摘 要:利用小试精馏装置对生物油模型化合物进行蒸馏实验,通过调节系统的真空度将生物油模型化合物分别在常压和减压状态下进行蒸馏,分析并总结了馏分中各组分的变化规律。结果表明,随着系统内真空度的不断升高,生物油模型化合物的总馏出率不断增加且结焦率不断降低,水分更容易被蒸出,馏分中有机物的初馏温度降低而馏出率增加。因此,增大真空度可有效分离生物油模型化合物的组分并降低蒸馏的能量损耗;当真空度为−0.08 MPa时,生物油模型化合物的蒸馏效果最好,其中,乙酸和糠醛的馏出率分别可达99.50%和65.88%、苯酚和愈创木酚的馏出率为25.19%和26.17%,均超过25%。
关键词:生物油模型化合物;精馏;真空度;减压蒸馏
生物质热解产物生物油的成分非常复杂,其内含有苯酚、愈创木酚、左旋葡聚糖、糠醛、甲基环戊烯醇酮等多种高附加值组分[1],是一种应用前景良好并可再生的精细化工原料,经分离和纯化可从中获取诸多具有高附加值的物质。据文献报道,催化裂解、加氢脱氧、催化酯化、萃取、柱层析等技术被用于生物油的分离提纯试验研究[2−6],但均不同程度地存在催化剂容易失活、转化率低以及分离成本高等问题。蒸馏技术可以根据生物油中各组分沸点的不同进行分离,且由于其工艺简单高效并易于大规模应用而受到不少学者关注:如Wang等[7]采用分子蒸馏技术,将木屑热解所得生物油分为轻、中、重三种馏分,轻、中馏分馏出率最高可达85%,且无明显结焦和聚合现象;Guo等[8]采用分子蒸馏技术分离富含羧酸和酮类的生物油馏分,再利用固体酸催化剂进行改性,达到降低生物油腐蚀性的目的;Rahman等[9]研究了短程真空蒸馏技术从生物油中分离出甲醇和丙烯醛,以及63%的乙酸和44%的丙酮醇;Choi等[10]对褐藻生物油进行减压蒸馏,馏分受温度的影响分成三类,其中,富集脂类、芳族化合物、脱水糖等有机物。
