摘要:采用实验测量和数值模拟的方法,研究了单独切向进气蜗壳和切向进气蜗壳耦合静叶结构的气动性能和流场特性。实验测量了3种出口马赫数下的单独切向进气蜗壳和4种进出口压比下的切向进气蜗壳耦合静叶结构的总压损失系数、出口气流角、质量流量。采用数值求解三维RANS和SST湍流模型分析了实验测量的切向进气蜗壳的流场形态。数值模拟得到的气动参数值与实验值吻合良好,验证了数值方法的可靠性。结果表明:单独切向进气蜗壳与切向进气蜗壳耦合静叶结构的出口气流角的分布与大小基本上不随进气总压的增加而改变,出口气流角在152.0°左右,切向进气蜗壳耦合静叶结构的出口气流角在166.6°左右;与单独切向进气蜗壳相比,切向进气蜗壳耦合静叶结构的出口气流角沿周向的分布更为均匀;单独切向进气蜗壳和切向进气蜗壳耦合静叶结构的总压损失系数和质量流量随着进气总压的增加而增加,单独切向进气蜗壳的总压损失系数由0.73%增加到1.64%,切向进气蜗壳耦合静叶结构的总压损失系数由0.82%增加到2.66%。研究工作可为汽轮机切向进气蜗壳的设计和性能分析提供参考。
关键词:汽轮机;切向进气蜗壳;气动性能;流场形态
汽轮机通流部分热功转换效率随高性能三维叶片设计技术的提高而提高。由于叶栅通道的设计历来受到各国的重视,经过长时间优化的叶栅通道的气动效率已经很难再提高,因此人们逐渐把目光投向了从主气阀到凝气器之间的管道、蜗壳以及蜗壳与叶栅耦合时的气动性能的提高[1]。对于大功率汽轮机的高压进气部分和低压排气部分,其气动性能的提高与优化对提高汽轮机的经济性有着非常大的作用[2]。目前,低压缸的第1级效率远低于其他级的效率[3],导致整缸性能大幅降低。为了提高进排气部分的气动效率,必须更加细微地掌握汽轮机进排气部分的流动机理[4]。
汽轮机进气蜗壳的气动参数分布和流场形态直接影响其下游通流的气动性能[5],掌握进气蜗壳的气动参数、流场形态以及损失产生机理,是进一步提高汽轮机热功转换效率的关键[6]。汽轮机进气蜗壳的设计对汽轮机组效率的影响主要体现在两个方面:一是进气蜗壳内部的气流组织形式造成的损失;二是进气蜗壳出口气流的角度与均匀性和静叶的匹配情况[7]。有研究表明,采用切向进气方式,并且根据蜗壳出口气流角匹配静叶叶型,可以提高低压缸第1级叶片的效率。
随着汽轮机通流精细化设计和实验数值手段的发展,科研人员对汽轮机进气蜗壳的气动性能和流场形态,以及对下游通流的影响特性开展了系统研究。李成勤等数值研究了1 000 MW超超临界汽轮机中压缸进气蜗壳的流场形态及其对下游静叶气动性能的影响,结果表明进气蜗壳具有左右对称和上下呈现高低压的流场特性,并导致下游静叶内总压在周向具有不均匀分布的特征[8]。Hecker等采用实验测量和数值模拟的方法研究了左右切向底部进气蜗壳的气动性能,指出进气预旋流动增加了蜗壳流动损失和下游静叶的攻角损失[9]。张怀宇等数值对比分析了1 000 MW汽轮机直接进气蜗壳和切向进气蜗壳在设计负荷和75%低负荷工况下的气动性能,结果表明全周进气结合补气结构能够提高进气蜗壳的流场均匀性,进而提高汽轮机进气段的气动效率[10]。
