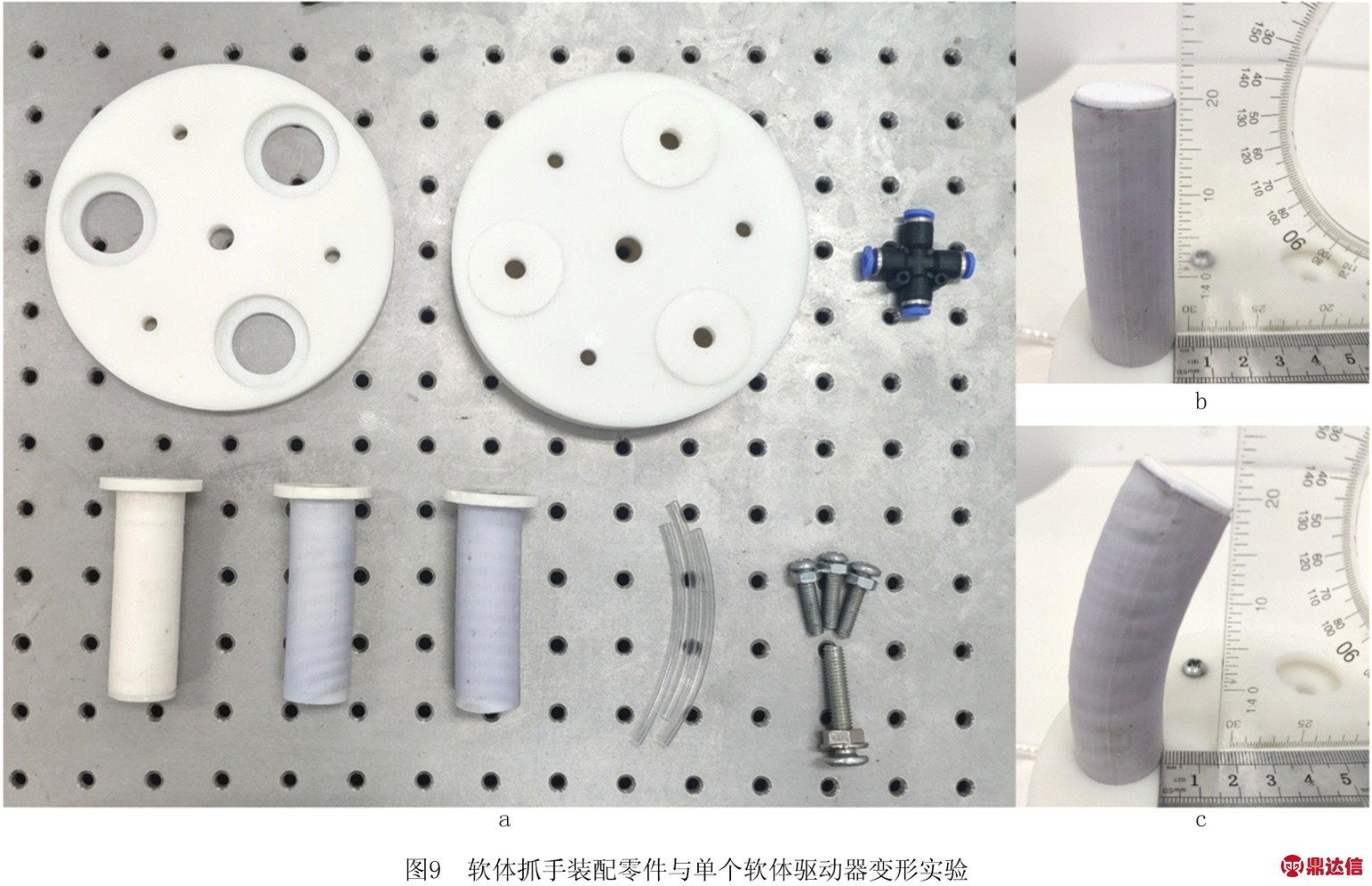
由图5b可知该软体气动抓手可抓取物体的最大半径为30 mm;通过在矿泉水瓶中加水并调节腔室气压的方法测试该抓手的最大抓取质量,如图10h所示,该软体气动抓手的最大抓取质量为0.58 kg。
同时,通过在烧杯中逐渐添加重物的方法测试不同气压下所能抓取的最大质量。如图11a所示,本文在烧杯中逐渐添加金属片测试,实验结果如图10b所示,该抓手所能抓取的重物质量与气动压力近似线性相关。
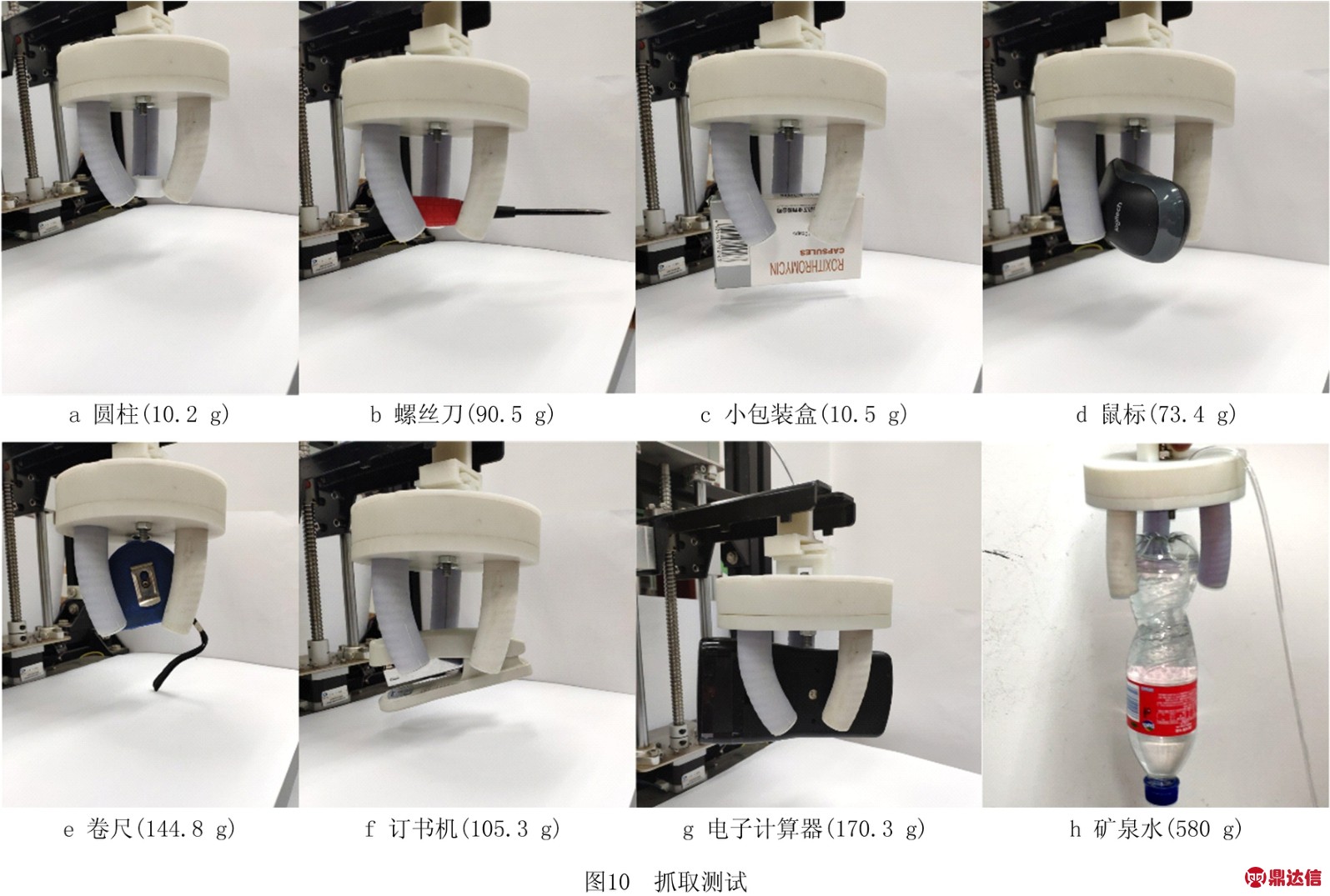