以上研究表明,蒸馏技术可以改善生物油的性能并分离出高附加值的物质。但这些蒸馏实验大多是在实验室台架试验装置中进行,对生物油在小试和中试实验蒸馏装置中的研究鲜有报道。由于生物油成分非常复杂,直接在小试或中试装置中进行蒸馏分离难度较大,因为这种复杂体系的蒸馏特性还不是很清楚,故本研究使用生物油主要特征组分构成的模型化合物(以下简称“生物油模化物”),采用小试蒸馏装置进行分离实验,探究不同真空度对生物油特征组分蒸馏特性的影响,分析不同真空度下各组分的馏出率,从而总结并获得生物油特征组分及其构成体系的蒸馏特性,为生物油原油的蒸馏打下基础。
1 实验部分
1.1 实验试剂
实验中选取的各模化物配比依据其生物油蒸馏馏分中的分布并进行一些调整[11],组成包括蒸馏水、乙醇、乙酸、糠醛、苯酚、愈创木酚、甲基环戊烯醇酮,将七种物质按照质量比为5∶4∶4∶2∶2∶2∶1混合,搅拌24 h,使其充分混合。
1.2 实验装置及步骤
精馏塔小试装置示意图如图1所示,塔节高1200 mm,塔径40 mm,材质为304不锈钢。经过前期的预实验,该实验中生物油模化物的用量与塔径尺寸相匹配。而塔高是利用简捷算法估算塔板数,首先用芬斯克方程计算最少理论塔板数,然后计算给定条件下的最小回流比,最后应用吉利兰经验关联估算所需理论板数,之后设置精馏塔塔高。本装置以乙酸和苯酚作为参考,计算其理论塔板数。其中,芬斯克方程公式如式(1)所示:
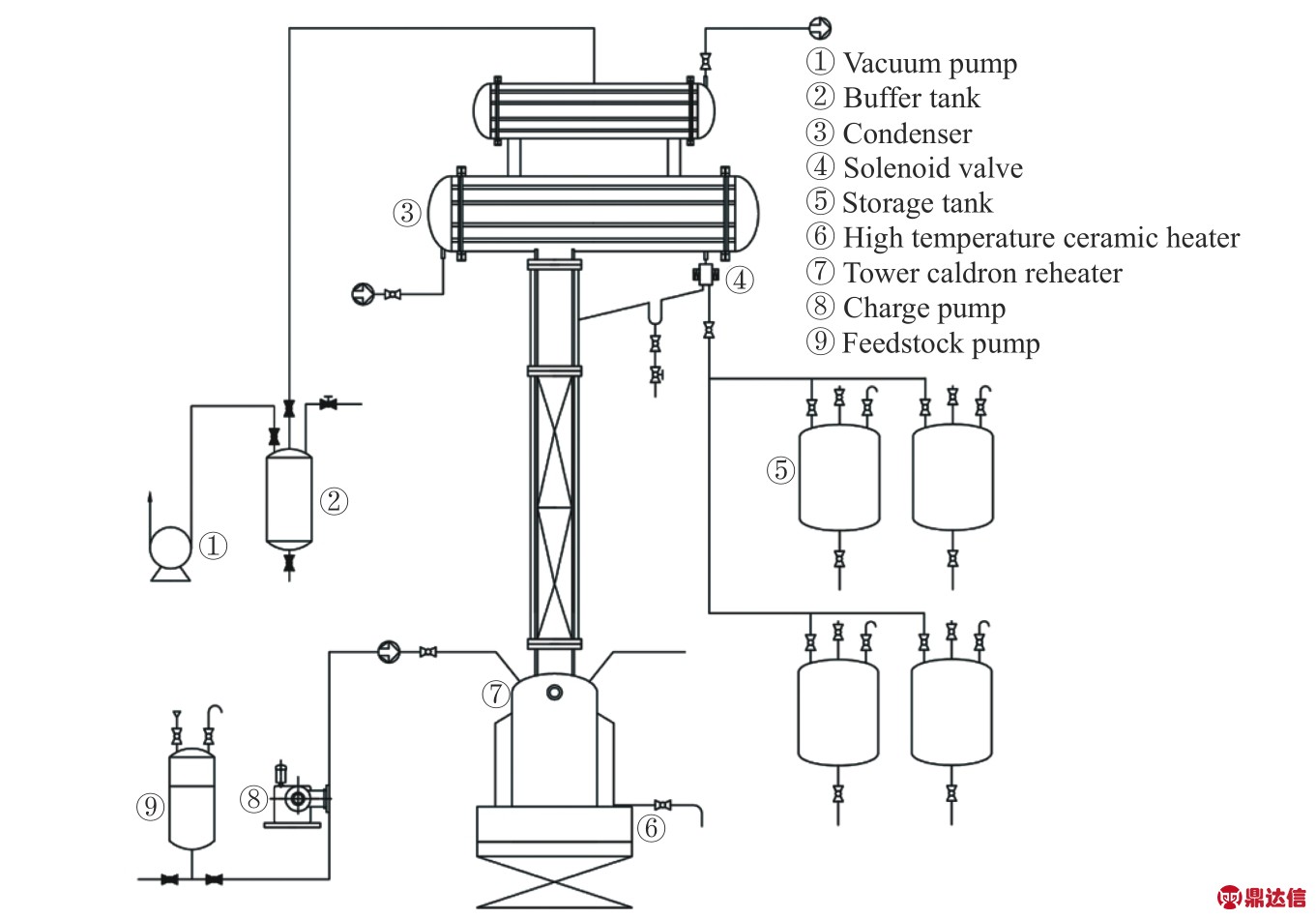
图1 精馏塔小试装置示意图
Figure1 Schematic diagram of small-scale rectification column
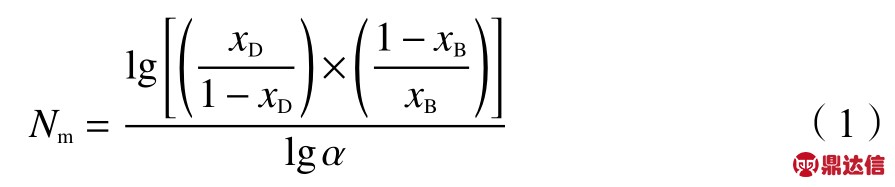
式中,Nm为精馏装置所需最少理论板数,xD、xB分别为塔顶产品组成和塔底产品组成的摩尔分率,α为乙酸和苯酚的平均相对挥发度。最小回流比Rm可由图解法求取[12]。吉利兰经验关联曲线回归得出算式如式(2)所示:

最终计算结果为N=20.0。但是考虑后期需要完成多组分生物油蒸馏实验,精馏塔塔板数要大于20.0,因此,设计时将塔板数设置为24块,塔高为1200 mm。该装置主体密闭性良好,压力表实时检测系统内压力;每次做蒸馏实验之前都会确认试验装置各连接处是否密封完好,进行气密性检查,将系统抽真空至−0.02 MPa时停泵,观察压强变化,完成气密性检测后,将塔底料液倒入塔釜。实验操作在真空度为−0.08、−0.065、−0.05、−0.03和0 MPa(常压)下进行。塔釜采用高温陶瓷加热器加热,根据Antoine公式[13]计算各物质的沸点作为参考,设置合适的加热温度,公式如式(3)所示:

式中,p为纯液体饱和蒸气压(mmHg),t为摄氏温度(℃),A、B、C为不同物质对应的不同物性常数。
每次实验取用2000 g生物油模化物,利用真空泵将原料抽入塔釜。蒸馏过程中设置全回流并加热塔釜,塔中节设置适当温度保温。当塔顶温度趋于稳定,视为馏分蒸出,记录塔顶温度数值,将回流比调至5∶1,采出馏分。当塔顶温度升高(1−3 )℃,再次设置为全回流。待温度降回馏分馏出温度后,取样,再次重复变回流比操作。当塔顶温度升高超过5 ℃后,视为该馏分完全蒸出,升高塔釜温度继续蒸馏下一组馏分。按此步骤将所有馏分采出,待储罐中再无液体馏出且塔顶温度降低至30 ℃以下视为生物油模化物全部蒸出。
馏分中各物质每一级的馏出率计算公式如式(4)所示:

式中,wi为物质在第i级馏分中的馏出率(%),Mi为第i级馏分质量(g),Ci为物质在第i级馏分中的含量(%),M为原料质量(g)。
1.3 样品分析
采用容积式卡尔费希尔滴定仪(ZDJ-3S XQWF北京)测定样品中的水分。
采用气相色谱-火焰离子化检测器(GC-FID)检测各组分的有机组成。采用内标法,以1-2-4-5-四甲基苯为内标物。GC的升温程序为:GC保持在50 ℃下3 min,4 ℃/min升至100 ℃。在FID中,H2的入口压力为0.15 MPa,空气的入口压力为0.1 MPa,进样口和检测器的温度为280 ℃[14]。
2 结果与讨论
2.1 总馏出率