姚宏等基于实验测量的工业汽轮机补气结构模型,数值研究了不同补气结构的总压损失的影响特性,指出所设计的椭圆形且沿周向截面面积逐渐缩小的补气结构,可通过有效控制蜗壳周向密流分布而减少总压损失[11]。王健等的数值结果表明:相比于传统进气结构,新设计的螺旋形切向进气蜗壳结构具有总压损失小和出口流场均匀度高的优势,能够保证汽轮机通流的气动效率[12]。钟主海等针对切向进气蜗壳结构的数值研究表明,切向进气蜗壳的通流截面的收缩比、截面形状以及进口管横向间距均影响其气动性能,总压损失系数和湍动能随着进气蜗壳通流截面收缩比的增加逐渐减小并趋于平缓,截面形状和进口管横向间距对切向进气蜗壳的总压损失影响有限[13]。邵卫东等优化设计了进气管道和蜗壳连接处结构,通过增大进气弯管的出流面积和倾角、减小滞止涡来减小气流角的不均匀度,进而实现了提高进气结构的气动效率[14]。Kang等数值研究了汽轮机级间进气结构对其气动性能的影响,结果表明进气结构出口流场不均匀性增加了下游静叶的气动损失,降低了通流部分的气动效率[15]。潘阳等采用数值模拟的方法研究了部分进气结构对汽轮机进气损失的影响,指出进气不均匀性明显降低气动效率[16]。王世超等研究了中排至低压缸的进气管道,通过增加进气管道直径,保持管道的直径前后一致,并在低压缸拐角处增加倒角,有效地减小了进气管道部分的阻力系数[17]。陈立德则对常用的管道流阻计算经验公式如何应用在燃气轮机进气系统中作了全面分析,给出了沿程阻力和局部阻力的计算方式以及误差[18]。
为了进一步提高汽轮机的热功转换效率,必须对汽轮机进气蜗壳结构的流场形态和气动参数分别进行研究,以降低总压损失和提高出口流场的均匀性。本文采用实验测量和数值模拟的方法研究了切向进气蜗壳的气动参数分布,开展了单独切向进气蜗壳和切向进气蜗壳耦合静叶结构在不同进口总压下的流场形态和损失特性研究,可为切向进气蜗壳的设计和性能分析提供参考。
1 模型和数值方法
1.1 实验测量
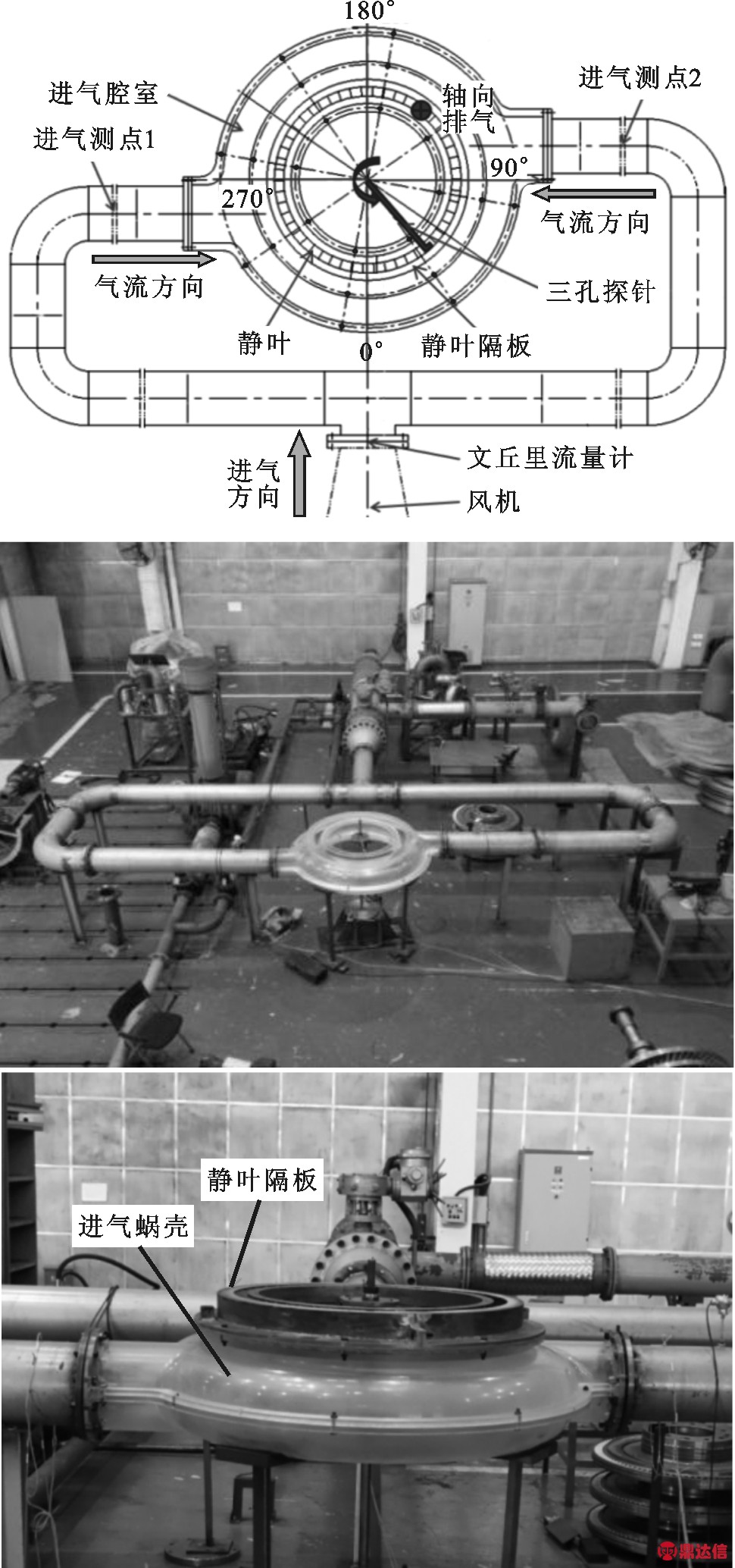
图1 进气蜗壳气动性能实验系统
图1给出了进气蜗壳气动性能实验测量系统图。压缩空气从压气机出来经过管道、阀门和文丘里流量计后,从进气蜗壳两侧的管道进入蜗壳。进气蜗壳水平放置,垂直向上排气,通过进气阀和风机放空阀调整进气压力改变实验工况。进气蜗壳采用有机玻璃进行加工制造,其圆环部分外径约1.5 m、内径为0.84 m,进气管直线段长度为2.1 m。进气蜗壳出口下游整圈共有50只静叶,根径为842 mm,轴宽为62.3 mm,由金属加工制造,并由大带冠结构在根顶部少量焊接后与进气蜗壳装配成一体。