对不同形状和质量的对象抓取实验(如图10)。抓取实验结果表明该软体气动抓手具有良好的自适应性,能够抓取小尺寸、较大尺寸的小质量物品。该软体气动抓手的抓取能力取决于其中的每个软体驱动器的驱动能力,软体驱动器的驱动能力取决于其本体材料、长度、壁厚、截面形状、接触面、摩擦系数、可承载的最大气压值、框架约束结构的密度和分布、框架约束结构杆的厚度。通过控制软体驱动器的相关结构、材质设计参数,可以实现具有不同刚度的软体气动抓手的设计。
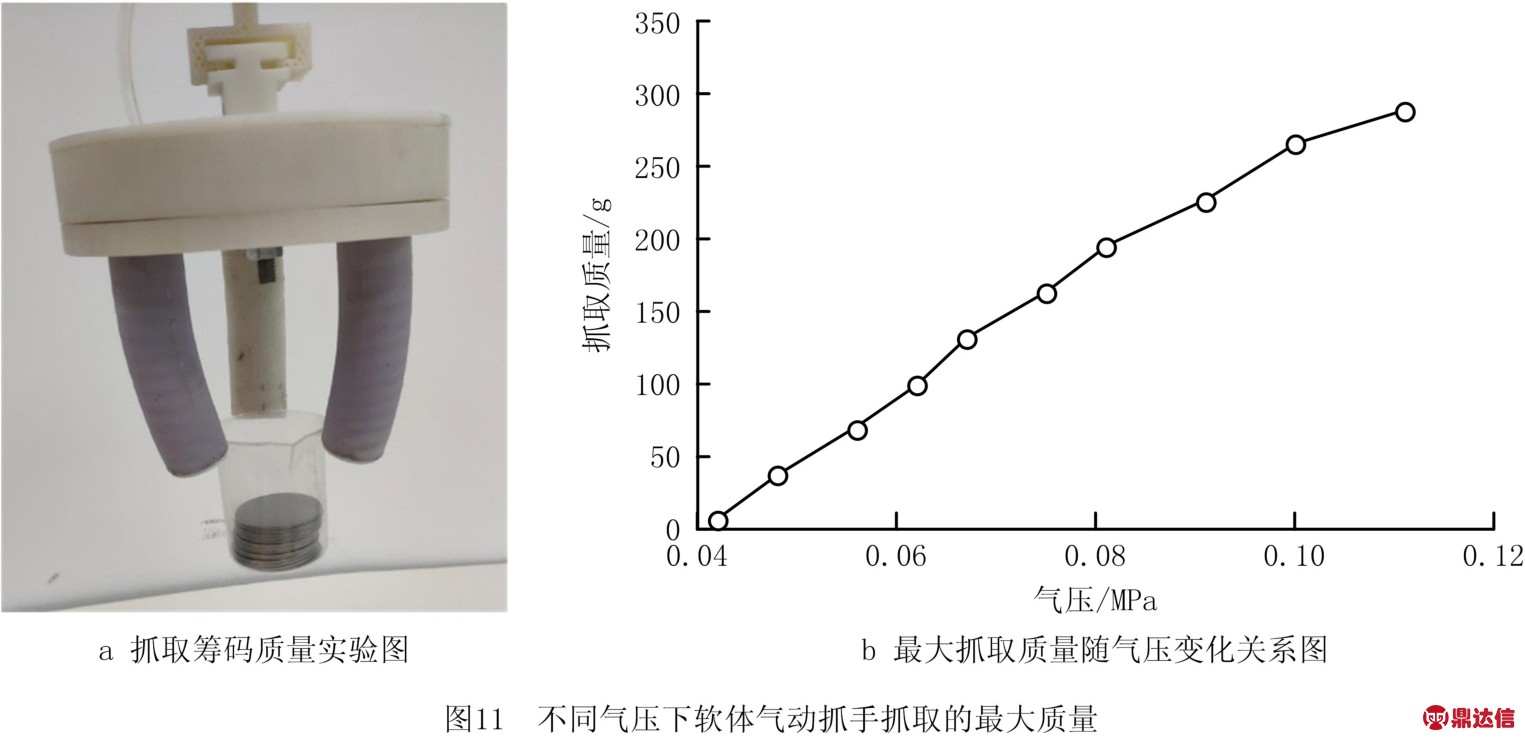
3 结束语
本文提出一种新型的软体驱动器设计方法,可以实现目标弯曲变形。基于给定的目标形状,通过有限元仿真并计算主应力线的方向,沿着主应力线的方向生成框架约束结构;基于目标形状通过启发式的方法优化框架约束结构的材质,并通过3D 打印与铸造的方法制作框架约束结构与软体气动驱动器的本体部分。沿着主应力线的方向生成的框架约束结构,与驱动器变形时的变形方向具有一定的一致性,因此驱动器在气动压力的作用下具有变形到目标形状的趋势。通过软体驱动器的弯曲实验测定软体驱动器的变形精度为2 mm~3 mm。基于本文的软体驱动器,设计了软体气动抓手,并进行抓取实验。实验结果表明该软体气动抓手具有很好的自适应性,能够实现对不同形状对象的自适应抓取。该抓手能够抓取0.6 kg左右的物品,可用于中小物品的抓取。未来将在本文单腔室多材料模型设计方法的基础上,对具有多腔室结构的驱动器从几何建模、材料分布、气压优化及制造方法等方面进行拓展研究。