图2表示不同真空度下蒸馏馏分的总馏出率随蒸馏温度的变化曲线,馏分可划分为六级。五条曲线表现出大致相同的增长趋势:当蒸馏温度较低时,曲线斜率较大,前四级馏分的总馏出率达到65%−70%;之后总馏出率增长变得平缓,最终馏出率达到74%−88%。随着蒸馏温度的升高,馏分的总馏出率减少。常压下,生物油模化物的结焦率达到15.19%,而真空度增加到−0.08 MPa时,结焦率显著下降,仅8.46%。这表明提高真空度可以有效降低生物油的结焦率。
由图2可知,系统内的真空度越高,馏分馏出所需要的温度越低。当系统真空度为−0.08 MPa时初馏温度最低,塔顶温度在45 ℃前大约收集到21%的馏分,而常压下直到塔顶温度升至70 ℃后才收集到15.4%的馏分。随着真空度的增大,最终总馏出率从74.07%提升至87.88%。由此可得系统真空度为−0.08 MPa时,生物油模化物的初馏温度最小,总馏出率最大,结焦率最低,该真空度下的蒸馏效果最好。该现象可归因于系统内真空度降低使得液体的饱和蒸气压降低,馏分的沸点降低,因此,减压蒸馏可以在较低的温度得到较高收率的馏分[15]。由曲线变化趋势可得,各馏分在第四级或者第五级出现拐点。在此拐点以下,总馏出率随着温度的升高而增大。过了拐点以后,随着蒸馏温度的升高,总馏出率基本保持稳定。从能量利用效率方面考虑,将蒸馏温度设置在该拐点附近,可有效地分离馏分并最大限度的减少能耗。
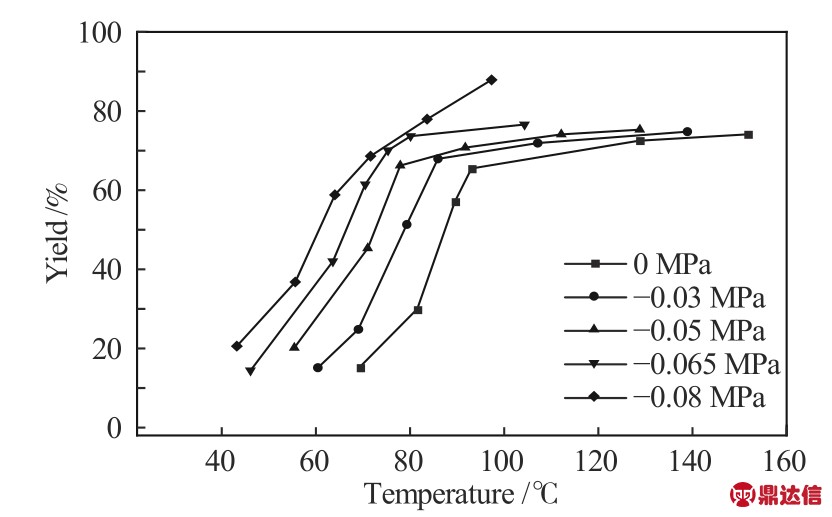
图2 不同真空度下蒸馏馏分的总馏出率
Figure2 Yields of total distilled fractions at different vacuum degrees
2.2 水分含量
图3表示在不同真空度下馏分中的水分馏出率。水分的馏出率在蒸馏过程中先稳定增长,随后增长趋势减缓,最后基本维持稳定。随着真空度的增大,水分的初馏温度从69.4 ℃降低到43.2 ℃以下,降低了能量损耗。当真空度为−0.08 MPa时,第五级馏分中水分质量保持稳定且馏出率接近100%,这表明生物油模化物中所含水分在整个蒸馏过程中基本被蒸出。由此可得,利用精馏塔对生物油进行蒸馏可以有效分离生物油中的水分。从馏出率的曲线变化来看,系统的真空度降低后,可以在较低的温度下移除更多的水分。从整体上来看,当系统真空度为−0.08 MPa时对水分的分离效果最好,最终能够分离生物油模化物中93.14%的水分,这表明在该真空度下蒸馏有利于改善生物油的性能,提高其热值。