实验气源采用2 500 kW风机,最大出口压力为273 kPa,最大进气量为1 800 m3/min。温度测量采用A级铂热电阻,精度为0.15 ℃±0.002t;压力测量采用压力扫描阀(PSI),精度为0.05%;流量测量采用BYW-DT/14-806型短式文丘里管,精度为0.5%。实验测量过程中采用了三孔探针,将其一端固定在蜗壳出口面的圆心上,通过绕轴旋转测量蜗壳出口或静叶出口不同周向位置处的出口气流角、总压和静压。
本文对单独进气蜗壳和进气蜗壳耦合静叶结构进行了气动性能的实验测量。表1和表2分别列出了单独进气蜗壳结构实验的3个工况和进气蜗壳耦合静叶结构实验的4个工况。
表1 单独进气蜗壳结构实验工况
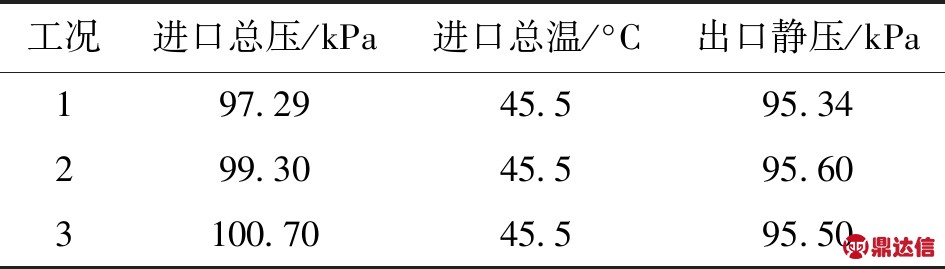
表2 进气蜗壳耦合静叶结构实验工况
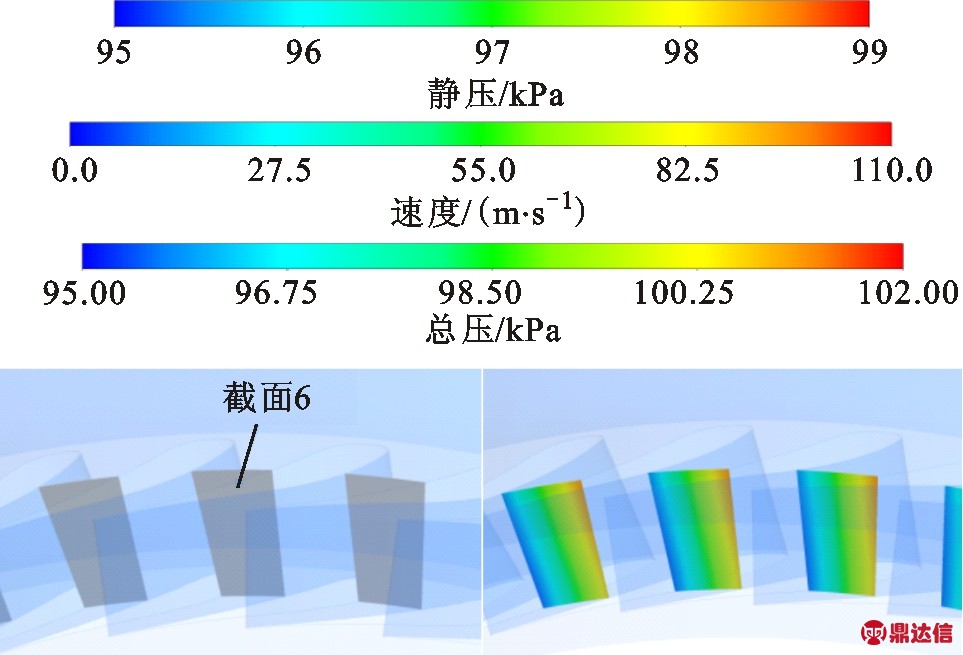
1.2 数值方法
图2给出了单独进气蜗壳结构的计算模型和网格图,进气蜗壳腔室采用ICEM生成非结构化计算网格,网格数约549万,壁面网格边界层数为20(首层高度为0.000 1 mm,膨胀比为1.2)。图3给出了进气蜗壳耦合静叶结构的计算模型和叶栅网格图,静叶由NUMECA生成结构化计算网格,整圈静叶网格数为609万。
本次数值模拟进行了单独进气蜗壳结构3个工况和进气蜗壳耦合静叶结构4个工况的计算,在7个工况中蜗壳和叶栅通道壁面y+均在2之内,满足SST湍流模型的要求。
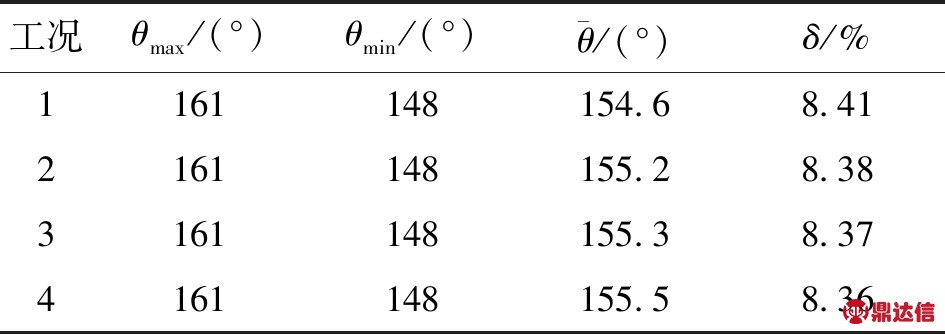
图2 单独进气蜗壳结构的计算模型和网格图
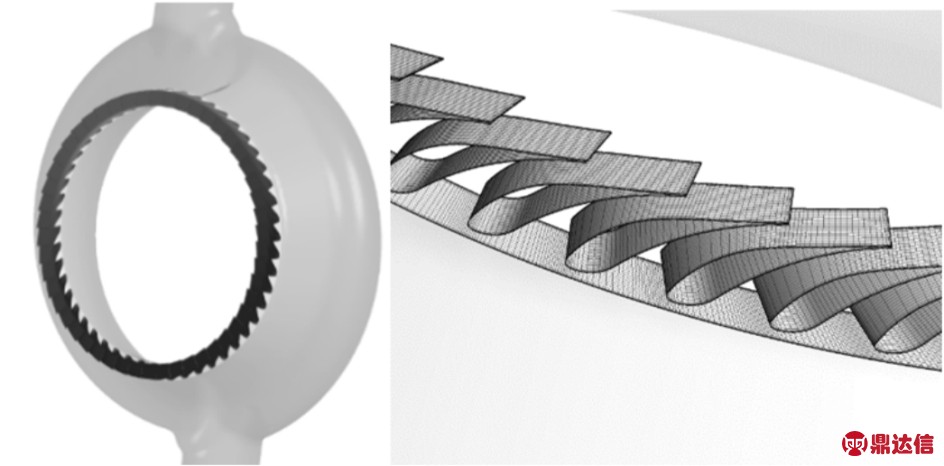
图3 进气蜗壳耦合静叶结构的计算模型和叶栅网格图
1.3 数值方法验证
采用ANSYS-CFX软件数值求解三维RANS方程和SST湍流模型,研究了实验测量的单独进气蜗壳和进气蜗壳耦合静叶结构的气动性能和流场,边界条件采用对应实验工况下测量得到的进口总压、总温和出口平均静压,壁面边界条件设置为光滑无滑移边界。总压损失系数计算式为
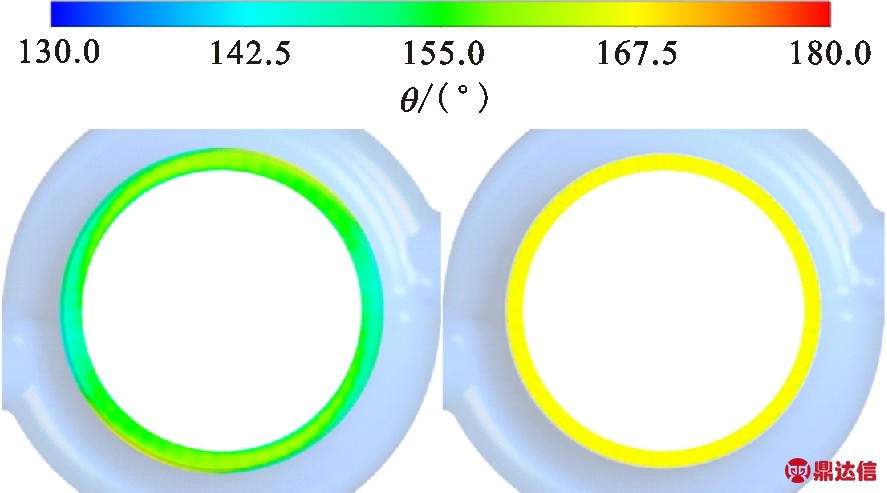
(1)
式中:p2T是出口总压;p0是进口总压。
出口气流角不均匀系数计算式为
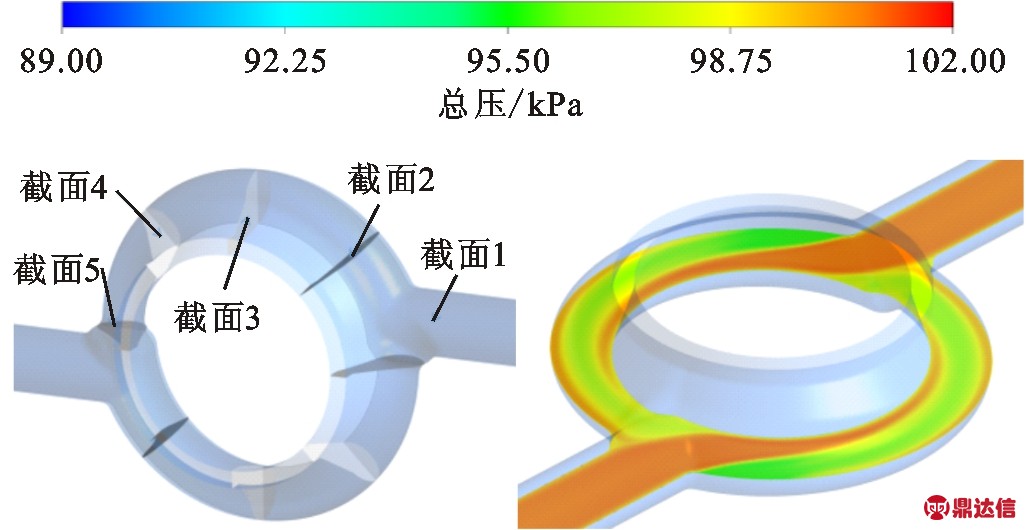
(2)
式中:θmax是出口截面不同周向位置的出口气流角最大值;θmin是出口截面不同周向位置的出口气流角最小值;是出口截面的出口气流角质量加权平均值。