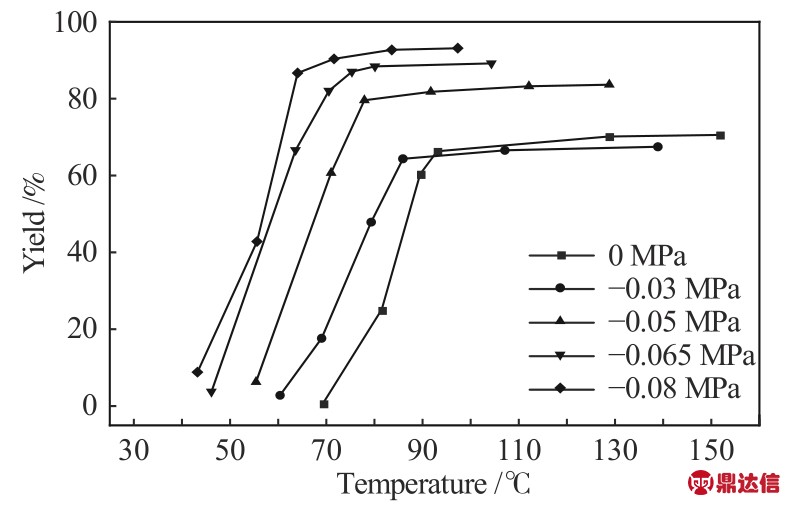
图3 不同真空度下馏分中水分馏出率
Figure3 Moisture of distilled fractions at different vacuum degrees
2.3 馏分中有机物含量的分析
采集的馏分中不含甲基环戊烯醇酮,原因可能是甲基环戊烯醇酮的沸点高且在生物油模化物中的质量占比较低,混合后较难蒸出。图4−8为采用GC-FID对不同真空度下馏分中其他五种有机物检测得到的结果。
图4表示不同真空度下馏分中乙醇的馏出率。蒸馏前期大部分乙醇被蒸出,随着蒸馏温度的升高,乙醇的增长趋势逐渐变缓最终趋于稳定,馏出率最高可达97.19%,这表明几乎将生物油模化物中的乙醇全部蒸出。第一级馏分中含有较多乙醇可以归因于组成生物油模化物的七种物质中,乙醇的沸点最低,当塔釜加热温度逐渐升高后,乙醇被最先蒸出。但文献[16]表明,生物油中不含或含有极少量乙醇,本研究加入乙醇的主要原因是作为溶剂让其他几种物质能够充分混合。
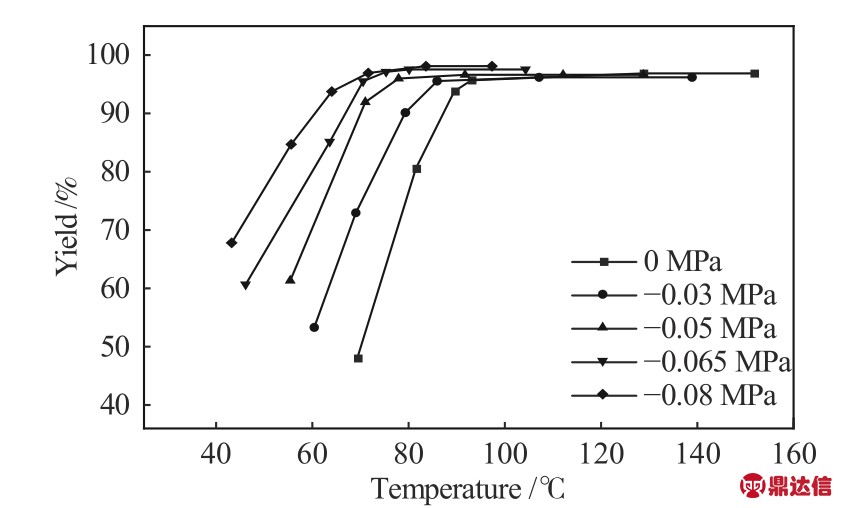
图4 不同真空度下馏分中乙醇的馏出率
Figure4 Alcohol yields of distilled fractions at different vacuum degrees
图5表示不同真空度下馏分中乙酸的馏出率。从增长趋势来看,各真空度下馏出率的变化曲线大致相同。可以将乙酸的蒸馏过程划分为三个阶段:缓慢增长阶段、快速增长阶段和维持稳定阶段。由图5可得,真空度为−0.08 MPa的蒸馏效果最好,因此,以真空度为−0.08 MPa为例进行分析。
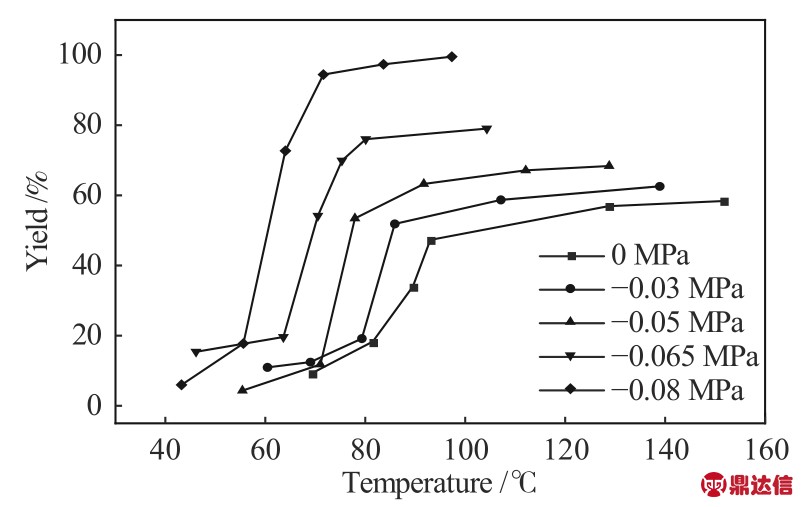
图5 不同真空度下馏分中乙酸的馏出率
Figure5 Acetic acid yields of distilled fractions at different vacuum degrees
第一阶段在塔顶温度55.6 ℃以下,这一阶段乙酸的增长趋势较为缓慢,馏出率为17.77%;第二阶段温度在55.6−71.6 ℃,该阶段乙酸馏出率快速增加,从17.77%增加到94.43%,因此,可参照此阶段设置蒸馏温度,提高能量利用效率;最后是第三阶段,此阶段乙酸的馏出率基本不变。出现该现象的原因是:在第一阶段,蒸馏温度较低且生物油模化物中可能存在不同强度的分子间作用力,阻碍了乙酸馏出[11],因而增长缓慢;第二阶段蒸馏温度接近该真空度对应的乙酸沸点,该温度下乙醇和水分基本被蒸出,而另外的四种有机物较难蒸出,因此,乙酸的馏出率显著增加;而到了第三阶段,乙酸几乎全部蒸出,因此,曲线维持稳定。总体而言,系统的真空度为−0.08 MPa时,有利于生物油模化物中乙酸的分离。
图6表示不同真空度下馏分中糠醛的馏出率。
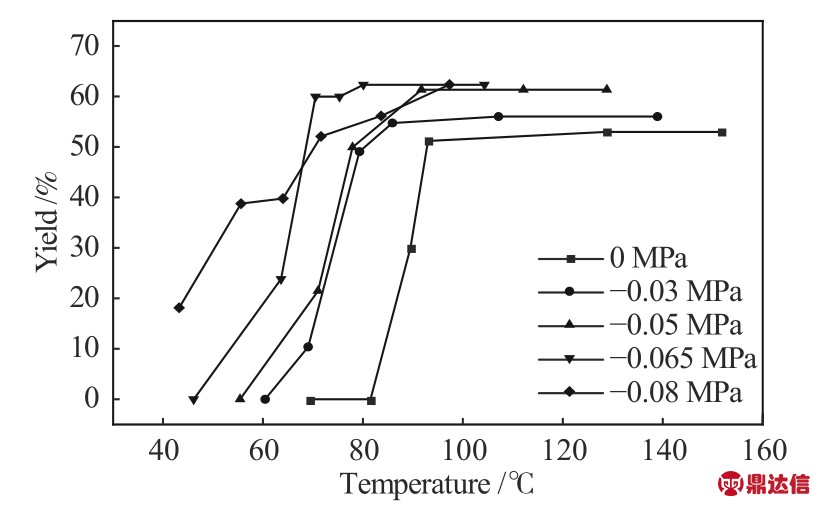
图6 不同真空度下馏分中糠醛的馏出率
Figure6 Furfural yields of distilled fractions at different vacuum degrees
从分布上看,随着真空度的增大,糠醛初馏温度向低温区移动。常压下,糠醛的初馏温度为81.5 ℃,而真空度达到−0.08 MPa时,糠醛的初馏温度降低到43.2 ℃。因此,增大系统内真空度有助于降低糠醛的初馏温度,减少能量损耗。当真空度在−0.065 MPa以下时,各真空度下糠醛馏出率的变化大致相同。以真空度为−0.065 MPa为例,第一级馏分中不含糠醛,当蒸馏温度升高后,糠醛的馏出率也随之增多。70.5 ℃是一个特殊的临界点,在此温度下大部分糠醛被蒸出,继续升温后糠醛的馏出率基本稳定。出现该临界点的原因可能是水、酚类和羧酸相互形成氢键,其中,酚和羧酸可以形成强氢键化学基序,模化物中含有乙酸、水和多种酚类物质,表明存在形成普通氢键和强氢键的条件,因此,可将模化物的阶段性变化归因于不同强氢键的断裂[17,18]。