针对单独进气蜗壳结构,采用251万、360万、439万和549万4套网格数进行网格无关性验证。图4和图5分别给出了单独进气蜗壳的总压损失系数和出口马赫数随计算网格数的变化曲线。根据计算结果,本文针对单独进气蜗壳结构选取的计算网格数为549万。图6和图7给出了在单独进气蜗壳结构中分别采用SST、k-ε和k-ω三种湍流模型计算得到的出口马赫数和总压损失系数与实验值的对比,SST模型计算结果比其他湍流模型更接近实验值,因此本文选取SST湍流模型进行进气蜗壳气动性能和流场特性数值计算分析。由图6和图7还可看出,出口马赫数与总压损失系数均随进口总压的增大而增大。
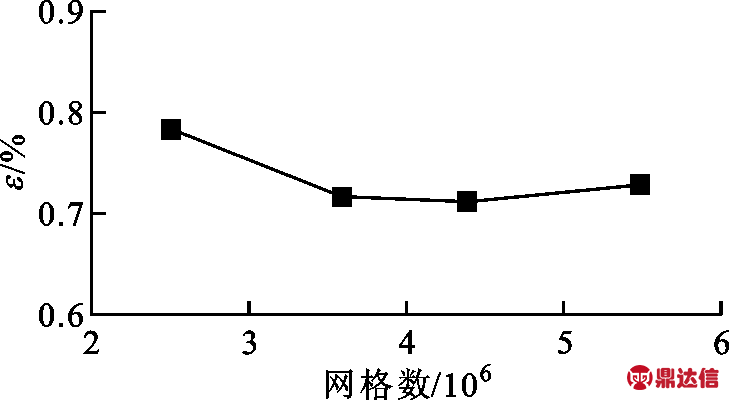
图4 单独进气蜗壳总压损失系数网格无关性验证
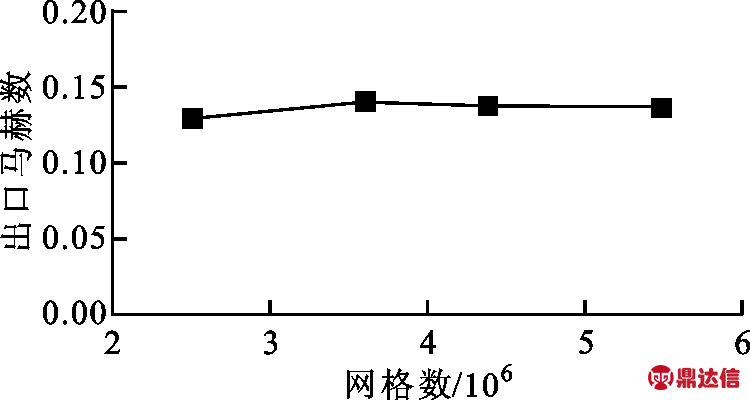
图5 单独进气蜗壳出口马赫数网格无关性验证
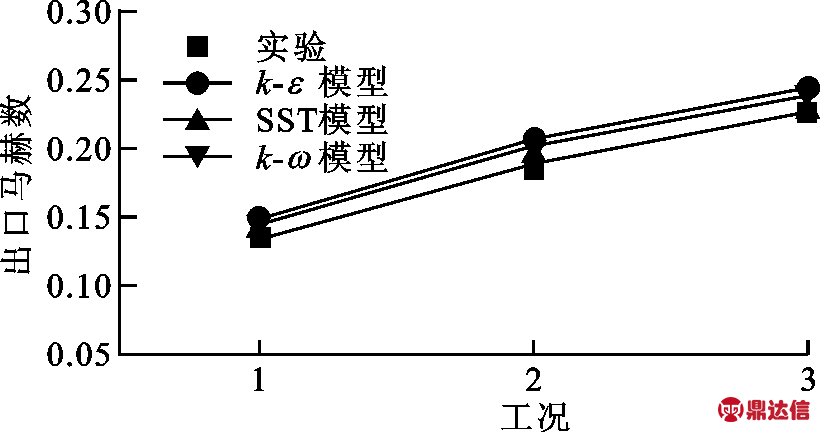
图6 采用不同湍流模型得到的单独进气蜗壳出口马赫数计算值与实验值的对比
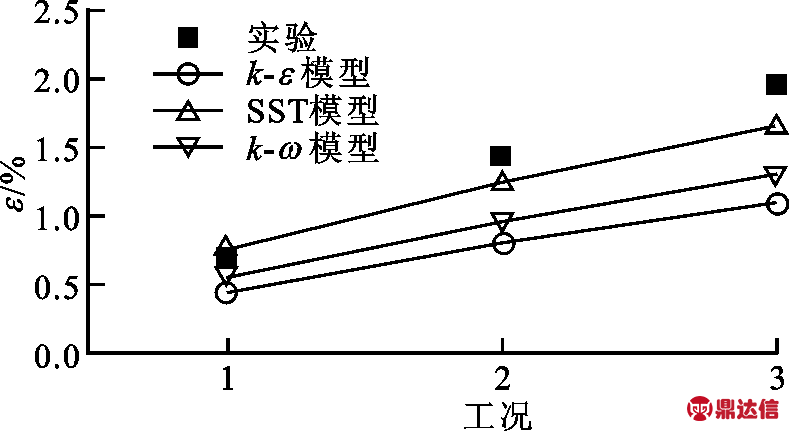
图7 采用不同湍流模型得到的单独进气蜗壳总压损失系数计算值与实验值的对比
2 结果分析
2.1 单独进气蜗壳气动参数
针对实验测量得到的单独进气蜗壳结构在表1所示的3种工况下的气动参数,结合数值模拟计算结果进行分析。图8和图9分别给出了单独进气蜗壳平均出口气流角和质量流量随出口马赫数的变化。由图可知:单独进气蜗壳平均出口气流角几乎不随出口马赫数的增加而改变;质量流量随出口马赫数的增加而增加。模拟结果显示随着进口总压的增加,即随着出口马赫数的增加,质量流量由4.04 kg/s增加到6.72 kg/s。单独进气蜗壳出口总压会随着进口总压的增加而增加,实验过程中不同工况下当地大气压对出口静压的影响可以忽略。由于出口总压增加而出口静压不变,故出口气流轴向速度增大,而在出口面积不变的条件下,质量流量随着出口轴向速度的增大而增大。
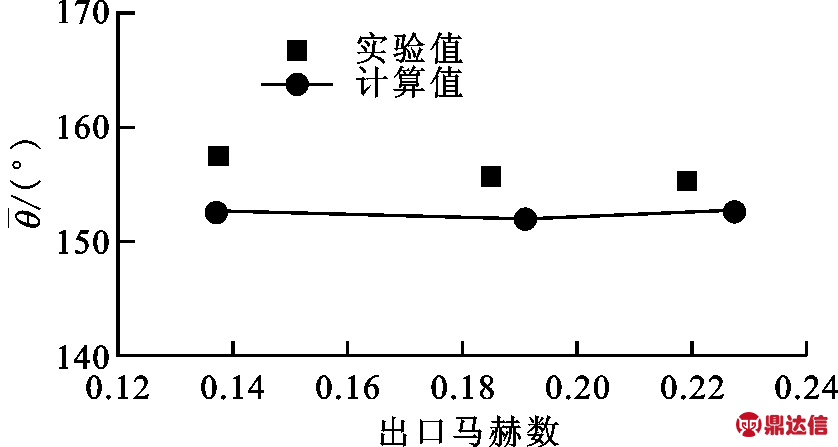
图8 单独进气蜗壳平均出口气流角随出口马赫数的变化
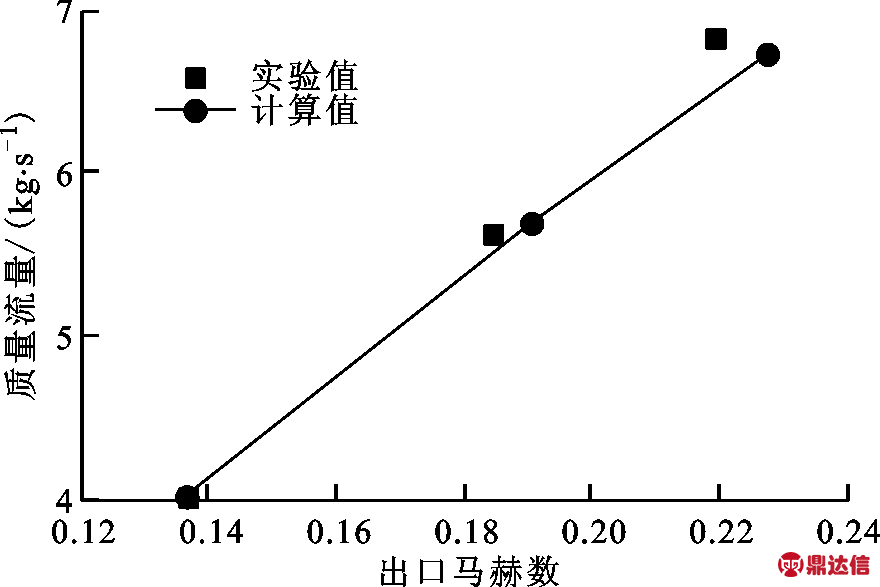
图9 单独进气蜗壳质量流量随出口马赫数的变化
图10给出了3种工况下单独进气蜗壳出口截面气流角沿周向的分布,实验与数值模拟得到的出口气流角沿周向分布规律吻合一致。3种工况下,出口气流角都在靠近进口位置时最小,距离进口越远时出口气流角越大。表3给出了单独进气蜗壳在3种工况下的出口气流角不均匀系数,其值均在20%左右。
表3 单独进气蜗壳出口气流角不均匀系数
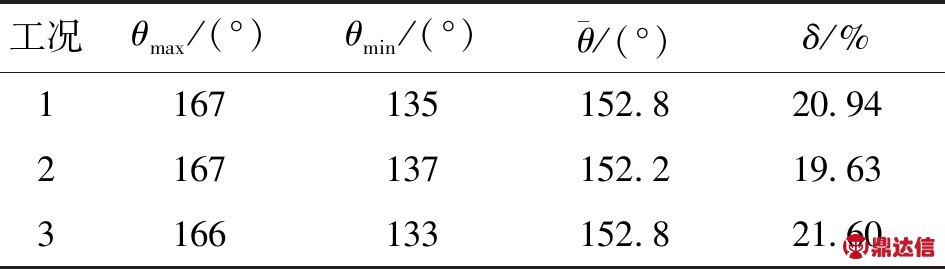
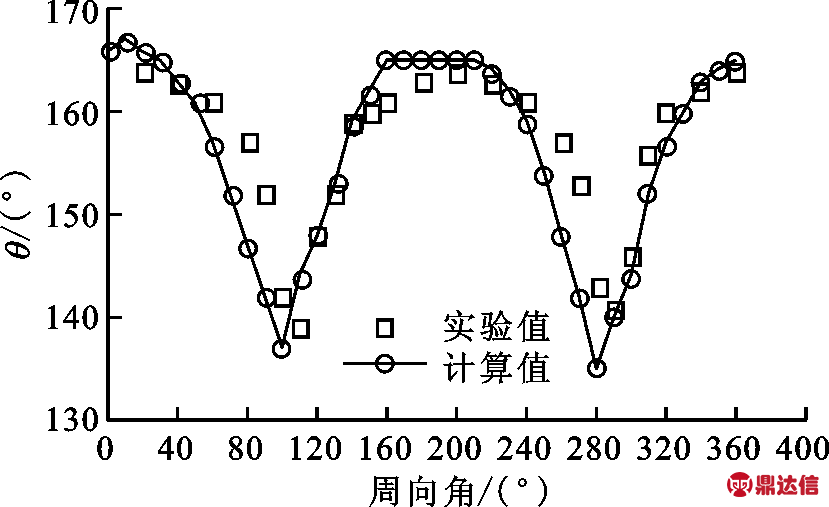
(a)工况1
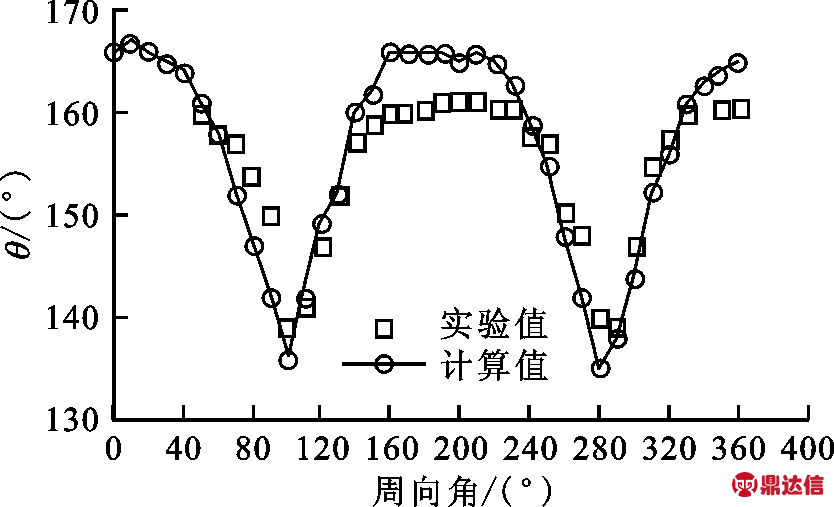
(b)工况2
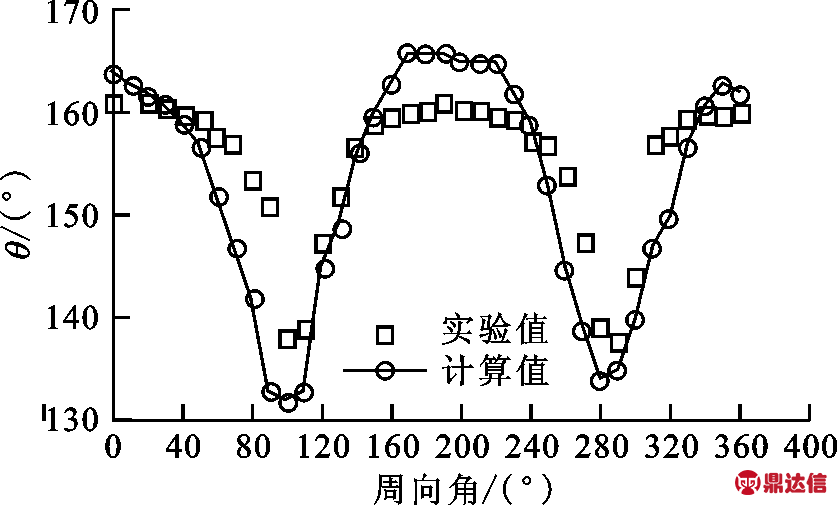
(c)工况3
图10 3种工况下单独进气蜗壳出口气流角沿周向分布
2.2 单独进气蜗壳流场
图11给出了3种工况下单独进气蜗壳的三维流线和出口截面静压等值线云图。由图可知,随着进口总压的增加,蜗壳内部流线基本未发生变化,因此出口气流角几乎没有随着进口总压的增加而变化。同时,由于切向进气,气流受离心力作用,在蜗壳出口截面形成了蜗壳外径压力高、内径压力低的分布情况,但压力沿周向的分布非常均匀。
由图11右边的流线图可知,进气管流入的气流在靠近蜗壳内壁和外壁处有着不同的流线,靠近蜗壳内壁的气流流线没有漩涡,流程较短,并且在靠近进气管的蜗壳下游出口排出。由于此部分气流沿蜗壳周向流程较短,周向分速度较小,导致进气管附近的蜗壳出口气流角较小。靠近蜗壳外壁的流体会在蜗壳下游产生漩涡,流程增加,甚至与另一个进气管流入的气流混合。由于此部分流体流过的周向距离较长,周向分速度较大,所以两个进气管中间的蜗壳出口气流角增大。
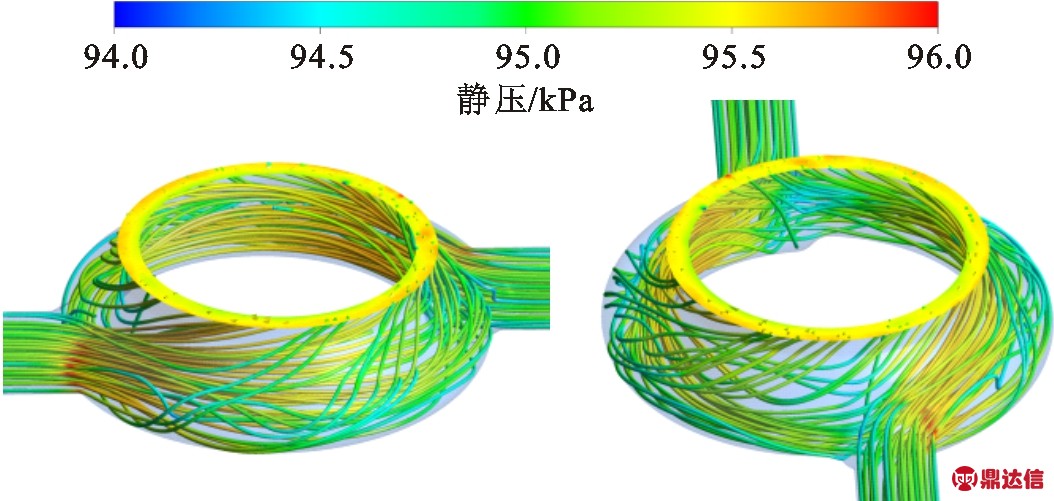
(a)工况1
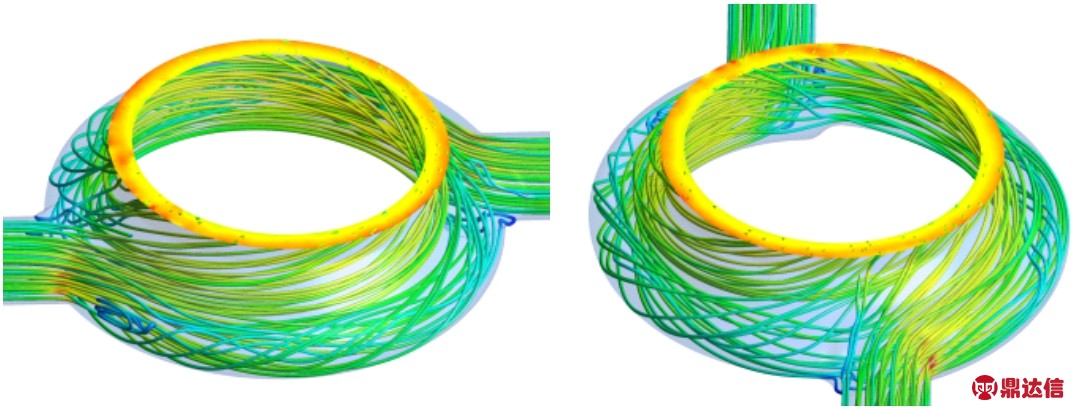
(b)工况2
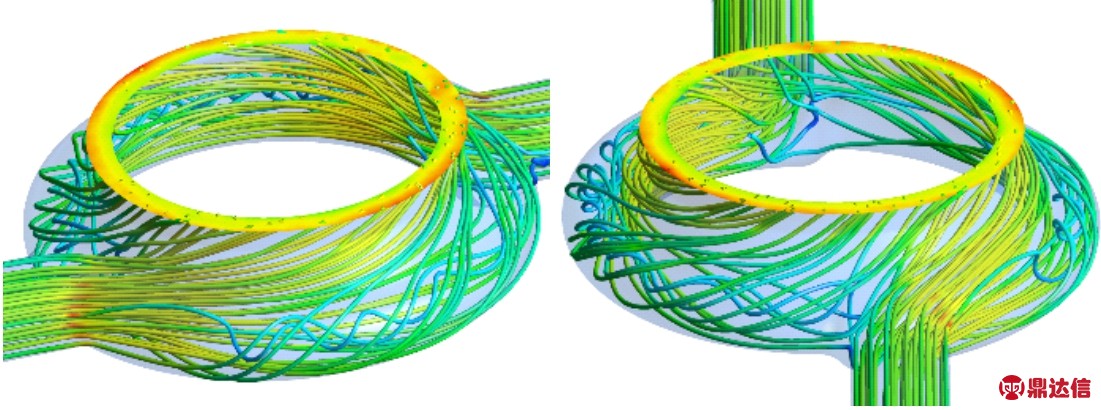
(c)工况3
图11 单独进气蜗壳三维流线和出口截面静压等值线云图
单独进气蜗壳的流场形态在3种工况下类似,因此采用工况3对单独进气蜗壳的总压分布进行分析。图12给出了单独进气蜗壳典型截面的总压等值线云图。由图11c和图12a可知,气体由进气管流入蜗壳之后,内壁流线没有出现漩涡,因此靠近蜗壳内壁的气体能量损失较少,总压几乎没有减小,而靠近蜗壳外壁处的气体由于存在着涡流,导致此处气体的能量损失增加,总压明显降低。由图12b可知,气体在沿着蜗壳周向流动时截面2处总压分布的差异最为显著。这是因为气体进入蜗壳后,流动面积突增导致流动分离,在靠近蜗壳外壁面形成了漩涡,随着流动向蜗壳下游进行,漩涡逐渐减弱。从截面2~5可以看出,总压在沿着流动方向上的径向截面的分布逐渐均匀。
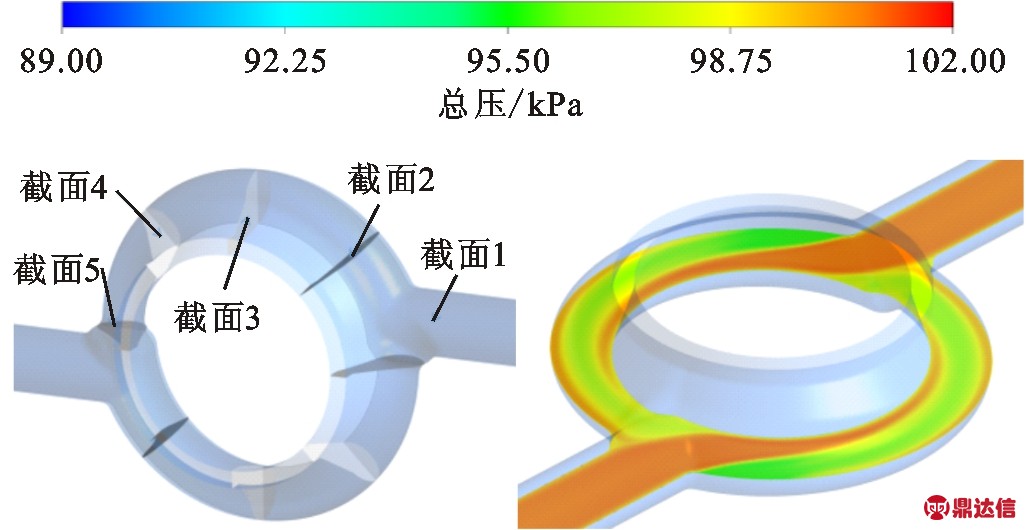
(a)截面1
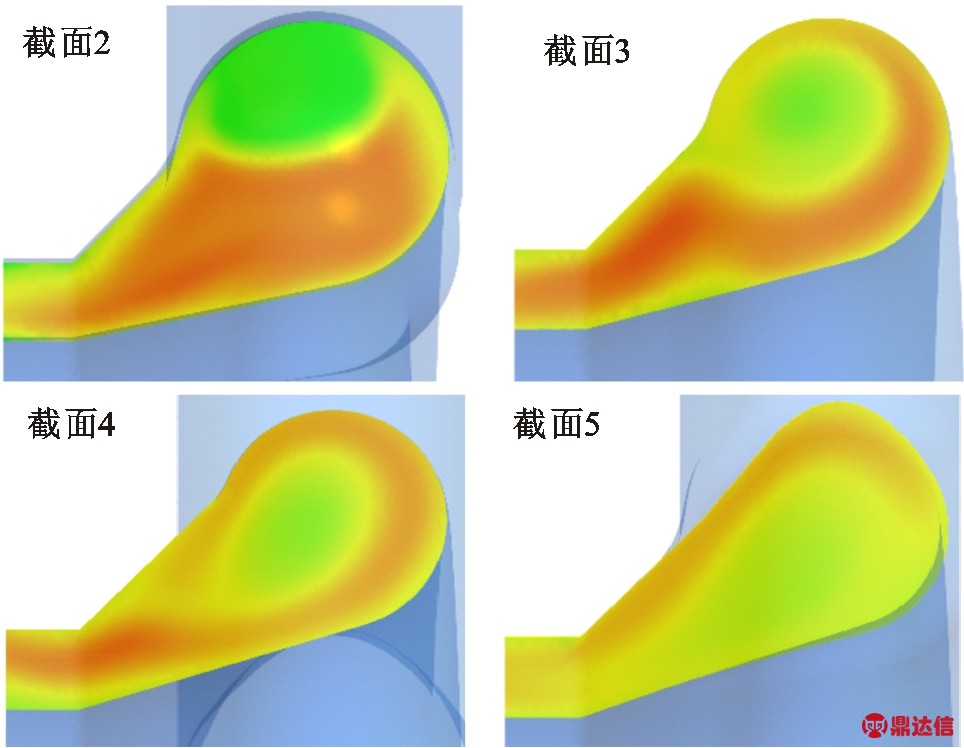
(b)截面2~5
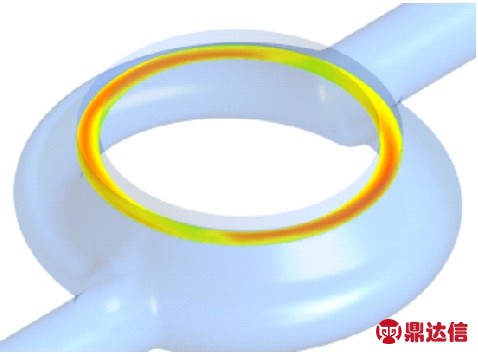
(c)出口截面
图12 单独进气蜗壳典型截面总压等值线云图