考虑到能量的利用效率,可以将蒸馏温度设置在该临界点处。当真空度在−0.065 MPa以下时,第四级馏分中糠醛的馏出率急剧下降,其原因可能是糠醛分子具有活泼性,塔釜中有剩余的乙酸未被蒸出,液体呈酸性,糠醛在高温和酸性条件下与苯酚发生了缩合反应形成大分子物质和焦炭[19],导致后期馏出率不再增加。这也解释了此时总馏出率不再增加的原因,该临界点处发生反应产生焦炭阻碍了部分有机物馏出。而真空度为−0.08 MPa时糠醛的馏出率一直增加,在第四级糠醛的出馏速率最大,最终达到62.37%。这表明真空度达到−0.08 MPa后,能够有效的分离糠醛。
苯酚的馏出率变化曲线如图7所示。真空度在−0.03 MPa以下时,苯酚在第二级以后初次蒸出,此温度下的苯酚出馏速率最快。当真空度高于−0.03 MPa后,随着真空度的逐渐增大,初馏温度随之降低。最大出馏速度随着真空度的增大向高温区移动。从分布上看,真空度在−0.03 MPa以下时苯酚的出馏速率在第三级最大。当真空度高于−0.03 MPa后则出馏速率在馏分的第五级最大。因此,可初步判定,系统真空度在−0.03 MPa以下时,苯酚收率最大化可限制塔顶温度为79.3−89 ℃,真空度在−0.05 MPa以上时,可考虑将塔顶温度升至83.6−112.1 ℃。五种真空度在第四级馏分中均不含苯酚,其原因可能是此阶段糠醛和苯酚在高温和酸性条件下发生了缩合反应[19],糠醛分子被消耗掉之后,塔釜中剩余的苯酚重新被蒸出。
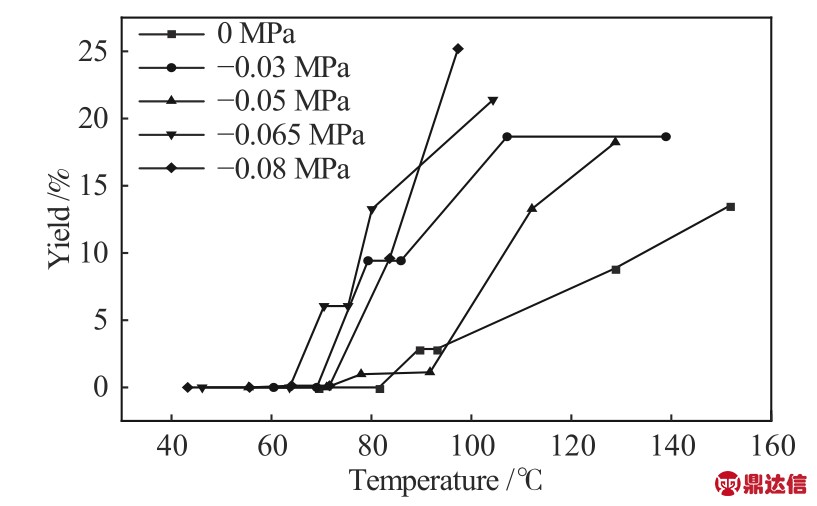
图7 不同真空度下馏分中苯酚的馏出率
Figure7 Phenol yields of distilled fractions at different vacuum degrees