由图12c可知,蜗壳出口在几何布置上靠近蜗壳内壁,因此出口截面处的总压分布受蜗壳内壁气体影响较大,随着流动向下游进行,周向截面上的总压趋于均匀并且逐渐减小。
2.3 进气蜗壳耦合静叶结构的气动参数
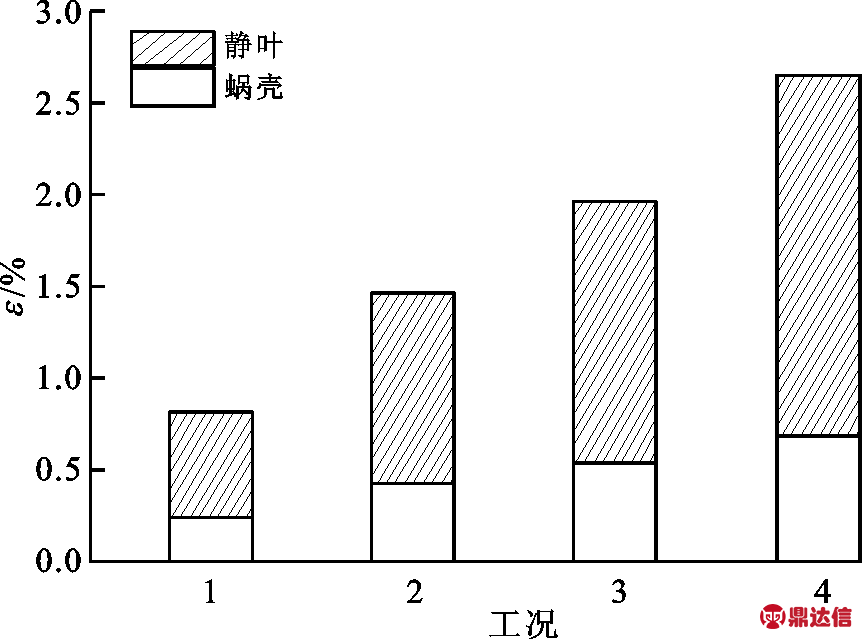
图13 4种工况下进气蜗壳耦合静叶结构的总压损失系数比较
基于单独进气蜗壳气动性能实验和数值研究的结果,开展了表2所示4种工况下的进气蜗壳耦合静叶结构的气动性能实验与数值分析。图13比较了进气蜗壳耦合静叶结构4种工况下的总压损失系数。由图可知,进气蜗壳耦合静叶结构的蜗壳和静叶局部总压损失系数均随进口总压的增加而增加,但是进气蜗壳部分的总压损失在整个腔室耦合静叶结构中占比较小,大部分总压损失发生在静叶中。表4给出了4种工况下蜗壳和静叶通道的局部总压损失系数。
表4 4种工况下蜗壳和静叶通道的总压损失系数 %
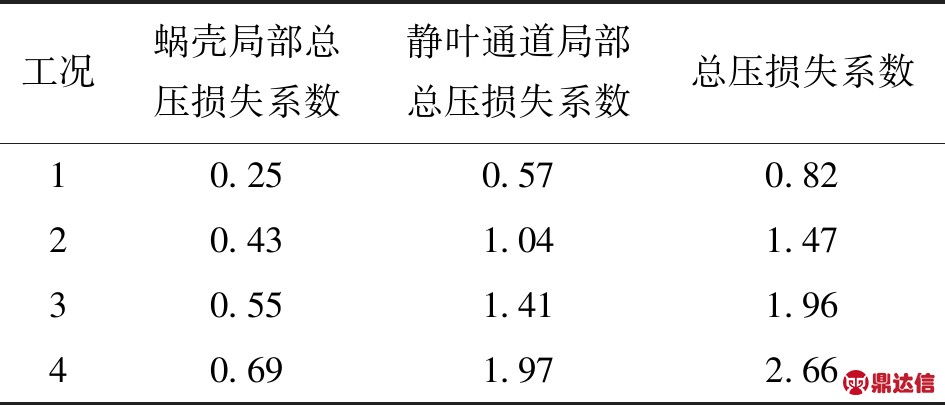
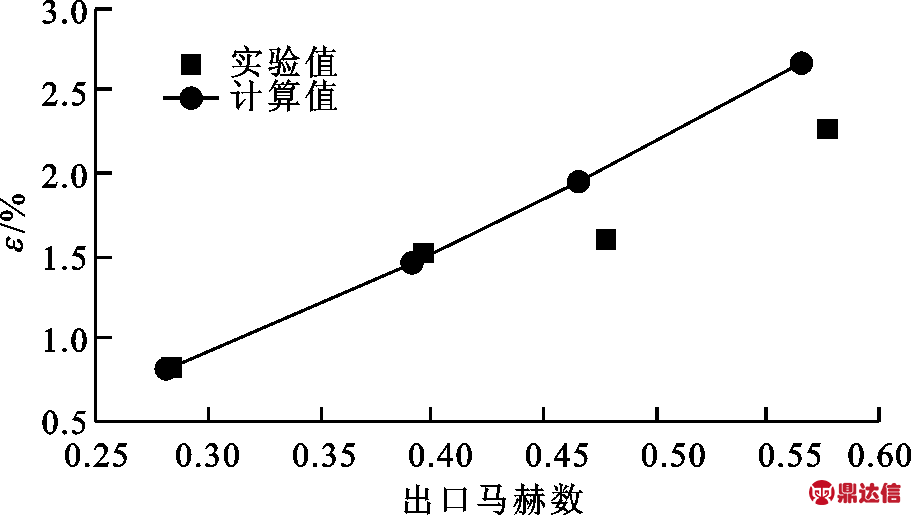
(a)总压损失系数
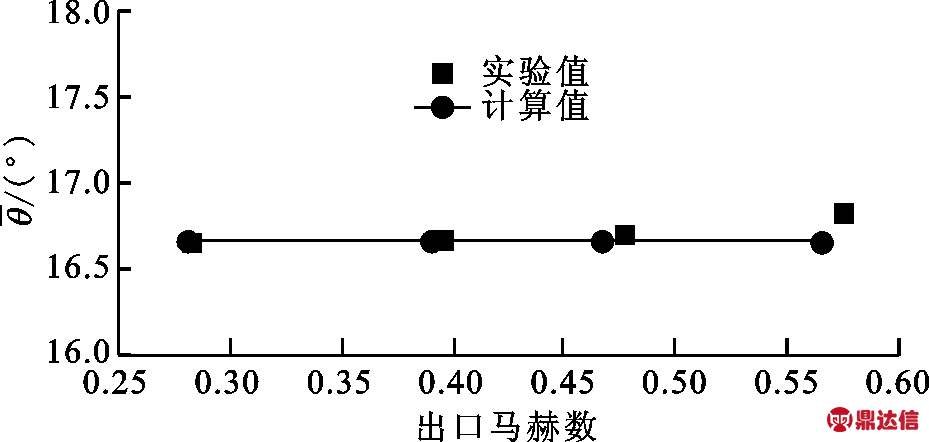
(b)平均出口气流角
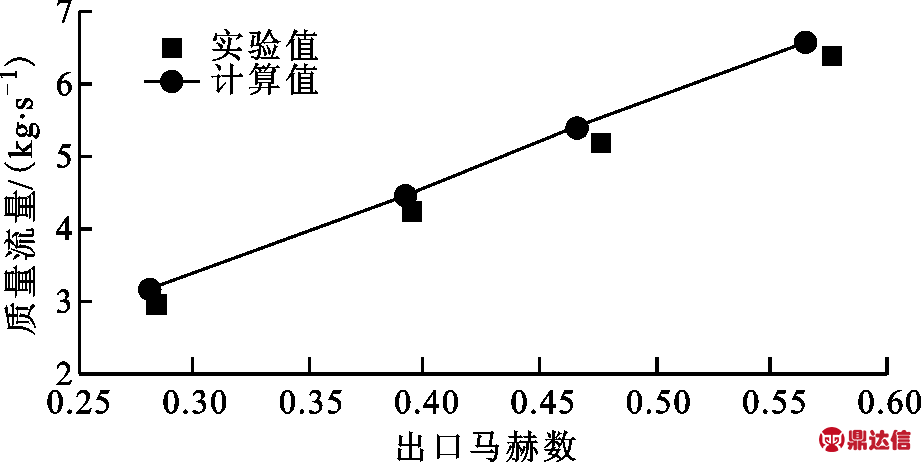
(c)质量流量
图14 进气蜗壳耦合静叶结构的气动参数随出口马赫数的变化
图14给出了进气蜗壳耦合静叶结构的气动参数随出口马赫数的变化。进气蜗壳耦合静叶结构的总压损失系数、出口气流角和质量流量的计算值与实验值吻合良好,验证了数值方法的可靠性。总压损失系数和质量流量均随着出口马赫数的增加而近似线性增加,总压损失系数由0.82%增加到2.66%,质量流量由3.13 kg/s增加到6.56 kg/s。静叶出口平均气流角随着出口马赫数的增加基本保持在166.6°。
图15给出了4种工况下进气蜗壳耦合静叶结构的蜗壳出口(静叶进口)气流角沿周向的分布,表5列出了进气蜗壳耦合静叶结构的出口气流角不均匀系数。可以看出,出口气流角沿周向的变化规律与单独蜗壳出口气流角一致,但耦合静叶的蜗壳出口气流角不均匀系数由单独蜗壳的20%降低到8.4%左右,说明蜗壳耦合静叶能使蜗壳的出口气流角沿周向分布更加均匀。这是因为在耦合静叶后静叶能起到导流的作用,使蜗壳的出口气流角分布变得均匀。
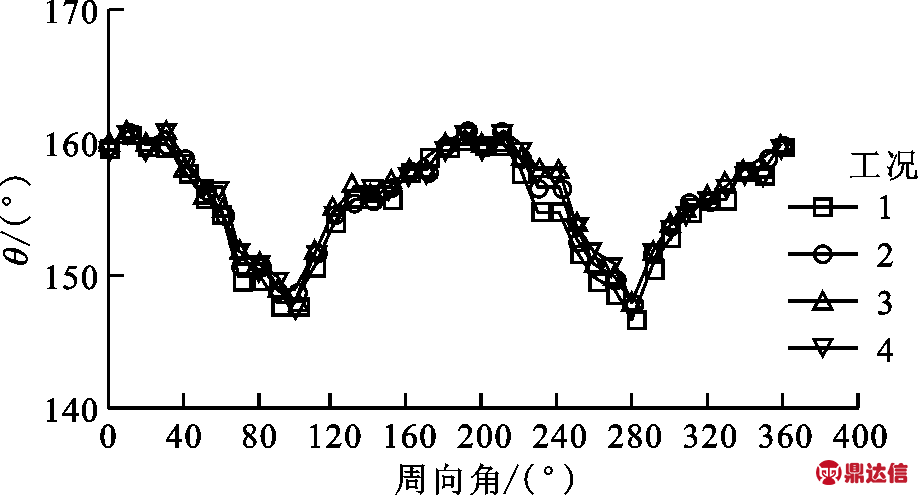
图15 4种工况下进气蜗壳耦合静叶结构的蜗壳出口气流角沿周向分布
表5 进气蜗壳耦合静叶结构中蜗壳出口气流角不均匀系数
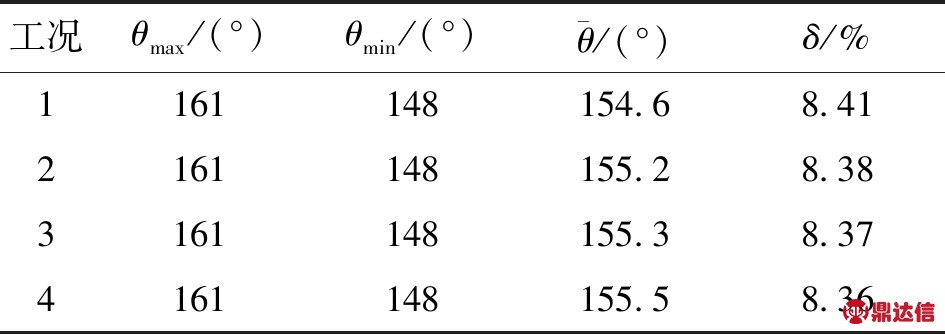
2.4 进气蜗壳耦合静叶结构流场
图16给出了工况1下进气蜗壳出口和静叶出口截面的气流角等值线云图。相比于单独进气蜗壳的出口气流角,由于静叶的整流作用导致进气蜗壳耦合静叶结构的静叶出口气流角分布更加均匀。静叶出口气流角在静叶尾缘处最大,在相邻静叶栅通道中间最小。在静叶尾缘处,流体受到静叶壁面的影响,使靠近静叶尾缘的出口处气流角增大,而在相邻静叶栅通道中间流出的气流由于轴向速度的增加,导致出口气流角减小。
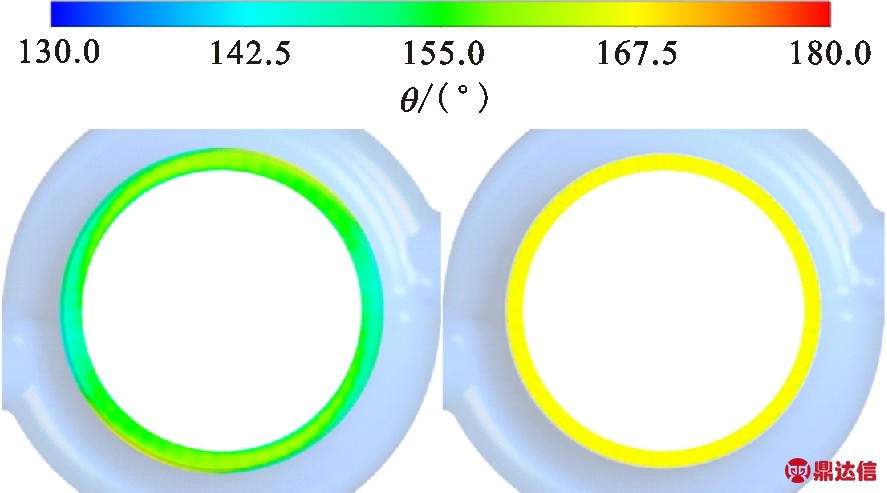
(a)进气蜗壳出口 (b)静叶出口
图16 进气蜗壳耦合静叶结构的出口气流角等值线云图
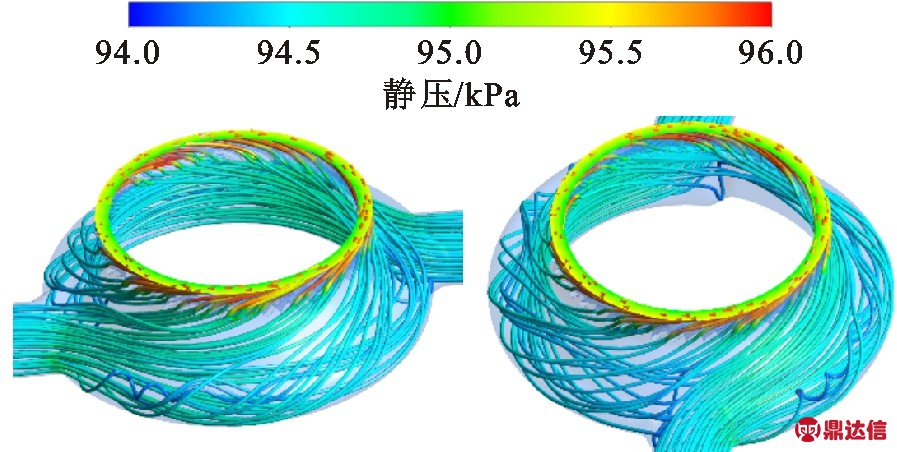
图17 进气蜗壳耦合静叶结构的三维流线和出口截面静压等值线云图
图17给出了工况1下进气蜗壳耦合静叶结构的三维流线和静叶出口截面静压等值线云图,此时蜗壳中的流线体现的流动规律与单独蜗壳中的相似,静叶中的流动规律将在下文具体分析。
静叶出口截面的静压分布与单独蜗壳出口相似,由于切向进气,气流受离心力作用,在蜗壳出口截面外径处压力高、内径处压力低。
图18给出了进气蜗壳耦合静叶结构的典型截面总压等值线云图,蜗壳内部总压分布规律与单独进气蜗壳的分布相似。由图18b观察发现,在静叶栅通道中,由于上下两个端面存在二次流,靠近上下端面流体的总压有明显的降低。由图18c可知,在静叶尾缘后的出口处,气体的总压有明显减小,这是由压力面和吸力面流出的两股气流在离开叶片后不能立刻均匀混合而形成涡流区造成的能量损失。
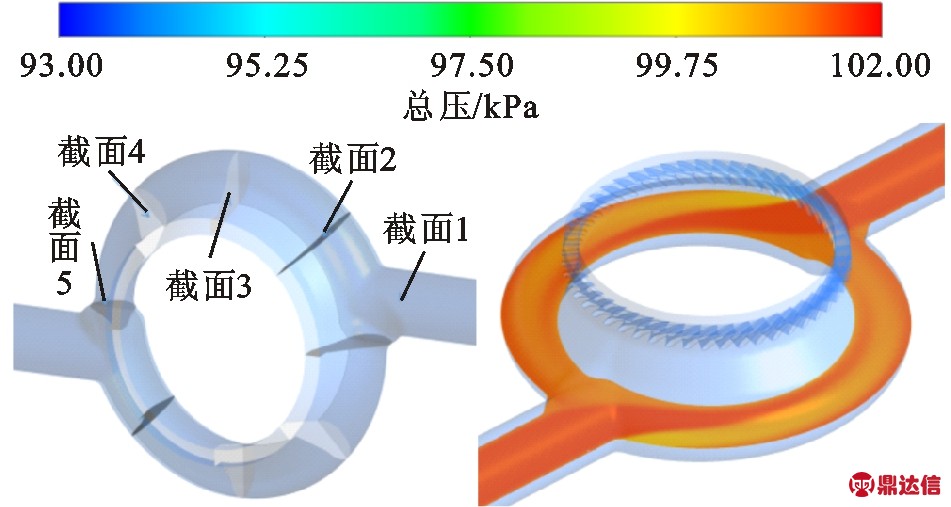
(a)截面1
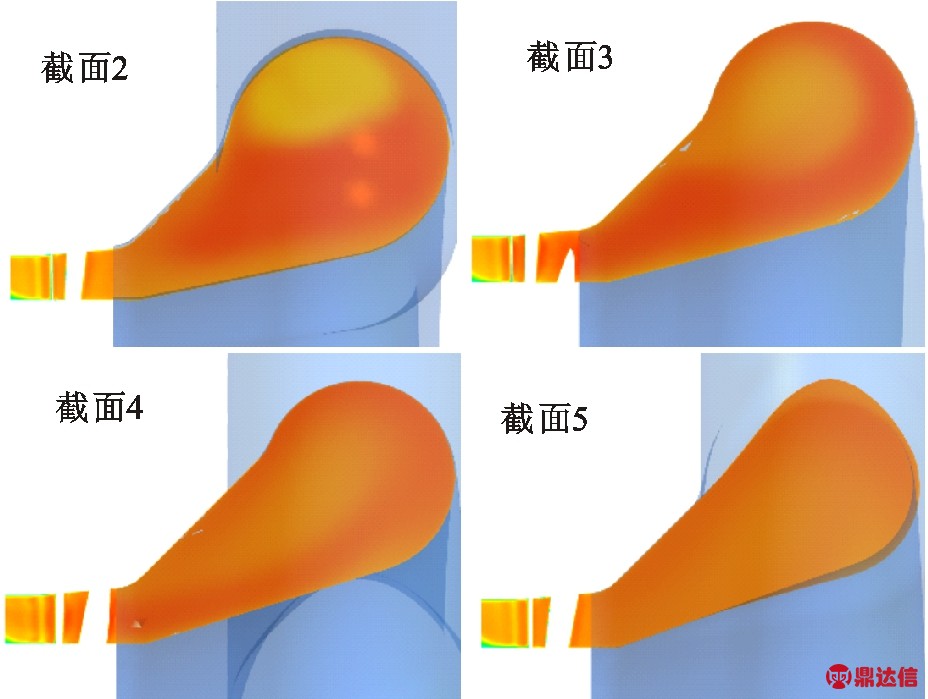
(b)截面2~5
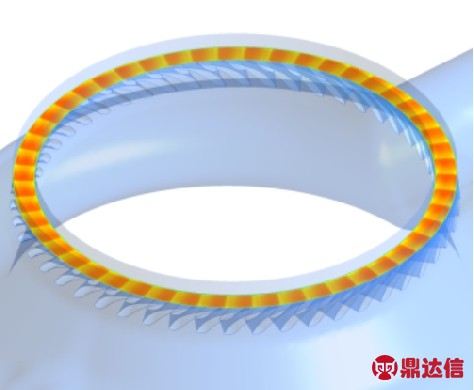
(c)出口截面
图18 进气蜗壳耦合静叶结构的典型截面总压等值线云图
图19给出了静叶通道典型截面静压、速度和总压等值线云图。在静叶通道内取与气流流动方向垂直的方向(如图19a所示)来分析端部损失,选取位置为图1中180°附近的叶栅通道。由于叶栅通道是弯曲的,当气流流过叶栅通道时会产生由叶型的背弧指向内弧的离心力。离心力的作用导致流体微团向叶栅内弧运动,使叶片内弧的压力大于背弧,即在叶栅通道中产生了一个由叶片内弧指向背弧的压力梯度,如图19b所示。
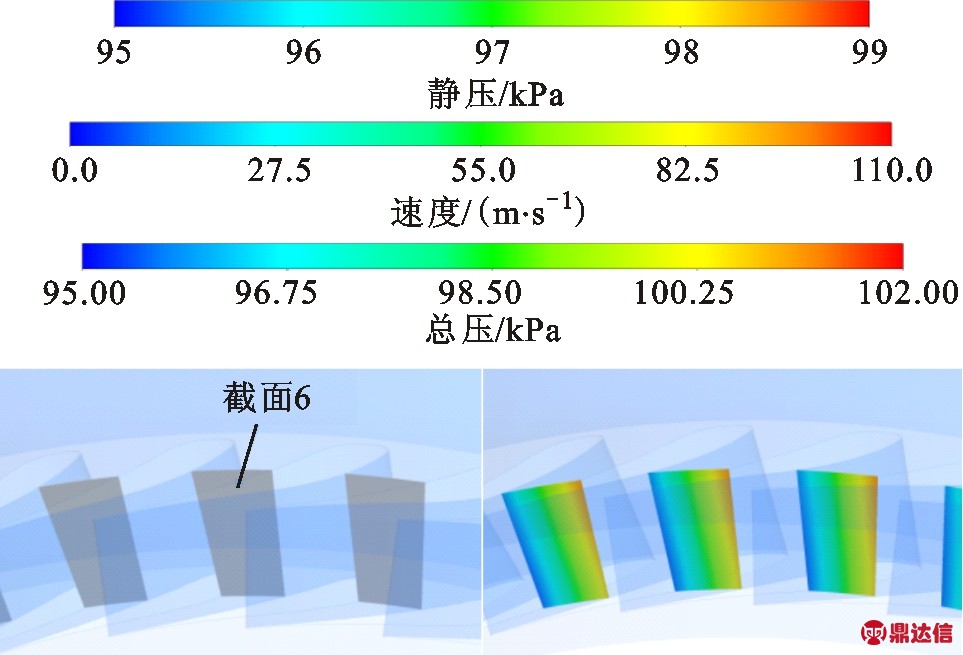
(a)典型截面位置 (b)静压云图
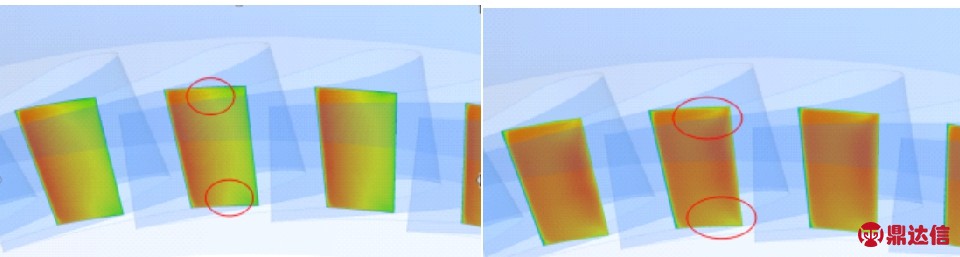
(c)速度云图 (d)总压云图
图19 静叶通道典型截面静压、速度和总压等值线云图