图8表示不同真空度下馏分中愈创木酚的馏出率。当真空度为−0.05 MPa时,第六级馏分中愈创木酚的含量达到48.34%,该结果表明,此真空度下有利于提取生物油中的愈创木酚。常压下愈创木酚的馏出率较低,最终馏出率为17.11%。减压环境中的馏出率基本相同,最终馏出率为24%−26%。这说明相较于常压蒸馏,减压环境更有利于分离生物油中的愈创木酚。从蒸馏温度方面来看,常压下当塔顶温度达到91.7 ℃时,愈创木酚被蒸出。减压下愈创木酚的初馏温度最低为64 ℃。从馏出率方面来看,常压下第四级馏分几乎不含愈创木酚,而减压下愈创木酚馏出率曲线的增长趋势大致相同,随着蒸馏温度的升高,愈创木酚的馏出率逐渐增大。该现象可归因于愈创木酚自身的沸点较高,常压下较难被蒸出,且第四级馏分中的其他产物多、占比大,导致愈创木酚含量较低。随着系统内真空度的增大,愈创木酚的饱和蒸气压降低,更易馏出。在真空度为−0.08 MPa时,愈创木酚的馏出率随着温度的升高不断增大。结果表明,真空度为−0.08 MPa是分离愈创木酚的最佳条件。
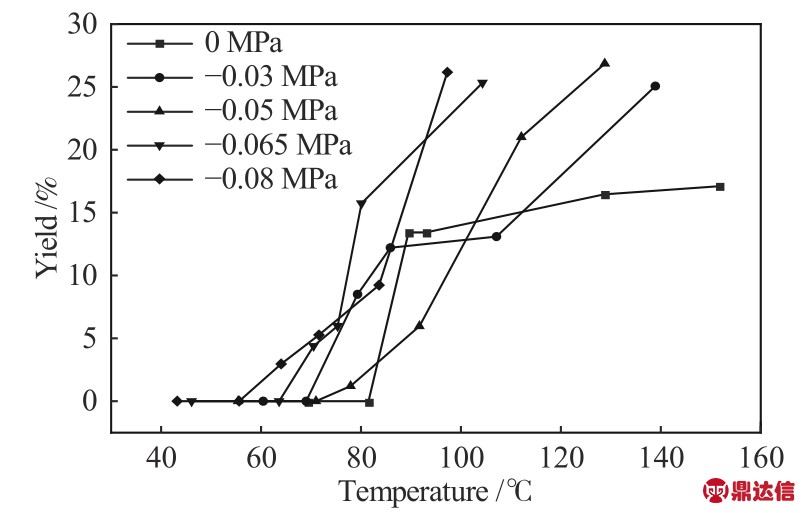
图8 不同真空度下馏分中愈创木酚的馏出率
Figure8 Guaiacol yields of distilled fractions at different vacuum degrees
3 结 论
本研究利用精馏塔小试装置对生物油模化物进行常压和减压蒸馏,设置五种真空度−0.08、−0.065、−0.05、−0.03和0 MPa比较产物组分分布变化,进而探究该小试装置内不同真空度对生物油各特征组分蒸馏特性的影响。结果表明,随着系统真空度的增大,生物油各特征组分的馏出率不断增加;在系统内不同的真空度下,馏分中的有机物馏出率变化较为相似;各有机物的初馏温度随着真空度的增大而减小;在蒸馏过程中当蒸馏温度较低时,主要馏出的是小分子有机物包括水分、乙醇和乙酸;随着蒸馏温度的提高,乙酸、糠醛以及酚类物质被富集。在真空度−0.08 MPa下蒸馏效果最好,总馏出率最高达到87.88%,结焦率为8.46%,水分馏出率为93.14%,乙酸、糠醛、苯酚、愈创木酚的馏出率分别为99.50%、65.88%、25.19%和26.17%。