在叶栅通道主流区里横向的压力梯度与流体微团的离心力相互平衡,但是在叶栅上下端部存在有边界层,由于其中的流体速度远小于主流区(如图19c圆圈内部所示),从而导致上下端部处流体微团产生的离心力不足以平衡横向的压力梯度。在这种情况下,叶栅上下边界层内将产生从叶型内弧向背弧的横向气流流动,其结果为上下端部边界层气流向叶片背弧流动并产生二次流损失,如图19d总压云图所示,圆圈内部即为二次流所在位置,此处的能量损失较大,总压明显降低。
图20给出了静叶通道典型截面流线图和静压、总压等值线云图。由于叶栅上下两端部的漩涡没有相互重叠和干扰,因此选取叶高中间位置的圆环面(如图20a所示)来分析叶栅通道的型面损失,选取位置为图1中180°附近的叶栅通道。由于进气蜗壳采用了切向进气方式,使叶栅进口的冲角很小,叶型背弧没有出现明显的扩压段(图20d圆圈中即为扩压段),背弧上也没有明显的边界层脱离,如图20b的流线图所示。
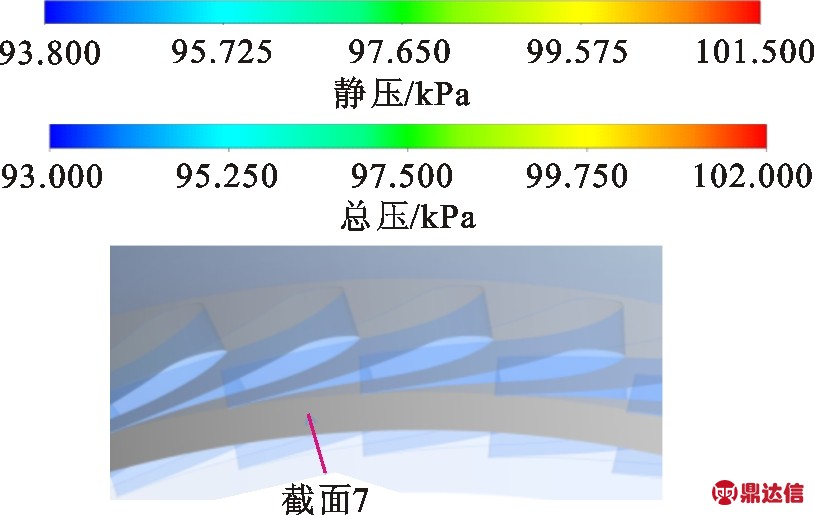
(a)典型截面位置
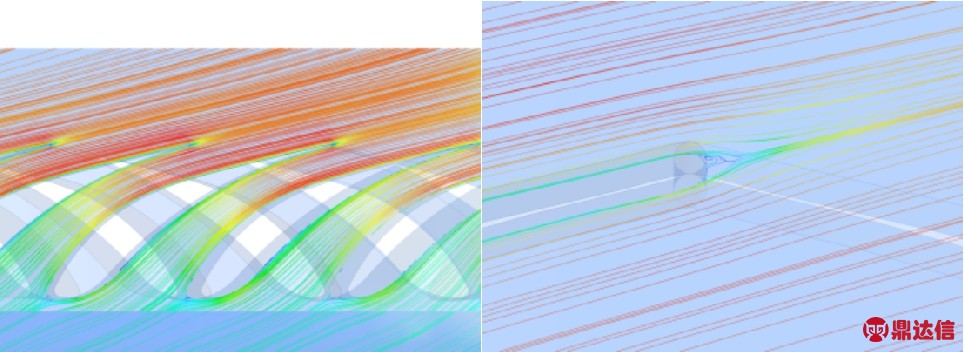
(b)叶栅通道流线图 (c)叶片尾迹区流线图
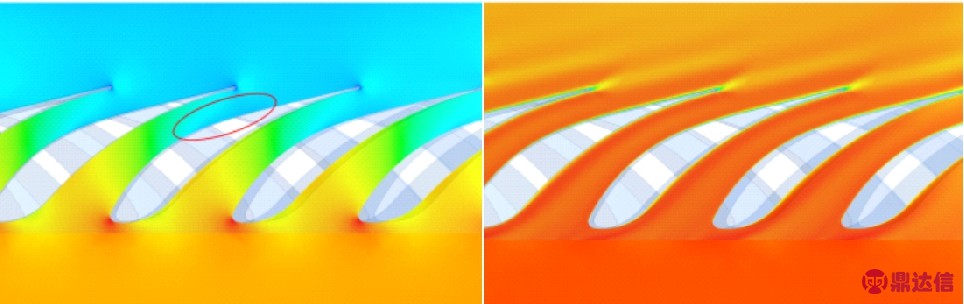
(d)静压云图 (e)总压云图
图20 静叶通道典型截面流线图和静压、总压等值线云图
本次实验中的型面损失主要为叶型表面的摩擦损失和叶片出口尾迹产生的涡流损失,如图20e总压云图所示,总压损失区域为叶片的表面以及叶片的尾迹区。
实验选用的叶片为反动式叶片,气流经过叶栅通道时会膨胀加速,加速气流使边界层厚度减小,有效地减小了摩擦损失。气流在叶栅通道中流动时,由于气流在背弧和内弧的膨胀程度不同,两股气流的压力和速度相差较大,沿着背弧和内弧的两股气流不能立刻均匀混合,因此在叶片尾迹区形成了充满漩涡的涡流区,如图20c的流线图所示。
3 结 论
采用实验测量和数值模拟的方法研究了汽轮机单独切向进气蜗壳和切向进气蜗壳耦合静叶结构的气动性能和流场特性,得到如下结论。
(1)切向进气蜗壳在蜗壳中能够实现良好的预旋流动,气动参数和流场形态具有180°对称性。单独切向进气蜗壳和切向进气蜗壳耦合静叶结构的气动参数计算值与实验值吻合一致。总压损失系数、质量流量均随着出口马赫数的增加而增加。
(2)单独切向进气蜗壳出口气流角基本上不随进口总压的增加而变化,其沿周向和径向分布不均匀,在进气管附件相对较小,在远离进气管的位置相对较大。切向进气蜗壳耦合静叶结构的出口气流角相比于单独切向进气蜗壳,沿周向的分布更为均匀。
(3)蜗壳内部产生总压损失的主要原因是当气流从进气管进入蜗壳后通流面积突然增大,导致气流在靠近蜗壳外壁处形成了充满漩涡的涡流区,而静叶栅通道中产生的总压损失主要来自于叶型表面边界层的摩擦损失、叶片尾迹区的涡流损失和在上下端部产生的端部损失。